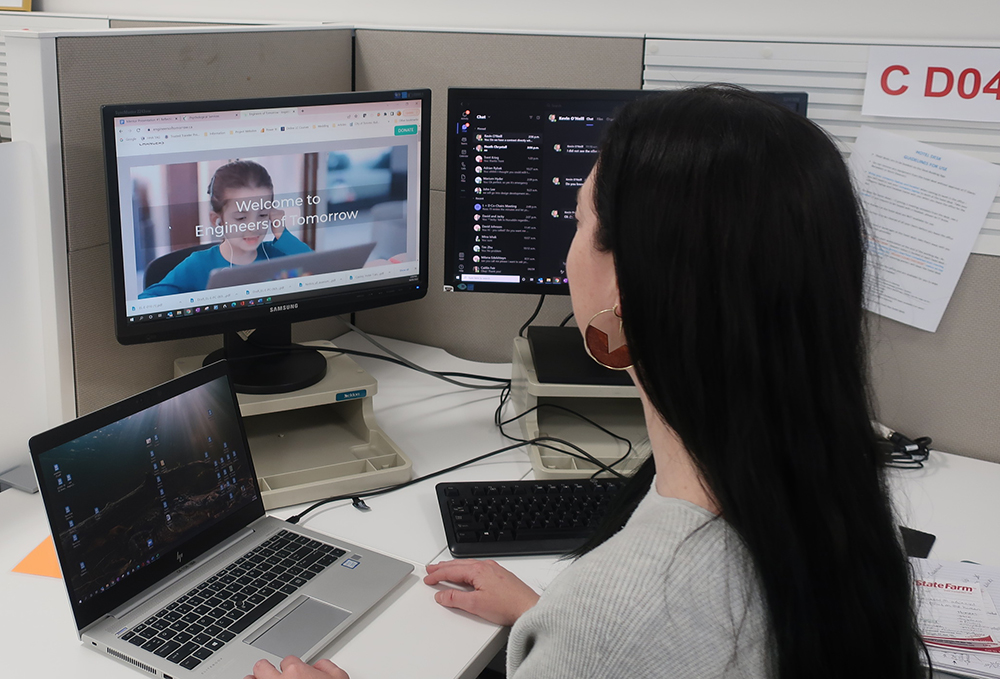
Engineers of Tomorrow is a non-profit volunteer organization dedicated to inspiring the next generation of problem solvers and game changers. According to their website, “We believe in the power of great engineering outreach to shape the future.” Their program pairs professional engineers with students working on an engineering problem. When Caitlin Campbell saw their call for industry volunteers, she accepted the challenge.
The opportunity appealed to Caitlin, because it was exactly the type of project that she would have enjoyed at that same age.
“The project is the Engineers of Tomorrow Future City Experience and this year’s theme is ‘Living on the Moon’. The students have to think about how humans could live on the moon and what they would need in terms of food, power, and infrastructure. They use this information to build a physical model of their city. I wanted to get involved to help the students work through any problems they encounter while also promoting engineering as a possible career. Many young people don’t know what engineers do and therefore don’t consider it as a possible career choice.”
As a mentor to a Grade 7 class, Caitlin first met with the students to talk to them about her work and life, and why she went into engineering. She was also able to offer advice on project management; the teacher identified the current challenge as possibly the biggest project the students had yet undertaken and felt they needed help planning their time. Caitlin will meet with the students a few more times before virtually attending the final presentations next month.
Caitlin sees her mentorship as a win-win proposition: “The students get to work on an engineering problem, dive into technical research to find out what’s needed to live on the moon and meet real-life engineers to learn about engineering. It’s impressive to hear what they have learned about the moon in such a short period of time. And I get to promote engineering as a career while also giving back to the community!”
If you would like to learn more about Engineers of Tomorrow, click here.
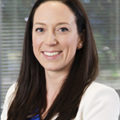
Caitlin Campbell, P.Eng., LEED® AP, LC
Caitlin is a Senior Electrical Manager in the Commercial Division of HH Angus. She has been involved in a wide variety of cultural, institutional and commercial projects involving all stages of design, construction and commissioning.