Location: Eastern Canada
Ontario Gaming GTA Limited Partnership
Great Blue Heron Casino
The Great Blue Heron Casino is located on Scugog Island, northeast of Toronto. HH Angus' scope for this project included electrical engineering, security and telecommunications consulting, and lighting design.
The first phase of the project featured a 20,000 ft2 expansion of the building to house gaming machines and tables, VIP rooms, bar and lounge, washrooms, offices, kitchen and service spaces.
HH Angus designed a new feeder, connected to the existing primary service, and full distribution throughout the expanded building and new outdoor generator. Telecommunications distribution required the addition of a new room to service gaming, corporate and security functions. The existing main telecom distribution room was expanded to support new networking and server equipment. In addition to horizontal distribution, new fiber and copper backbones, and incoming fiber service from Bell, was required to service the expansion. Upgraded and expanded surveillance and access control systems service the new gaming area.
The second phase saw renovation of the existing gaming floor and bar, buffet service and seating areas. The gaming area was completely reorganized for electronic games and a new Play Smart area. The front entrance also received a face-lift and new lighting. Phase 2 leveraged the earlier expansion of the main distribution room and upgrade for telecom distribution, and expanded on the security systems upgrade. As well, it included for a new 4 storey, 116 room hotel and connecting walkway, which required a second high voltage transformer in the existing substation to support the hotel operations.
Four telecommunication rooms were added, along with fiber and copper backbone connectivity. Additional surveillance and access control were included in the hotel scope. Phase 3 is still ahead.
Among the challenges of this project was an accelerated schedule for both design and construction. One solution was to develop strategies to save time on the design side and push the coordination into the construction phase.
SERVICES
Electrical Engineering | Telecommunications and Security Consulting | Lighting Design
PROJECT FEATURES
Size: 20,000 ft2 | Status: Phases 1 & 2 - Completed 2020 | Phase 3 tbd
LOCATION
Scugog Island, Ontario
KEY SCOPE ELEMENTS
Accelerated schedule | New 4 storey hotel and connecting walkway | Expansion of and upgrades to existing facilities, including significant expansion of telecommunications infrastructure and spaces

Meeting Challenges
A significant challenge of this project was completing all the renovations and expansions while the facility was fully operational.
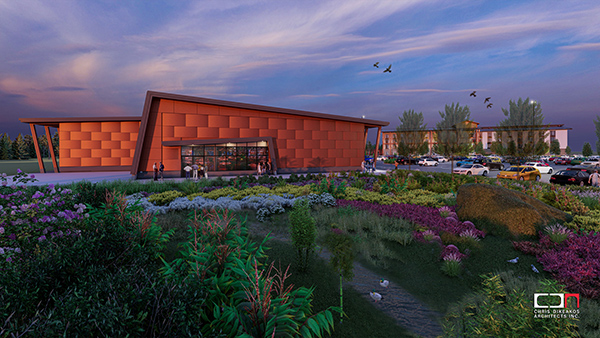
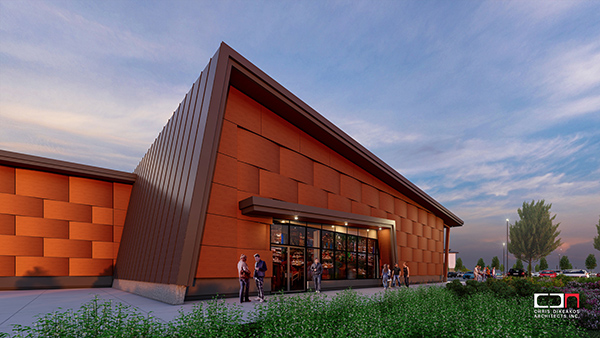
Renderings courtesy of Chris Dikeakos Architects.
GO Transit
Erindale GO Station Parking Structure
The 6-level parking structure, on Rathburn Road West in Mississauga ON, provides 1,740 parking spaces for GO Transit patrons.
Engaged as the Vertical Transportation (VT) consultant on this project, a design-build led by Kenaidan Contracting, HH Angus was responsible for overseeing the team’s effort in the development of vertical transportation system requirements. These included design coordination, tender and eventual participation in shop drawing reviews, progress field reviews, and acceptance services, with support from other direct report team members. HH Angus coordinated all stages of the VT work to ensure appropriate quality control standards were maintained through all phases of the project, and identified related work requirements associated with the elevating devices, permitting coordination of these with the remaining Design Team disciplines.
Six machine room less (MRL) traction elevators were provided - four in the Parking Garage, and two additional units serving the elevated pedestrian bridge connection down to track level.
SERVICES
Vertical Transportation Consulting
PROJECT FEATURES
Award winning project | 6 storey parking structure | 6 machine room less traction elevators | Status: Completed 2014
LOCATION
Erindale (Greater Toronto), Ontario
KEY SCOPE ELEMENTS
Development of vertical transportation system requirements | Identification of work requirements associated with elevating devices
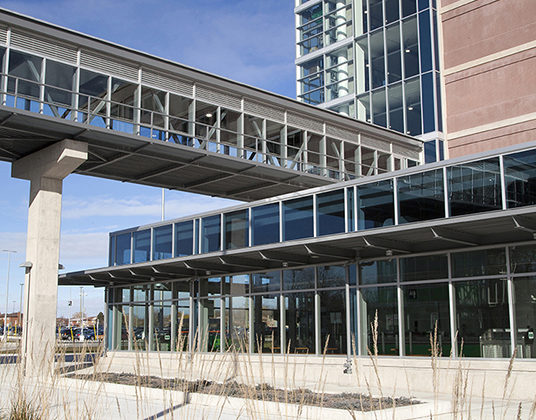
Award-winning project
The project was honoured with the 2014 International Parking Institute’s (IPI) Award of Merit and the 2014 City of Mississauga Urban Design Award of Merit.
Images courtesy of Kenaidan Contracting Ltd.
Oshawa Clinic Group
West Whitby Medical Clinic
The Oshawa Clinic Group is developing a new healthcare facility in response to the need for a large integrated medical office building to support the growing population of Durham Region.
HH Angus is providing M&E consulting services for this 120,000 ft2 clinic. The building is 4-storeys plus a basement fitout. When complete, the building will include primary care physicians’ offices and exam rooms, an urgent care walk-in clinic, and a range of specialist clinicians, including an audiology and hearing aid clinic, a chest pain clinic, chiropractors, dentists, diagnostic imaging, medical supply sales, a retail pharmacy with a compounding area, physiotherapy clinic, and a sleep study clinic with nine beds.
Additional patient services include:
- eye wear sales
- home respiratory equipment sales and services
- phlebotomy and medical test laboratories
- sterilization area, and
- traditional Chinese medicine clinic.
The project was featured in Canadian Healthcare Technology in July 2021.
SERVICES
Mechanical Engineering | Electrical Engineering
PROJECT FEATURES
Size: 120,000 ft2 | Status: Completion 2024
LOCATION
Whitby, Ontario
KEY SCOPE ELEMENTS
Purpose-built clinic | 4 storeys plus basement fitout | Primary care physician offices, urgent care walk-clinic | multiple specialized labs and clinics
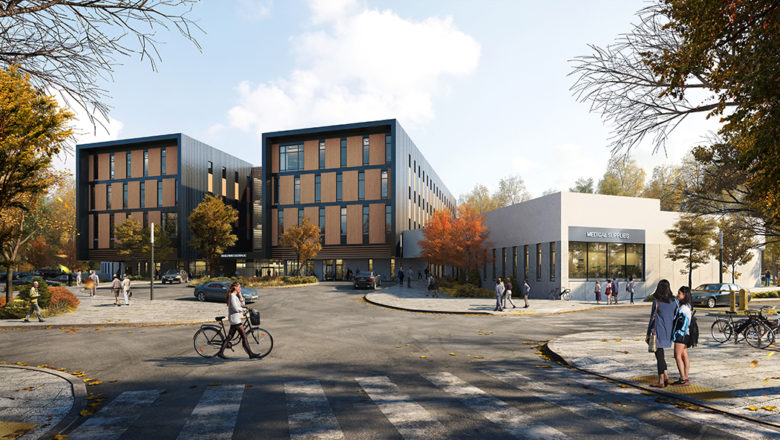
Customized design
The project is a purpose-built building in Whitby Ontario.
Renderings courtesy of Lett Architects Inc.
Sunnybrook Health Sciences Centre
Garry Hurvitz Brain Sciences Centre
“The Garry Hurvitz Brain Sciences Centre will revolutionize the future of brain health like never before. It will be a global hub of innovation that will accelerate the discovery of the next generation of treatments, prevention and possible cures to the world’s most debilitating brain conditions.”*
HH Angus is providing mechanical and Electrical engineering for this 118,285 ft2, three-storey above-grade structure. The building will be constructed within a dense urban campus between existing building wings and will be connected to the main hospital circulation spine, with flexibility provided to accommodate future expansion.
Our project scope includes:
- Expansions to existing infrastructure, including a new 1600 ton centrifugal 4160 volt Chiller;
- A major modification to the Emergency Power System to provide emergency power to at least one chiller and the chilled water distribution system;
- New steam service and high voltage electrical services to the new building from the existing power plant
- A significant Information Technology service and distribution system, including fibre cable connections to the hospital’s existing Core Distribution Rooms, new network hub room components, including network switches and all on-floor cable/outlet systems
- Significant expansions to the existing Building Automation System, central electrical metering system, fire alarm system, security system, CCTV system, nurse call system and Code White systems.
The new building includes:
- Mechanical and electrical services in the basement designed to provide for the current construction, as well as a possible future four-storey addition
- Adult In-Patient Mental Health Unit and PICU Unit on the ground floor, both with access to outdoor courtyards
- Child & Youth Mental Health Unit
- Circadian Study Unit on 1st Floor
- Neuromodulation Treatment Unit, Enhanced Examination, Teaching and Research units on the 2nd Floor
The Sunnybrook M&E services tunnel is a complicated space. Because this is a new building on an existing site and represents a major expansion to the campus, connections to existing buildings with multiple M&E ties are required.
Among the interesting challenges of this project was obtaining the required mechanical and electrical services spaces. The larger they became, the more they impacted the functional programming and the project budget. Compromises were made regarding ceiling heights, and collaboration with facilities management staff helped in obtaining the space required.
As well, the main entrance “glass box” presented some unique mechanical design challenges. Ventilating a two-storey structure with no exposed services required innovative engineering, including ventilating from below.
In designing the building systems for this project, our team devoted special attention to providing a living space that offers an excellent therapeutic environment for the brain-injured patient while, at the same time, ensuring the safety of both patients and staff; in particular, preventing any opportunity for self-harm by patients.
Within HH Angus’ lighting scope, LED linear fixtures set the stage for modern lighting aesthetics used throughout the new, state-of-the-art centre, including corridors, inpatient bedrooms, the main triple height lobby, and the exterior soffits. The efficient LED non-glare, dimmable lighting will be connected to a centralized lighting control system. The provided lighting management software enables facility managers to monitor, maintain and control the entire networked lighting control system, including schedules and energy usage.
SERVICES
Mechanical Engineering | Electrical Engineering | Plumbing | Lighting Design | Audio-Visual Design | Communications Design | Condition Assessment | Feasibility Study
PROJECT FEATURES
Size: 118,285 ft2 | Status: Ongoing | Adult In-Patient Mental Health Unit | PICU Unit | Child and Youth Mental Health Unit | Circadian Study Unit | Neuromodulation Treatment Unit | Complex M&E services tunnel
LOCATION
Toronto, Ontario
KEY SCOPE ELEMENTS
Expansion to existing infrastructure | Major modification to Emergency Power System | New steam service and high voltage electrical services | Significant IT service and distribution system | Expansion to numerous systems, including BAS, electrical metering, fire alarm, security, CCTV, nurse call and Code White
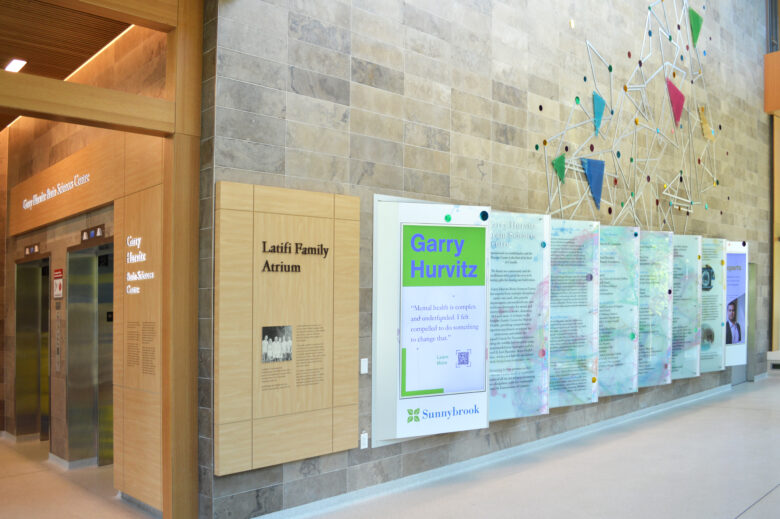
Innovative engineering
The main entrance “glass box” presented some interesting mechanical design challenges. Ventilating a two-storey structure with no exposed services required innovative engineering, including ventilating from below.
Experience counts
HH Angus’ many years of working on the Sunnybrook campus and our familiarity with this particular space aided significantly in designing the connections to the existing services.
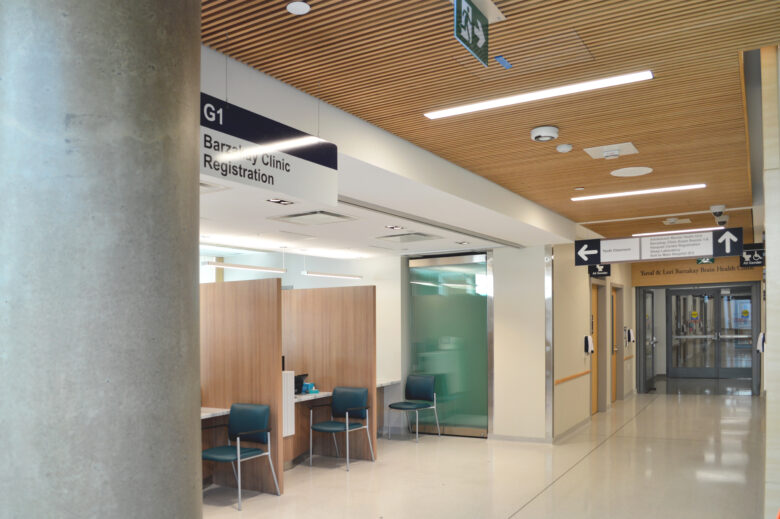
St. Joseph’s Health Centre
Mental Health Emergency Services UnitWe consulted with hospital clinical staff, the architect and best practices documentation in the field of Mental Health design in order to provide tamper-proof and anti-ligature versions of M&E devices and services in all patient rooms.
Our project scope was the complete redevelopment of the existing Mental Health Emergency Services Unit. This involved upgrading and modernizing the unit in order to support eight patient rooms, (the previous unit had only three patient rooms).
New, energy-efficient LED lighting fixtures, complete with dimming controls, replaced the old, inefficient fluorescent lighting fixtures. Remote patient room controls, located at the Nurses’ Station, allow clinical staff to control the electrical receptacle in each patient’s room, the smart glass on the room’s door/window, as well as the room’s lighting fixture, including remote-controlled dimming. A modern real-time locating system was also provided; it includes patient tracking, staff duress and patient wandering functionality. Note: This project was honoured with a 2020 Toronto IES Illumination Section Award
More than 30 IP-based security cameras were installed, including two cameras in each patient room. These are viewable from computers at the Nurses’ Station.
One of the challenges of the project was that the hospital did not have a viable existing IT room to house all the new voice/data infrastructure. As a result, we had to design a new IT room on the floor below the renovation area to support the new unit and future Emergency Department redevelopment. This was done during construction; therefore, the design and coordination were fast-tracked and subsequently completed successfully.
Also, remote patient room controls were not well defined throughout the design process. During construction, we had to quickly coordinate with several vendors, each with a proprietary system, in order to provide a solution that the contractor could execute.
SERVICES
Mechanical Engineering | Electrical Engineering | Communications and Security Design | Lighting Design
PROJECT FEATURES
Status: Completed 2019 | Winner: 2020 Toronto IES Illumination Section Award | Energy-efficient LED lighting | Remote room controls | Real-time locating service | 30 IP-based cameras | New IT room
LOCATION
Toronto, Ontario
KEY SCOPE ELEMENTS
Tamper-proof and anti-ligature M&E services | Design of remote room controls to provide enhanced staff safety and minimizing disturbance to patients | Fast-track design of IT room was required during construction stage
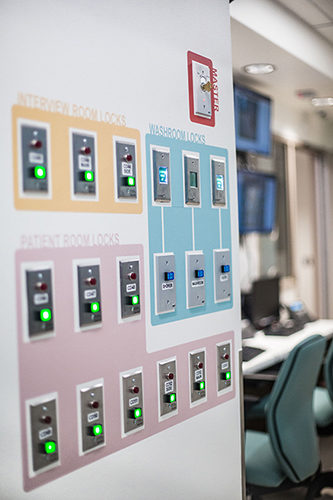
Remotely located controls
This approach provides increased staff security and convenience, and minimizes disturbance to patients.
Optimal visibility
A new security and communications design allows safe observation of patient activities from a secure staff area.
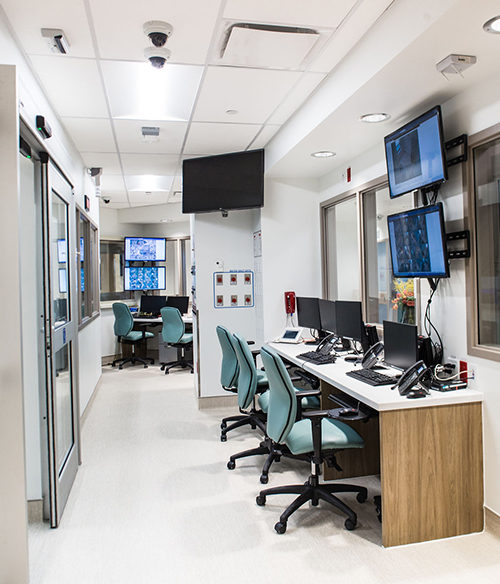