
Interest in and implementation of Automated Guided Vehicles (AGVs) has become more common in healthcare capital projects, with clients recognizing the value these systems can bring in terms of productivity, safety and efficiency. While AGVs have been in use for some time in other industries, a hospital AGV system differs from these in that its ability to consistently achieve performance parameters and throughput is heavily influenced by both the users and the technical performance of the system. In hospitals, a large number of users from many different programs (eg., food service, pharmacy, logistics) must interact with the system. The ability to prevent backlogs and ensure critical deliveries relies on strict adherence to the AGV schedule, cart removal timing, and coordination with a central operator. The technical performance of the system is highly influenced by the space programmed, elevator capacity, programming and system capabilities, which differ among vendors.
Some factors driving increased adoption of AGVs by healthcare clients include:
- The increased floor plate associated with new hospital builds, as a result of a higher ratio of single-patient rooms and improved circulation space
- Improvements in sensor technology that have greatly enhanced the performance of AGVs in areas such as collision avoidance and environment recognition, navigation, fleet management, material tracking, and the ability to conduct detailed diagnostics and maintenance of individual vehicles
- A greater need to improve sanitation (cleanliness) in the hospital environment, as well as the increased priority to disinfect various spaces (i.e. UV robots) – also supporting minimizing hospital acquired infections
- Increasing labour costs, and a focus on workplace injury prevention
Benefits that can be realized include:
- Improved productivity. AGVs can reduce supply chain management costs and deliver reliability of supplies compared to non-automated methods.
- Availability. AGVs can operate on a 24/7/365 basis. Advances in battery technology have significantly shortened battery charging times, resulting in AGV systems that can be designed to be on call throughout the entire day to respond to demand. This also means that distribution can be scheduled for off-peak hours.
- Reduced damage to facilities. With improved collision detection and environmental recognition, well designed AGV systems can almost eliminate damage to doors, walls, elevators and other structures in the hospital while also ensuring safety as they are programmed to never collide with other objects (including people).
- Predictability. Because AGVs are programmed to operate to a schedule, it becomes easier to schedule complementary resources within the same delivery periods.
AGVs are currently being used for a range of tasks in hospitals. These include pick-up and delivery of meals, waste, linens, sterile supplies, medications, and other supplies. The systems are quite sophisticated and are capable of activating and navigating automatic doors, signaling and navigating elevators (both dedicated and shared), delivering carts for cleaning, activating cart-washing systems, and are able to safely navigate busy spaces, such as hallways and elevators, that are shared with humans. The use cases for AGVs increase as we discover more needs they can support!
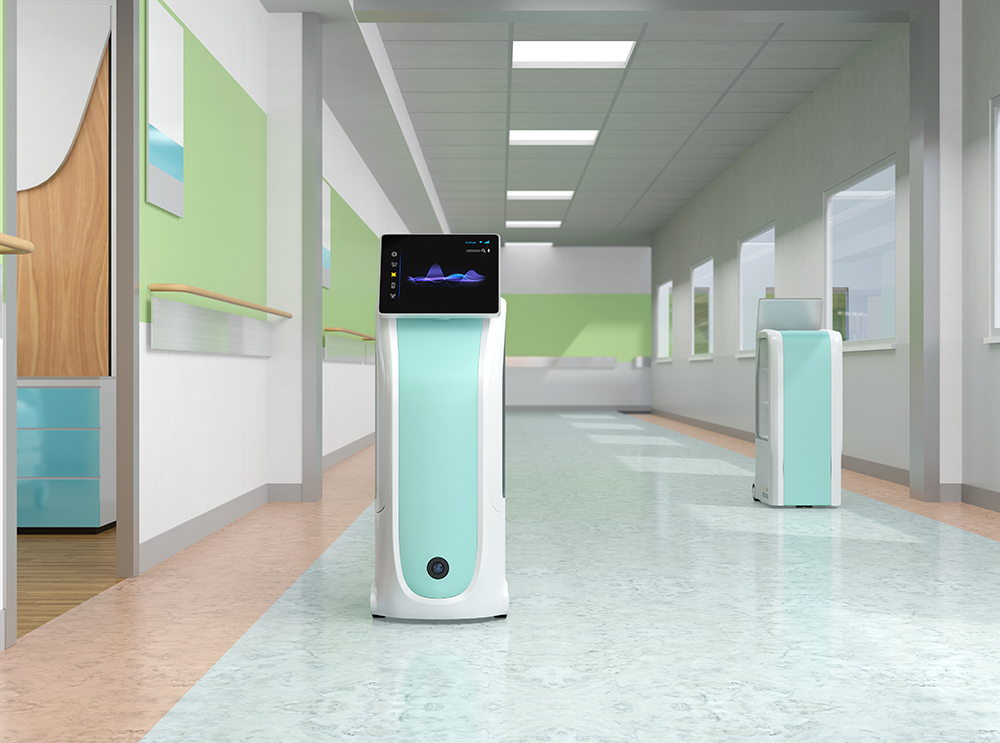
Designing AGV Systems
In designing AGV systems for healthcare facilities, HH Angus has the specialized expertise and experience to produce exceptional results in a highly technical process that requires insight and knowledge of healthcare facilities operations and logistics, vendor experience, and a depth of networking and integration expertise. Our Angus Connect Division is a Canadian leader in delivering forward-thinking and robust digital and technology strategies, along with design and implementation for healthcare and other facilities.
At the outset, our team examines our clients’ overall business objectives and operational goals. Some of these include improved supply management for clinical services, timely medication dispensing, and reduction in portering and housekeeping steps to deliver supplies. Drawing on our clinical, building and AGV design experience, we collaborate with the client to understand their vision, and then contribute our deep knowledge of materials management, hospital flows and implementation of AGV systems to successfully tie together workflows and technical requirements. Taking time early in the design stage to fully understand the project requirements allows us to track changes in client requirements that can occur over the design and construction life of the project. Ensuring the operational assumptions and the AGV and hospital designs align with the overall goals of our clients is crucial to delivering a successful AGV system.
Through our extensive experience with the P3 (public-private partnership) model, both in proponent and compliance roles, we have developed some methodologies for success, which include:
Informed Decision Making Based on Clinical and Hospital Operations Best Practices
Our Connect team has significant knowledge of hospital operations, with the expertise of four clinicians who bring hands-on experience and consulting advisory on process flows. We also bring the knowledge gained from previous AGV and materials management work with key hospital clients, such as Providence Health Care for its New St. Paul’s Hospital, Alberta Health Services for its proposed New Edmonton Hospital, the Nova Scotia Health Authority for the QEII Halifax Infirmary Expansion, and SickKids Hospital as part of its massive Project Horizon Redevelopment project. Work on over 10 large-scale AGV projects globally has given us an in-depth appreciation for the technical and operating challenges our clients face when implementing an AGV system. Given the heavy clinical and operational implications of AGVs, clients have often extended our team’s engagement in order to provide comprehensive planning, design and compliance support.
By combining our clinical and technical skillsets and AGV knowledge, we were able to deliver a design that was highly commended by the hospital.
The significance of this was put into particular focus during our proponent role for the New St. Paul’s Hospital. We were able to support the hospital in defining their scheduling and operational assumptions, developed a well-thought out AGV design that recognized infection control and staff safety requirements, and applied LEAN design principles to optimize workflows, creating optimal efficiency for supply chain management across the site. By combining our clinical and technical skillsets and AGV knowledge, we were able to deliver a design that was highly commended by the hospital.
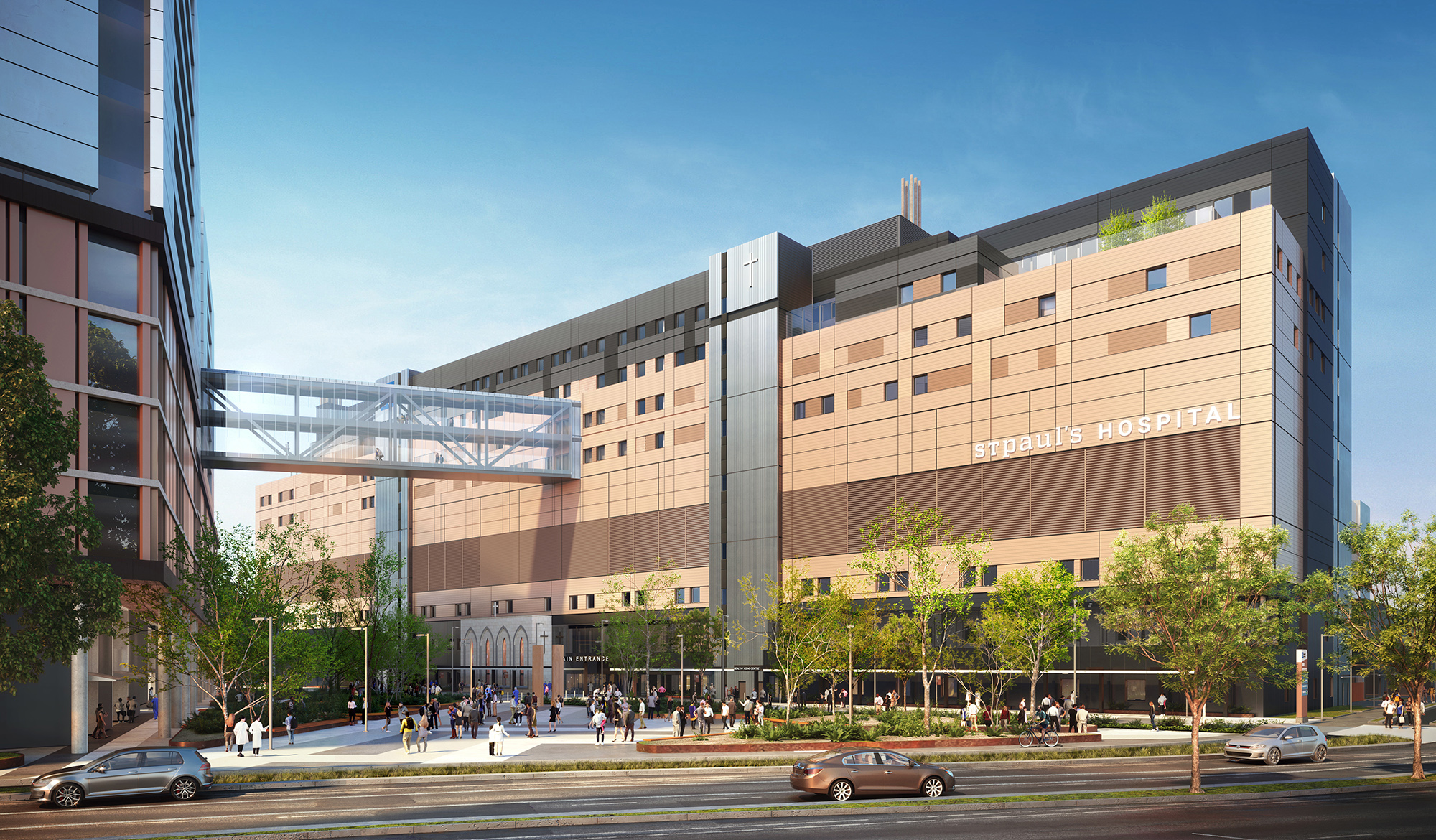
Elements of a Successful Implementation
A key to a successful AGV system is fully defining the operational processes of the AGV users in concert with the AGV system design. It is heavily dependent upon the human interfaces with the system, such as users respecting the design of the AGV Cart Matrix, prompt removal of carts upon delivery within the design time parameters, keeping all AGV areas free of obstacles, cart alignment, and having a central operator who monitors the system, proactively ensuring on-time deliveries and preventing system backlog. It is critical that the AGV and associated departmental operations, policies, procedures and staffing are reflected in the basis of design. In addition to these operational impacts, throughput of an AGV system is also significantly influenced by the design of the system, including space (including corridor widths, send/receive locations, and elevator lobbies), design of routes, the technical capability of the system, proper maintenance, WiFi, Local Area Network (LAN), elevator capacity, and integrations with the fire alarm and access control systems.
There are key differences between the implementation of AGVs in new builds versus existing sites. To name just a few, AGVs require wider corridors and pathways that support their turning radius’, specially-designed elevator lobbies that support not only the AGV navigation but also the cart-associated workflows, elevator type and capacity, battery charging locations, maintenance rooms and ‘send and receive’ locations within programs. The required space is driven by the AGV schedule and cart quantities, thereby making early planning critical to the end success of the system. While new builds can incorporate these requirements into early planning by ensuring the programmed space captures these, there are limitations to retrofitting existing hospital buildings with an AGV system due to narrow hallways, non-compliant elevators and WiFi limitations. While a thorough examination is needed to determine the options available to existing sites, there have been promising advances in Automated Mobile Robots (AMRs) that can help automate certain supply management services such as food, medication and supply delivery. AMRs do not require the same space requirements as AGVs and therefore can mitigate the need for renovations, making it a cost-effective technology for organizations interested in automating their supply chain management processes or implementing just-in-time deliveries.
Our team has experience developing AGV business cases, cost estimates, cart matrixes, specifications, and technical design on several large AGV-related projects, including SickKids, New Edmonton Hospital, Halifax Infirmary, and the New St. Paul’s hospital. These projects have provided us with a wealth of lessons learned and experience, allowing us to provide expert consulting for the successful planning, design, implementation, ongoing operation and maintenance of your AGV system.
For more information about how our AGV experience can help your healthcare facility, please contact:
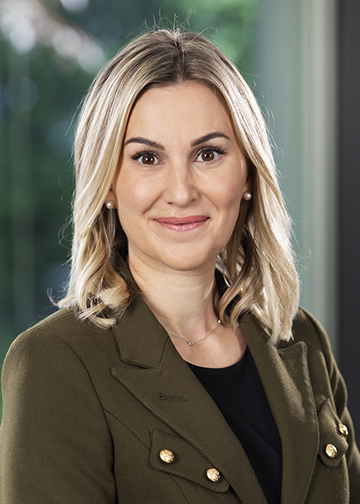
Megan Angus, RN, MBA, Lean
Division Director, Angus Connect
megan.angus@hhangus.com
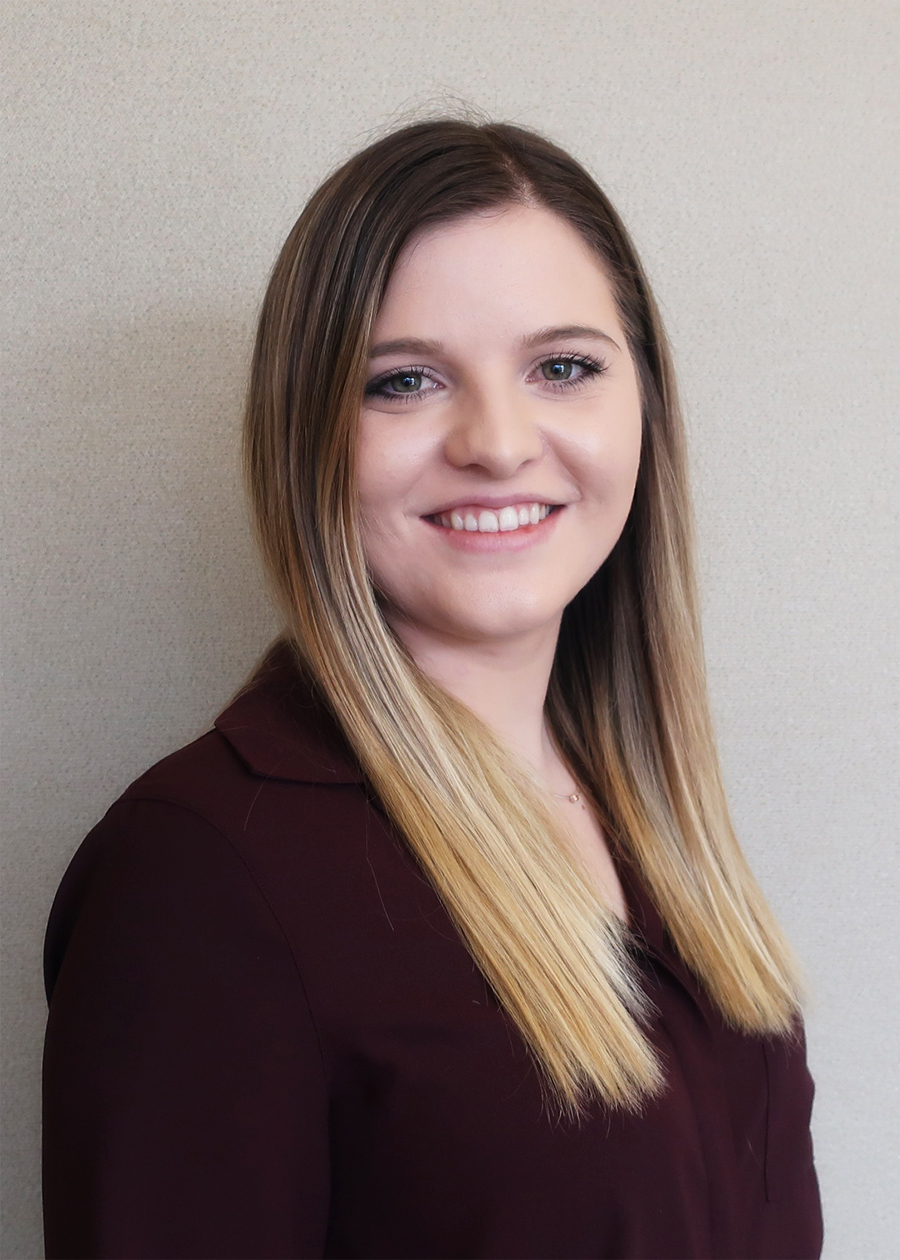
Robyn Munro, RN
ICAT Analyst, Angus Connect
robyn.munro@hhangus.com