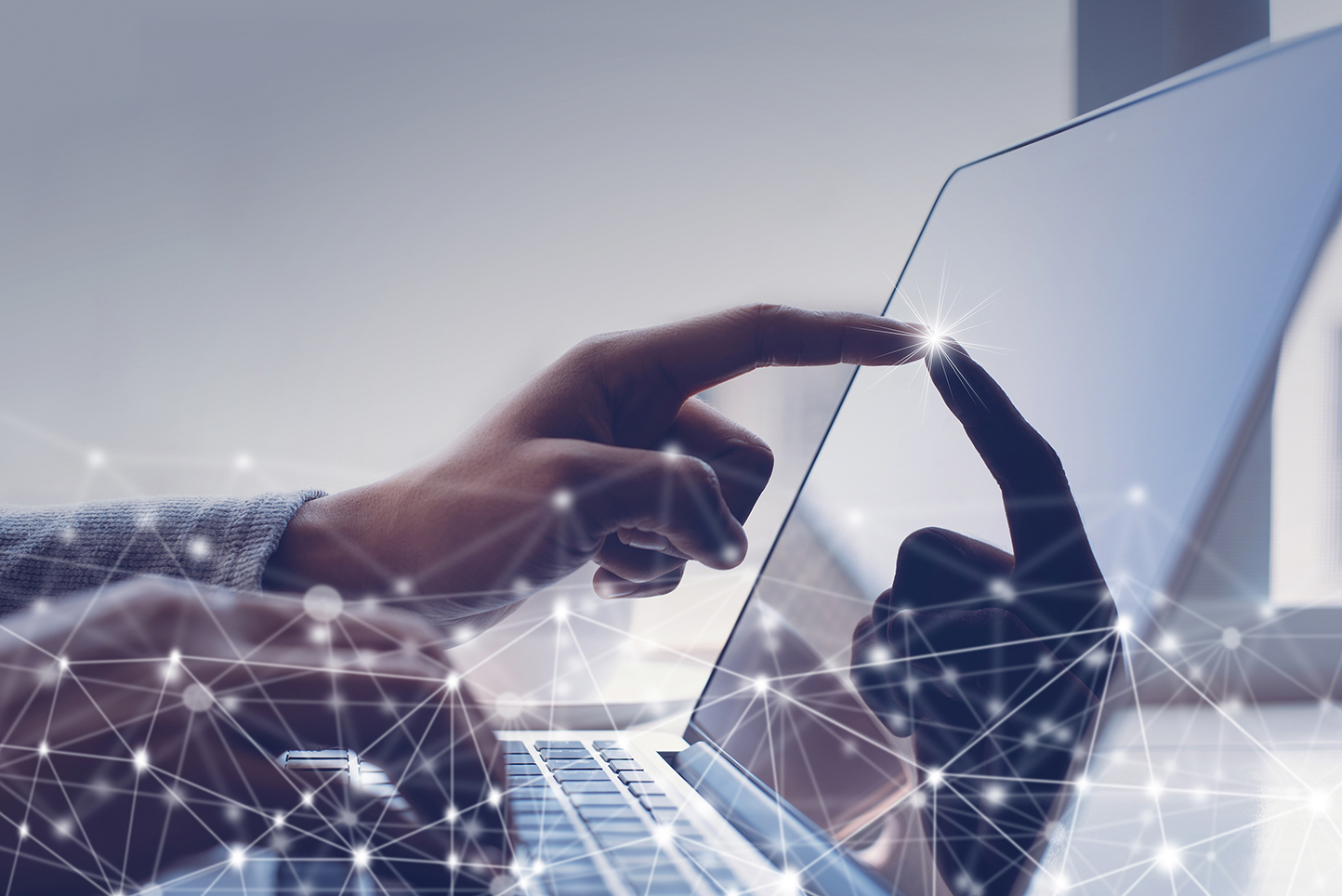
What’s Happening in Our Market?
Akira Jones, Director of Digital Services at HH Angus, was recently a featured speaker at the annual conference of the Ontario Society of Professional Engineers. His presentation (available below in both text and video) examines the drivers pushing greater adoption of new technologies and the impact of these on our clients and how we work, as well as the threats to our industry from non-engineering firms.
HH Angus has seen a lot of change in its 100+ years, from drafting on paper, the introduction of computers and CAD, the shift towards BIM, and now computational design. However, today’s rate and availability of technological change is unprecedented. HH Angus’ BIM team was born out of necessity to service a large healthcare infrastructure project. Initially, the team was created to help our designers with BIM-related activities and projects, which meant providing support using database-driven technologies associated with BIM, developing our reality capture and scan-to-BIM capabilities, and other tools around using Revit or BIM processes.
The Architecture-Engineering-Construction (AEC) industry has been slow to embrace productivity and technological advancements. Recently, the industry has been experiencing change through leveraging existing and emerging technologies in design and construction. BIM tools have become mainstream in our workflows, with increasing adoption of 3D imaging, estimating software, computational fluid dynamics analysis, computational modeling, and more.
What’s driving our industry’s embrace of technology and new processes? Escalating project costs are a major factor. This typically flows back to consulting engineering firms through pressure for lower fees – do more or the same work for less. This can be an opportunity if we use new technologies to improve efficiency, improve workflows, provide novel solutions, and improve the quality of the solutions we deliver. Projects are also increasing in complexity, with design teams being more multidisciplinary, which requires greater collaboration and more quality assurance. BIM has helped with improving efficiency and collaboration within the firm and across project teams. For existing buildings, advances in 3D scanning technology have allowed us to quickly scan spaces and convert into REVIT models, which are far more accurate than 2D drawings or dated as-builts, and can be shared with project teams in any location.
Sustainability and resiliency are also driving adoption of new technologies. With buildings contributing nearly 40% of greenhouse gases, the AEC sector can make a positive impact by designing and constructing buildings more sustainably. Reducing use of materials with high embodied carbon, decarbonizing heating and cooling systems, and leveraging smart buildings technologies to realize more energy efficiency are some of the emerging technologies we can employ.
Over the last decade, our team has explored digital twinning, smart buildings/IoT and cloud technologies. Through pilot and research projects, I've had the opportunity to work with folks with new skillsets that will be valuable for future consulting engineers. There is vast potential to leverage, to really supercharge our ability to solve problems for our clients.
Our industry is changing rapidly in other ways, not just in technology adoption. Disruptive technologies are attracting non-engineering businesses into the AEC market. Both Google, with their Sidewalk Labs division, and Microsoft have made significant investments in developing services and products focused on the built environment. Tech start-ups focused on real estate technology seem to be emerging almost daily. And large, established consulting firms like Deloitte, KPMG, and Accenture have created practices and market offerings around smart buildings. We are in the era of smart buildings, IoT, big data and cloud computing, which are the ‘bread and butter’ for these technology and large professional service firms. A tremendous amount of technology and data collection will be critical for smart cities – representing opportunities for optimizing building operations as well as new revenue streams. These firms are very interested in providing their solutions to our clients.
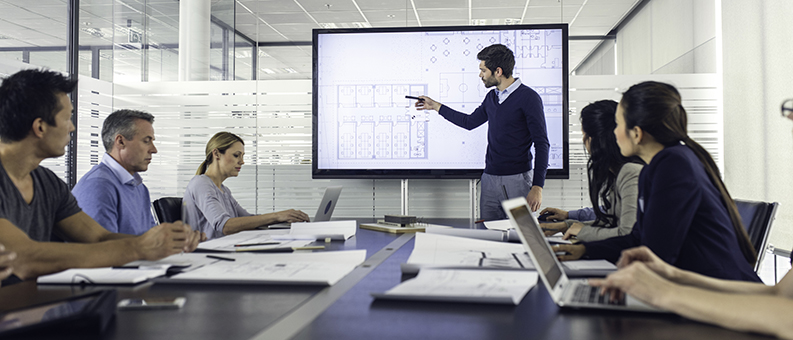
What is the impact to consulting engineering?
How will these changes impact consulting engineering?
- The way we do our work
- The solutions we offer to our clients
- New and enhanced services we provide to the market
Consulting engineering is in the process of reorganizing itself, not just because of technological advancements, but also market pressures, evolving client expectations and generational change.
Firms that embrace technology to improve operations are better able to scale, manage and attract talent, and improve productivity and profitability. We generate a wealth of data for projects – from design specifications, standards, products, materials, schedule, budget, facilities operations and more. Cloud computing, IoT, digital twins and machine learning are some of the technologies capable of automating routine tasks, quickly iterating design options and generally streamlining workflows.
The growing role of technology has blurred the lines between traditional consulting engineering and technology work (i.e. software and application development). With digital and other technologies at the heart of much innovation and how projects are designed and delivered, engineering firms are doing much more technology work – developing custom scripts for computational design, creating digital twins, developing a single plane of glass (dashboard) for BAS and smart buildings solutions. We’re often as likely to be designing and developing apps, prototypes, databases, cloud platforms as we are doing project management, construction admin, load calculations or other ‘traditional engineering’ tasks. The distinction between an engineer and a software solution provider or cloud expert are converging, because the future requires understanding of all these.
Clients’ expectations of engineering consultants are also changing, regarding how we solve their problems, and the types of consultants involved in design and construction. It may mean that non-traditional design consultants become involved – such as management consultants, tech start-ups or cloud computing consultants. Clients are more knowledgeable about artificial intelligence, robotics, automation and the Internet of Things (IoT), and are apt to hire engineering firms using these technologies to deliver better outcomes.
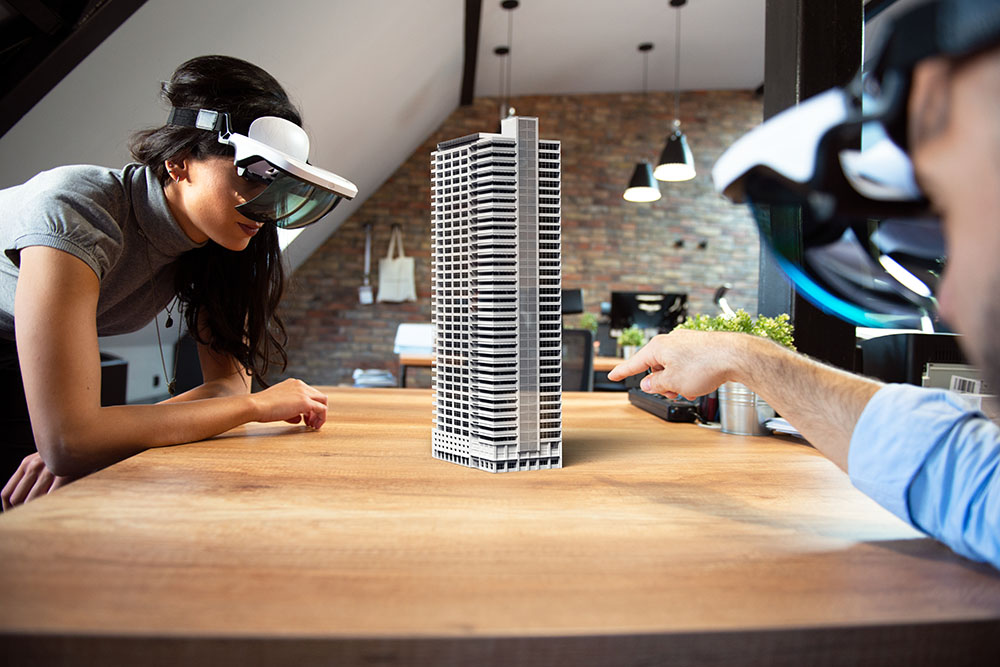
The Consulting Engineer of the Future
As in many other industries, the perspective on how we work has shifted between older generations and the more digitally savvy next generation. So, what kind of skills will this consulting engineer of the future need? Certainly, a critical skill set will revolve around software development. Programming and software development are skills that have become required in many industries; however, it’s relatively new within the AEC industry. It is not just the knowledge of how to program software, it is understanding what software is capable of, from both specific applications to enterprise scale. Engineers don’t necessarily need to know how to code or write software, but they will need to understand how software can be applied to solve problems.
Understanding how software can improve processes will be an increasingly important key skill for consulting engineers. It is a unique skill in and of itself. It’s extremely important to understand how to use software to automate processes, or iterate in ways that would typically take a human significantly more time in a standard or traditional approach.
The application programming interfaces (APIs) for design software such as REVIT or Rhino affords the opportunity to easily automate routine tasks, which is made even easier with visual programming languages such as Dynamo or Grasshopper. Not only can we use these APIs for simple automation, but also for more sophisticated processes, such as running parametric simulation for spaces loads, or extracting data from our models to validate design assumptions and inform future designs.
There are tools available that improve how we conduct our work, validate our assumptions and use data to inform our future designs. Beyond that, there is a major opportunity for consulting engineers to provide unique solutions to clients. It might seem a stretch to say every engineering consultant is going to become a software developer/provider; however, by going beyond simple automations and engaging in research partnerships and pilot projects, we can provide valuable insights, and have the potential for creating something novel and valuable to the client. For example, today one can use predictive analytics on a data set to get a high-level picture of future patterns. But employing true machine learning could take that same data set to generate a system model that learns as new data points are created and potentially predicts future outcomes. How would this work with the built environment? In a current pilot project, we are collaborating with a commercial client and a large university to generate a purpose-built digital twin using existing BAS and IoT data sources to model how building systems behave in real life. The building owner’s facilities team can then predict how changes to the physical environment or building systems would impact operations or occupant comfort.
The application of machine learning to our workflows is not in the distant future - it can be applied effectively today in appropriate use cases.
IoT is a technology that allows us to gather data about how buildings, equipment and people behave, and it’s one that consulting engineers should become more familiar with. It has quickly become a mature technology in some sectors, like mining and manufacturing, with rapid uptake in other sectors like healthcare and commercial. As we design buildings, we need to understand how to leverage IoT devices and properly implement them. And it does not stop at understanding IoT devices; we must also understand how data is gathered, architected, stored, analyzed and presented so that we can derive actionable insights. So, cloud computing comes into play, and building skills in technologies such as Amazon Web Services (AWS), Azure, Google Cloud and others will be important.
At HH Angus, we have found that engaging in pilot projects with clients is an effective way for us to understand the impact of these technologies to deliver better project and business outcomes for our clients, while also building our own competencies in these emerging technologies. We embarked on an internal pilot project to implement IoT sensors in our own office to gather environmental and space occupancy data, and then developed our own app and dashboard to view insights. In another pilot project, we partnered with a healthcare client on the implementation of 5G and IoT sensors in an ER setting. On other recent pursuits, we have developed strong expertise in designing Automated Guided Vehicle (AGV) systems. The common theme is that we are employing and developing skills that are atypical of traditional engineering and with greater emphasis on new technology hardware and programming.
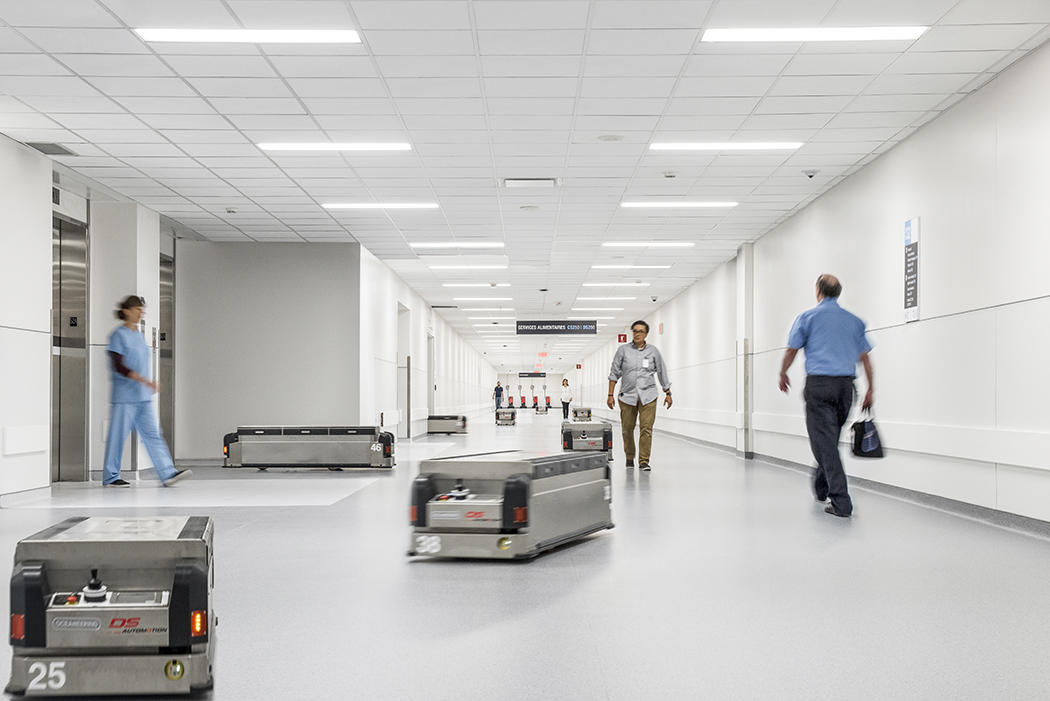
Summary
The world is constantly evolving and sometimes change can be faster that we expect or want. Clients are adapting and they prefer consultants who are also adapting and able to deliver better value. To be relevant, consulting engineers need to expand beyond traditional roles and expectations. Fault lines are already emerging that will separate those who embrace technology and change, and those who cannot.
It's important for consulting engineers to invest in developing a range of skills. While it can be daunting to explore new areas, the reward is worth it. Through HH Angus’ research initiatives and pilot projects mentioned previously, we have enjoyed success and learned some key lessons:
- Gain a better understanding these emerging technologies and when and where they can be most effectively employed
- Create a work environment in which we can work more efficiently
- Enable a culture where entrepreneurship and ideas are valued and new services can emerge
- Better engage staff and attract new talent
Ultimately, we're in the business of solving more than just our clients’ infrastructure challenges – we also should be helping them discover opportunities to do more with their real estate assets and supporting their business goals. By expanding our skills so that we can understand and leverage emerging technologies, deliver novel solutions, become more efficient in our own processes, and better leverage their building assets, consulting engineers can continue to be trusted advisors to our clients.
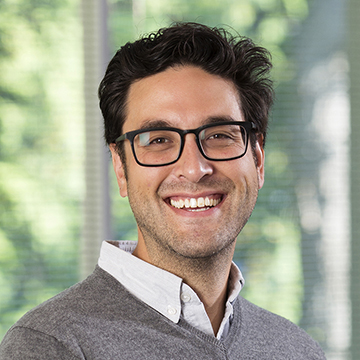
Akira Jones, B.Sc., P.Eng., LEED AP
Director, Digital Services