Location: Eastern Canada
TD Bank
Living Roof“The Green Council [tenant representatives] has made it clear, through a commitment to action, that sustainability is a core value of TD Centre tenants.”
David Hoffman, then-General Manager. TD Centre
At the TD Centre’s iconic towers in downtown Toronto, TD Bank’s Living Roof offers both environmental benefits and some much-needed green relief from the usual hardscape views had by occupants of the Centre’s towers. It covers 22,000 ft2 and is planted with creek sedge grasses, a hardy semi-evergreen native species tough enough to survive the extremes of Toronto’s climate. Annual energy savings from the green roof are approximately $23,000. This is achieved by reducing summer cooling and winter heat loss by 25%.
HH Angus provided mechanical and electrical engineering for the green roof installation and irrigation system, as well as the project’s preliminary Feasibility Study. To avoid over-watering, the irrigation system features a sensor that shuts down the irrigation system when it rains. This sensor also reduces irrigation when the water received during previous rainfalls or irrigation has not yet evaporated.
In order to evaluate the requirements for mechanical and electrical design for the irrigation system, the ceiling plenum for the single story building below had to be surveyed. The storm water drainage system was original and would need modification and updating. The existing plumbing was modified to allow connection of the new irrigation.
Installation of dedicated electrical circuits and automated controls was required in order to operate the self-draining irrigation system. The controls were ceiling mounted with remote computer access. Rain spray heads, valves, head sensors, pattern nozzles, valve boxes, and stainless roof drains were incorporated.
Before the design could be executed, rainwater calculations were carried out based on Environment Canada data, along with spreadsheets detailing storm water run-off. These calculations assisted in sizing the storm water piping and locating roof drains and spray nozzles.
A roof leak detection system was also designed, along with a new soil pipe vent stack through the Pavilion roof, and a gooseneck conduit for rooftop wiring. A new replacement filter rack was added to the roof air vents.
SERVICES
Feasibility Study Plumbing Design | Mechanical Engineering | Electrical Engineering
PROJECT FEATURES
Size: 22,000 ft2 | Status: Completed 2015 | Annual energy savings through reduction in summer cooling requirements and in winter heat loss
LOCATION
Toronto, Ontario
KEY SCOPE ELEMENTS
Feasibility study | Rainwater calculations | Plumbing design with supporting mechanical and electrical design and engineering | Roof leak detection system
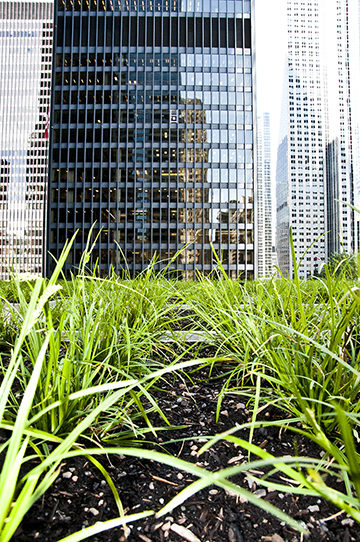
Sustainable
design
TD Bank's Living Roof represents tenant values and is a bold expression of collaboration in support of environmental stewardship
Honouring the design
The green roof’s grid pattern mimics Mies van der Rohe’s original design for the pavilion roof. This was done to respect the ‘designated heritage site’ aspect of the TD Centre.
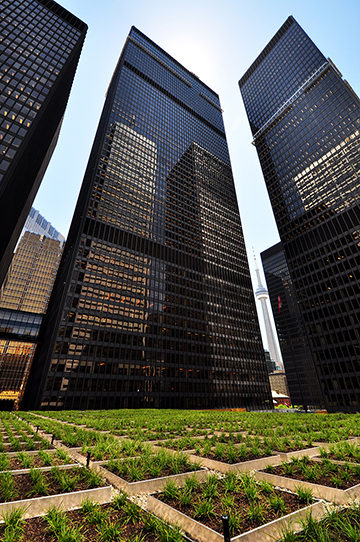
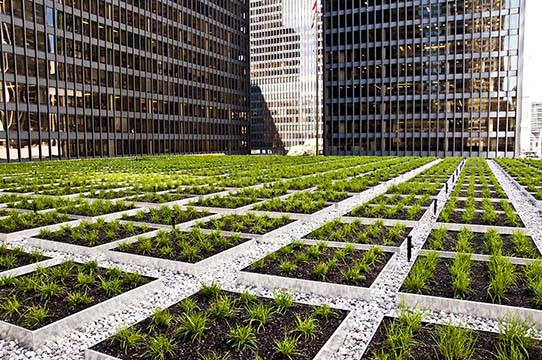
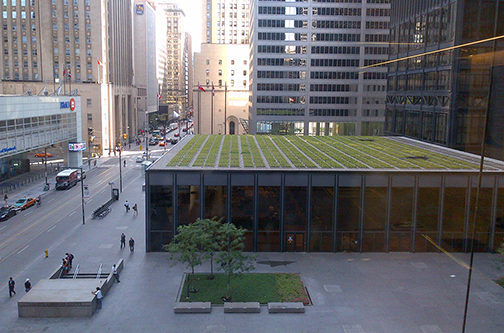
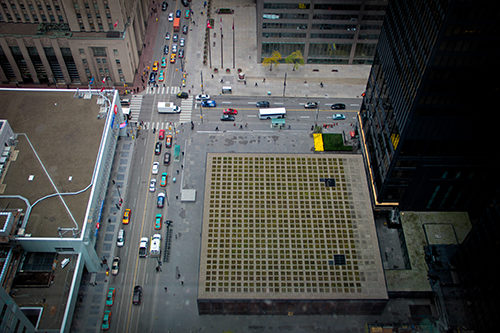
Images courtesy of Flynn Canada
Town of Havelock
Long Term Care ResidenceThe greenfield Havelock long term care facility features power redundancy for heating and cooling, allowing the residential facility to remain fully operational in the event that both power and natural gas are unavailable under emergency conditions.
This 91,000 ft2 greenfield residential facility is a mass timber project, consisting of 128 beds, a 5000 ft2 medical clinic and support spaces, including a kitchen, four dining areas, and communal spaces such as lounges and meeting/activity rooms.
HH Angus is providing mechanical and electrical consulting engineering, as well as lighting design. The mechanical design includes a new hot water heating plant and distribution systems. Rooftop units have been designed with energy recovery ventilators to recover heat from washroom exhaust. A chiller system will provide cooling for the units and boilers will provide the heat. The project is designed to meet CSA Z317.1 standards.
Our design team was challenged to provide suitable fire protection to this mass timber project, equipping the entire attic with fire protection service. In order to avoid excessive heat tracing, a nitrogen dry sprinkler system was used.
The lighting control system has been designed to provide the residence with optimal comfort through the use of daylight harvesting. A mixture of automatic, manual and scheduled controls were specifically designed to allow residents individual control while providing the owner the flexibility to identify areas where energy consumption can be reduced.
SERVICES
Mechanical Engineering | Electrical Engineering | Lighting
PROJECT FEATURES
Sice: 91,000 ft2 | Completion estimated for 2021 | Greenfield mass timber project | Power redundancy for emergency operation | 128 residential rooms | Medical clinic | 4 dining areas | Communal meeting spaces
LOCATION
Havelock, Ontario
KEY SCOPE ELEMENTS
Dual source boiler | Perimeter heating | daylight harvesting | Rooftop energy recovery ventilators | Designed to met CSA Z317.1
St. Michael’s Hospital
Barlo MS Centre
Canada has the highest rate of multiple sclerosis in the world; in fact, the disease is known internationally as ‘Canada’s Disease’. St. Michael's Hospital in Toronto is one of North America's busiest MS centres. It has been caring for people with MS since 1981, and now treats 7,000 patients.
The new Barlo MS Centre offers one-stop care, bringing together neurologists, nurses, social workers, neuropsychologists, physiotherapists, occupational therapists and speech therapists in a world-leading treatment and research centre for multiple sclerosis. The 25,000 ft2 clinic has been constructed on the top two floors of the new Peter Gilgan Patient Care Tower.
HH Angus’ mechanical scope for the fitout of the shelled space included ventilation, plumbing, medical gas, heating & fire protection, and controls. Our electrical scope covered power, lighting, communications and security.
Unique aspects of the project's design included: presentation to the client of a number of ventilation strategies to address the shortage of air supply available to the design, and a reworked ventilation strategy under a very aggressive schedule to redistribute and extend air to the clinic from an existing air handling unit that was previously feeding another floor.
Some of the project challenges included:
- The addition of a compounding pharmacy late in the design, for which additional requirements had to be vetted to meet NAPRA. The team took advantage of early works to investigate available shaft space for running new biological exhaust to the roof.
- Design activities had to be scheduled concurrently with testing and commissioning still underway at the time for the main Patient Care Tower.
- Ceiling construction and new structural constraints limited accessibility. The team used 3D imaging and Revit to coordinate all ceiling elements requiring accessibility, in order to integrate services into areas with wooden slatted ceilings.
- The team took advantage of early works to coordinate structural openings for future ventilation in order to limit ceiling interference for the fitout design.
SERVICES
Mechanical Engineering | Electrical Engineering | Lighting | Plumbing | Communications Systems | Security Systems
PROJECT FEATURES
Size: 25,000 ft2 | Status: Completion 2021
LOCATION
Toronto, Ontario
KEY SCOPE ELEMENTS
Two floor clinic fitout | Variety of room types and functions | Custom smoke venting and fire alarm zoning to accommodate feature staircase

Achieving the design vision
We worked closely with the architect to modify the existing fire alarm zoning and smoke venting strategy in order to accommodate a new mezzanine on Level 17. This allowed the architect to achieve the design vision for the feature staircase without the use of smoke baffles.
Variety of functions
The space includes a variety of room types, including exam rooms, gym, medical infusion centre, group physiotherapy studio, auditorium, cognitive lab and a pharmacy.
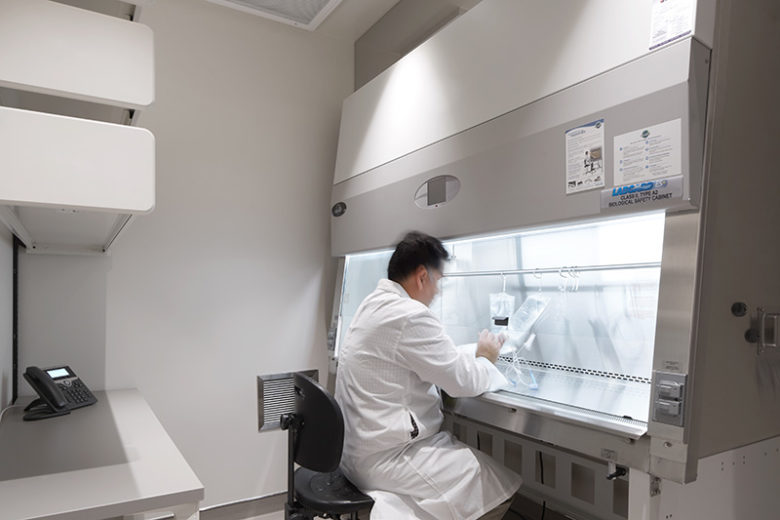
Click here for the St. Michael’s Hospital video feature on the Barlo MS Clinic.
Mirvish Village
Central Utility Plant
Mirvish Village is reimagining a 4.5 acre section of Toronto's Bloor/Bathurst neighbourhood, including the former site of the the iconic Honest Ed's store, a beloved Toronto landmark. Featuring four high-rise, one low-rise and twelve heritage buildings*, the mixed-use site will be home to more than 2000 residents.
HH Angus is working with Creative Energy Developments to provide mechanical and electrical engineering services for the Mirvish Village central utility plant, which includes a combined heat and power plant (CHP), a boiler plant, and a cooling plant. The CHP plant will include an 800 KW generator set with auxiliaries and heat recovery system. The generator is expected to run continuously to provide power to the complex.
Heat recovery consists of two systems: High Temperature to provide heat to buildings, and Low Temperature to provide additional heating for a winter snow melting system and swimming pool heating. The boiler plant will include installation of four condensing hot water boilers, with the option for two additional boilers in future. All boilers will have an output of 3.1 MW.
The cooling plant will include installation of two water-cooled chillers, operating at 1200 tons each. One chiller is a magnetic bearing chiller with variable frequency drive (VFD), and the other is a centrifugal chiller with VFD. As well, two cooling towers at 1200 tons each will be installed on the roof.
Central distribution piping from the plant will provide hot water and chilled water to multiple energy transfer stations, with heating, cooling, and domestic hot water heat exchanges for each building within the complex.
The photo-voltaic solar system will have a capacity of 103KW, 480V. HH Angus is providing direction for locating the installation, coordinating with the PV supplier for modeling the panel direction and angle for optimal PV output, developing technical connection requirements with Toronto Hydro, and identifying requirements for parallel generation with the central utility plant.
We also assisted the client with a successful incentive funding application. Ultimately, the incentive was not applicable due to schedule changes, which meant the project could not meet the incentive deadline.
* The World Architecture News Awards
This international organization recognized Mirvish Village with a Bronze Award in their 2023 world-wide competition. The project won in the category of 'Future Projects'. According to the judges, "Integrating old and new, small-scale buildings and towers, it proposes a dynamic, dense and diverse micro-city with the perfect scale to enjoy as a pedestrian."
Renderings courtesy of Westbank Corp.
SERVICES
Mechanical Engineering | Electrical Engineering
PROJECT FEATURES
Status: Completion 2022
LOCATION
Toronto, Ontario
KEY SCOPE ELEMENTS
Combined Heat and Power Plant | Boiler Plant | Cooling Plant | High Temperature and Low Temperature Heat Recovery Systems | Photo Voltaic System
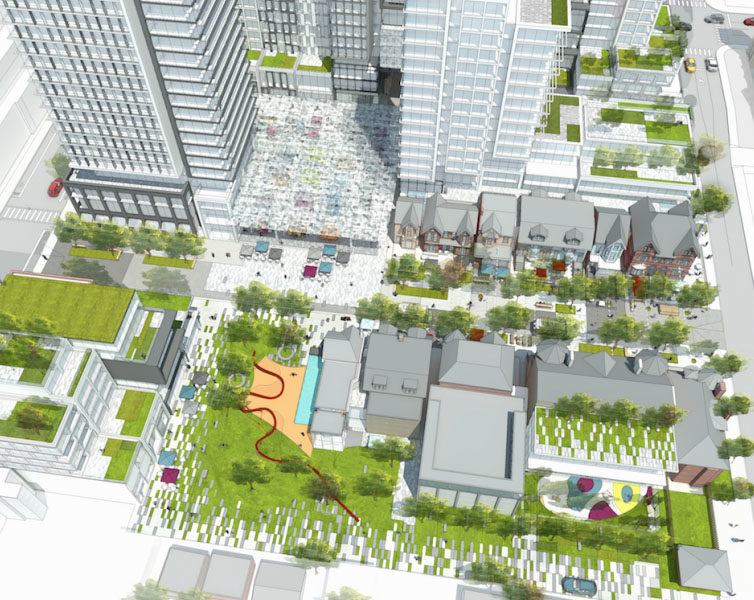
Metering Strategies
Our scope also included developing thermal and electrical metering strategies within a microgrid system, design of operation for gas-fired emergency generators in electrical peak shaving mode, and the design of a roof mounted PV solar system.
Sustainable design
Mirvish Village is being designed to meet LEED® Platinum ND standards, and will feature sustainable transportation options.
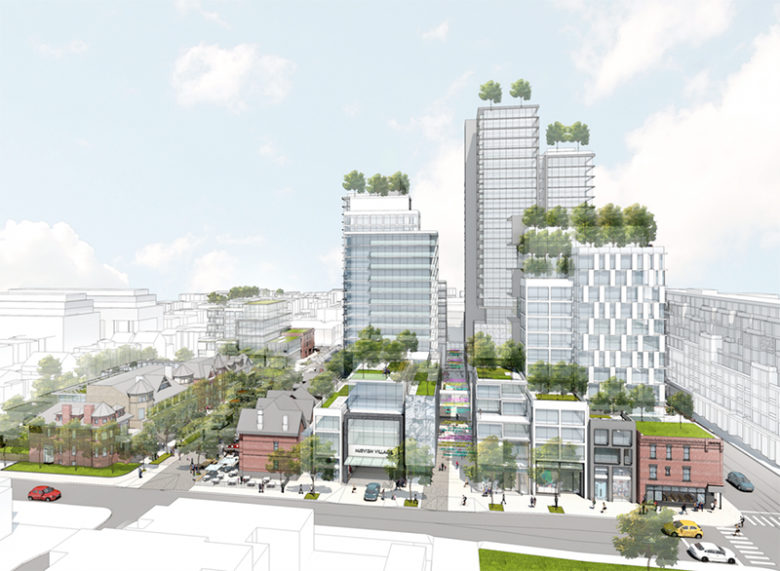
Toronto Transit Commission
Easier Access Program - Subway Station UpgradesThe TTC’s ongoing Easier Access (EA) Program is making public transit more accessible for customers. The entire subway train fleet is accessible, and more than half of Toronto’s subway stations are wheelchair and scooter friendly.
HH Angus has been providing vertical transportation consulting and mechanical and electrical engineering to the TTC since 2010, as the transit system implements EA accessibility upgrades. This involves the design and construction of new elevator systems, as well as changes to the electrical and mechanical systems needed to accommodate the addition of EA upgrades across the subway system.
At the Wellesley Station, for example, two new elevators have been added. The work to support this upgrade included hydraulic, electrical, mechanical, structural and architectural components, along with the detailed project coordination aspects related to renovations.
Some of the challenges associated with the EA renovations include emphasis on limiting space requirements for new subsoil structures, reduced encroachment on property lines, reduced access limits for new equipment installations, relocation of existing services, and routing of new services through very confined and limited space, all requiring very specific, detailed and well-coordinated design.
Detailed coordination between all disciplines regarding all aspects of the project must be part of the design phase to minimize the potential for contractor-claimed extras during construction. For example, quick turnaround times for construction support activities must be adhered to, in order to achieve the construction schedule.
Some of the key success factors in EA upgrade projects include:
- Thorough site investigations prior to design to confirm all as built information. This is critical to determining where new services will be located and connected to existing services, in order to avoid any interference with those services, and to identify where relocation of existing equipment may be required.
- Close coordination between all disciplines to ensure a) the responsibilities of all project team members are clearly defined, and b) that the design is fully buildable without additional unknown factors; for example, avoiding issues that can arise from incomplete or outdated as built drawings.
-Having all stakeholders review the design, with all comments being addressed prior to Issued for Bid stages.
Over twenty subway stations are already complete or currently have upgrades in design or construction:
Union | St. George | Pioneer Village | Kennedy | St. Clair West | Queen | Bay | Ossington | Lansdowne | Museum | Lawrence | Yorkdale | Yonge/Bloor | Finch West | Kipling | Warden | Bathurst | Jane | Sherbourne | Wellesley | Christie | Keele | Rosedale | Chester
SERVICES
Vertical Transportation | Mechanical Engineering | Electrical Engineering | Lighting Design
PROJECT FEATURES
Status: Ongoing system-wide upgrades for subway stations to provide accessibility | Mechanical, electrical and lighting system renovations and upgrades to support vertical transportation installations
LOCATION
Greater Toronto, Ontario
KEY SCOPE ELEMENTS
Design Build | Work within confined and limited space | Rapid turnaround on construction activities support to achieve schedule
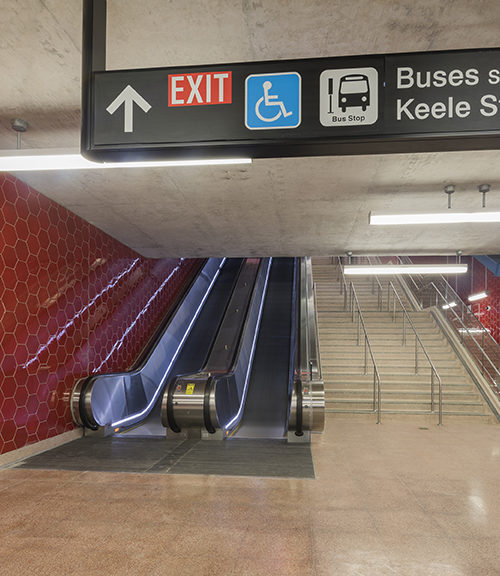
Space constraints
Because space for EA projects is very limited and within a confined area, all construction details must be effectively designed to ensure constructability.