Location: Eastern Canada
Queen Elizabeth II Health Sciences Centre
Bayers Lake Community Outpatient Centre
The Outpatient Centre is part of the $2-billion redevelopment of the QEII Health Sciences Centre. The EllisDon Infrastructure Healthcare consortium led the P3 project. The Outpatient Centre was honoured as a Gold Winner by the 2024 Urban Design & Architecture Awards for its innovation and design excellence, and has also been certified LEED Gold under the LEEDv4 Healthcare rating system.
The Bayers Lake Community Outpatient Centre in Halifax was built as Nova Scotia’s first public-private partnership (P3) healthcare project and is its largest healthcare project to date. Its LEEDv4 Gold certification is the first in Nova Scotia and one of only approximately 50 facilities in the Canadian hospital sector to attain this status. Sustainability features include a stormwater retention pond to capture and filter 100% of rainfall, and an energy-efficient design that reduces energy consumption by 39%.
The Centre provides a range of patient services that do not require a hospital setting, including initial visits with specialists, post-surgery and post-treatment follow-up, blood collection, eye care clinic, physio and occupational therapy, diabetes and orthopedic assessments, rehabilitation services, 17 examination rooms, 24 dialysis stations, and diagnostic imaging (x-rays and ultrasounds). The Centre expects 28,000 clinic visits, and 30,000 x-ray and blood collection visits every year.
HH Angus provided mechanical consulting engineering to the project, which was completed on time and on budget. Kim Spencer, Director of HH Angus’ Healthcare Division, commented that “we were very pleased to be able to support this new facility with HH Angus’ deep experience in the P3 delivery model, and proven track record of thoughtful healthcare design.” HH Angus acted as the prime mechanical consultant, in affiliation with Dillon Consulting, a local sub-consultant. Our mechanical scope of work included HVAC design, with support from Dillon on plumbing and fire protection.
SERVICES
Mechanical Engineering
PROJECT FEATURES
P3 | 134,000 ft2 | 15-acre site | Part of a $2 billion redevelopment | Completed November 2023 | Gold Winner, 2024 Urban Design & Architecture Awards | LEEDv4 Gold certified
LOCATION
Eastern Canada
KEY SCOPE ELEMENTS
Prime mechanical consultant | HVAC | Fire protection | Plumbing design
Ministry of the Solicitor General | Infrastructure Ontario
Thunder Bay Correctional Complex (TBCC)
The TBCC involves replacement of aging jail and correctional facilities with a new 345-bed, multipurpose complex. Both the existing Thunder Bay Jail and Thunder Bay Correctional Facility are among the oldest provincially-run adult correctional facilities, built in 1928 and 1965 respectively.
The new TBCC updates automation and technology to address issues of health, safety and security, and introduces efficiencies around design, technology, and the use of space. HH Angus is providing mechanical consulting engineering and vertical transportation consulting to the EllisDon Infrastructure Justice design team.
The TBCC is targeting LEED Silver certification and LEED Resilient Design pilot credits through the United States Green Building Council. The design focuses on energy efficiency, healthy indoor environments and reduced greenhouse gas emissions. The complex will also include views of nature, allow ample natural light and feature dedicated Indigenous cultural spaces, such as smudging space and sweat and teaching lodges.
The new facility is the first of its kind for an Ontario correctional facility, incorporating design features that promote rehabilitation of inmates. It will also improve access to programming, living conditions and education, while updating automation and technology.
The TBCC project has presented several challenges to our design team, including a compressed schedule and the involvement of numerous stakeholders. It has also been interesting on a technical level: mechanically, the various modes of operation and interconnection of systems are quite complex, necessitating a high degree of flexibility within the capacity of the mechanical equipment. The building construction featured a precast exterior with block walls, requiring very close coordination with trades to align openings and allow access for equipment.
Due to the secure nature of the facility, the mechanical system was integrated seamlessly into the architectural features, all accessible equipment is provided in a secure location, and all building systems interact
with the BAS.
The facility will include a connection to an existing 50-inmate facility — the Thunder Bay Modular Built Facility — located southeast of the TBCC and currently under construction. The project also involves the design and construction of a 4,000 ft2 wastewater treatment facility to allow for a fully self-sufficient and self-contained facility.
SERVICES
Mechanical Engineering | Vertical Transportation
PROJECT FEATURES
$1.2 billion | 345-bed, multipurpose facility | 450,000 ft2 | Completion expected in 2026
LOCATION
Eastern Canada
KEY SCOPE ELEMENT
Design required careful consideration of all inmate-accessible areas | Compressed schedule | Close collaboration with trades to ensure pre-cast exterior elements align accurately with equipment access openings
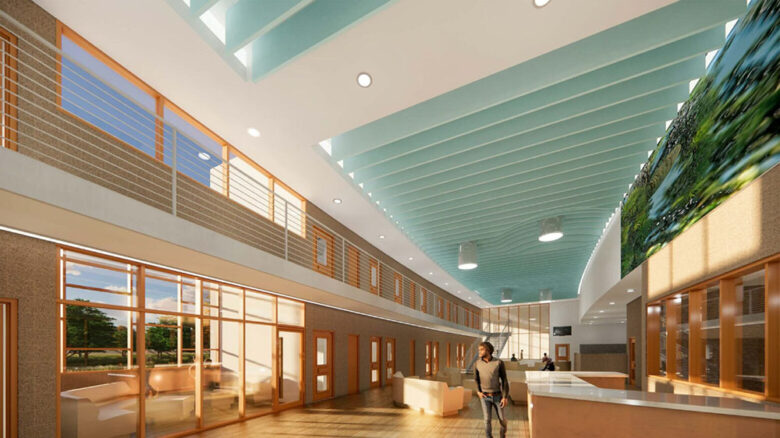
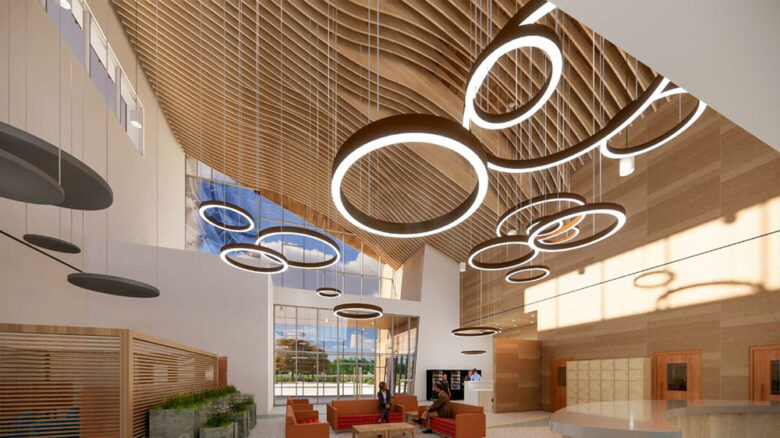
Images courtesy of Zeidler Architecture
Niagara Health System | Infrastructure Ontario
New South Niagara Hospital
New South Niagara Hospital is targeting LEED Silver certification and is being designed to be Canada’s first WELL-certified healthcare facility. The project was recently nominated for two CCPPP awards for excellence in public-private partnerships.
HH Angus is part of the design team under EllisDon Infrastructure Healthcare, the proponent to design, build, finance and maintain the new South Niagara Health Hospital project. The EllisDon Infrastructure Healthcare team includes:
- Leads: EllisDon Capital Inc. & Plenary Americas LP
- Design Team: Parkin Architects Ltd. & Adamson Associates Architects
- Construction Team: EllisDon Corporation
- Financial Advisor: EllisDon Capital Inc.
HH Angus is providing consulting services for conveyance systems (automated guided vehicles, autonomous mobile robots, and vertical transportation) and mechanical engineering as part of the design team. Of special note, we have designed the building’s mechanical HVAC systems to accommodate Indigenous ceremonies taking place not just in a few designated spaces, but throughout the patient care tower, so that patients do not have to be moved in order to take part in healing ceremonies.
The new facility will be a full acute care hospital with 24/7 Emergency Department, diagnostic, therapeutic, and surgical services. The latter will include medical, surgical, and intensive care inpatient beds. Also included will be ambulatory services; post-acute Complex Continuing Care (CCC) Inpatient services; and Centres of Excellence specializing in stroke, complex care, geriatric/psychogeriatrics, and wellness in aging.
The new hospital will integrate technology that supports innovation in and delivery of high-quality healthcare and will be designed to achieve LEED Silver certification. The design will also work toward being the first WELL™-certified healthcare facility in Canada.
Image courtesy of EllisDon Infrastructure Healthcare
SERVICES
Mechanical Engineering | Conveyance Systems Consulting (AGVs, AMRs and Vertical Transportation)
PROJECT FEATURES
Completion: Estimated for 2028 | Full acute care hospital | Targeting LEED Silver and WELL Certifications
LOCATION
Eastern Canada
KEY SCOPE ELEMENTS
~1.2 million ft2 | 469 beds, 8 ORs, 42 hemodialysis stations, 2 MRIs | AGV, AMR and VT planning and design | Mechanical engineering
Collège Bois-de-Boulogne
Server Room Air Conditioning
Pavilion Saint-Paul
One of the challenges of this project was to replace the main and redundant cooling systems in the server room while maintaining operations and minimizing impact on the College.
HH Angus’ scope of work for this project included analyzing the mechanical and electrical infrastructure of the server room, and proposing permanent corrective solutions. It also included implementation of solutions to provide redundancy for the mechanical infrastructure to guarantee full operation of the servers in the event of a critical power emergency or failure of the server room's main cooling system.
In order to analyze the existing installations, we performed site visits and surveys, and interviewed technicians responsible for the server room to gather as much information as possible about the existing installation, including any ongoing issues. We also reviewed and analyzed plans for the existing installation and performed a condition assessment - chilled water and glycol piping, insulation, ventilation ducts, electrical systems serving the equipment, and control systems - and took measurements in the mechanical and server rooms to ensure the new equipment could be properly installed while still providing space for maintenance work.
Following our analysis, we produced a report outlining the scope of work to refurbish the server room's cooling systems (main and redundant systems), ensuring the installation complied with current codes and standards. We produced mechanical and electrical drawings and specifications, including proposed solutions and equipment selection, and consulted with vendors to identify optimal solutions to meet the client’s requirements. During the tender process, we reviewed bids submitted by the contractor and provided recommendations to the College.
The intention was to complete this work over the summer when classes were not in session. Due to COVID-related delays in production of the necessary equipment, the work could not be completed on the original schedule and had to be undertaken when students were back in class. We worked very closely with stakeholders to avoid disruption to the students, with some work being completed before and after class or on weekends.
SERVICES
Mechanical Engineering | Electrical Engineering
PROJECT FEATURES
Analysis of mechanical and electrical infrastructure | Recommendations for permanent corrective solutions | Infrastructure redundancy in the event of critical power emergency | Status: Completed 2022
LOCATION
Montreal, Quebec
KEY SCOPE ELEMENTS
Analysis of existing equipment and installations | Design of new cooling systems
WPP
Toronto Waterfront Campus
WPP Group's building is part of the largest urban revitalization project in North America, bringing together new businesses, restaurants, and transport connections.
Work Design Magazine March 28, 2023
This cutting-edge project on Toronto’s downtown waterfront represents an evolution in commercial office development and reinvents how employees work together in Toronto’s rapidly evolving creative and technology sectors. The new space merges a large number of WPP’s operating companies and 2,000 employees into the top seven floors of the Waterfront Innovation Centre at the city’s iconic ‘Sugar Beach’. HH Angus provided engineering consulting services for this 250,000 ft2 tenant fitout project. WPP is the anchor tenant for the Waterfront Innovation Centre.
The fitout included raised floors for underfloor HVAC systems and is targeting LEED Platinum certification. On each floor, the design features a café, hub and IT equipment room, with one single Main Communications Room.
The 8th floor has a custom production area with very specific acoustic requirements. Our mechanical team worked closely with the acoustical consultant to provide a design that meets the strict acoustic requirements for video and audio production and recording. This was achieved through careful placement of fan-powered boxes equipped with silencers. The production area includes multimedia studios, photo studios and a print lab. Lighting control for these rooms is enhanced with tunable lighting, allowing users to adjust the colour temperature in real time.
The 10th floor is the client-facing floor and includes meeting rooms with fully-integrated AV, smart lighting control, open ceiling design concept (industrial design), a large point-of-sale catering kitchen with back of house facilities and an outdoor terrace.
Our communications team designed several interconnecting fibre risers to provide the client with the most cost effective solution and full redundancy to meet their current and future needs, and to ensure the system will continue to operate in the event of external critical failures.
SERVICES
Mechanical Engineering | Electrical Engineering | Communications Design
PROJECT FEATURES
250,000 ft2 colocation project unifying 28 different companies | Seven-floor fitout | Status: Completed 2022
LOCATION
Toronto, Ontario
KEY SCOPE ELEMENTS
WELL design principles | Pressurized raised floor systems with underfloor HVAC systems | Rigorous acoustic requirements for audio and video recording | Redundant interconnecting communications fibre risers to ensure system will operate in the event of external critical failures
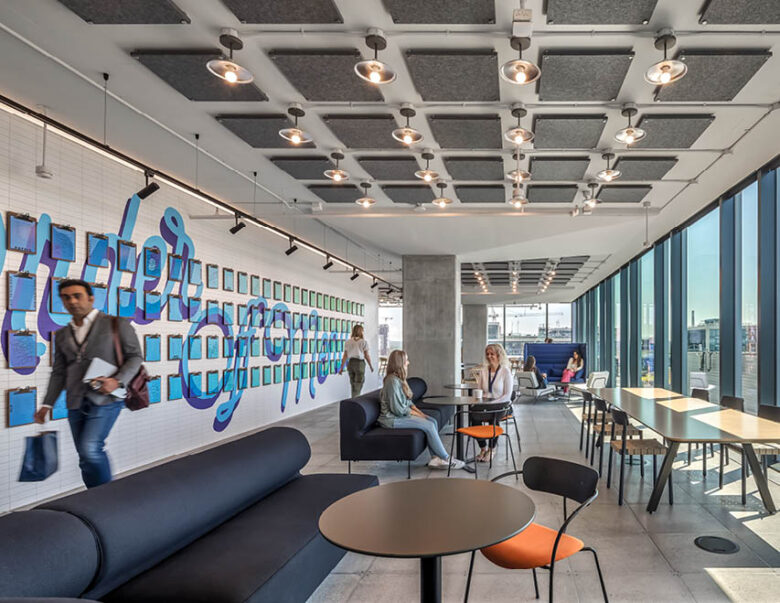
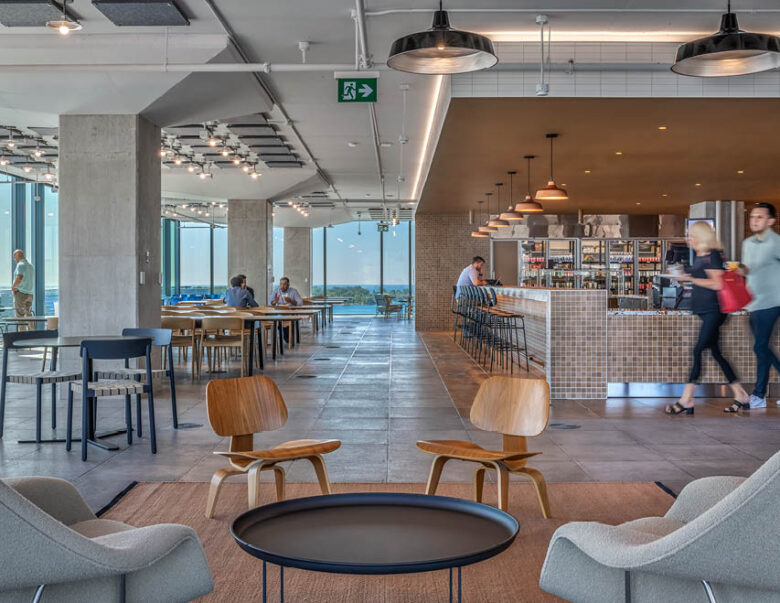