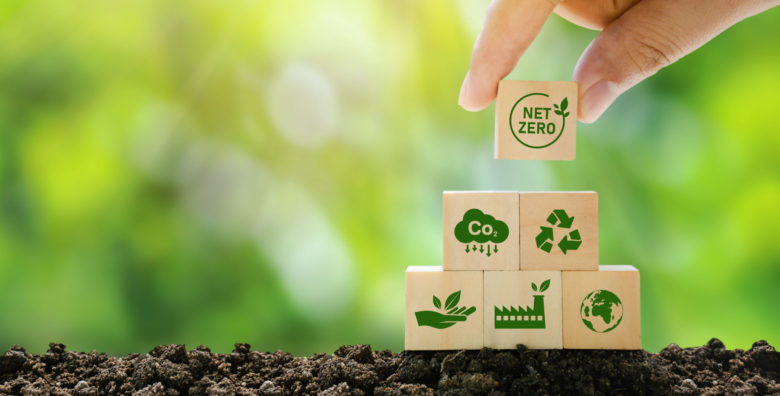
Through our experience in central energy plant design in numerous industry sectors, we believe that sustained successful outcomes stem from proactive engagement with our clients’ unique requirements. This commitment extends beyond the construction stage and well into a building’s lifecycle and the operations and maintenance aspects of its systems. In addition, HH Angus puts strong emphasis on the key performance metrics that guide our clients’ business goals so that we can balance value and project delivery tailored to each client.
Energy Master Planning
Energy master planning provides the opportunity to consider current and future expected building uses and loads, up-front capital availability, and timelines to establish appropriate phasing of projects, level of planning and detail design, along with meaningful cost estimates and analysis. For example, on a project to expand a large pharmaceutical manufacturing campus, we performed a feasibility study considering year-round energy load profiles with specified hydronic temperatures and steam pressures conditions in order to maximize the value delivery of new invested infrastructure and lower carbon footprint objectives. We explored options involving a mix of steam to hot water heat exchangers versus a low temperature network with heat pump “boosters” at point of application, taking into account characteristics of the existing distribution network and equipment conditions while improving operational resiliency and redundancy. The final decision was to proceed with a system that would satisfy the existing needs of the buildings in the short term but be adaptable to lower temperatures in future as existing buildings are upgraded or replaced.
Case Study - Post Secondary Campus
For this project, we joined an industry partner to study the feasibility of a centralized retrofit district hydronic heating and cooling cogeneration plant. The study considered networking various existing decentralized building heating and cooling infrastructure. This approach provided significant energy savings through the higher efficiencies inherit in larger scale equipment, load diversification and less equipment to achieve redundancy requirements. The original design involved multiple magnetic bearing chillers and heating boilers, and gas-fueled cogeneration with placement of one central plant close to the various buildings. The project was partially driven by a concern for aging decentralized equipment that would be phased out within the next decade or so. Preliminary cost estimates identified limitations in the preliminary centralized design approach resulting from cost-inhibiting disruptions to an active campus for installation of distribution hydronic piping. As a result, our energy modeling and feasibility review focused on a phased strategic implementation to network a smaller cluster of campus buildings which required less up-front capital. This provided the benefits of the original iteration while supporting the owner’s longer term infrastructure upgrade plans. A peaking plant was separately constructed and successfully commissioned to support electrical demand.
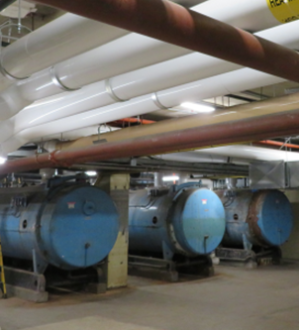
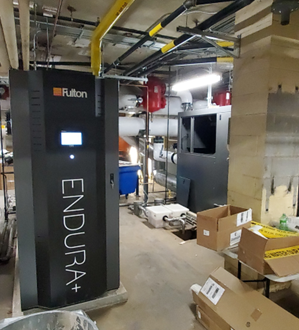
End-of-life heating boilers replacement (left) with new high efficiency gas-fired condensing boilers serving various networked campus buildings; Fulton EDR+ units shown(right)
Retrofit Design
Facility owners approach design consultants looking for a solution to a current problem or a predicted problem. To provide a solution, several factors need to be considered, such as budget constraints and, often, limited (as-built) documentation available for existing facilities. Due to these constraints, some consultants may seek to use project solutions that worked in the past and limited information via site surveys, which may not take into consideration current operational conditions or other factors that were not considered during feasibility and modeling. This can lead to significant financial implications for the owner over the life of a plant. HH Angus recognizes that active early engagement with operational team members familiar with the facilities is often key to uncovering the optimal design solution approach.
On one project, we were retained for detailed design engineering work to scale up treated water storage to increase steam production for an urban district steam plant. This included requirements by the owner to minimize capital expense and limit plant space for the conversion by reusing existing infrastructure, including storage tanks and piping. We held discussions with experienced plant staff and reviewed multiple past retrofit projects that led to the current condition of the overall system. Our investigations brought to light atypical control sequences of past applications, operational limitations in sizing of piping that resulted in excessive energy consumption, and discrepancies in drawings and documents. Following a review with the control solutions consultant, our team was able to propose, develop and implement a flexible design arrangement in line with facilities engineering objectives, while minimizing disruption through detailed assessment and understanding of existing plant operations. These steps are critical in steering our efforts towards real capital savings and delivering value to our clients.
Decarbonization
A growing trend toward low carbon energy production. This entails reducing the carbon footprint of a district energy plant and dependence on non-renewable energy sources such as coal, oil or natural gas for energy generation. Environmental regulatory bodies and design standards are increasingly stringent, but the push towards low carbon energy production is also driven by consumer demand, particularly on the west coast in North America. A good example is a decarbonization project at an existing fossil fuel gas burning steam plant where electric steam boilers will be used to offset production of the existing boilers. This involves an additional high voltage feeder arrangement with the local utility to support the infrastructure upgrade. A substantially reduced carbon footprint is expected throughout the life of this electric boiler plant that operates year-round. HH Angus is also increasingly incorporating the use of district energy steam to hot water energy transfer stations, heat pumps, geothermal, and low temperature ambient systems to support low carbon design initiatives. Look for a future white paper on heat pump applications.
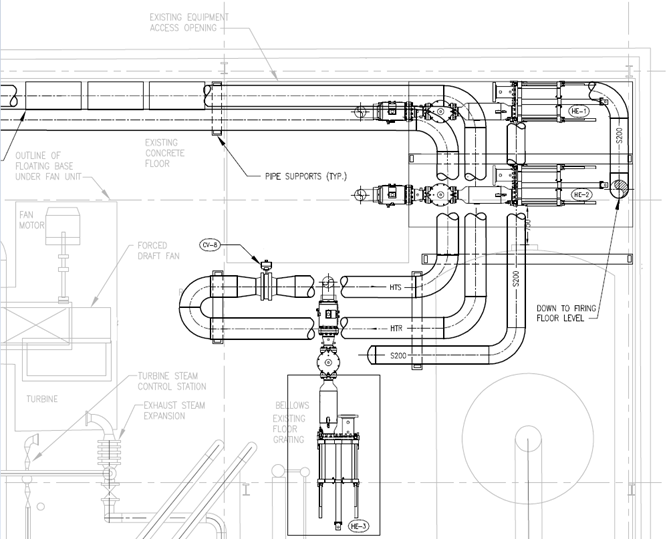
Another solution to meet the decarbonization goal is the introduction of thermal microgrid systems which utilize renewable energy sources, with thermal storage and heat recovery to satisfy low-temperature district heating requirements. As renewable energy sources are used, the carbon footprint is significantly reduced in these systems; for example, geothermal can be used as a primary energy source as it uses thermal energy from the ground, which is then distributed through the use of heat pumps. Thermal storage systems may also be installed with these systems to optimize the system and provide protection during load fluctuations.
Implementation
Beyond the conceptual, HH Angus generally seeks a collaborative approach to best utilize key areas of expertise between consultants, owners, and installation contractors during detailed design and construction. For example, market fluctuations in commodity pricing, such as steel—commonly observed post-pandemic—has impacted the construction industry’s supply chains, which poses significant risk to project stakeholders’ budgets and timelines. HH Angus has adapted workflows accordingly to better manage risk and unknown conditions, with cost reviews being referenced across various sources, including HH Angus’ active projects. The feasibility of early procurement of major equipment is reviewed with owners and suppliers to mitigate concerns relating to fluctuations in construction cost and timeline.
Building Information Modeling
Increasingly, the use of reality capture such as Matterport 3D scanner provides a much improved channel and engagement platform for communication of client needs and clarity in design scope, while enhancing and bridging gaps in technical subject matter otherwise difficult to describe during the project planning and development process.
Use of REVIT tools minimize the risk of drafting errors and improves engineering documentation quality through automation of equipment schedules, sections, and schematic drawings. Site scans further improve collaborative efforts between team members, dimensional accuracy during equipment layout, and clash avoidance, while facilitating client discussions and proposed solutions in detail.
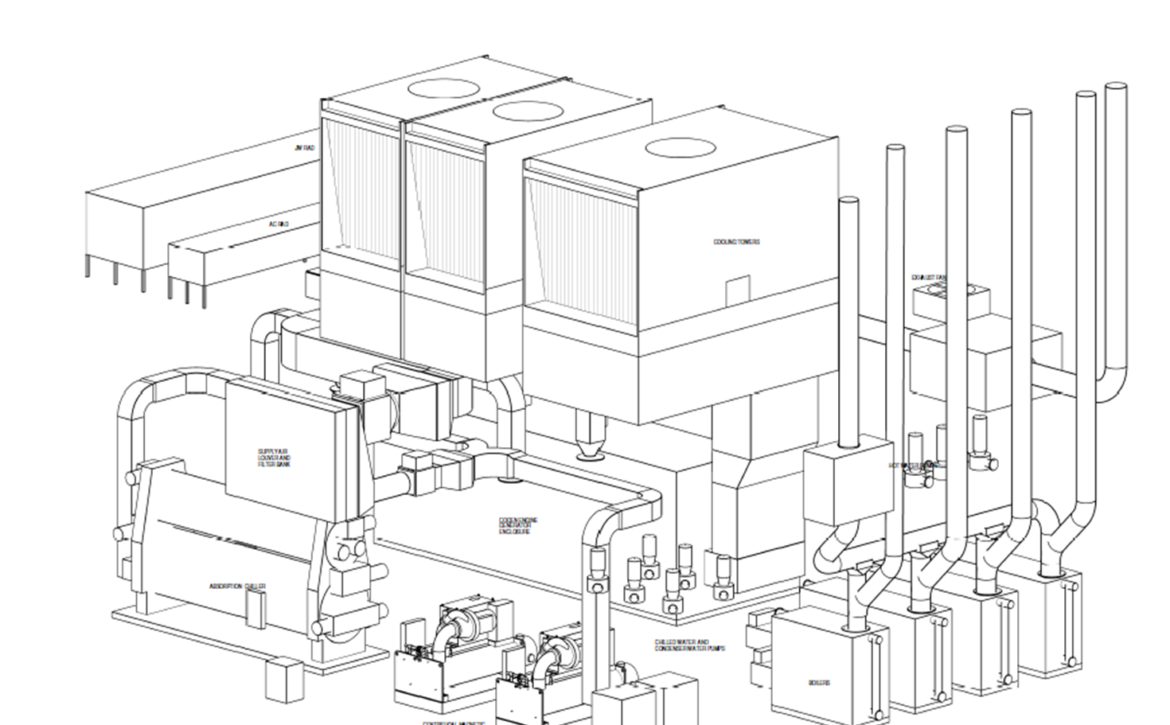
Conclusion
For most building infrastructure, energy consumption contributes significantly to operational cost and risk. Energy needs represent a recurring, long-term expense for building owners who can benefit greatly from proactive management. An energy master plan can provide the road map needed to guide scalable and effective approaches to achieve deep energy savings, improve resilience, reduce carbon emissions, and increase reliability.
Thoroughly reviewing and documenting a site’s energy systems, utility infrastructure, and future energy needs is the first step in creating an energy master plan. The next step is to combine this information and develop a forward-looking, holistic energy strategy focused on optimizing existing assets, hedging future energy risks, and further growth in sustainable options.
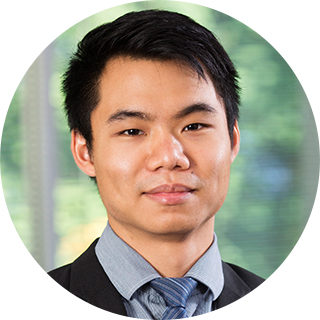
Justin Lau, B.A.Sc., P.Eng
Justin is a mechanical engineer in the Energy Division of HH Angus and Associates. He is involved with project development and detailed engineering design to help clients meet energy targets and carbon reduction objectives in numerous market sectors.
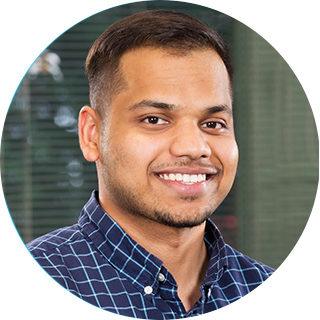
Sabari Manoharan, B.Eng., E.I.T.
Sabari is a mechanical engineering designer in HH Angus’ Energy Division. He is responsible for successful implementation of all aspects of design on low carbon projects under direction of senior technical staff.