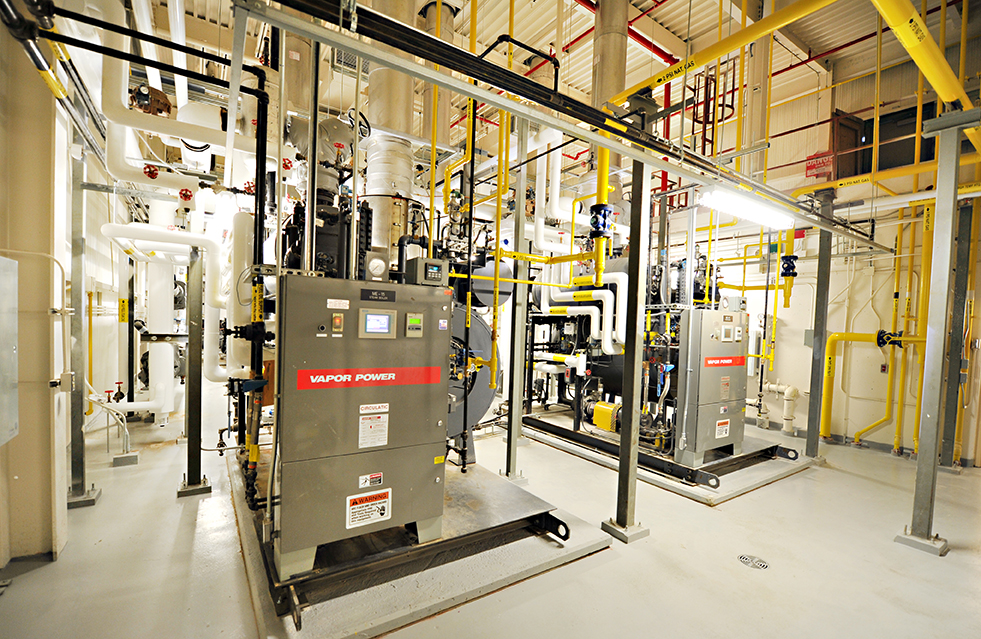
The following information is provided as a public service to Owner/Operators of heating oil and diesel fuel appliances and systems in Ontario. It addresses regulatory requirements and the Technical Standards and Safety Authority’s (TSSA) Code Adoption Document as they relate to Owner/Operators responsibilities for operation and maintenance of fuel oil systems, specifically for fuel tanks. Performing the required inspections and maintenance activities can improve the life expectancy of fuel tanks and reduce the risk of an unintended release of heating oil and diesel fuel to the environment.
ONTARIO REGULATORY FRAMEWORK
Technical Standards and Safety Act, 2000
Ontario Regulation 213/01 Fuel Oil
CSA B139: 2019 Series Installation Code for Oil Burning Equipment
In Ontario, the use and operation of heating appliances using heating oil, including stationary diesel engine-driven equipment, and their associated fuel and combustion systems, are subject to Ontario Regulation 213/01 made under the Technical Standards and Safety Act, 2001, S.O. 2000, c.16.
This regulation is administered by the Technical Standards and Safety Authority (TSSA), which is a not-for-profit, self-funded organization, with delegated authority from the Government of Ontario concerning specific technical safety subjects. TSSA inspectors and technical staff have authority as officers-of-the-court in regard to enforcement of the Act and its regulations, including access to private property for the purpose of inspection of safety-related equipment and systems.
Under this regulation, there are certain obligations imposed on the Owner/Operator of these systems. These obligations can be organized in the following categories:
- maintenance of these systems
- periodic inspection of these systems by a qualified technician
- record keeping
- actions to be taken when a leak of heating oil or diesel fuel is known or suspected
- actions to be taken when fuel systems are no longer used or are to be removed.
These operational requirements are specified in three documents:
- the regulation (O.Reg. 213/01), which can be found on the Ontario Government e-Laws website
https://www.ontario.ca/laws/regulation/010213 - TSSA Code Adoption Document for CSA B139, available through the TSSA website https://www.tssa.org/en/fuels/fuels.aspx
- CAN/CSA B139 Installation Code for Oil Burning Equipment, available for purchase at CSA Group
https://www.csagroup.org/store/ or other on-line technical document retailers.
While the regulation rarely changes, the CSA standard is typically updated on a five year cycle. The TSSA then undertakes a code adoption review process, and issues a code adoption document which may include amendments to the adopted codes or standards.
O.Reg. 213/01 Maintenance Requirements
In respect to operation and maintenance of equipment governed under this regulation, the Owner of the equipment is to:
- maintain the appliance and associated systems in accordance with the manufacturer’s recommended maintenance procedure [O.Reg. 213/01, s. 8.(1)(a)];
- have those maintenance procedures evaluated every 10 years, and the maintenance procedures modified if determined to do so by the evaluation [O.Reg. 213/01, s. 8.(1)(b)];
- have the appliance or work inspected every 10 years by a person who is a holder of a certificate of qualifications for this purpose [O.Reg. 213/01, s. 8.(a)(c)] – in most installations other than residential, this means a person who holds a license as an Oil Burner Technician Level 1 (“OBT1”); and,
- maintain a copy of these inspection reports until the next inspection and report are completed [O.Reg. 213/01, s. 8.(3)]
TSSA Code Adoption Document for Fuel Oil
Through the TSSA Code Adoption Document for Fuel Oil, it amends CSA B139:2019:
- “Annex M – Operations” of CSA B139 becomes a mandatory requirement
- Adds additional requirements to Annex M concerning Owner/Operator environmental responsibilities.
In addition to the operations requirements found in Annex M, the additional requirements concerning environmental responsibilities describe:
- the actions the Owner or Operator of a fuel oil system must do when a leak is suspected or detected, or if a fuel spill occurs; and
- the actions that the Owner must do if an underground or aboveground tank is no longer used or is being replaced.
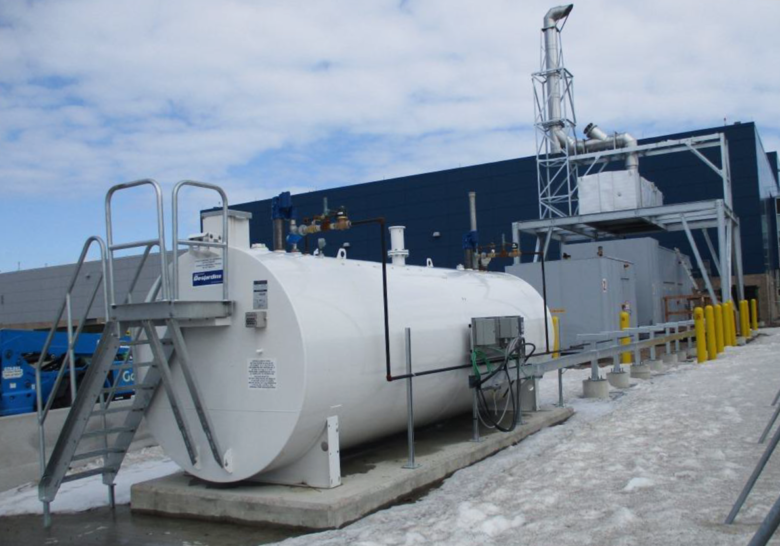
CSA B139:2019 – Maintenance and Operations
While this CSA standard primarily concerns the installation of oil-fired equipment and systems, it includes requirements concerning maintenance and operations of these systems:
- oil-burning equipment to be inspected and maintained in accordance with the manufacturers’ recommendations
- testing for presence of water at the bottom of a tank at least annually; if detected, the water must be removed
- visual inspection of oil tanks, tubing, piping and filters for leaks at least once per year, and replaced if leaks are found
- bottom outlet tanks (where the appliance is supplied fuel from a fitting on the bottom of the tank) are checked for proper slope and, if necessary, the tank pitch is corrected to slope the tank bottom towards the outlet
- periodic operational testing for detection of leaks in underground tanks and piping systems
- maintenance requirements of aboveground and underground tanks, and underground piping and piping sumps (Annex K)
- operation requirements concerning filling of tanks (Annex M) – this annex is made mandatory by the TSSA CAD.
Annex J of this Standard provides background information on the importance of testing for water in fuel tanks, and for the removal of water and oil-sludge from the bottom of steel tanks to protect them from internal corrosion.
Having a fuel tank that is “free and clear” of oil, sludge and other debris at the bottom of the tank will go a long way to improving the usable life of the tank.
For more information, please contact:
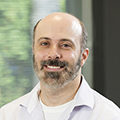
Peter Formosi, P.Eng.
Mechanical Engineer
peter.formosi@hhangus.com
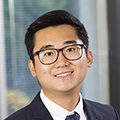
Anthony Ho, P.Eng.
Mechanical Engineer, Manager
anthony.ho@hhangus.com
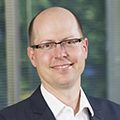
Craig Sievenpiper, P.Eng.
Associate Director, Technology
craig.sievenpiper@hhangus.com