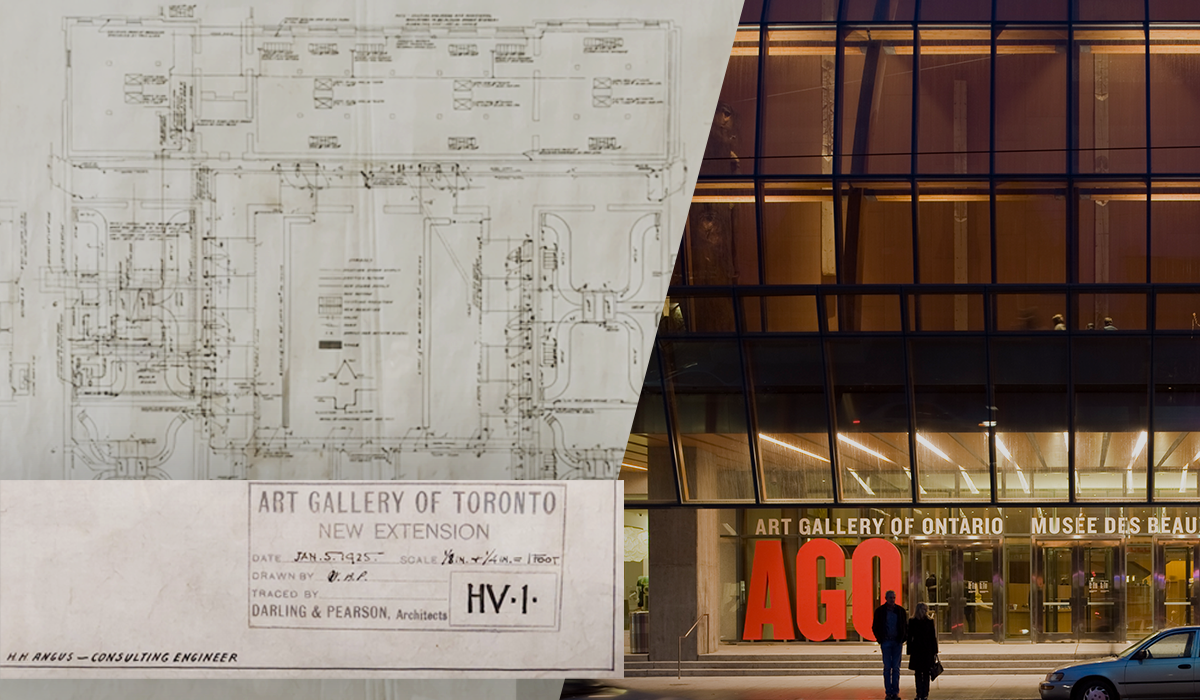
The Art Gallery of Ontario (AGO) is celebrating its 125th anniversary this year, and we congratulate the AGO on this important milestone.
Today, the AGO is considered one of the largest art museums in North America with a collection of over 120,000 works of art. Currently 583,000 ft2 and growing, the gallery ranks among Ontario’s premier cultural attractions, drawing over one million visitors annually. But like most well-established cultural icons, its origins were far more modest.
The Art Museum of Toronto began life on July 4, 1900, at 165 King Street West. A few years later, it relocated to ‘The Grange’, a large home bequeathed to the Museum and still part of the AGO today. In 1919, the name was changed to the Art Gallery of Toronto. Admission to its three galleries was 25 cents. In 1920, the Gallery hosted the first exhibition by the newly formed Group of Seven. In 1966, the name was changed again, to the Art Gallery of Ontario, underscoring the growing importance of the gallery.
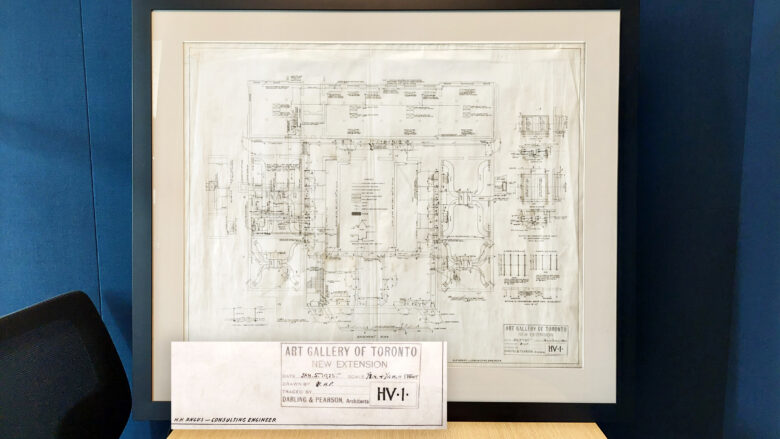
HH Angus began providing consulting services to the AGO in 1925, creating design and engineering drawings for its first HVAC system and we subsequently worked on numerous projects for the gallery. For its comprehensive 2008 ‘Transformation AGO’ project, we acted as the mechanical engineering and vertical transportation consultants.
The Transformation project was designed by world-renowned architect Frank Gehry and included 97,000+ ft2 of new space to increase viewing areas by 47%, plus 187,000 ft2 of renovations to the existing space. Innovative design considerations were implemented for phased construction, installation and commissioning, and in the integration of the new and existing spaces.
‘Transformation AGO’ Project - Engineering approaches to protecting and preserving works of art
To achieve the desired functionality and aesthetics of the project, the client and architectural team proposed three main challenges:
- Phased construction to allow continued regular service to galleries
- Sophisticated mechanical systems to meet the specific needs of each gallery to be physically remote from the galleries for aesthetic reasons
- Integration of new systems with existing base systems.
The building was divided into 70 zones, with each gallery space fitted with dedicated sensors controlling the individual equipment in remote rooms.
Frank Gehry’s design aesthetic provided some interesting challenges for the engineering design. Adrienne Cressman, HH Angus’ Lead Mechanical Engineer for the Transformation project and currently Director of our Project Management Office, recalled that “the attention to detail on the part of the Gehry team was unparalleled. No direction was passed on to the design team until it had been modelled in physical 3D by the architectural team. There was also a heightened level of coordination with curators at the Gallery for our scopes of service, regarding the specific requirements of individual exhibit areas.”
Among the requirements, the mechanical systems had to be virtually invisible, so that normal HVAC connections were not seen by visitors to the galleries. Executing this design feature was complicated by the fact that, to avoid the risk of water leakage, which would be a serious issue for the collection, all mechanical rooms were situated in no-impact locations well away from gallery spaces. For the same reason, no equipment was housed above ceilings in the galleries. According to Tom Halpenny, HH Angus’ Principal-in-Charge of the Transformation project and current Executive Vice President, the architectural vision for the project dictated a custom approach not only to our system designs but also for equipment specifications: “We made a number of changes to our specs in order to meet Frank Gehry’s design vision; for example, for the HVAC system, we replaced standard air supply and return vents with air slots that appear as a line at the top and bottom of the gallery walls, as these were considered to be a more aesthetic alternative. Even sections of the fire sprinkler system, wherever these could be seen by visitors, were fitted with stainless steel piping rather than the normal standard steel piping.”
A reduction in fresh air intake during off-peak visitor hours simplified the HVAC system control by reducing the influence of changes in outside air temperature and humidity. This approach helped considerably in providing more stable environmental conditions for the artworks. Tom Halpenny noted that, “the success of HH Angus’ design had two important results for the AGO: first, being able to guarantee the stability of the HVAC system allowed the gallery to attract touring exhibits of rare and fragile artwork and artifacts that have very specific and stable environmental conditions; second, the reliability of the HVAC system was recognized by the AGO’s insurance provider such that the gallery was able to secure better terms.”
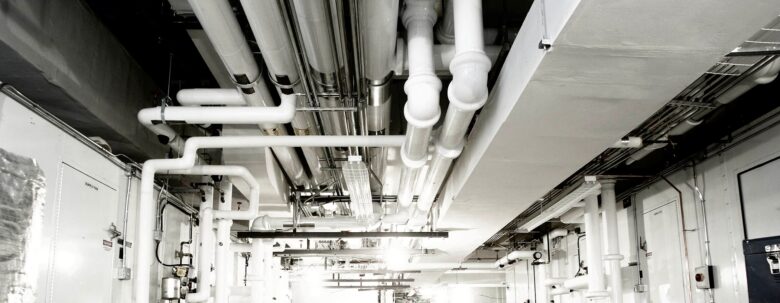
Integrating the new mechanical systems with the existing building systems made an already complicated assignment even more complex technically. The form and arrangement of the new and renovated spaces resulted in an irregularly connected multi-level project. Interconnected atrium spaces required careful attention to detail to ensure that mechanical services were concealed and that service access routes were maintained. The prediction of temperature- and pressure-induced airflow patterns and the arrangements to segregate returns for balancing of the return air to the individual air handling units all required complex analysis.
The vertical transportation system included three passenger elevators, one high-capacity freight elevator, two material lifts, and two platform lifts to accommodate persons with physical disabilities. All elevators are of the “traction” type, with special design features to accommodate large groups and the travel distances required.
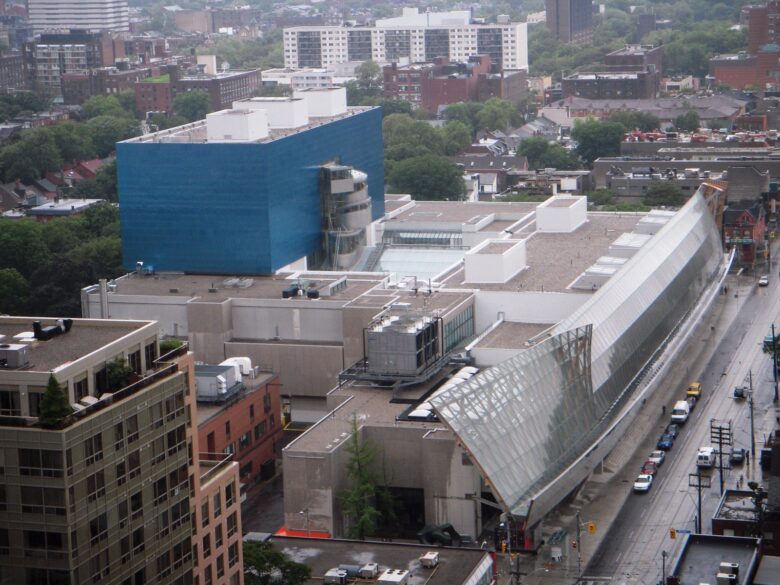
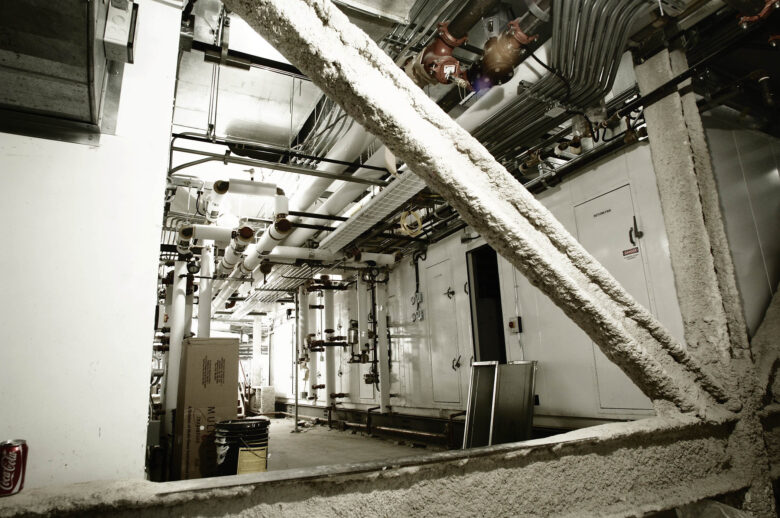
We’re very proud of our association with the Art Gallery of Ontario and wish them many years of continued success!
For more information about the AGO’s 125th anniversary events, click below for their website: AGO125.