Location: Eastern Canada
North Bay Regional Health Centre
The first LEED® registered healthcare facility in Canada, North Bay Regional Health Centre was built on a greenfield site and replaced two general hospitals and a separate mental health facility. HH Angus provided mechanical, electrical, vertical transportation, specialty lighting and communications design consulting engineering for the project.
The gross building area is 725,000 ft2. The facility includes the full range of departments normally found in a regional acute-care, 275-bed hospital, plus a new facility for the Northeast Mental Health Centre. The mental health portion is significant, consisting of 150,000 ft2 and 113 beds, and also includes a significant forensic component.
Using a completely innovative approach, our staff developed 100% outdoor air systems with total enthalpy heat recovery wheels, the first time this system had been implemented in North America. A major advantage of this system is that there is no re-circulated air, which greatly reduces the possibility of infection transmission for patients, staff and visitors. As well, delivering 100% fresh air rather than re-circulated air reduced the need for as many air changes in patient rooms as had previously been the norm. And that change meant that smaller fans and less ductwork were possible, resulting in lower capital cost.
As a value added service, HH Angus constructed a mock patient room to verify airflow patterns for the air distribution system. This ensured that the design was flawless. In addition, reducing air volumes to patient rooms to four changes per hour resulted in changes in the CSA standard.
The project also included:
- Planned future remote cogeneration plant
- High efficiency central heating plant with hot water and steam boilers
- Centrifugal chillers supplemented with a 24/7 chilled water system
- Radiant ceiling panels for perimeter heating
- Enhanced building envelope to achieve energy performance
- Bi-fuel emergency generators with provision for dispatch lighting
- LED lighting
SERVICES
Mechanical Engineering | Electrical Engineering | Communications Design | Lighting Design | Vertical Transportation Consulting
PROJECT FEATURES
Size: 725,000 ft2 | The first modified Alternate Finance Partnership (AFP) in Ontario | Status: Completed 2010
LOCATION North Bay, Ontario
KEY SCOPE ELEMENTS
Greenfield hospital with new mental health centre | A North American first: 100% outdoor air supply with high efficiency total enthalpy heat recovery wheels throughout the hospital, resulting in reduced risk of infection and lower capital costs | One of Canada's first LEED® registered facilities
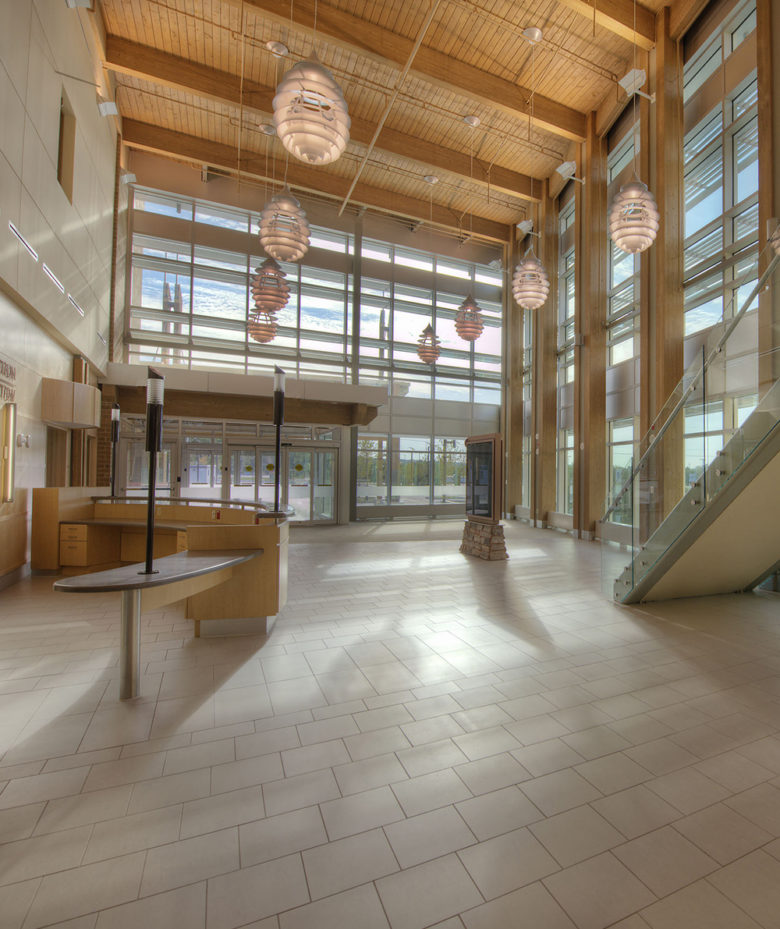
Custom electrical design
Specialized electrical systems features for the project included a centralized uninterrupted power system and an integrated communications systems platform used for all building operations and healthcare applications.
One of Canada’s first LEED® registered facilities
The main challenge with the design of this facility was performing energy modeling for LEED®. HH Angus’ design team included LEED® Accredited Professionals qualified to carry out a project that met LEED® standards for creation of an energy-efficient building.
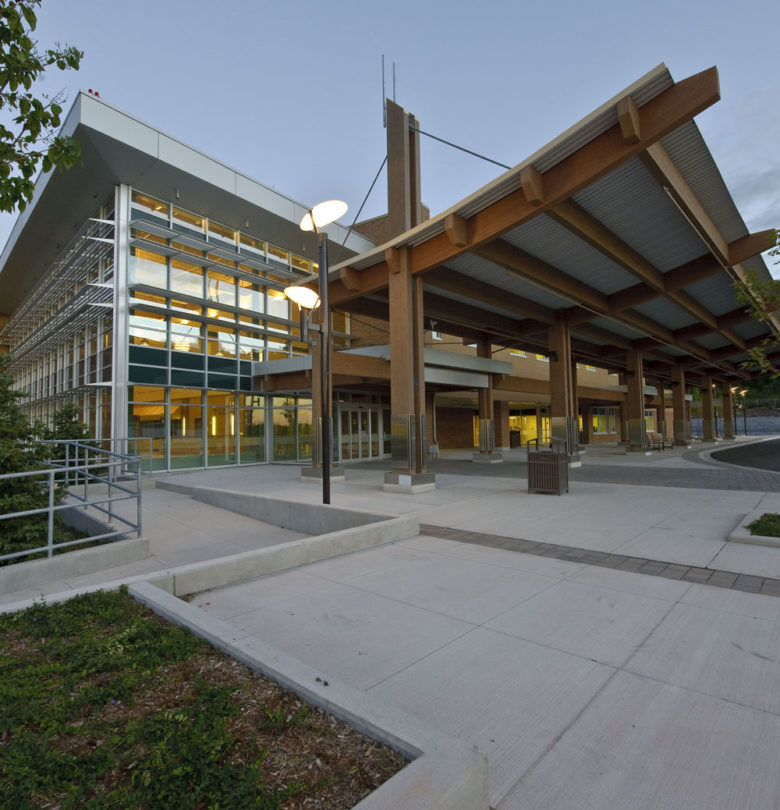
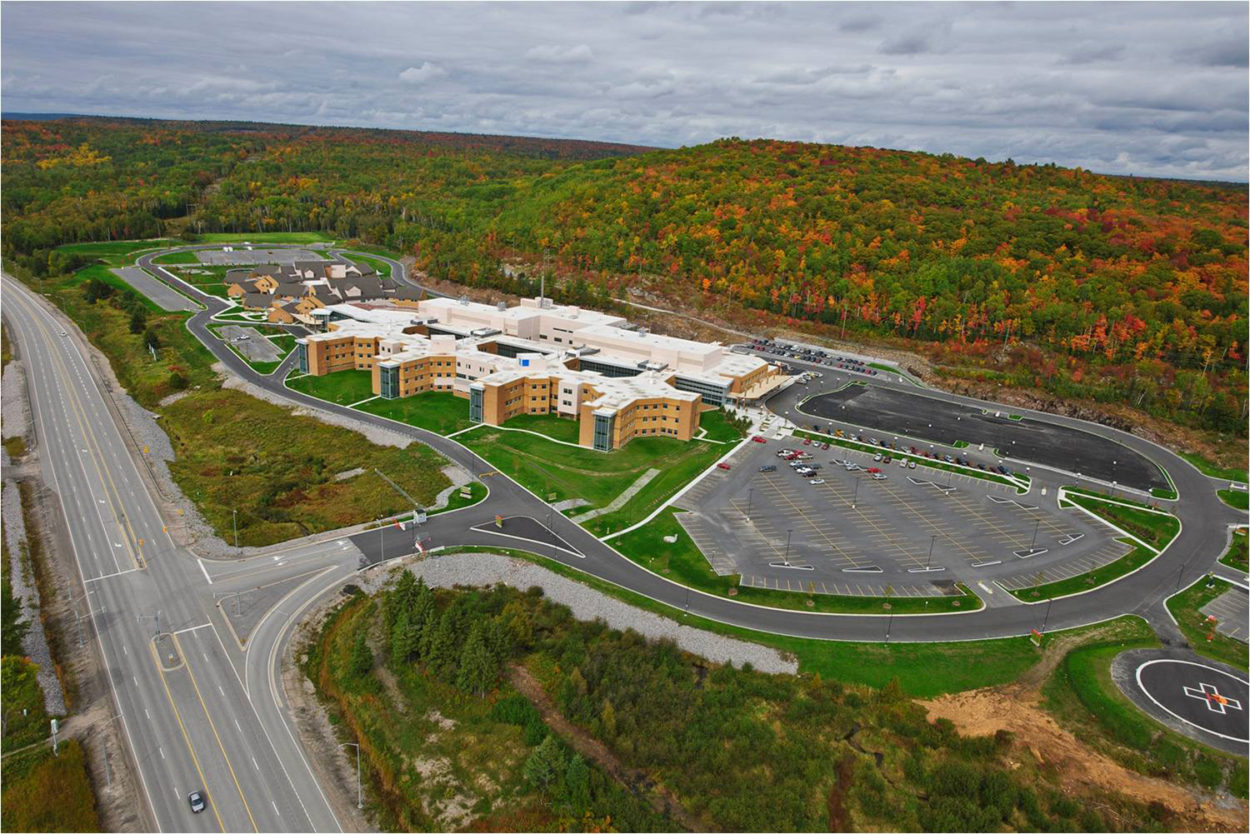
— Image courtesy of Evans Bertrand Hill Wheeler Architecture Inc.
Brookfield Developments
Bay Adelaide Centre, Phase 1 West Tower
The Bay Adelaide Centre Phase 1 West is a large downtown Toronto office tower. HH Angus was involved in the design and tendering of elevating devices in this new 51-storey development.
Elevating systems include 28 passenger elevators, 2 service elevators and 2 escalators. The passenger elevators have rated speeds ranging from 3.5 m/s (700 fpm) in the 5-car low rise bank to 7.0 m/s (1400 fpm) in the 8-car high rise bank.
SERVICES
Vertical Transportation Consultants
PROJECT FEATURES
Status: Completed 2009
LOCATION
Toronto, Ontario
KEY SCOPE ELEMENTS
Design and tendering of elevating devices | Elevating systems included 28 passenger elevators, 2 service elevators and 2 escalators
Queen’s University
Tindall Playing Field Relocation & Parking Structure
“The opening of Tindall Field is the first step for Queen's Athletics in moving towards our vision of becoming the best in Canada.”
– Leslie Dal Cin, Director of Athletics and Recreation, Queen’s News Centre Sept. 2008
Kingston, Ontario’s first outdoor artificial playing surface, Tindall Field at Queen’s University, was developed as a two-level underground parking structure and a running track and Soccer/Football Playing Field. The roof of the parking structure forms the base of the playing field, and includes a playing field storm drainage system that directs the storm water to a large cistern for flow control into the municipality’s storm drainage system. The field is surrounded by a 3-lane rubberized track.
Resolving light pollution issues was critical, given the proximity of the field to a student residence and the campus observatory. Lighting consisted of pole-mounted luminaires on each side of the playing field. The light distribution was controlled by designing shields for the upward lighting component and reflectors with cut-offs to reduce light distribution at the edge of the playing field.
SERVICES
Mechanical Engineering | Electrical Engineering | Lighting
PROJECT FEATURES
Status: Completed 2008
LOCATION
Kingston, Ontario
KEY SCOPE ELEMENTS
Playing field over underground parking | Rubberized running track | Storm drainage system with large cistern for flow control |Specialized light distribution control
Toronto Community Housing
341 Bloor Street West, Senator David A. Croll Apartments
“The system brings enormous value to the facility. Not only does it increase the emergency power load to near peak load, but also it reduces emissions and eliminates transmission losses, thus reducing the need for expanded power generation.”
- Paul Isaac, Principal in Charge, HH AngusThe Senator David A. Croll Apartment building, formerly Rochdale College, is a typical multi-unit residential building managed by the Toronto Community Housing Corporation.
This 335 kW combined heat and emergency power (CHeP) project was built to avoid the cost of replacing a diesel generator, with a significant saving of $300,000. Conventional emergency on-site generation uses dedicated equipment that is rarely operated, yet has a very high capital cost (known as a ‘stranded asset’). HH Angus converted this stranded asset to provide an economic benefit to the facility. The benefit comes from recovering heat so that the overall efficiency rose from 33% to 83%, as well as the use of natural gas, which is cheaper than diesel.
The new generator produces enough electricity for the entire building load on most days. The heat generated by the engine is captured and used to heat the domestic hot water system and building spaces, thereby producing a highly efficient use of the fuel - greater than 90%!
The most important benefit for the building’s occupants is the increased emergency power load capabilities. Instead of powering just a minimum of elevator and emergency lighting services during power outages, the CHeP system provides a power load that runs all regular systems, including heating and air-conditioning systems.
SERVICES
Prime Consultant | Mechanical Engineering | Electrical Engineering
PROJECT FEATURES
Status: Completed 2008
LOCATION
Toronto, Ontario
KEY SCOPE ELEMENTS
Combined Heat and Emergency Power (CHeP) | Co-generation tied into a network system, a first for Toronto | Stranded asset converted to economic benefit - heat recovery efficiency rose from 33% to 83%
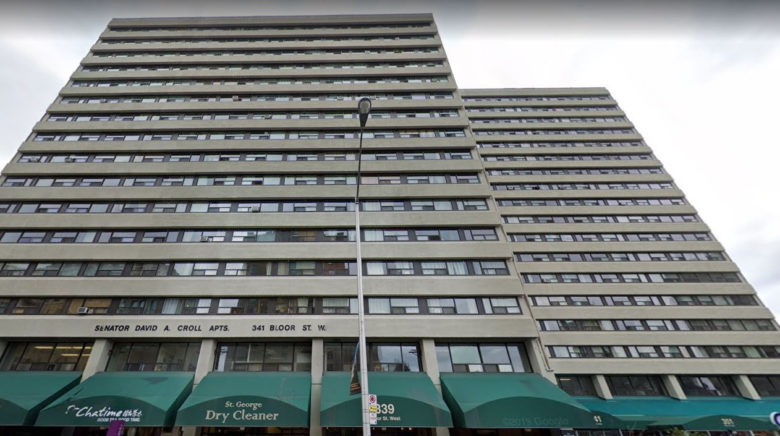
A Toronto ‘first’!
The 341 Bloor Street system was a first in Toronto and was carried out with funding assistance from the Toronto Atmospheric Fund and Natural Resources Canada.
General Motors of Canada
Welder Water System, Car Assembly & Truck Plants
HH Angus designed the Welder Water System for the car assembly and GMT 800 C/K Truck plants in Oshawa. These systems provide cooling water for all the robot welders, circulating cooling water to the tips of the welders to prevent overheating.
C/K Truck Plant
This plant’s welder water system consisted of a cooling tower system and cooling distribution system. The pumps re-circulate tower water from the indoor sump through heat exchangers and up to the cooling towers. The cooling tower system featured five main components: Cooling towers, indoor sump, recirculation pumps, plate heat exchangers and centrifugal filter units.
The two vital conditions that had to be maintained were temperature and differential pressure. A temperature sensor on the hot side of the heat exchanger (closed loop side) controlled the staging of the cooling towers and the speed of the variable speed drive cooling tower fans. Pressure differential transducers located at the index runs staged the cooling water pumps to maintain differential pressure. The welder tips are extremely sensitive to differential pressure, so very tight pressure tolerances have to be maintained at all times.
Car Assembly Plant
In the Car Plant, renovations required the relocation of the welder water system, together with the supply and installation of three new cooling tower pumps and three new circulation pumps.
The three cooling tower pumps were each 100 horsepower, electrically driven, and with a flow rate of 2670 US gallons per minute. The three circulating pumps were each 150 horsepower.
The distribution piping system extended over 3,000 feet, serving welding robots throughout the car assembly plant. The heat transfer, between the circulating (robot cooling) water and the tower cooling water, takes place in four plate-type heat exchangers.
SERVICES
Mechanical Engineering
PROJECT FEATURES
Status: Completed 2008
LOCATION
Oshawa, Ontario
KEY SCOPE ELEMENTS
Cooling tower system | Sensor-controlled temperature and differential pressure | Three cooling tower pumps @ 100hp with a flow rate of 2670 USGPM | Over 3000 feet of distribution piping serving robots throughout the car assembly plant
— Photos courtesy of General Motors of Canada