Location: Eastern Canada
Woodbine Entertainment Group
Woodbine Casino Expansion
Woodbine Entertainment Group (WEG) is a longstanding and valued client of HH Angus, dating back to the late 1980s. Through successful projects at Woodbine over the years, and the development of a strong relationship, we are privileged to serve as a trusted advisor.
Woodbine Racetrack is home to Ontario Lottery & Gaming’s (OLG) most successful revenue generating facility. One of the challenges in providing services for this site is the uncompromising need to keep all services fully operational at all times. The system must provide total redundancy for 24/7 operation of the slot floor area and associated support spaces. When required, we provide around-the-clock service to minimize disruptions.
WEG’s “1 West Expansion” saw a former storage space renovated to accommodate 1000 new gaming floor slot machines, complementing the 2000-slot installation we had previously designed during original base building and fit out. The expansion required all new mechanical and electrical (M&E) services.
The slots expansion included significant upgrades to the electrical service, which had to be brought a long distance from the main electrical room. The new distribution was sized to handle all the new games, audio/visual equipment, surveillance equipment, lighting and general power loads. We also upgraded the emergency power system and synchronized the generators while, at the same time, maintaining the same level of available emergency power.
Other major projects at Woodbine have included:
- On-track lighting for Thoroughbred and Standardbred racing
- Replacement of the steam boiler plant with three 5,000,000 BTU/h (input) high efficiency boilers and two 1,200,000 BTU/h (input) high efficiency boilers
- Base building improvements to escalator, kitchen, grandstands
- Responsible Gaming offices
- ‘Backstretch Barn’ renovations
- ‘Backstretch’ domestic water service
- Generator system upgrade
SERVICES
Mechanical Engineering | Electrical Engineering
PROJECT FEATURES
Status: Ongoing
LOCATION
Vaughan, Ontario
KEY SCOPE ELEMENTS
Renovated storage space to accommodate 1000 new gaming floor slot machines | Critical up-time requirement to keep all services fully operational around the clock
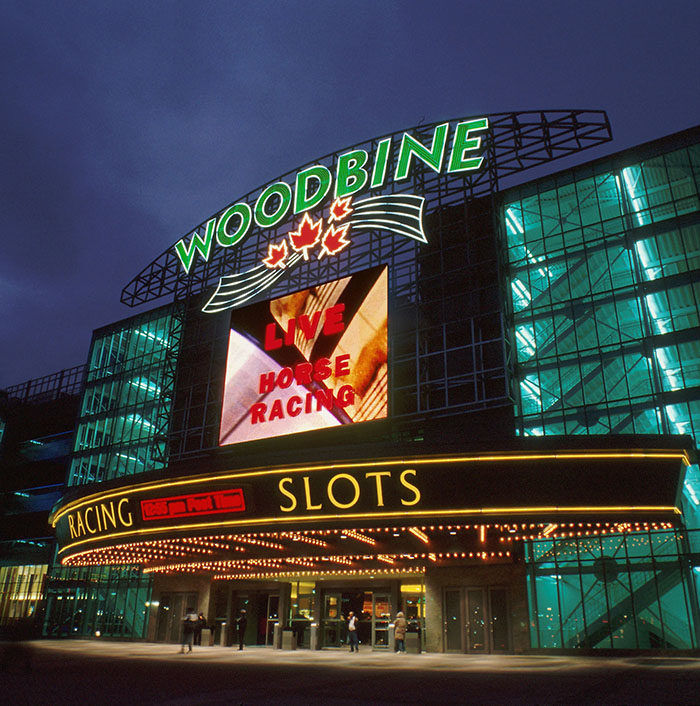
Renovating dining spaces
The expansion also contains an 80-seat casual dining area featuring “Willows Restaurant” and “Willows Noodle Bar”.
St. Michael’s Hospital
Peter Gilgan Patient Care Tower
HH Angus is part of the Compliance Team for the new 17-storey Patient Care Tower. The Tower will provide an additional ~250,000 ft2 to the Hospital’s main campus at 30 Bond Street, with an additional ~150,000 ft2 of renovation distributed throughout the existing building.
The new tower will allow patient care to move out of aging and inadequate space, clinical programs and services to be right-sized to meet current standards, and costly, leased administrative space to be repatriated.
The project includes five new operating rooms, enlarged, state-of-the art facilities for orthopedic surgery, coronary care and respirology, an expanded emergency department, and the demolition and new construction of the Shuter Wing. The project is targeting LEED Gold certification.
SERVICES
Mechanical Compliance Engineering | Electrical Compliance Engineering | ICAT Compliance Consulting
PROJECT FEATURES
Size: 26710 m2 | Tertiary Care Hospital | Status: Current
KEY SCOPE ELEMENTS
17 storey patient care tower | Integration of new and existing M&E and IMIT infrastructure | Targeting LEED® Gold
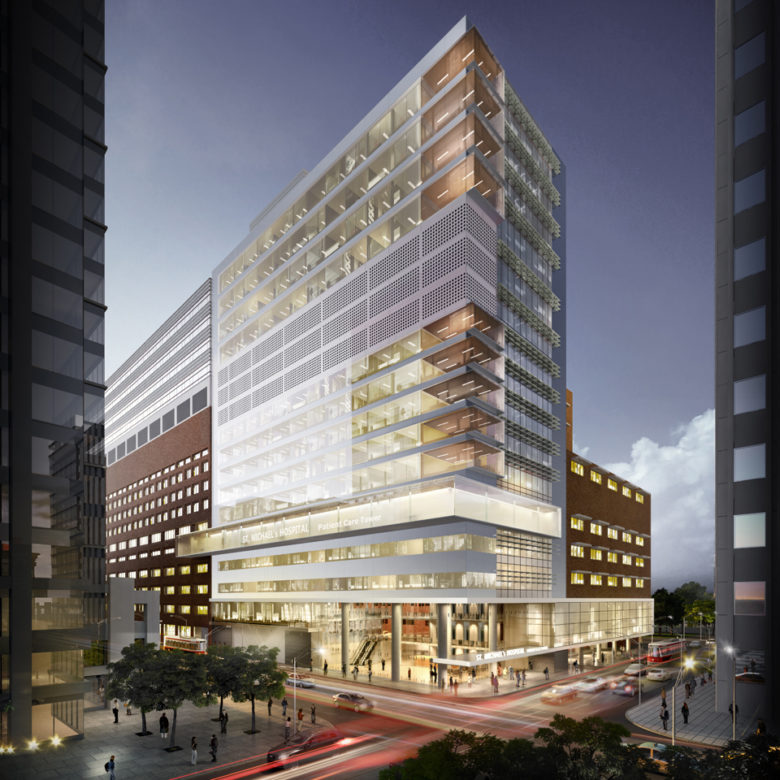
Integrating old and new buildings
Addressing major renovations and integrating new infrastructure with existing systems was a key challenge for the team. To address this, HH Angus provided detailed background information and on-site investigation to mitigate the risks to the Hospital.
IMIT challenges
This challenge extended to the IT systems, where the team had to integrate existing IT infrastructure with the new building. Extensive work was required to bring the Hospital’s aging IT infrastructure up to current standards, and to provide future flexibility. HH Angus designed a solution that would properly integrate and communicate with both new and existing systems.
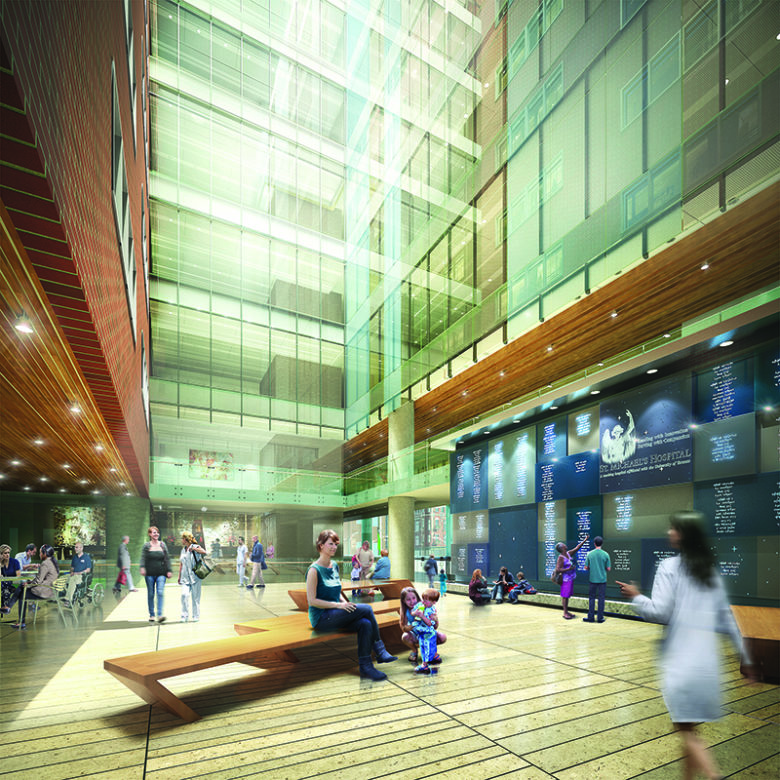
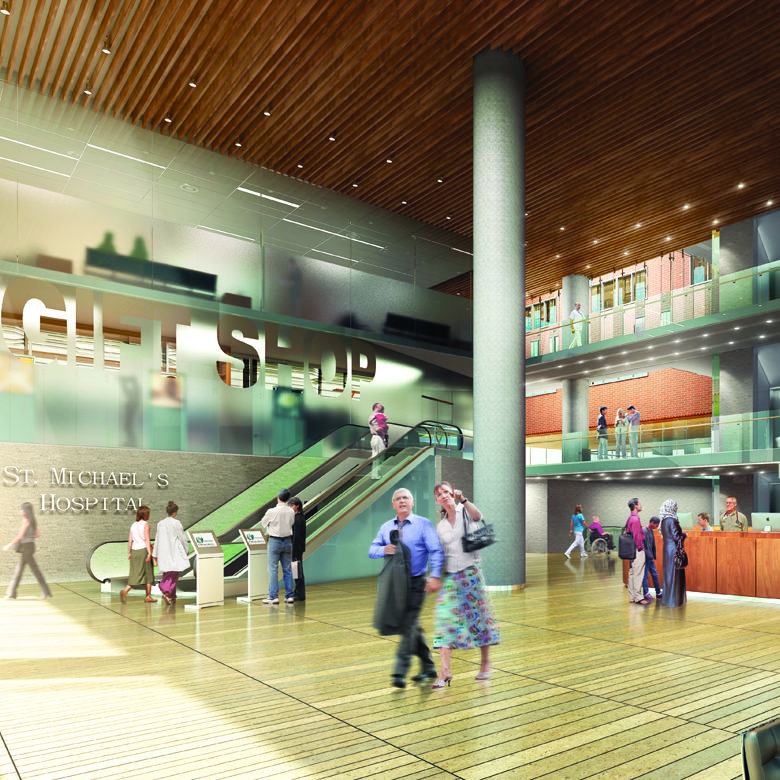
Daylight harvesting
The Tower’s atrium, with 11 storeys of natural light, will feature retail space, a patient information centre, and the Admitting Department.
— Renderings courtesy of Cicada Design
Toronto Metropolitan University (formerly Ryerson)
Pitman Hall Food Facility
Pitman Hall, located in the heart of downtown Toronto, is Toronto Metropolitan University's second largest residence, with 14 floors and 565 rooms.
HH Angus provided electrical and mechanical consulting services for the renovation of the existing kitchen and dining facilities in Pitman Hall. The refurbishment was implemented in two phases, with the kitchen and seating area as Phase 1, and the Dining Hall expansion into Pitman Quad in Phase 2.
The objective of the renovation was to increase capacity throughout the existing facility, both in number of meals served and seating capacity.
HH Angus’ scope included review of existing building systems, preparation of mechanical and electrical designs, creation of preliminary construction and other tender documents, and identification of future mechanical and electrical space requirements.
SERVICES
Mechanical Engineering | Electrical Engineering | Security | Communications | Fire Protection | Lighting Design
PROJECT FEATURES
Status: Completed Phase 1 - 2018; Phase 2 - 2019
LOCATION
Toronto, Ontario
KEY SCOPE ELEMENTS
Created preliminary construction and other tender documents | Identified future mechanical and electrical space requirements | Increased facility’s meal preparation capacity | Innovative ceiling lighting design
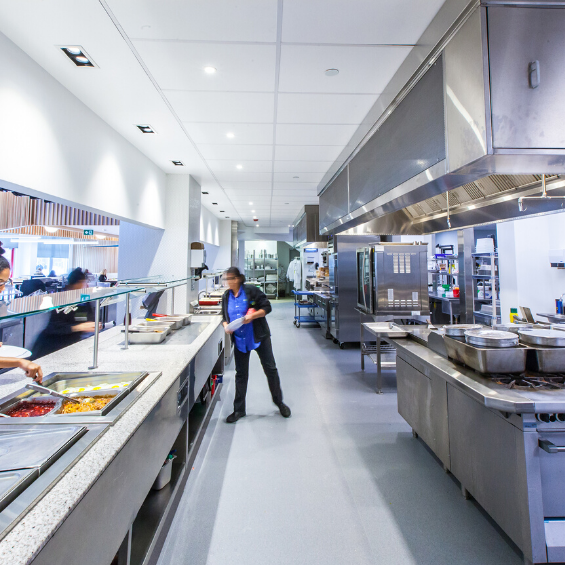
Ecological Exhaust
Increasing the meal preparation capacity of the facility presented some design challenges for the Planning, Design Consulting (PDC) team. This is usually accomplished by increasing the exhaust volume of the cooking facility; however, the location of the building was such that other nearby buildings were too close for direct exhaust. HH Angus worked closely with the kitchen consultant to design and specify a grease filtering “ecological” exhaust unit that would sit on the existing structure.
Ventilation and Lighting Design
The wave-style ceiling presented an interesting challenge to the PDC team in designing the lighting for the unique ceiling architecture. The team worked closely with the architect to create a design that would accommodate linear diffusers and lights.
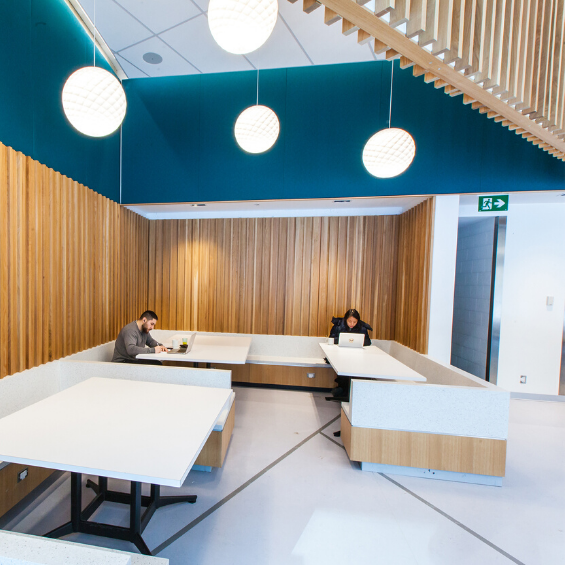
General Electric
Brilliant Factory
General Electric’s new state-of-the-art gas engine plant is one of the most advanced in GE’s global operations and the first of its kind in Canada. “It’s a plant that is reimagining how we manufacture. It incorporates all the concepts of lean: speed with excellent quality — coupled with everything that is now available and that is coming down the pipe in digital technology, with the latest in software developments.”*
— Elyse Allan, GE Canada CEO
HH Angus provided mechanical, electrical, plumbing, security, IT, lighting and vertical transportation consulting. The multi-modal plant, now owned by Advent International, manufactures gas engines that are coupled with either air or gas compressors, or with electric generators. The engines are distributed worldwide, primarily outside North America, in the oil and gas industry.
The plant runs three-dimensional machining simulations for CNC programs, gains real-time analytics to better understand the operating conditions of a machine or a test cell, operates lights-out machining, and combines all with advanced lean manufacturing practices.
Our IMIT scope included flexible structured cabling systems and supporting infrastructure, consisting of the latest shielded copper and fiber technologies, providing a transport platform for data, voice, video and other IP-based systems.
We also provided design for all low voltage technology systems. The factory uses equipment and machines embedded with sensors and connected to the high availability Industrial Internet Protocol-based network. Equipment data is streamed over secure links to the cloud for analysis.
Extensive design and installation of multiple audiovisual systems facilitate collaboration between global sites. Plant cabling design was provided per the most recent Industrial Premises standard. Working closely with the client’s IT, Security and AV groups, network-based systems were designed to the latest technology.
Our Angus Connect team was also involved in determining the performance requirements of client systems, product selection, preparation of working drawings and specifications, tender preparation and response evaluation.
SERVICES
Mechanical Engineering | Electrical Engineering | Security and IMIT Design | Vertical Transportation Consulting | Lighting Design
PROJECT FEATURES
Size: 450,000 ft2 | Status: Completed 2018
LOCATION
Welland, Ontario
KEY SCOPE ELEMENTS
Multi-model plant | Plant is fully air-conditioned to prevent "flash rust" | real-time analytics | Transport platform for data, voice, video and other IP-based systems | AV systems enable collaboration between global sites | Test cell scope added later | Met aggressive schedule for working drawings | LEED Silver Certified
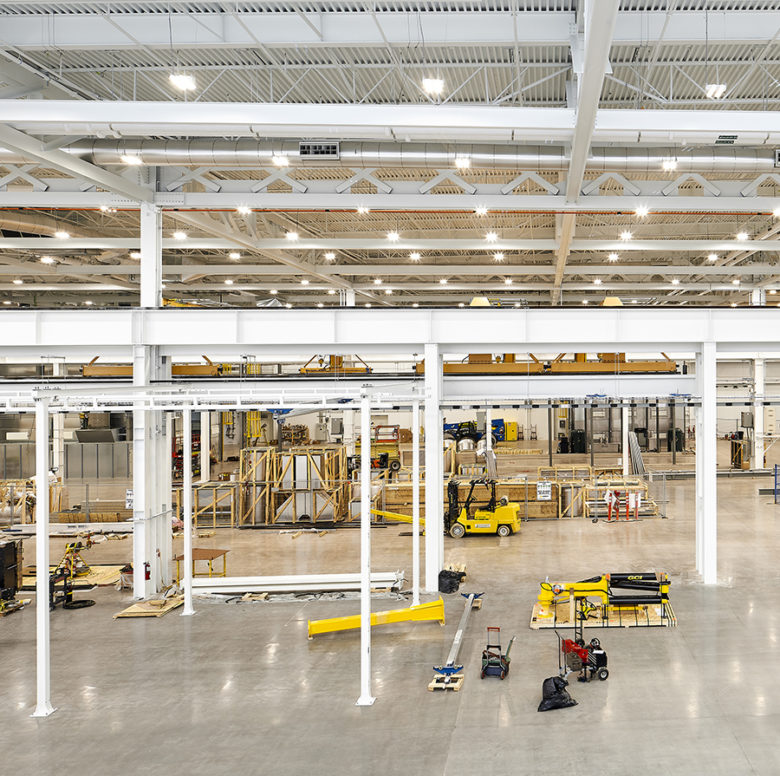
Custom HVAC control
The plant is fully air-conditioned to prevent ‘flash rust’, which can occur during machining of items such as crankshafts and connecting rods if humidity levels are not carefully controlled.
Industrial and support spaces
In addition to the main assembly and machine areas, three test cells, warehouse space, and paint areas, the plant also features front of house spaces such as offices, staff support, fitness centre, customer areas, hoteling for visiting customers and GE staff, conference rooms, etc.
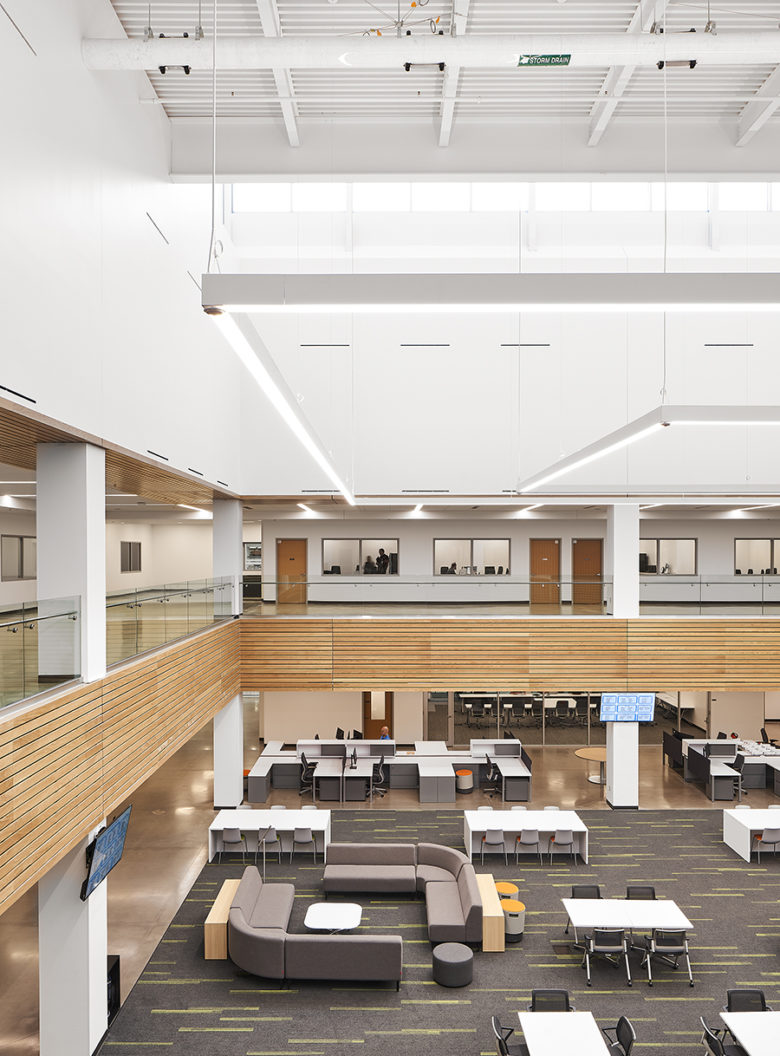
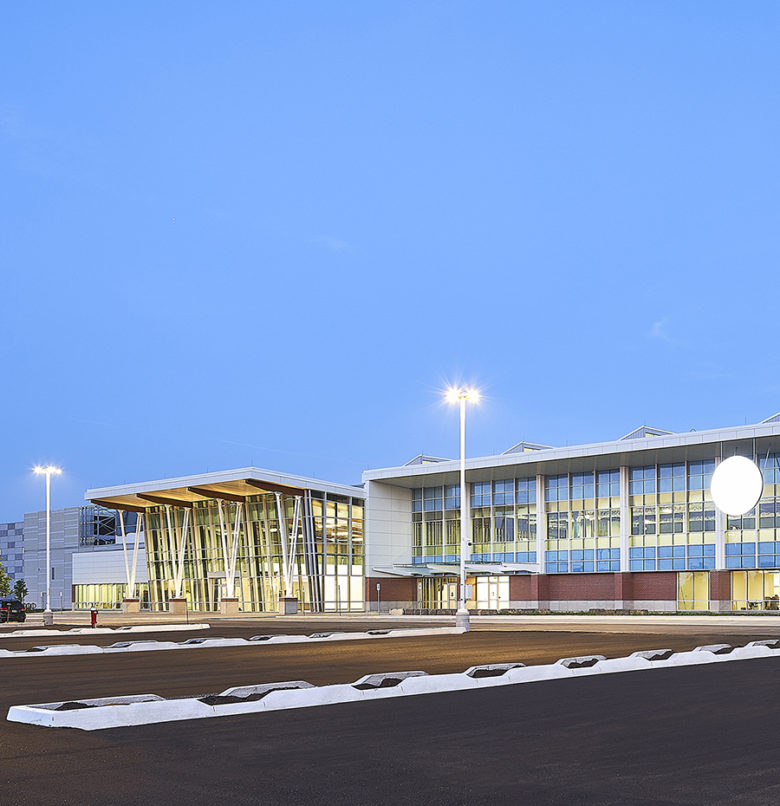
Expanding our scope
HH Angus’ project scope was increased to include the physical design of a significant new Test Cell addition to the plant, and to ensure Canadian compliance. The three test cells are connected to the main plant for testing engines prior to delivery. We met an aggressive schedule to produce working drawings for tender.
Toronto Sunnybrook Regional Cancer Clinic
HH Angus has been providing mechanical and electrical engineering at the Sunnybrook campus since 1945. The complex now totals more than 2,000,000 ft2. In that time, a great many individual projects have been successfully delivered. The Cancer Centre, described below, represents an ongoing program of redevelopment and renovation. Other large project examples from Sunnybrook include M Wing and the Sunnybrook High Voltage Emergency Power Renewal.
Toronto Sunnybrook Regional Cancer Clinic
The Cancer Centre at the Sunnybrook campus has been upgraded, renovated and expanded a number of times since originally constructed over 40 years ago. We have been involved with this facility since its inception. The original building was 70,000 ft2, with four Radiation Therapy Treatment Rooms and one Simulation Suite for treatment planning.
The facility saw a major expansion and renovation in the early 1990s, which increased the area to 200,000 ft2 and included eight new Radiation Therapy Treatment Rooms and two new Simulator Suites. An on-going program of upgrades has seen comprehensive replacement of older treatment equipment with newer options.
The original building construction included one simulator suite, two high energy (25MEV) radiotherapy treatment rooms, one medium energy (6 MEV) radiotherapy treatment room, one cobalt room and full chemotherapy facilities. Later, a second cobalt room was added, along with a building addition, including one medium energy (6MEV) radiotherapy treatment room and two simulators.
In 1993, a major addition included three medium energy (6MEV) radiotherapy treatment rooms (Siemens), a Simulator suite (Philips), three high energy (25 MEV) radiotherapy treatment rooms (Philips), a CT simulator suite (Picker), one new cobalt room, and relocation of the existing cobalt room.
In a renovation project in 1999/2000, we replaced existing treatment equipment, specifically two medium and two high energy radiotherapy treatment rooms (Siemens), and added a new high energy radiotherapy treatment room. That was followed a few years later by replacement of the existing cobalt treatment equipment with new medium energy radiation therapy equipment.
SERVICES
Mechanical Engineering | Electrical Engineering
PROJECT FEATURES
Size: 200,000 ft2 | Status: Ongoing Upgrades
LOCATION
Toronto, Ontario
KEY SCOPE ELEMENTS
Ongoing expansion and renovations
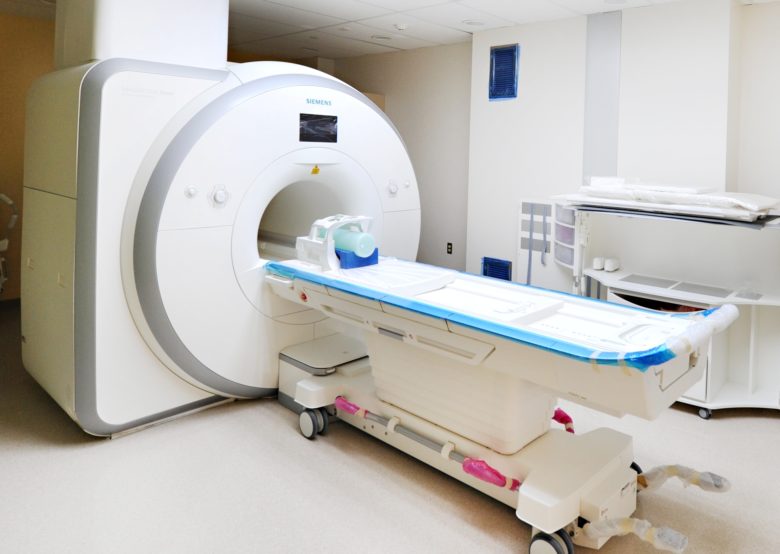
Increasing treatment options
In the decade from 2000 to 2010, we added a PET simulator, an MRI Suite, replaced one cobalt treatment room with a tomotherapy treatment room and, tackling one room at a time, have replaced all existing equipment.
Improving service
We also completed a renovation to modernize the Main Reception area and new Pharmacy, and renovations to the chemotherapy treatment area.
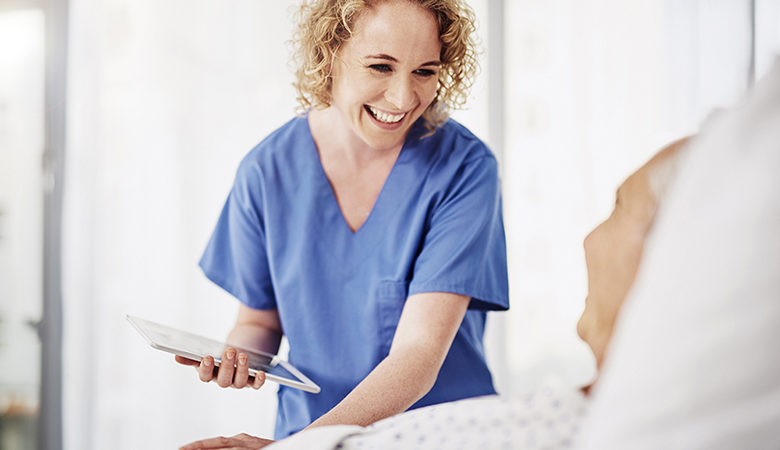