Location: Western Canada
TELUS
Len Werry Building Turbine Replacement
The TELUS Len Werry Building in downtown Calgary houses offices, computer facilities, toll switch equipment, and local switching equipment for a major toll complex.
The project involves the replacement of the building's existing turbines with new reciprocating diesel generators and redundant synchronization switchboards in a new penthouse on top of the building.
HH Angus is providing electrical engineering services to support upgrades to the electrical distribution system related to the installation of the new diesel generators.
SERVICES
Electrical Engineering
PROJECT FEATURES
Infrastructure replacement in occupied commercial tower | Status: Ongoing
LOCATION
Calgary, Alberta
KEY SCOPE ELEMENTS
Upgrades to electrical distribution system
The Co-operators Calgary
Tenant Fitout
This project focused on a tenant renovation of two floors in The Co-operators' newly-acquired downtown Calgary office space, and comprised 40,000 square feet. The project has been certified WELL Gold.
Our approach included early coordination with the landlord to ensure handover conditions suited the client’s requirements, as well as close coordination with the construction manager in creating a pre-order due to a condensed construction schedule.
The construction schedule was a key challenge of the project along with the timing of tender. The completion date was an unmovable milestone as the client’s lease was expiring at their other location. At time of tender, product and material availability were fluctuating, which created uncertainty around delivery. To meet the deadline, our team was tasked to do everything possible to ensure the success of the project and keep the schedule on track.
To help ensure timely delivery, our team incorporated a pre-order package for the construction manager to tender, which allowed products to be reviewed and released ahead of the official tender. This effort was successful and was completed according to plan; however, some delivery delays were unavoidable, due to market conditions. To mitigate the impact, we were then tasked with contacting industry partners to help expedite deliveries. In addition, alternative temporary designs were implemented to ensure the move-in date could be met by planning the switchover date once the outstanding equipment arrived.
The Calgary office marks our fifth tenant improvement project for The Co-operators, following similar fitouts for their locations in Guelph ON and Regina SK, as well as pilot projects in Montreal QC and Burlington ON.
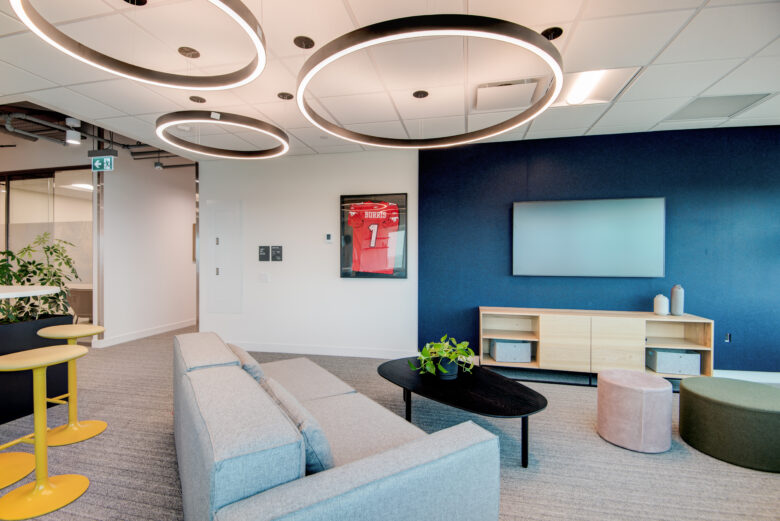
New Lutron lighting control design
New UPS N+1 Design and new LED Lighting Design
SERVICES
Mechanical Engineering | Electrical Engineering | Lighting Design | Communications & Security Design
PROJECT FEATURES
Size: 40,000 ft2 over two floors | Status: Completed 2023
LOCATION
Calgary, Alberta
KEY SCOPE ELEMENTS
Feasibility Study | Tenant renovation | Condensed construction schedule | WELL Gold certified
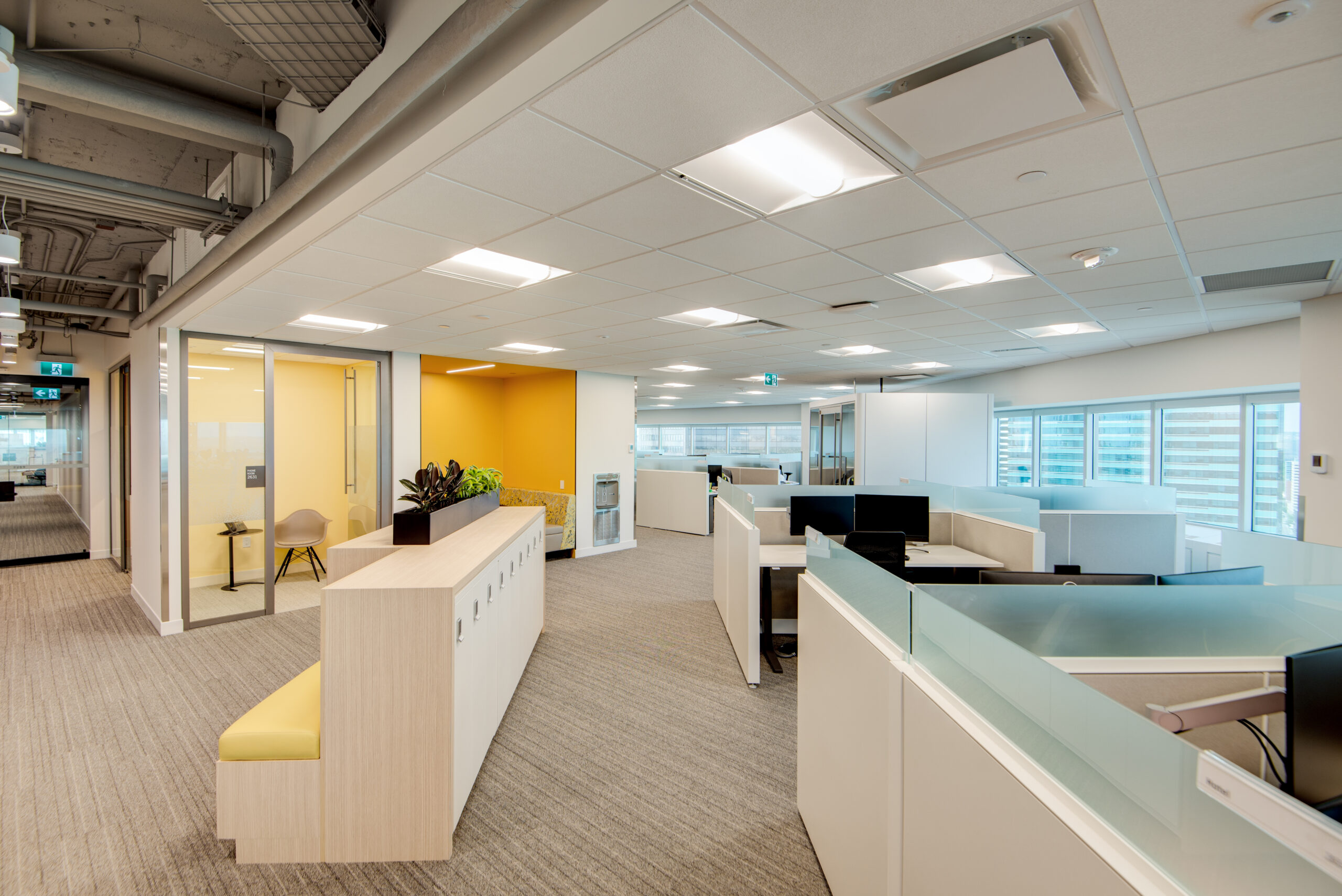
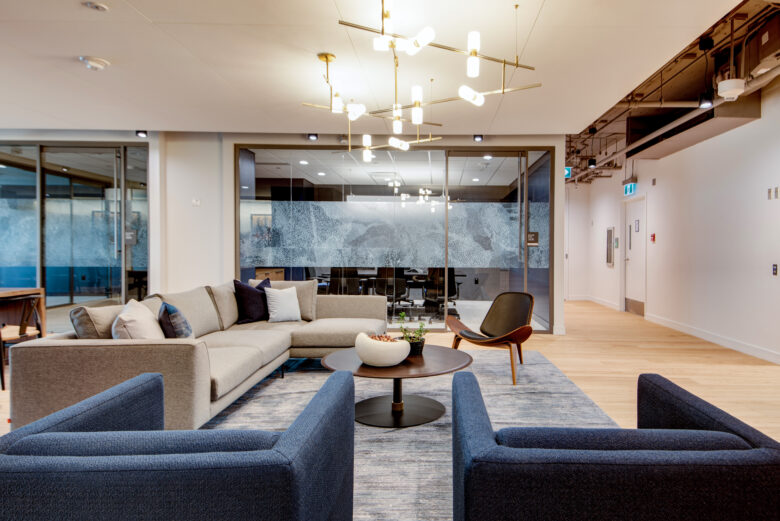
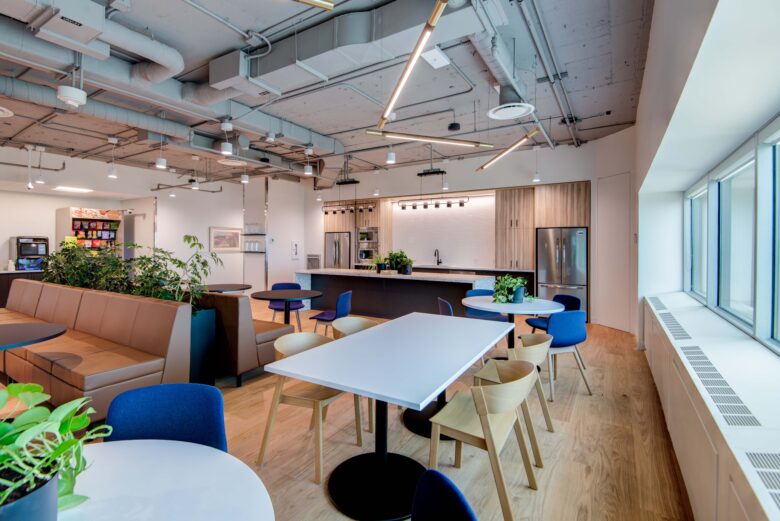
Fraser Health
New Surrey Hospital and BC Cancer Centre
Surrey BC is a fast-growing community in need of additional healthcare resources. The New Surrey Hospital and BC Cancer Centre will provide 168 hospital beds and 55 Emergency Department treatment spaces in a state-of-the-art facility to improve health services in the region.
The $2.88B hospital project reached its one-year construction milestone in August 2024 and is anticipated to be completed in 2029 and open to the public in 2030. Additional features of the fully-electric facility include a surgical/perioperative suite with five ORs, four procedure rooms and virtual care options in all clinical service areas to increase capacity and expand care. The new BC Cancer Centre is expected to provide approximately 105,000 ambulatory oncology care visits, 50,000 radiation therapy visits and 22,000 chemotherapy visits each year. The facility is being built under a Design-Build Agreement with EllisDon Design Build Inc.
Leading BC's first generation of smart hospitals, the new Surrey hospital will embed data insights and new technologies into both the design of the facility and delivery of clinical care. The Angus Connect team is providing a full spectrum of ICAT/IMIT design and AGV consulting, and HH Angus’ Vertical Transportation team is designing the elevator systems.
Images courtesy of Fraser Health and EllisDon Design Build – conceptual renderings, subject to change
SERVICES
ICAT/IMIT Design | AGV Consulting | Vertical Transportation Consulting
PROJECT FEATURES
Smart hospital | Fully electric facility | Design Build | 168 hospital beds, and 55 ER beds | Perioperative suite with 5 ORs and 4 procedure rooms | Status: Completion anticipated for 2029
LOCATION
Surrey BC
KEY SCOPE ELEMENTS
Information, communications and automation technology | Automated guided vehicle design consulting | elevator design consulting
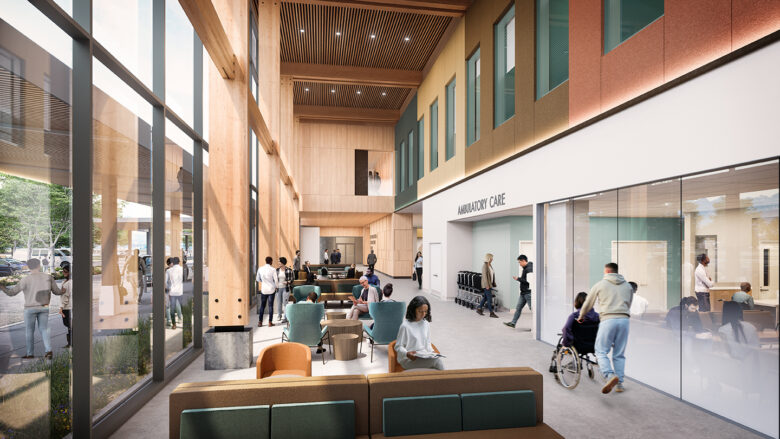
New BC Cancer Centre
The facility will provide ~105,000 ambulatory oncology care visits, 50,000 radiation therapy visits and 22,000 chemotherapy visits annually.
Smart hospitals
The NSHBCCC is one of BC's new generation of smart hospitals.
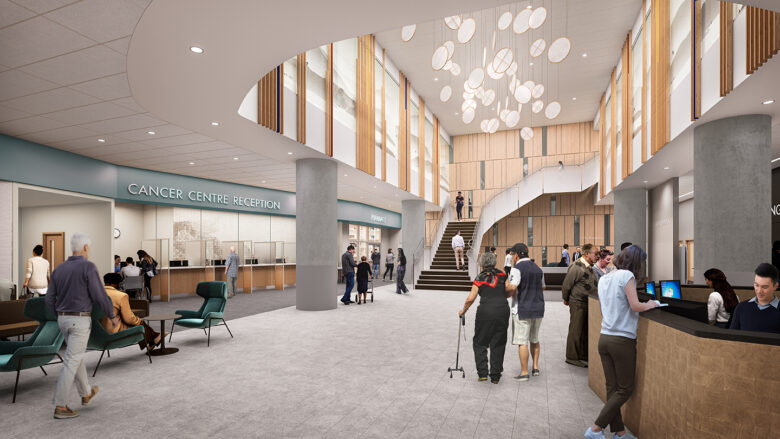
Lonsdale Energy Corporation
Heat Recovery Feasibility Study
HH Angus conducted a study to evaluate the feasibility of exhaust air heat recovery from the Global Relay (GR) data centre facility at 22 Gostick Place in North Vancouver, BC.
Some of the key aspects of the study included:
- The location and footprint of the heat recovery system components were studied within the context of considerable site constraints. The study evaluated the design, construction, and cost considerations for the implementation of the proposed heat recovery system.
- We investigated available heat pump technologies that would be appropriate for recovering waste heat and would satisfy the LEC DES requirements.
- The energy recovered would be used by a water source heat pump to provide hot water to the local LEC District Energy System (DES).
- A water source heat pump system was proposed as the best solution to provide the ability to recover heat from the building ventilation system. The new system would recover heat from the GR facility and would transfer this recovered heat via a hot water loop to the local LEC DES.
- Heat recovery is feasible for the facility and can provide up to 1,100 kW of heating capacity to the LEC DES.
- Constraints to the design of the heat recovery system were also identified, and included:
(i) the quantity of air exhausted from the facility is not fixed and ranges at each exhaust plenum on a seasonal basis and depending on outdoor air temperature – this impacts how much heat can be recovered at a given time;
(ii) the minimum and maximum exhaust air temperatures range from 30°C to 43°C (86°F to 110°F) - the temperature of the exhaust air will influence how much heat can be recovered from the exhaust air; and,
(iii) the cross-sectional area available for the heat recovery coil - the more cross-sectional area that is available for a given amount of heat transfer, the less deep the coil must be (and less airside pressure drop penalty is incurred).
The study concluded that a purpose-built containerized heat pump system would be the most suitable solution to meet the needs of the project. This new containerized structure would be conveniently located adjacent to the GR facility and would exhibit the same architectural character as the existing facility. The proposed heat pump system would include one heat pump unit (based on Emerson Heat Pumps) and four heat recovery water pumps. Control valves, piping accessories, ventilation, lighting, and system controls would all be included in the proposed pre-fabricated containerized enclosure.
Outdoor hydronic piping would connect the heat pump enclosure to the GR facility and the proposed hydronic heat recovery coil system. The heat recovery coil system would consist of four new heat recovery coils placed within the existing facility exhaust air plenums. The existing exhaust fan motors would have to be upgraded in order to address the additional pressure drop introduced by the new heat recovery coils. This fan motor upgrade would also trigger upgrades to the existing electrical infrastructure.
SERVICES
Prime Consultant | Mechanical Engineering | Electrical Engineering
PROJECT FEATURES
Size: 5,600,000 ft2 | Status: Ongoing
LOCATION
Vancouver, British Columbia
KEY SCOPE ELEMENTS
Feasibility study | Heat recovery
Oakridge Centre
Redevelopment
Vancouver's Oakridge Centre is a visionary mixed-use redevelopment of approximately 4.3 million square feet, plus residential areas. The work will be completed in two phases and will encompass a vibrant mix of retail, office, residential, cultural, and civic spaces, along with a landscaped rooftop park.
HH Angus provided fire protection Engineer of Record design services for approximately 2.5 million ft2 of the retail, parkade and service areas, as well as peer review of the central plant engineering.
An interesting aspect of our project scope is the multiple water parcels and phasing, which meant needing to design each section with expansion in mind. Our project design work is being completed entirely in Revit, with a program called Autosprink that allows us to place the sprinkler heads and then connect them to provide highly-detailed hydraulic calculations. This involves laying out heads, branches and mains, and performing all calculations to present for sprinkler permits. The design also includes multiple fire pumps and a back-up cistern to store water on-site for use in the event of waterflow emergency.
The project requires a strong focus on effective communication. Our team's seamless collaboration with multiple partners and consultants through open and inclusive communication channels encouraged the flow of information and ideas, fostering creative problem-solving and innovative solutions. These often required coming up with alternative code-compliant solutions.
Despite only joining the project during design development, we successfully applied cutting-edge software and project management techniques to deliver our assigned scope within the designated time frame. As a result, we have been awarded additional project scope and the opportunity to further contribute to the overall success of the project.
SERVICES
Fire Protection, Phase 1A & B | District energy plant peer review
PROJECT FEATURES
2,600 residences | Office space for 3,000 workers across multiple towers | 2.5 million ft2 of retail, parkade and service areas | Status: Completion estimated for 2027
LOCATION
Vancouver, British Columbia
KEY SCOPE ELEMENTS
Our team's close collaboration with multiple partners and consultants through open and inclusive communication channels encouraged productive flow of information and ideas, fostering creative problem-solving and innovative solutions
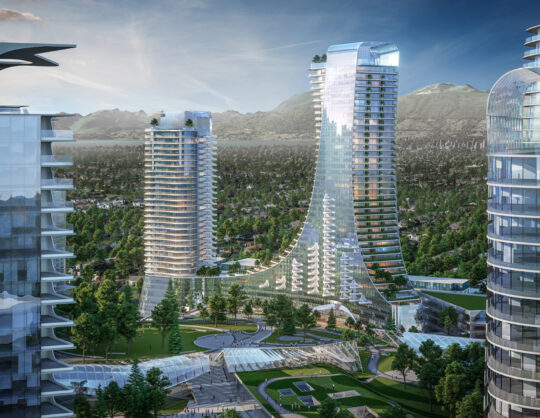
Photos courtesy of Adamson Associates Architects.
Efficient resource allocation
Given the vast scale of the project, it has been important to identify critical resource needs and to optimize their deployment in order to avoid bottlenecks.