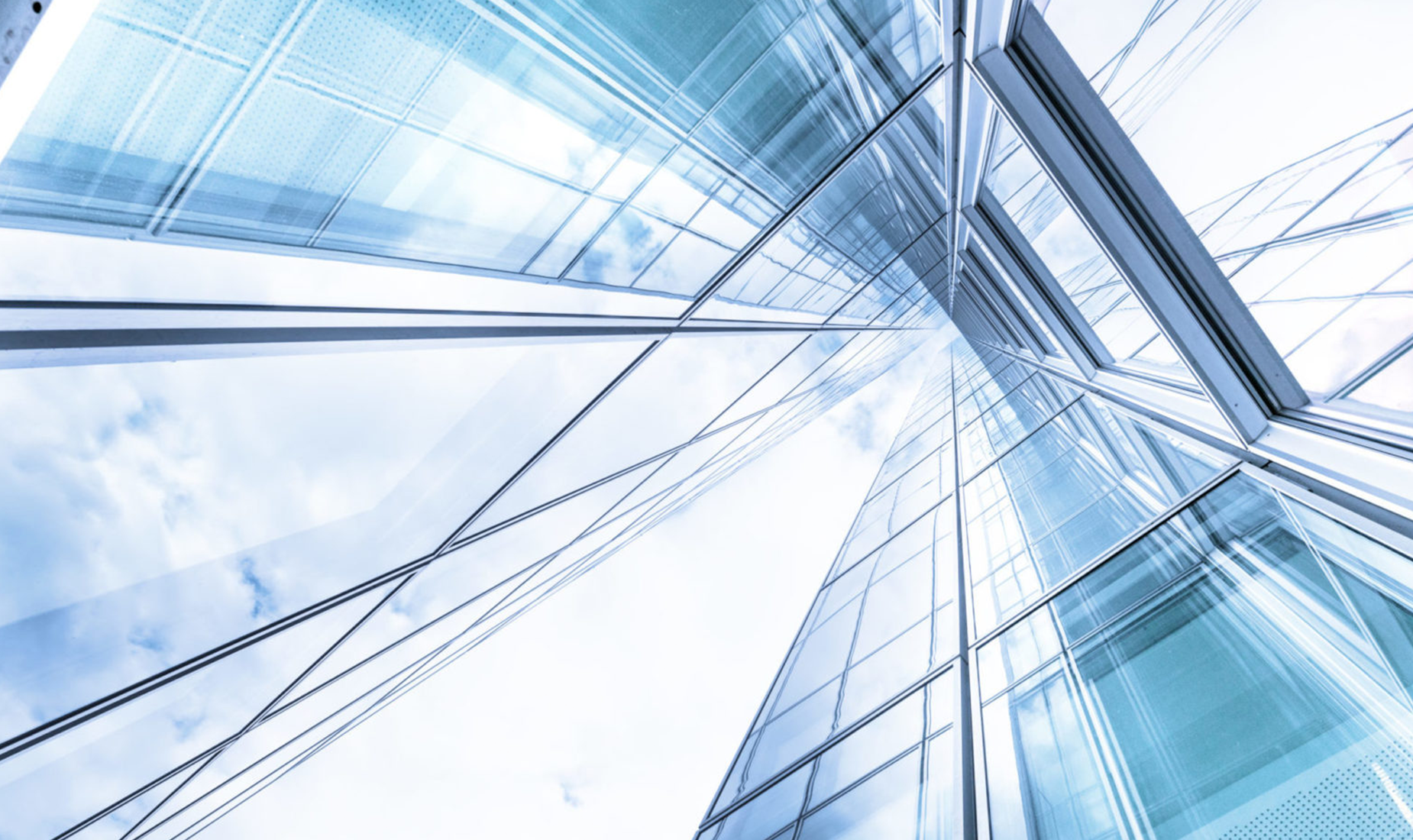
At this year’s The Buildings Show, HH Angus’ VP Operations & Director, Commercial Division, Kevin O’Neill, joined a panel with Kris Landon, Senior Director Construction, Enwave Energy Corporation, and Sean Smithson, Executive Vice President, Modern Niagara Group to share insights and strategies to improve the construction closeout process. The panel was moderated by Tom Coyle, Director, BTY Group. Here are some of Kevin’s key takeaways on construction closeout from the consulting engineering perspective:
Why construction closeout can be stressful
Closing out of a construction project is the culmination of all the hard work of the team to transfer a project to an end user. If the closeout is not completed properly, deadlines are missed, owners are upset, and costs spiral out of control. Closeout starts as soon as you begin working on a project, and it is important that you get ahead and stay ahead to avoid stress and lost profits for all involved. It is an essential component of the construction process – and can make or break an otherwise successful construction project.
How specifications help the closeout process
Specifications are as critical as constructability, schedule, and budget. It is essential that the specifications are edited and modified for each project and are read and understood by the builder and trade contractors. The specifications are written to define the scope of work, the owner’s requirements, the quality and performance of equipment, items pertaining to process and, in some instances, references to construction phasing. When it comes to construction closeout, specifications must be updated to capture the specific requirements for the project and for equipment, methods, and procedures that are to be generally followed. All of this helps to ensure a smooth closeout process. The specifications should outline:
- Shop drawing submission protocol
- Procedure for clarifications
- Specific manufacturers and specialty equipment
- Minimum testing requirements or 3rd party inspection
- Site review by the engineer including milestone reviews
Specifically for closeout, the specifications should also provide:
- A list of attic stock/spare parts to be turned over to the owner
- Outline of the general and specific training requirements for owner’s personnel
- A checklist of requirements for application for both substantial and total performance
- General and specific warranty requirements
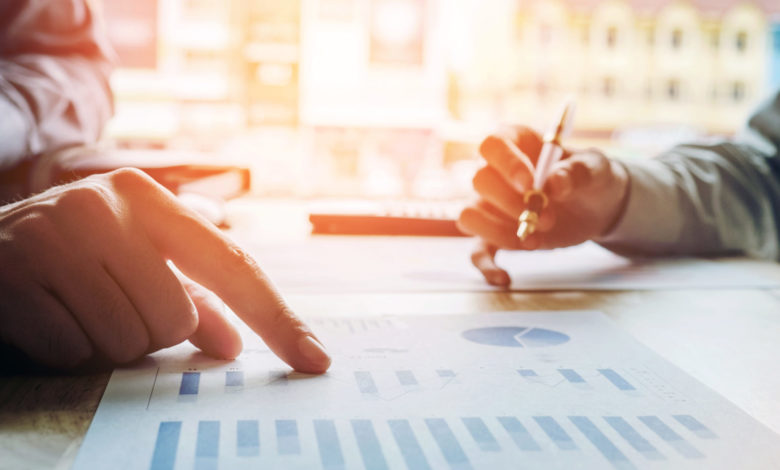
Energy performance or measurement and verification as a closeout deliverable
The expected or even guaranteed energy performance for new or renovated buildings is becoming more common, especially for P3 projects and projects that have received government funding. In this case, the specifications will outline target or maximum energy use or green house gas emissions and will refer to measurement and verification requirements post construction.
Obligations of the consultant or engineer in closeout
Engineers are required by local building codes to review the work performed when our drawings and specification are the basis upon which a building permit was issued. We conduct periodic reviews to ensure that the work generally conforms to the permit documentation; however, these can be augmented depending on the requirements of our service agreement with the client; for example, they may include:
- Recording any deficiencies found
- Reviewing reports of independent testing agencies, other 3rd parties, and installing contractors, such as fire alarm verification and sprinkler systems reports
- Interpreting plans and specifications when requested by the client or contractor and responding to RFIs
- Reviewing shop drawings and samples
When reviews should take place
Deficiency reviews are conducted when the work has been declared complete and are carried out on a sampling basis. The review by the engineer does not replace or supersede the reviews, deficiency lists, or punch lists developed by the contractor and sub-trades.
The engineer’s reviews can be milestone reviews, performed when areas are finished and in advance of services being concealed. We also provide reviews for occupancy as required by local codes and local inspectors, as well as providing certification for both substantial and total performance following complete application by the Contractors.
Requests for Interpretation (RFIs)
Engineers provide written clarifications when an RFI is submitted by the builder. The RFI process ensures that the intent of the specifications is clear. In the case of site issues that inevitably arise, the RFI process documents the exchange of information, and may trigger an adjustment to the contract in the form of a change order or site instruction.
The best RFIs are those that provide a possible solution to the issue at hand. These can even be submitted after the issue has been reviewed on site or discussed offline. However, RFIs for the sake of creating paperwork only distract and bog down the team.
It is important to include language defining the RFI process in your specifications. When HH Angus is acting in a sub-consultant role and providing Division 00 and 01 specifications, we must review what the prime consultant has prepared in this regard to mitigate and avoid nuisance RFIs described above.
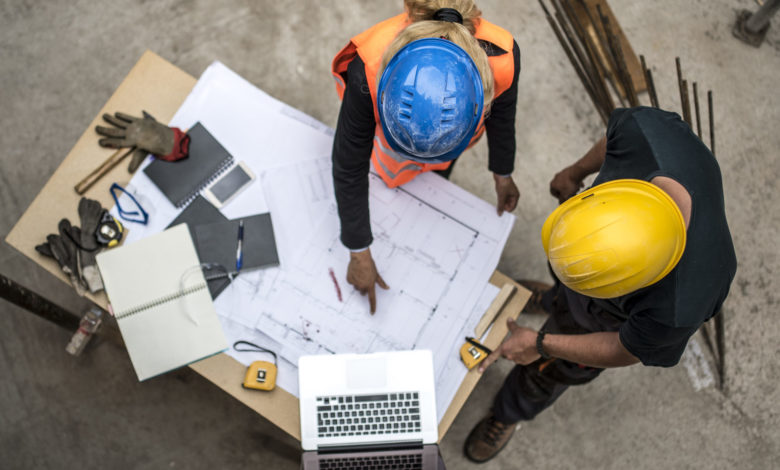
Role of the engineer during trade contractor execution of specifications
The obligations for the consulting engineer vary from project to project during the trade contractor execution of the specification requirements during closeout. In addition to a general review, the consultant may be asked to:
- Participate in planning for commissioning activities and to attend commissioning meetings
- Attend factory witness testing for major equipment
- Attend, on a sample basis, start-up testing of equipment
- Review test results for systems that may be turned over ahead of occupancy or substantial completion (plumbing, for example); and
- Monitor that as-built or record drawing information is being updated.
The consulting engineer also typically reviews the following documentation:
- O&M Manuals
- Shop drawings and 3rd party certificates, testing or otherwise
- Training records
- As-built documentation
- Warranty information and contact details
- Commissioning reports
- Final testing, adjusting, and balancing reports required for substantial performance
- BIM and Modeling turnover requirements
Closing thoughts about closeout stress reduction
Planning for construction closeout starts at the beginning of the project. The basis of the processes required to ensure a smooth transition from construction to closeout are outlined in our Engineering documents. However, this is just one part of a larger operation. Effective closeout will also highly depend on the experience of the owner and the trade partner. Regular communication of our expectations throughout the project assists with ensuring that we achieve the desired outcome; however, reducing stress is only possible when all parties are aligned to this common goal.
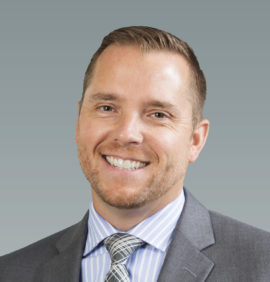
Kevin O’Neill
VP Operations | Division Director, Commercial
kevin.oneill@hhangus.com