Location: Eastern Canada
Town of Oakville
Fire Hall #8
This project was designed and constructed under the Integrated Project Delivery procurement model, a methodology that, in our experience, provides excellent results for our clients, as well as fostering greater collaboration within the project team.
Oakville’s new fire station and amenities have been designed to serve a growing population. LEED Silver certified, the 1.5 storey facility was almost fully constructed from glue laminated and cross laminated timber (CLT). CLT is a relatively new construction material in North America; CLT panels/walls are fabricated off site, where all M&E openings and penetrations are cut out, and then subsequently assembled on site. This approach required extremely close coordination between the structural designers and the M&E designers since, unlike drywall, wood openings cannot be adjusted once cut. The modular construction approach also helped meet the aggressive schedule for this project.
HH Angus’ mechanical scope included variable refrigerant flow, energy recovery ventilators, infrared tube heaters, and vehicle exhaust system. Electrical systems include natural gas backup generator, daylight harvesting sensors, provision for solar PV, CCTV and card access, and fire locution (radio system for 911 dispatch). Special provisions were made to allow speakers to be installed strategically throughout the building to support the locution/fire alerting system, with additional provisions for the radio antenna. In 2021, the project was honoured with the Toronto IES Illumination Section Award.
The fire hall floor plan consists of three fire truck bays - two drive-through and one back-in bay, gymnasium, dormitory, kitchen, offices, meeting rooms, IT room, and many specialized service spaces. Fire Hall #8 is designated as a “post disaster building”; hence, the M&E systems are very robust.
Perhaps ironically, the new fire station is clad in charred wood. Shou Sugi Ban charred siding, made from logs reclaimed from Ontario and Quebec waterways, offers many safety and operational advantages: it is ultra-low maintenance, naturally resistant to insects, moisture and rot, has proven fire resistance qualities, and is sun and water repellent. At end of life, the siding can be disposed of safely, without environmental damage.
The project team, under the IPD procurement model, included the Town of Oakville - Owner | Chandos - Builder/IPD Lead | LETT - Architect | HH Angus - Mechanical and Electrical Engineer | Bering Mechanical - Mechanical Contractor | Plan Group - Electrical Contractor | Gillam Group - Construction Management | Element 5 - Wood Structure Fabrication | LEA Consulting - Structural Engineer | Tresman Steel - Steel Structure Contractor | Groundworks Construction - Early Works and Landscape | Fluent - LEED Consultant | Husson - Stormwater Management.
Construction time-lapse: https://youtu.be/2dydglnYkRM
SERVICES
Mechanical Engineering | Electrical Engineering | Lighting Design | Communications Design | Security Design
PROJECT FEATURES
Status: Completion 2020 | 11,500 ft2 | Integrated Project Delivery | Mass timber construction | LEED Silver certified| Designated 'post disaster' building
LOCATION
Oakville, Ontario
KEY SCOPE ELEMENTS
Net Zero provisions for future conversion, with high efficiency M&E | Shou Sugi Ban charred wood cladding | Provision for future photo voltaic installation | locution/fire alerting system
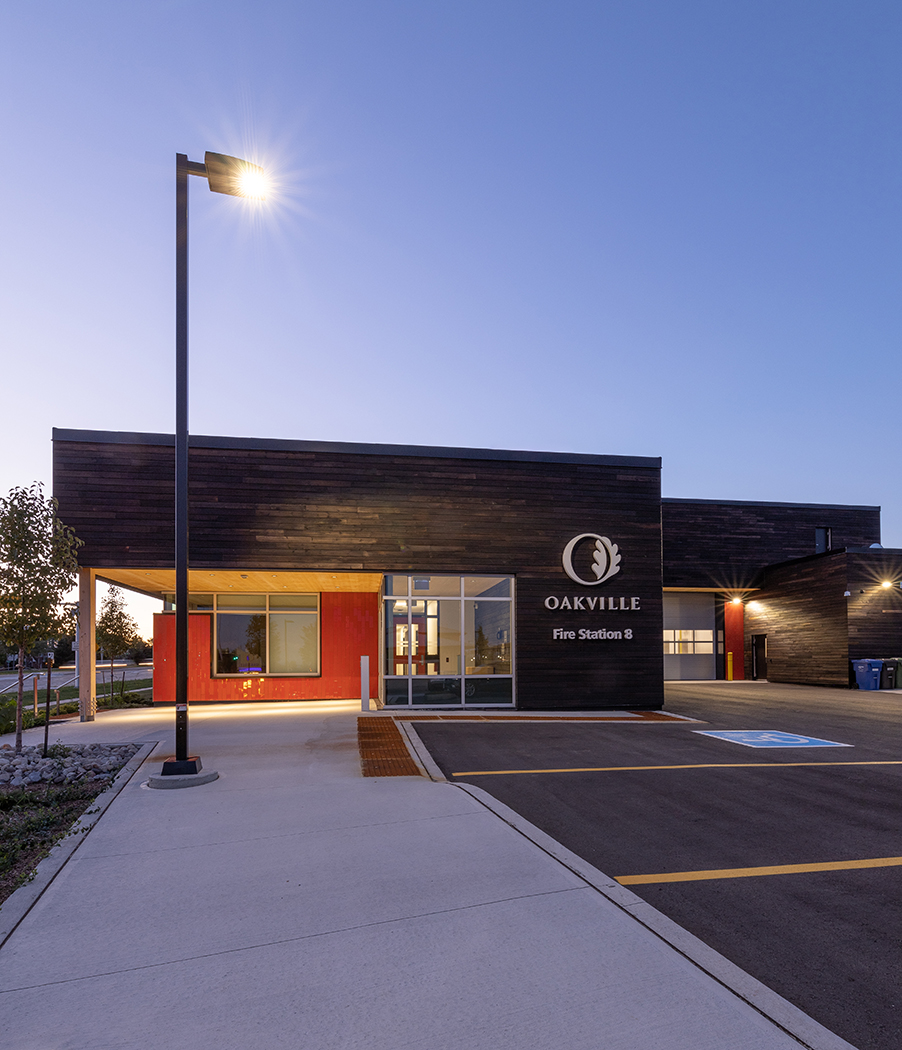
Net Zero Conversion
Highly efficient M&E systems provide for future Net Zero conversion. The Fire Hall is designed to accommodate a 40kW Solar PV system to offset and displace energy usage.
Site Challenges
The Fire Hall was built adjacent to an existing EMS Station and shares the road entrance and utilities. This presented a challenge in planning for construction, service entrances and operations. The team had to ensure that the Fire Hall does not impede EMS' emergency response process.
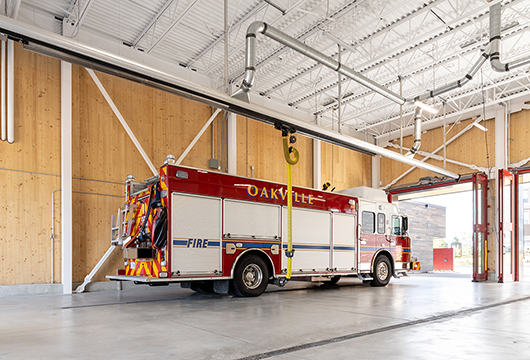
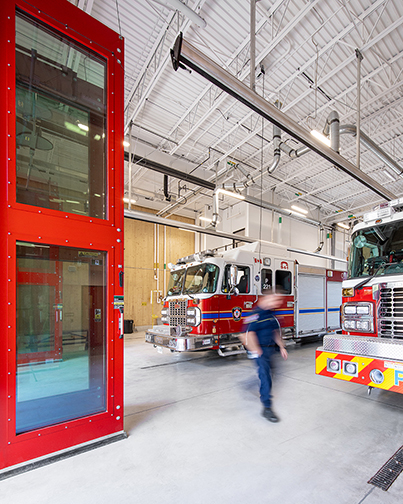
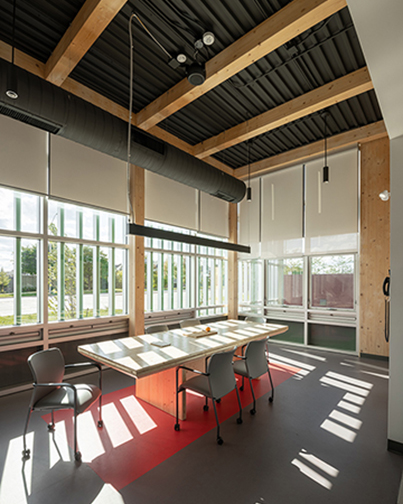
Wildeboer Dellelce LLP
365 Bay Street, 3 Floor Fitout
This 12-storey building is located in the heart of Toronto’s business and financial core. Constructed in 1960, the mechanical and electrical infrastructure was outdated and major redistribution and rework of the existing systems was required in order to suit the new tenant fitout.
HH Angus was engaged to provide fitout services for this commercial office renovation project. Our scope included mechanical, electrical, lighting and communications engineering design for renovations to three floors of office space for a standalone corporate finance and tax law firm.
The 8th floor consisted of renovations to 7,000 ft2 of client-facing space, including a universal washroom, meeting rooms, reception and welcome areas. A large existing boardroom was converted into multipurpose meeting space. This conversion required additional ventilation in order to accommodate up to 50 people.
A new build out included open and enclosed office space to accommodate future growth. A new universal washroom was also provided as part of the updated layout.
Extensive demolition was required in the central part of the floor plan to accommodate the new layouts. Construction took place during working hours; therefore, special planning and design were needed to accommodate critical areas and workstations during construction. Hoarding was required to separate these areas and ensure the safety of occupants. The project schedule was very aggressive.
SERVICES
Mechanical Engineering | Electrical Engineering | Communications Design | Lighting Design | Tenant fitout
PROJECT FEATURES
Status: Completed 2018 | Renovations to non-contiguous floor plates | Infrastructure upgrades
LOCATION
Toronto, Canada
KEY SCOPE ELEMENTS
Renovations to three floors of office space for a standalone corporate finance and tax law firm | Heavily phased to allow tenant operations to remain active throughout construction
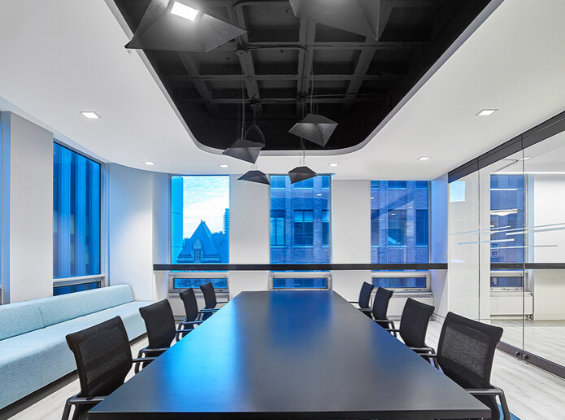
Innovative lighting design
Special attention was paid to highlighting unique design features, including dropped ceilings and feature walls.
Centralized amenities
The 9th and 10th floor renovation covered 16,050 rentable ft2. The objective was to refresh the employee work space and create a new, centralized café space.
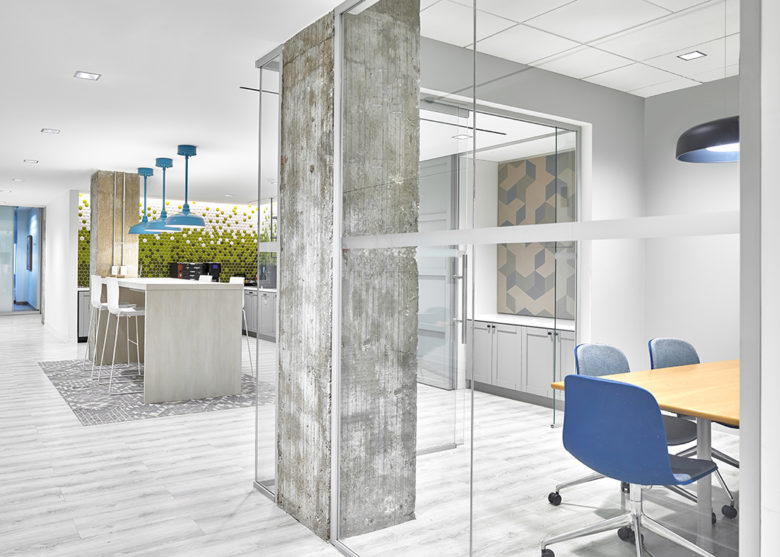
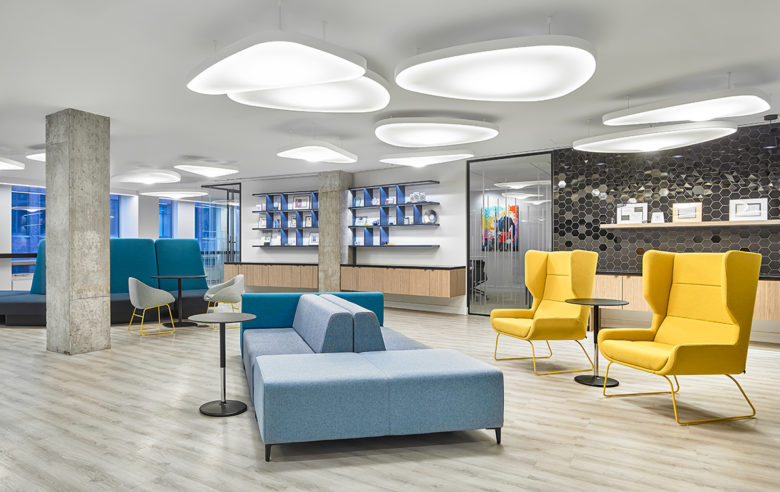
Close
coordination
The project team was able to achieve the schedule requirements by engaging in close coordination and communication from project inception to completion.
York University
Osgoode Professional Development Centre
Osgoode Hall Law School is considered a world leader in continuing legal education. Its Professional Development Centre is located in the heart of Toronto's downtown core, at Yonge and Dundas Streets, and forms part of York University's Downtown Campus.
HH Angus provided mechanical, electrical and lighting and ICAT design for a fit-out and renovation of the 26th floor of 1 Dundas St. Spaces included the reception area, open concept workstations, meeting rooms, lounge area, kitchen, staff room, phone rooms, accessible washrooms, academic classrooms of various sizes and functions, video/audio studio, and other support spaces.
Our scope for the 17,000 ft2 space included the alteration and renovation of the base-building elevator lobby and the entire 26th floor, complete with architectural, interiors, mechanical, electrical, telecommunications, accessibility, code and life safety, space and program planning, and fully integrated Building Information Modeling. The design was based on meeting LEED CI Silver standards.
SERVICES
Mechanical Engineering | Electrical Engineering | Lighting Design | Security Consulting
PROJECT FEATURES
Size: 17,000 ft2 renovation and fitout, meeting LEED CI Silver standards | Status: Completed 2019
LOCATION
Toronto, Ontario
KEY SCOPE ELEMENTS
Renovations to professional development institution | Fully integrated BIM
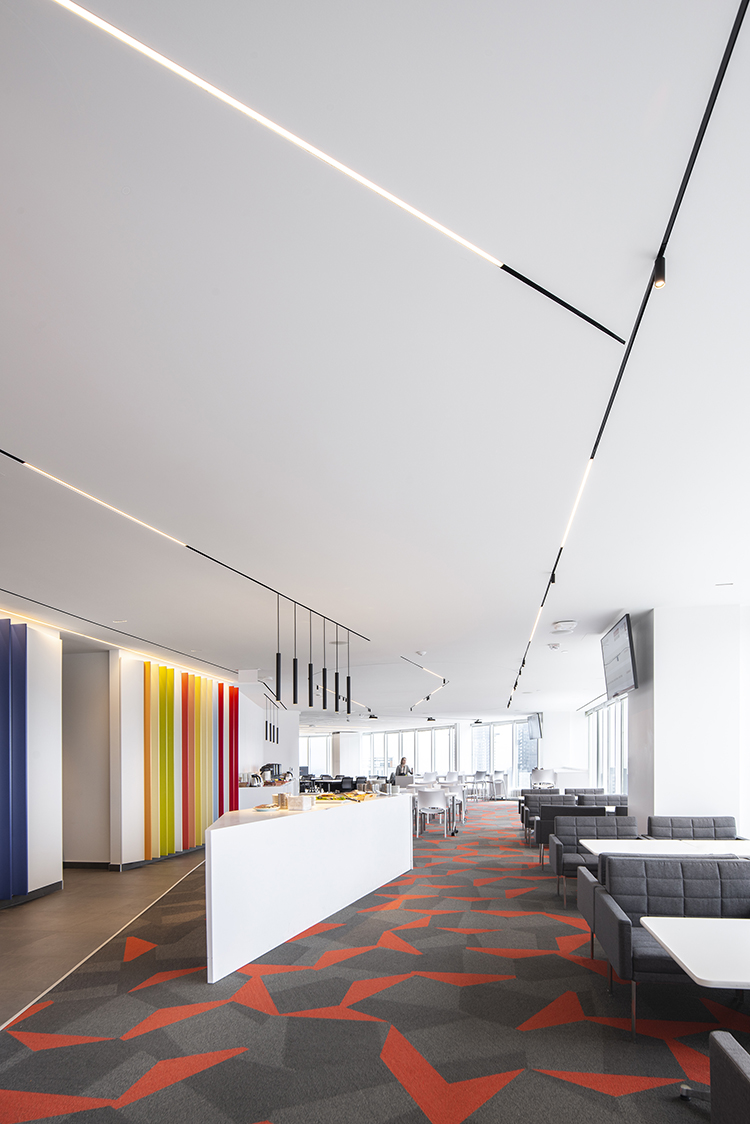
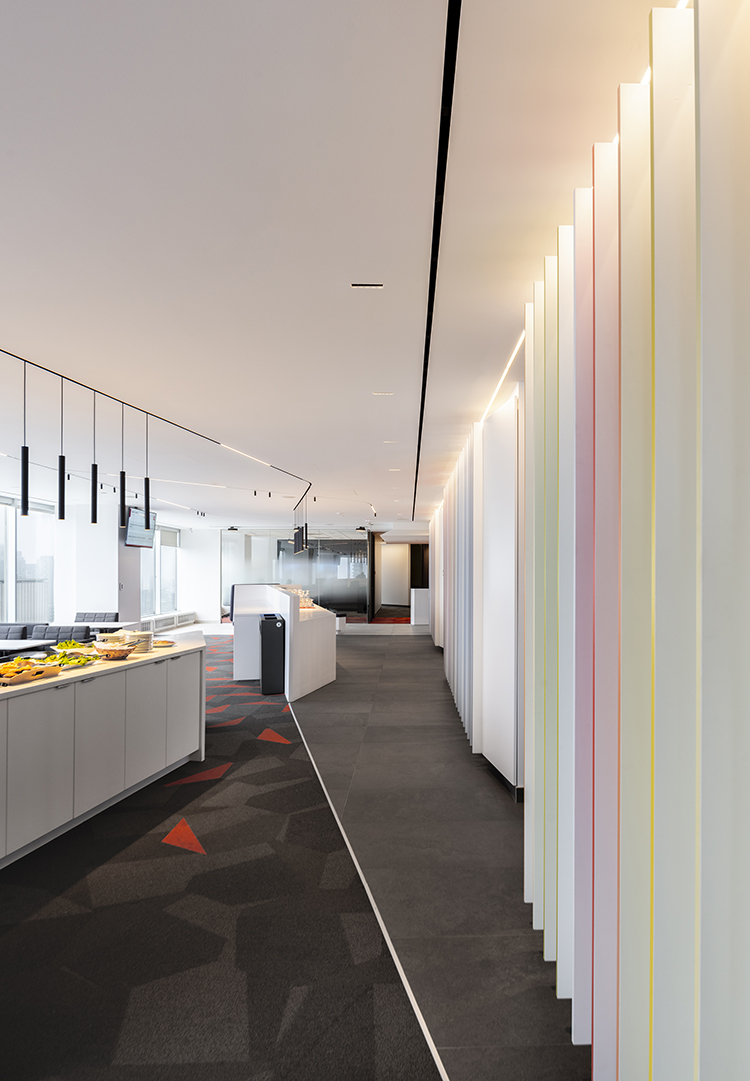
Cadillac Fairview
Toronto Dominion Centre
HH Angus has been working at this site since the earliest days of the Toronto Dominion Centre, Canada’s first skyscraper. We provided complete mechanical and electrical engineering services to the Toronto Dominion Bank and Cadillac Fairview (CF) in the construction of the first four towers, which total 5,600,000 ft2.
Those original iconic towers (now six) and the interconnecting below-ground shopping concourse comprise office space, underground parking and a retail and restaurant complex in the heart of downtown Toronto.
With the certification of 95 Wellington as Gold Level WELL Core, the entire TD Centre is now WELL certified, the largest real estate complex in Canada to have achieved this designation.
We have been involved in numerous technical infrastructure upgrades, including the installation of heat exchangers to the cooling plant in order to link to the Deep Lake Cooling system. We have provided detailed redesign of the service floors so that the space previously occupied by the cooling plant can be upgraded.
The Toronto Dominion Tower, the tallest at fifty-five stories, employs a perimeter induction heating and cooling system; all other buildings, which were designed later, employ variable air volume systems. Each building has a number of air handling plant room floors located approximately every twelve floors. This helped to minimize the size of individual pieces of equipment and the on-floor shaft sizes required.
Steam is used as the prime heating and humidification source for the Centre. Supplied from the Enwave District Energy System, the steam demand is rated at more than 70,000 kg/hr. The cooling load of over 49,000 kW is supplied by the Deep Lake Cooling system.
As part of the ongoing evaluation and revision of existing mechanical and electrical systems for this property, CF has invested in a new luminaire and ceiling combination. This investment provides tenants with base building illumination of a high quality while reducing the total lighting power density for building operations. This new luminaire system, in combination with accurate metering and appropriate building automation, is contributing to CF’s success in meeting and exceeding the ASHRAE 90.1 energy standards.
SERVICES
Mechanical Engineering | Electrical Engineering
PROJECT FEATURES
Size: 5,600,000 ft2 | Status: Ongoing
LOCATION
Toronto, Ontario
KEY SCOPE ELEMENTS
Ongoing technical infrastructure upgrades | Installed heat exchangers to link the cooling plant to the Deep Lake cooling system | LEED Gold
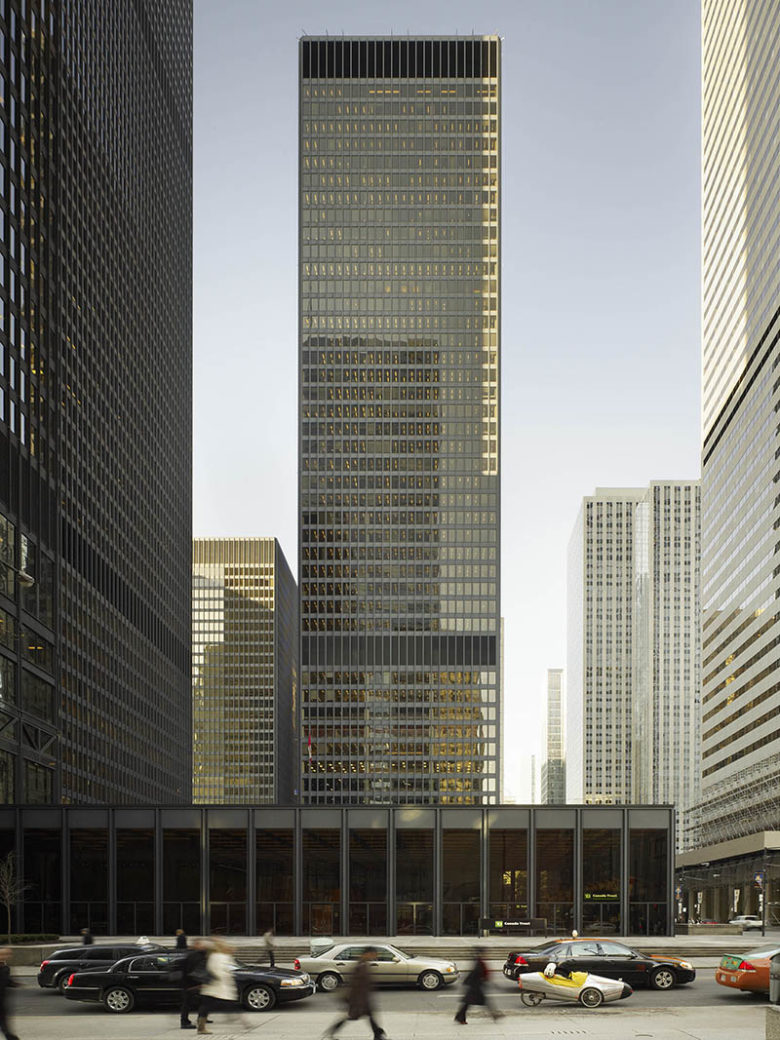
The imperative of good service
“The volume of work which you perform here at the TDC, I believe, is a direct reflection of your team’s reliability, high performance, and value.”
Adrian Sluga, Former Senior Manager, Tenant Projects, Cadillac Fairview
A lasting impression
TD Centre Heritage Designation:
The TD Centre in Toronto was designed by Ludwig Mies van der Rohe and, from 1967 to 1972, was the tallest building in Canada. A leading example of the International style, the TD Centre altered the city’s skyline while influencing many subsequent buildings across the nation.*
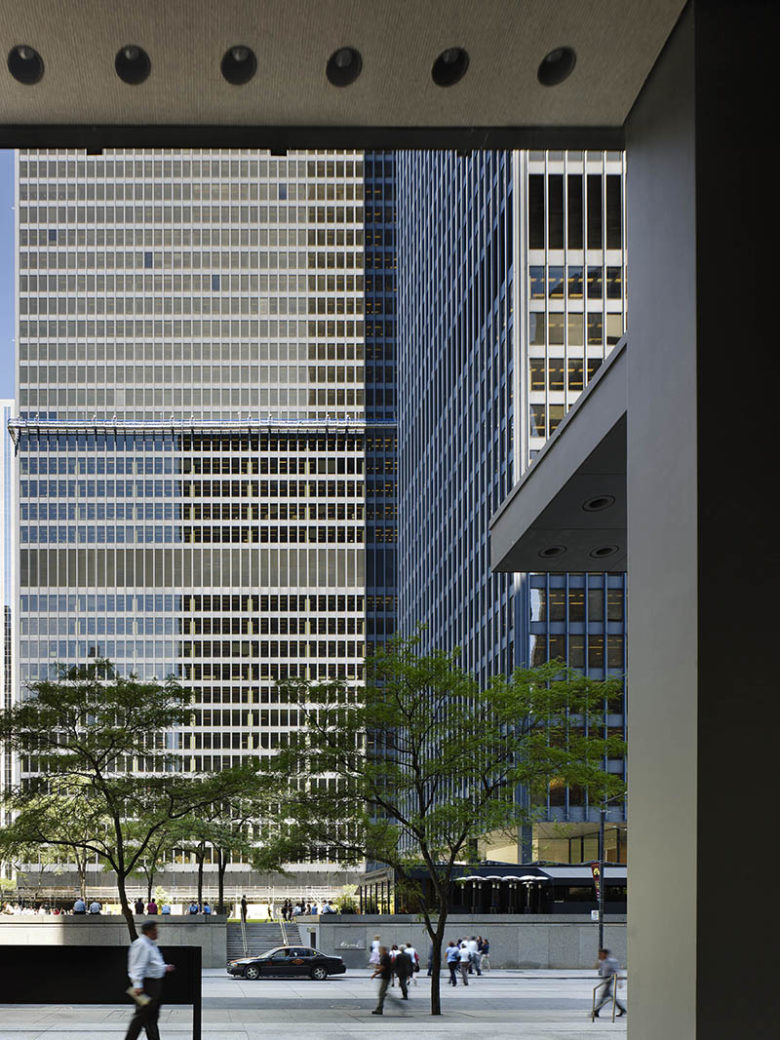
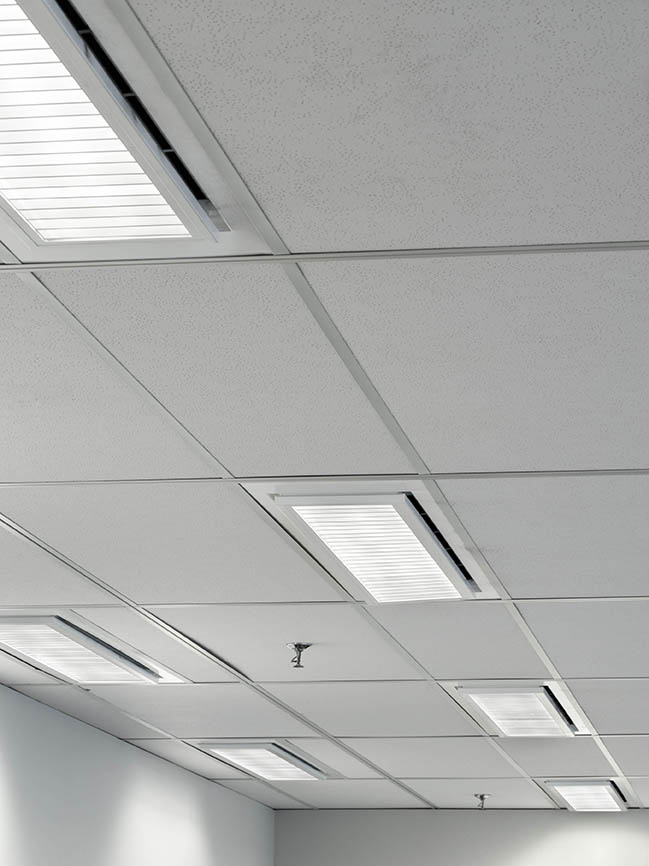
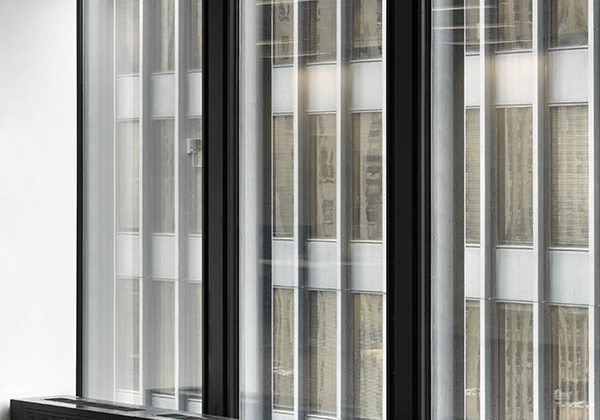
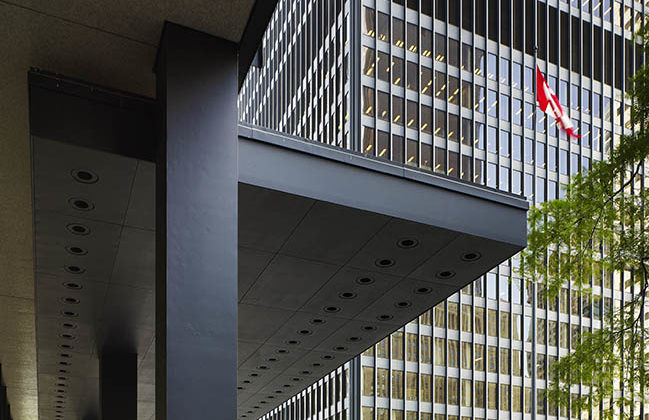
Infrastructure Ontario/Metrolinx
Eglinton Crosstown Light Rail Transit
This project is the largest transit expansion in Toronto’s history, and one of the largest P3 projects in North America. When complete, it will move people 60% faster than existing bus service and will accommodate ten times as many passengers.
The new light rail transit line runs along Eglinton Avenue between Mount Dennis Station (Weston Road) in the west and Kennedy Station in the east. The 19-kilometre corridor includes a 10-kilometre underground portion between Keele Street and Laird Drive. The line features 25 stations and stops, with links to bus routes, 3 subway stations and various GO Transit lines. HH Angus is providing mechanical and electrical consulting engineering for three stations – Mt. Pleasant, Leaside (Bayview) and Laird.
HH Angus’ mechanical scope includes ventilation and air conditioning of services spaces, sanitary and storm drainage throughout the station, track level and specialty trackwork drainage, fire protection systems for retail and service areas, water efficient plumbing fixtures and energy efficient HVAC systems.
Electrical scope covers power distribution, lighting and communications systems. Design layouts are provided for power distribution of the subway station, as well as traction power for the trains.
The lighting design features reduced power consumption. Exterior public areas lighting designs incorporate increased daylight levels, LED lighting in pylon signs, and energy efficient lighting in illuminated wayfinding signage to minimize power consumption.
Communications systems design includes fire alarm protection, public address speakers, passenger intercom, TTC pax telephones, public telephones and security systems including closed circuit television.
SERVICES
Mechanical Engineering | Electrical Engineering | Communications and Security Design
PROJECT FEATURES Status: Completion 2022
LOCATION
Toronto, Ontario
KEY SCOPE ELEMENTS
Mechanical, electrical, security and communication design was provided for 3 LRT stations | Design included ventilation, sanitary and storm drainage, fire protection, plumbing and energy-efficient HVAC systems, lighting, security and communications systems | Largest transit expansion in Toronto’s history