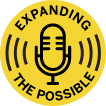
Episode 8 “Energy Master Planning”
Expanding the Possible: Energy Master Planning EP- 08
Welcome to Expanding the Possible. This podcast series from HH Angus explores how engineering is advancing the built environment. From innovations in building systems to the Internet of Things, from digital services connecting the modern workplace to combating the impact of climate change, we delve into exciting developments in today's and tomorrow's building infrastructure.
Hello, I'm Kirsten Nielsen. In today's podcast, we're exploring energy master planning for multi-building and campus infrastructure. Joining me from HH Angus’ Energy Division, are Sabari Manoharan, and Justin Lau. Justin and Sabari are mechanical engineers, and both are experienced in large infrastructure upgrade projects.
Kirsten:
Welcome, Justin and Sabari. Let's start Justin with you. Set the scene for us today. How do you define what an energy master plan is?
Justin:
Well, I'd say that energy master planning is, in essence, a really simple concept that most people are already quite familiar with, and that's simply to look ahead before committing and diving headfirst into doing something. So, for large campus facilities with multiple interconnected buildings, taking the time and effort to come up with a master plan is particularly important to ensure that projects undertaken are in alignment with the overall vision and long-term objectives of stakeholders. So, some of these objectives may include reducing carbon emissions and lowering utility costs, all while improving reliability and resiliency of the overall system.
HH Angus service offerings for energy master plans are categorized by various stages of implementation. We do aim to remain flexible in execution depending on the specific client needs. During the planning advisory stage, we work with the owner in an overall visioning, facilitating workshop for sustainable design, looking into government incentives and other green certification. During the feasibility analysis stage, some of our offerings would include energy modeling, utility coordination, design assist and optimizations, and business planning. And then during the design and concept development, we provide tailored and coherent solutions that fit in with the overall planning effort that has taken place. And finally, during the post-project phase, some of our offerings would include training and education for facility staff in the relevant topics.
Kirsten:
So, we're talking about multi-building and campus infrastructure here. What do you include in those categories, Sabari?
Sabari:
We are typically considering manufacturing facilities that may include HVAC and process space loads for these facilities; government research facilities; there are post-secondary institutions such as colleges and universities, like the entire campus, as well as district energy plants serving multiple buildings and hospitals. An important thing to notice here, at least for campuses is, basically, what's common with these facilities is that they're networked through large services that may not be immediately visible to most people. These include underground services, buried services that may run through the entire campus. These may be service corridors that people may not see. But all these aspects go into planning for the future and saving space, etc.. These networks are typically serviced by one or more central plants. There are multiple approaches to addressing the needs of an entire campus. Sometimes there's the centralized approach where you would feed the entire campus with one central plant, whereas other times it might just make more sense to decentralize and have a facility near where the load is.
Kirsten:
Justin, what would you describe as the characteristics of an effective energy master plan? What goes into that, and whose input are you looking for to create an effective plan?
Justin:
I think that one major hurdle is that greenfield projects are more of the exception rather than the norm. So, in other words, there's always limitations, instead of having a blank canvas to build on. Older facilities tend to have undergone various stages of upgrade, so, the documentation could be a little bit obsolete or not reflective of the actual conditions. Upon closer review, different parties might have different visions on what the right solution looks like. So, I would say that effective planning really starts with the information gathering stage. It's very important to ask the right questions of the right people, engage them meaningfully and early on to understand what's important from their individual perspectives. Very commonly, stakeholders would include the capital planning and project management groups, which sometimes would have more of a focus on the financial aspects and project scope definition. Whereas the operations and the engineering teams on the client side would be much more intimate with their existing systems, any nuances that they have which may not be immediately apparent.
So, it's really important to pay attention to these things. At the end of the day, there's no single right solution or best way to plan, but I do believe that effective planning needs to respect the complexity, history, and uniqueness of every building system and individual client group that we work with.
An effective plan should have a balanced approach relative to the level of detail and complexity for the end user, with great care taken so we don't create new problems and solving existing ones. We can achieve this with ongoing engagement during the different iterations of planning, using the right technology for the application, planning for some flexibility and future unknowns, using a hybrid approach when it's appropriate. And of course, HH Angus is often also the prime consultant, so we need to coordinate effectively with all the project partners for their input. In addition to mechanical and electrical design, some of these would include civil, structural, environmental, geotechnical consultants, or controls contract that contribute a different role to the overall plan.
Kirsten:
Sabari, how far into the future should an energy master plan be looking? And typically, what drives the decision as to how long it should go on.
Sabari:
For smaller, quote unquote, smaller developments, we're looking at roughly a time of 5 to 20 years into the future; for larger developments that could extend up from 20 to 30 years. What typically drives this decision comes down to essentially our clients. We have to understand what their plan is for future growth. For manufacturing facilities, that could mean any additional production that they see in the future.
On the energy side of things, this may be additional customers that need heating or cooling. So that expansion is something that we need to relatively understand now. Overall, so we can't quite understand all aspects of it. But a few other factors may involve understanding the capital cost of these new installations or these new retrofits, and quantifying the risk in this from a financial point of view, that's quite important. Items such as equipment delivery time come into play here that may disrupt day-to-day services.
Another factor to consider is possibly a change in government means this may bring about a few new incentives. It may take away a few incentives. It may bring in a few bans on certain elements, certain materials, etc. And so that is a realm where, you know, one can do their best to predict it, but it's still quite unknown. So, I guess at the end, there has to be an understanding that this is in fact just a plan. It can't be rigid. And we work to make it flexible enough to adapt as the environment changes in the future.
Kirsten:
We can't really talk about energy master planning without also talking about feasibility studies and energy modeling and road mapping. Those are going to be the subject of a future podcast. But Justin, for our discussion today, can you just talk briefly about how an energy master plan is informed by those types of investigations and exercises?
Justin:
I think it's important to just go into briefly what those terms actually mean, feasibility study and energy modeling and sort of the typical context. It can be quite difficult to demonstrate a value of any plans or in other words, how much of an impact the change is going to have relative to how much it's going to cost without metrics and numbers and feasibility studies and energy modeling, essentially is what bridges this gap.
So, with some level of estimation and quantitative analysis before making a decision to fine-tune design details specifics, energy modeling can vary in the level of complexity. It could be on an hourly basis or some other time scale. But the overall goal is to estimate the heating and cooling load consumptions based on available information, whether data specific to the location, any energy metering, trending data that may be available, gas, hydro and water, utility bills, and even any anecdotal information that may be available from the operational staff that could help to form a more complete overall picture.
Once we have this energy profile, we now have some more insight into what's sort of the right approach with sizing of the plant. We evaluate the model against different options that the owner may want to explore and compare in order to understand the financial damage, so to speak, relative to what they get in the return, or also what we call the simple payback on the investment. One way to do this would be to calculate it based on the energy savings, versus the capital cost estimate of each of the options.
The specifics of the options would also depend on what level of planning is expected, and it can be about diversification of the asset technologies between electrification and perhaps some portion remaining on gas, depending on site utility limitations. It could be phasing in retrofit versus full replacement, or even looking at different manufacturers with varying levels of performance and maintenance needs, relative to the energy loads. Of course codes and standards are also a key aspect of the study. Some of these would include the Ontario Building Code, city bylaws, CSA standards and TSSA.
Sometimes the owner may also want to place some greater emphasis towards cost estimates, and we work with cost consultants to develop those areas. Or, if they wish to take on some of the additional financial analysis. In those cases, we may assist with the technical specifics to support their forecasting and modeling.
Kirsten:
Certainly, it takes a lot of expertise to put that kind of plan together. Okay, we've been talking about overview and generalities. Let's get down to some specifics here. Sabari, all across HH Angus, I'm hearing engineers talking about decarbonizing buildings, and reducing the carbon footprint of our clients’ assets. I'm also picking up a sense of excitement because these projects are not only interesting to work on, because they present some unique technical challenges, but they also provide important environmental benefits for the communities in which they're located. Tell us about some of the projects you're currently working on and what these involve.
Sabari:
For sure. Yeah, there's quite a bit of excitement. We get to possibly use newer technologies, etc., to help the environment. In terms of projects we're currently working on, there is a project, a steam plant that is being designed for the downtown Vancouver core, and this is a relatively large steam plant. There is basically introducing four 11 megawatt electric boilers to essentially reduce the demand of natural gas from the gas fired boiler side of the steam plant. Now, it must be understood that the electric boilers will be running most times satisfying the loads, while the gas boilers will be used in the cases where there's too much load for the electric boilers to handle. So, they'll be working with one another, but it'll mainly be the electric boilers taking up most of the loads for this project. In fact, early earlier in the project, there was a study conducted not by us, but we were looking at this study, where there was an argument for biomass, essentially wood pellets being used. In conclusion, we determined that introducing a biomass plant, the overall size just wouldn't work out. And electrification doesn't take too much space. Now it is a bit on the grid, but it's the best solution.
In addition, another project that I could speak of is one of the steam plants in downtown Toronto. We're going to be introducing heat pumps into this plant to once again reduce the load on the natural gas-fired steam plants, ergo reducing the carbon emissions there and I mean, of course, that comes with its challenges, but it's to benefit the environment by reducing our carbon footprint from these plants, which are so essential to us.
Kirsten:
Successful implementation of a master plan necessarily involves managing risks. Justin, what are some of the risk factors that you typically discuss with owners during energy master planning?
Justin:
Because of the long timeframes that these master plans often extend to, and with the involvement of so many stakeholders, it's a fairly complex landscape with, evolving technologies, regulatory requirements that are changing and, with respect to economic conditions, cost escalation is just one of the many risk factors. So, while feasibility studies may address some quantifiable cost benefits perspectives, there are some areas that are also not quantifiable; for example, the new dependency on utility grids or other types such as biomasses, as Sabari has mentioned, the emergence of competing technologies and in more detail assessment factors including governance and tax policies, inflation, and bank interest rate assumptions - these are all risk factors in a model which ultimately inform the master plan.
Other social and economic risk factors we look into from past experience, and we provide an opinion on, are the perceived level of risk, we look at the greenhouse gas emissions reduction potential in terms of production of C02; so, for example, comparing the level of electrification relative to other combustion fuel types, the impact to the public - for example, running a large industrial plant in an urban area can be quite disruptive to the public with emissions, noise and all of that - future-proofing, meaning understanding potential future expansion needs of the facility and the business, looking into planned space uses and relocations versus what actual spaces are available now for this anticipated expansion.
Another risk is also, with any change, what are the implications for additional training for the staff and additional service calls and maintenance requirements.
Kirsten:
Sabari, HH Angus is now a 100% BIM company. Why is it important to facility owners and how does being 100% BIM create value for our clients?
Sabari:
Being 100% BIM, what it does, at least from my perspective, is essentially it saves time on the design and as you know, time is money. So how it saves time is basically coordination between other teams within a project, whether it be consultant teams, contractors, etcetera - having that ability to proactively work on a singular model whilst taking into account other systems. I'm going to speak based on central plants, but within essential plants you'd have base building systems, there are structural components, other mechanical systems, heating systems, cooling systems, etcetera, and whether it be piping or ventilation, having that ability to deal with it in real time rather than asking for, let's say, a drawing set to be sent over and then coordinating, putting that on an AutoCAD background that we have and it just makes the entire process quicker. And that ability, I think, helps us save time in these projects, getting us to our end solution a lot quicker.
In addition to that, there are other capabilities of BIM and, from a design point of view, we have the capacity, once the piping or ventilation is completed, to understand flows within BIM, understand pressure losses. I do need to mention that at the end of the day, the designer, it would be best to review those numbers, etcetera. However, we do have that capacity to get those high-level numbers from BIM, which is great for us in terms of timing.
Kirsten:
What are the implications for project delivery compared to traditional design bid build that designers and engineers may be used to seeing in the past?
Sabari:
So, from a project delivery standpoint, as I guess I mentioned before, we do get to the end solution, in my opinion, a bit quicker, so that may reduce the schedule, etcetera. However, another aspect that I've noticed is when it's all either on the cloud or online, the computer always has a memory of what's being done, whether we need to document it or not.
There's always going to be documentation in the form of a timestamp. And BIM has the ability to spit out schedules, other important documents just from the model itself. And there's equipment lists or bill of materials that can be spit out from BIM, which saves us a lot of time, rather than going through each system and figuring that out. And yeah, overwhelmingly, I think that aspect of being able to document everything, understanding we don't need a separate record, although it's good to have, we don't need it on the side. And we can rest easy knowing that there's a timestamp on most of these documents being sent out, etcetera, and we can figure out how to trace certain documents back. I think it's really important, especially if you're trying to organize, managing a project and sending out deliverables, etcetera. It's a very useful tool in that manner.
Kirsten:
So, we're talking a little bit about ‘time is money’. Justin, I want to talk to you in a different aspect about cost. Energy consumption is a huge part of any facility's operating costs. What risks are owners running if they're not actively planning for their energy future?
Justin:
So, without proactive planning, I think that owners place a great risk in terms of extensive and sometimes unfeasible rework to correct these uncoordinated efforts and poor capital planning. These could result in delayed design and construction project timelines and, ultimately, incurred costs from poor phasing and execution of the work.
As noted earlier, construction design is fundamentally complex with many parties involved and, in particular, navigating the regulatory framework. Adhering to technical standards can place limitations against the overall objective to reduce project capital. So, one good example would be domestic water systems in healthcare facilities. We need to have them at elevated water temperatures at the right part of the system to prevent Legionella while avoiding scalding building occupants. And having the elevated temperature also fundamentally means that we're working against the competing objective of energy conservation.
Another example would be redundancy requirements from CSA codes. Essentially, depending on the code interpretation and how you interpret it, it could essentially put a multiplier on your capital if you don't consider it carefully ahead of time and plan accordingly. So overall, I think that owners can expect less resiliency against the risk factors that we've talked about today. All of this can amount to a significant loss of opportunity over time and through the operating life of the asset that often ran for decades. So, I think that retaining HH Angus as a trusted and experienced advisor early on in the planning stage from start to finish will help to mitigate and avoid these preventable pain points and pitfalls. There's less effort for the owner and better outcome overall to the end users and the public.
Kirsten:
So the takeaway advice is make sure you have an effective energy master plan. Thank you, gentlemen. Our guests today have been Justin Lau and Sabari Manoharan of the Energy division of HH Angus. If you'd like to learn more about our Energy Master planning services and low carbon solutions, you can drop a line to Justin and Sabari at lowcarbon@hhangus.com. Thank you for joining us for this episode of “Expanding the Possible!
Welcome to Expanding the Possible. This podcast series from HH Angus explores how engineering is advancing the built environment. From innovations in building systems to the Internet of Things, from digital services connecting the modern workplace to combating the impact of climate change, we delve into exciting developments in today's and tomorrow's building infrastructure.
Hello, I'm Kirsten Nielsen. In today's podcast, we're exploring energy master planning for multi-building and campus infrastructure. Joining me from HH Angus’ Energy Division, are Sabari Manoharan, and Justin Lau. Justin and Sabari are mechanical engineers, and both are experienced in large infrastructure upgrade projects.
Kirsten:
Welcome, Justin and Sabari. Let's start Justin with you. Set the scene for us today. How do you define what an energy master plan is?
Justin:
Well, I'd say that energy master planning is, in essence, a really simple concept that most people are already quite familiar with, and that's simply to look ahead before committing and diving headfirst into doing something. So, for large campus facilities with multiple interconnected buildings, taking the time and effort to come up with a master plan is particularly important to ensure that projects undertaken are in alignment with the overall vision and long-term objectives of stakeholders. So, some of these objectives may include reducing carbon emissions and lowering utility costs, all while improving reliability and resiliency of the overall system.
HH Angus service offerings for energy master plans are categorized by various stages of implementation. We do aim to remain flexible in execution depending on the specific client needs. During the planning advisory stage, we work with the owner in an overall visioning, facilitating workshop for sustainable design, looking into government incentives and other green certification. During the feasibility analysis stage, some of our offerings would include energy modeling, utility coordination, design assist and optimizations, and business planning. And then during the design and concept development, we provide tailored and coherent solutions that fit in with the overall planning effort that has taken place. And finally, during the post-project phase, some of our offerings would include training and education for facility staff in the relevant topics.
Kirsten:
So, we're talking about multi-building and campus infrastructure here. What do you include in those categories, Sabari?
Sabari:
We are typically considering manufacturing facilities that may include HVAC and process space loads for these facilities; government research facilities; there are post-secondary institutions such as colleges and universities, like the entire campus, as well as district energy plants serving multiple buildings and hospitals. An important thing to notice here, at least for campuses is, basically, what's common with these facilities is that they're networked through large services that may not be immediately visible to most people. These include underground services, buried services that may run through the entire campus. These may be service corridors that people may not see. But all these aspects go into planning for the future and saving space, etc.. These networks are typically serviced by one or more central plants. There are multiple approaches to addressing the needs of an entire campus. Sometimes there's the centralized approach where you would feed the entire campus with one central plant, whereas other times it might just make more sense to decentralize and have a facility near where the load is.
Kirsten:
Justin, what would you describe as the characteristics of an effective energy master plan? What goes into that, and whose input are you looking for to create an effective plan?
Justin:
I think that one major hurdle is that greenfield projects are more of the exception rather than the norm. So, in other words, there's always limitations, instead of having a blank canvas to build on. Older facilities tend to have undergone various stages of upgrade, so, the documentation could be a little bit obsolete or not reflective of the actual conditions. Upon closer review, different parties might have different visions on what the right solution looks like. So, I would say that effective planning really starts with the information gathering stage. It's very important to ask the right questions of the right people, engage them meaningfully and early on to understand what's important from their individual perspectives. Very commonly, stakeholders would include the capital planning and project management groups, which sometimes would have more of a focus on the financial aspects and project scope definition. Whereas the operations and the engineering teams on the client side would be much more intimate with their existing systems, any nuances that they have which may not be immediately apparent.
So, it's really important to pay attention to these things. At the end of the day, there's no single right solution or best way to plan, but I do believe that effective planning needs to respect the complexity, history, and uniqueness of every building system and individual client group that we work with.
An effective plan should have a balanced approach relative to the level of detail and complexity for the end user, with great care taken so we don't create new problems and solving existing ones. We can achieve this with ongoing engagement during the different iterations of planning, using the right technology for the application, planning for some flexibility and future unknowns, using a hybrid approach when it's appropriate. And of course, HH Angus is often also the prime consultant, so we need to coordinate effectively with all the project partners for their input. In addition to mechanical and electrical design, some of these would include civil, structural, environmental, geotechnical consultants, or controls contract that contribute a different role to the overall plan.
Kirsten:
Sabari, how far into the future should an energy master plan be looking? And typically, what drives the decision as to how long it should go on.
Sabari:
For smaller, quote unquote, smaller developments, we're looking at roughly a time of 5 to 20 years into the future; for larger developments that could extend up from 20 to 30 years. What typically drives this decision comes down to essentially our clients. We have to understand what their plan is for future growth. For manufacturing facilities, that could mean any additional production that they see in the future.
On the energy side of things, this may be additional customers that need heating or cooling. So that expansion is something that we need to relatively understand now. Overall, so we can't quite understand all aspects of it. But a few other factors may involve understanding the capital cost of these new installations or these new retrofits, and quantifying the risk in this from a financial point of view, that's quite important. Items such as equipment delivery time come into play here that may disrupt day-to-day services.
Another factor to consider is possibly a change in government means this may bring about a few new incentives. It may take away a few incentives. It may bring in a few bans on certain elements, certain materials, etc. And so that is a realm where, you know, one can do their best to predict it, but it's still quite unknown. So, I guess at the end, there has to be an understanding that this is in fact just a plan. It can't be rigid. And we work to make it flexible enough to adapt as the environment changes in the future.
Kirsten:
We can't really talk about energy master planning without also talking about feasibility studies and energy modeling and road mapping. Those are going to be the subject of a future podcast. But Justin, for our discussion today, can you just talk briefly about how an energy master plan is informed by those types of investigations and exercises?
Justin:
I think it's important to just go into briefly what those terms actually mean, feasibility study and energy modeling and sort of the typical context. It can be quite difficult to demonstrate a value of any plans or in other words, how much of an impact the change is going to have relative to how much it's going to cost without metrics and numbers and feasibility studies and energy modeling, essentially is what bridges this gap.
So, with some level of estimation and quantitative analysis before making a decision to fine-tune design details specifics, energy modeling can vary in the level of complexity. It could be on an hourly basis or some other time scale. But the overall goal is to estimate the heating and cooling load consumptions based on available information, whether data specific to the location, any energy metering, trending data that may be available, gas, hydro and water, utility bills, and even any anecdotal information that may be available from the operational staff that could help to form a more complete overall picture.
Once we have this energy profile, we now have some more insight into what's sort of the right approach with sizing of the plant. We evaluate the model against different options that the owner may want to explore and compare in order to understand the financial damage, so to speak, relative to what they get in the return, or also what we call the simple payback on the investment. One way to do this would be to calculate it based on the energy savings, versus the capital cost estimate of each of the options.
The specifics of the options would also depend on what level of planning is expected, and it can be about diversification of the asset technologies between electrification and perhaps some portion remaining on gas, depending on site utility limitations. It could be phasing in retrofit versus full replacement, or even looking at different manufacturers with varying levels of performance and maintenance needs, relative to the energy loads. Of course codes and standards are also a key aspect of the study. Some of these would include the Ontario Building Code, city bylaws, CSA standards and TSSA.
Sometimes the owner may also want to place some greater emphasis towards cost estimates, and we work with cost consultants to develop those areas. Or, if they wish to take on some of the additional financial analysis. In those cases, we may assist with the technical specifics to support their forecasting and modeling.
Kirsten:
Certainly, it takes a lot of expertise to put that kind of plan together. Okay, we've been talking about overview and generalities. Let's get down to some specifics here. Sabari, all across HH Angus, I'm hearing engineers talking about decarbonizing buildings, and reducing the carbon footprint of our clients’ assets. I'm also picking up a sense of excitement because these projects are not only interesting to work on, because they present some unique technical challenges, but they also provide important environmental benefits for the communities in which they're located. Tell us about some of the projects you're currently working on and what these involve.
Sabari:
For sure. Yeah, there's quite a bit of excitement. We get to possibly use newer technologies, etc., to help the environment. In terms of projects we're currently working on, there is a project, a steam plant that is being designed for the downtown Vancouver core, and this is a relatively large steam plant. There is basically introducing four 11 megawatt electric boilers to essentially reduce the demand of natural gas from the gas fired boiler side of the steam plant. Now, it must be understood that the electric boilers will be running most times satisfying the loads, while the gas boilers will be used in the cases where there's too much load for the electric boilers to handle. So, they'll be working with one another, but it'll mainly be the electric boilers taking up most of the loads for this project. In fact, early earlier in the project, there was a study conducted not by us, but we were looking at this study, where there was an argument for biomass, essentially wood pellets being used. In conclusion, we determined that introducing a biomass plant, the overall size just wouldn't work out. And electrification doesn't take too much space. Now it is a bit on the grid, but it's the best solution.
In addition, another project that I could speak of is one of the steam plants in downtown Toronto. We're going to be introducing heat pumps into this plant to once again reduce the load on the natural gas-fired steam plants, ergo reducing the carbon emissions there and I mean, of course, that comes with its challenges, but it's to benefit the environment by reducing our carbon footprint from these plants, which are so essential to us.
Kirsten:
Successful implementation of a master plan necessarily involves managing risks. Justin, what are some of the risk factors that you typically discuss with owners during energy master planning?
Justin:
Because of the long timeframes that these master plans often extend to, and with the involvement of so many stakeholders, it's a fairly complex landscape with, evolving technologies, regulatory requirements that are changing and, with respect to economic conditions, cost escalation is just one of the many risk factors. So, while feasibility studies may address some quantifiable cost benefits perspectives, there are some areas that are also not quantifiable; for example, the new dependency on utility grids or other types such as biomasses, as Sabari has mentioned, the emergence of competing technologies and in more detail assessment factors including governance and tax policies, inflation, and bank interest rate assumptions - these are all risk factors in a model which ultimately inform the master plan.
Other social and economic risk factors we look into from past experience, and we provide an opinion on, are the perceived level of risk, we look at the greenhouse gas emissions reduction potential in terms of production of C02; so, for example, comparing the level of electrification relative to other combustion fuel types, the impact to the public - for example, running a large industrial plant in an urban area can be quite disruptive to the public with emissions, noise and all of that - future-proofing, meaning understanding potential future expansion needs of the facility and the business, looking into planned space uses and relocations versus what actual spaces are available now for this anticipated expansion.
Another risk is also, with any change, what are the implications for additional training for the staff and additional service calls and maintenance requirements.
Kirsten:
Sabari, HH Angus is now a 100% BIM company. Why is it important to facility owners and how does being 100% BIM create value for our clients?
Sabari:
Being 100% BIM, what it does, at least from my perspective, is essentially it saves time on the design and as you know, time is money. So how it saves time is basically coordination between other teams within a project, whether it be consultant teams, contractors, etcetera - having that ability to proactively work on a singular model whilst taking into account other systems. I'm going to speak based on central plants, but within essential plants you'd have base building systems, there are structural components, other mechanical systems, heating systems, cooling systems, etcetera, and whether it be piping or ventilation, having that ability to deal with it in real time rather than asking for, let's say, a drawing set to be sent over and then coordinating, putting that on an AutoCAD background that we have and it just makes the entire process quicker. And that ability, I think, helps us save time in these projects, getting us to our end solution a lot quicker.
In addition to that, there are other capabilities of BIM and, from a design point of view, we have the capacity, once the piping or ventilation is completed, to understand flows within BIM, understand pressure losses. I do need to mention that at the end of the day, the designer, it would be best to review those numbers, etcetera. However, we do have that capacity to get those high-level numbers from BIM, which is great for us in terms of timing.
Kirsten:
What are the implications for project delivery compared to traditional design bid build that designers and engineers may be used to seeing in the past?
Sabari:
So, from a project delivery standpoint, as I guess I mentioned before, we do get to the end solution, in my opinion, a bit quicker, so that may reduce the schedule, etcetera. However, another aspect that I've noticed is when it's all either on the cloud or online, the computer always has a memory of what's being done, whether we need to document it or not.
There's always going to be documentation in the form of a timestamp. And BIM has the ability to spit out schedules, other important documents just from the model itself. And there's equipment lists or bill of materials that can be spit out from BIM, which saves us a lot of time, rather than going through each system and figuring that out. And yeah, overwhelmingly, I think that aspect of being able to document everything, understanding we don't need a separate record, although it's good to have, we don't need it on the side. And we can rest easy knowing that there's a timestamp on most of these documents being sent out, etcetera, and we can figure out how to trace certain documents back. I think it's really important, especially if you're trying to organize, managing a project and sending out deliverables, etcetera. It's a very useful tool in that manner.
Kirsten:
So, we're talking a little bit about ‘time is money’. Justin, I want to talk to you in a different aspect about cost. Energy consumption is a huge part of any facility's operating costs. What risks are owners running if they're not actively planning for their energy future?
Justin:
So, without proactive planning, I think that owners place a great risk in terms of extensive and sometimes unfeasible rework to correct these uncoordinated efforts and poor capital planning. These could result in delayed design and construction project timelines and, ultimately, incurred costs from poor phasing and execution of the work.
As noted earlier, construction design is fundamentally complex with many parties involved and, in particular, navigating the regulatory framework. Adhering to technical standards can place limitations against the overall objective to reduce project capital. So, one good example would be domestic water systems in healthcare facilities. We need to have them at elevated water temperatures at the right part of the system to prevent Legionella while avoiding scalding building occupants. And having the elevated temperature also fundamentally means that we're working against the competing objective of energy conservation.
Another example would be redundancy requirements from CSA codes. Essentially, depending on the code interpretation and how you interpret it, it could essentially put a multiplier on your capital if you don't consider it carefully ahead of time and plan accordingly. So overall, I think that owners can expect less resiliency against the risk factors that we've talked about today. All of this can amount to a significant loss of opportunity over time and through the operating life of the asset that often ran for decades. So, I think that retaining HH Angus as a trusted and experienced advisor early on in the planning stage from start to finish will help to mitigate and avoid these preventable pain points and pitfalls. There's less effort for the owner and better outcome overall to the end users and the public.
Kirsten:
So the takeaway advice is make sure you have an effective energy master plan. Thank you, gentlemen. Our guests today have been Justin Lau and Sabari Manoharan of the Energy division of HH Angus. If you'd like to learn more about our Energy Master planning services and low carbon solutions, you can drop a line to Justin and Sabari at lowcarbon@hhangus.com. Thank you for joining us for this episode of “Expanding the Possible!