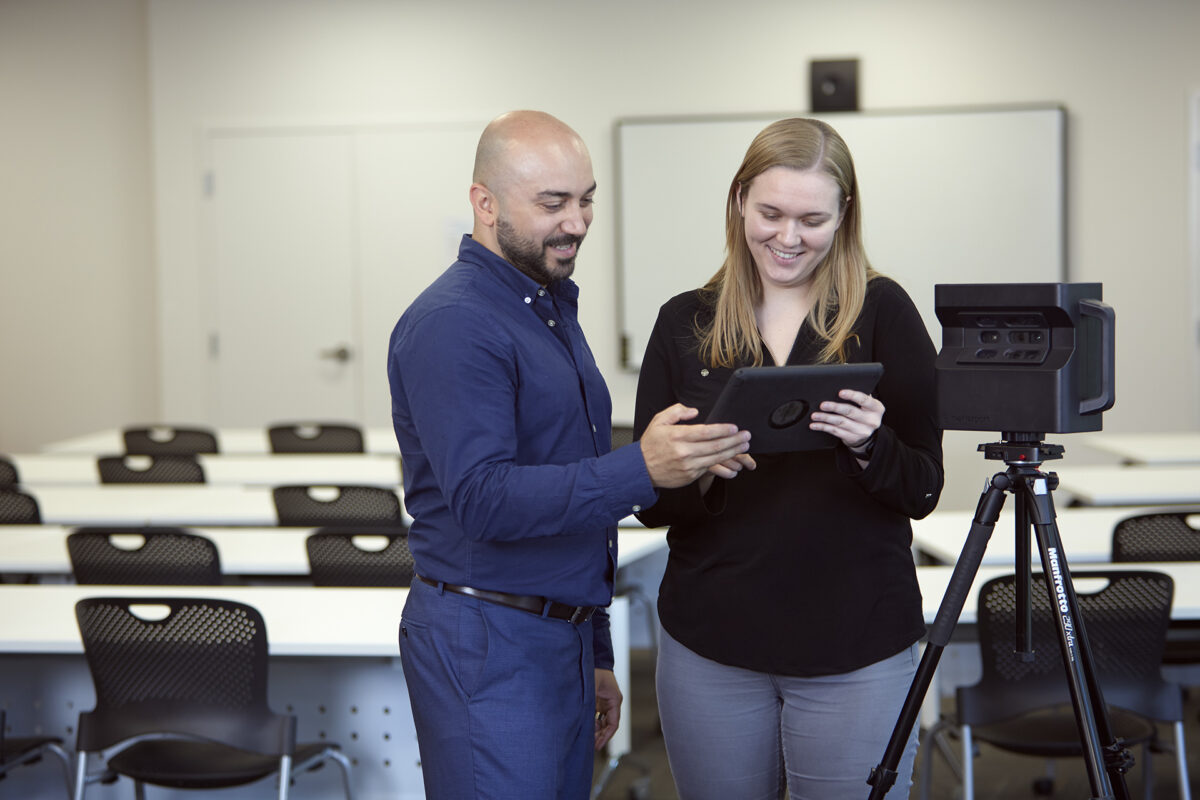
Enhancing the BIM process with 3D image capture
Prior to the digital age, engineers conveyed their work and collaborated through hand-drawn designs. Building inspections and site investigations were conducted using a tape measure, a pencil and graph paper. At that time, drawing by hand was the only way to accurately capture existing information and to develop new designs.
Advances in technology have since changed the way that engineers capture and convey information. Digital cameras replaced hand drawn sketches during site investigations, and computer-aided design programs, such as Sketch-up and Revit, replaced the practice of drawing by hand. These new tools lead to increased accuracy, efficiency during site investigations and design, and the ability to digitally store and reuse information.
As technology continues to develop, so too do the methods for which buildings are designed and their data is captured, stored and used. Revit has become the industry standard for accurately modeling new buildings and their systems in 3D – more commonly included as part of Building Information Modelling (BIM). Even with BIM tools, designers and engineers are confronted with days of laborious and time consuming BIM modeling due to hand-drawn measurements, notes and 2D photographs from the site which add to the length of the project schedule and budget. New technologies are emerging, including lasers and infrared beam scanners, which allow for data-rich information of existing spaces to be rapidly captured, stored and digitally explored.
HH Angus uses a Matterport 3D Scanner to capture existing spaces which is then converted into 3D models for our clients. We have used these models in a variety of situations and continue to push what can be accomplished by having an accurate, to-scale 3D model of existing buildings and their systems as well as the value it can help us deliver to our clients.
The value of 3D image capture and modeling for existing buildings projects:
1. Capture site information faster and accurately
An accurate 3D model of existing conditions (typically within a centimetre of hand measurements) through image scanning the space. This process can usually be done up to 60% faster than traditional hand measurements. Because the image scanning captures information in a point cloud, this information can be automatically imported into Revit, eliminating the need for manually entering hand measurements and reducing the time of creating the Revit model by nearly half. The BIM model can be provided to consultants, potential bidders and contractors allowing them 24/7 access. When the site information is available in a digital and 3D photorealistic format, the result is fewer questions during RFP periods and fewer site visits are required.
2. Capture spaces during construction
The ability to use image scanning to capture site information and create a 3D model at any time during construction can be very useful in a variety of situations. For example, recording a snapshot of progress for contractor payment draws or to provide enhanced construction documentation to project stakeholders. Capturing the space when services are installed but before walls and ceiling are in place can be a great reference for reference for future maintenance and renovations.
3. Digital representation of spaces and assets
While many newer buildings may have accurate construction data stored in a BIM model which is helpful for future renovations, expansions or retrofits, many older buildings were built before CAD and BIM was common. 3D image scanning can quickly create digital models of these existing buildings by vastly streamlining the time-consuming process of collecting building details by hand measurements and then subsequent manual entry to create a BIM model.
Information can also be associated to a building space or asset within a 3D model such as a piece of mechanical equipment or electrical panel. Information that can be mapped to an asset can include the O&M manual, last service date, information from a building condition assessment, and other types of information. This can be done for an existing facility without requiring a complete BIM model.
4. Remote access for facility managers
A 3D model can allow facility managers to ”walk” through building areas and read equipment information from a nameplate remotely with only an internet connection required. It could also be done from a mobile device such as a smartphone or tablet. The ability to access this level of detail remotely can be extremely useful for troubleshooting and for organizations that have multiple sites spread out geographically.
5. Future Developments in 3D Image Scanning
Currently, point cloud data generated in 3D image scanning still needs to be converted into useable data to create a BIM model. This is typically an additional and fairly manual process. With advancements in machine learning and artificial intelligence, research is underway where algorithms can be used to automatically identify structural elements and interior furnishings, elimintating the need for a person to manually identify these items in the process of converting a point cloud file to a BIM model. This could even further streamline the process allowing engineers and designers to focus on value-added tasks rather than losing time on determining the status of the existing building condition.
3D Model in Action
HH Angus has captured and converted over 165 of our clients’ spaces to 3D models. We were engaged by St. Joseph’s Healthcare Centre to redesign and renovate the Nuclear Medicine and MRI areas of their Digital Imaging Suite. During the first site visit, HHA scanned the area using the Matterport Scanner to create a 3D model of the space. This model has since been used throughout the design and tender process of the project, and will continue to be used in the construction phase.
Authors:
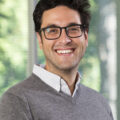
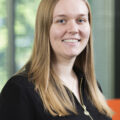