Sector: Industrial
General Electric
Brilliant Factory
General Electric’s new state-of-the-art gas engine plant is one of the most advanced in GE’s global operations and the first of its kind in Canada. “It’s a plant that is reimagining how we manufacture. It incorporates all the concepts of lean: speed with excellent quality — coupled with everything that is now available and that is coming down the pipe in digital technology, with the latest in software developments.”*
— Elyse Allan, GE Canada CEO
HH Angus provided mechanical, electrical, plumbing, security, IT, lighting and vertical transportation consulting. The multi-modal plant, now owned by Advent International, manufactures gas engines that are coupled with either air or gas compressors, or with electric generators. The engines are distributed worldwide, primarily outside North America, in the oil and gas industry.
The plant runs three-dimensional machining simulations for CNC programs, gains real-time analytics to better understand the operating conditions of a machine or a test cell, operates lights-out machining, and combines all with advanced lean manufacturing practices.
Our IMIT scope included flexible structured cabling systems and supporting infrastructure, consisting of the latest shielded copper and fiber technologies, providing a transport platform for data, voice, video and other IP-based systems.
We also provided design for all low voltage technology systems. The factory uses equipment and machines embedded with sensors and connected to the high availability Industrial Internet Protocol-based network. Equipment data is streamed over secure links to the cloud for analysis.
Extensive design and installation of multiple audiovisual systems facilitate collaboration between global sites. Plant cabling design was provided per the most recent Industrial Premises standard. Working closely with the client’s IT, Security and AV groups, network-based systems were designed to the latest technology.
Our Angus Connect team was also involved in determining the performance requirements of client systems, product selection, preparation of working drawings and specifications, tender preparation and response evaluation.
SERVICES
Mechanical Engineering | Electrical Engineering | Security and IMIT Design | Vertical Transportation Consulting | Lighting Design
PROJECT FEATURES
Size: 450,000 ft2 | Status: Completed 2018
LOCATION
Welland, Ontario
KEY SCOPE ELEMENTS
Multi-model plant | Plant is fully air-conditioned to prevent "flash rust" | real-time analytics | Transport platform for data, voice, video and other IP-based systems | AV systems enable collaboration between global sites | Test cell scope added later | Met aggressive schedule for working drawings | LEED Silver Certified
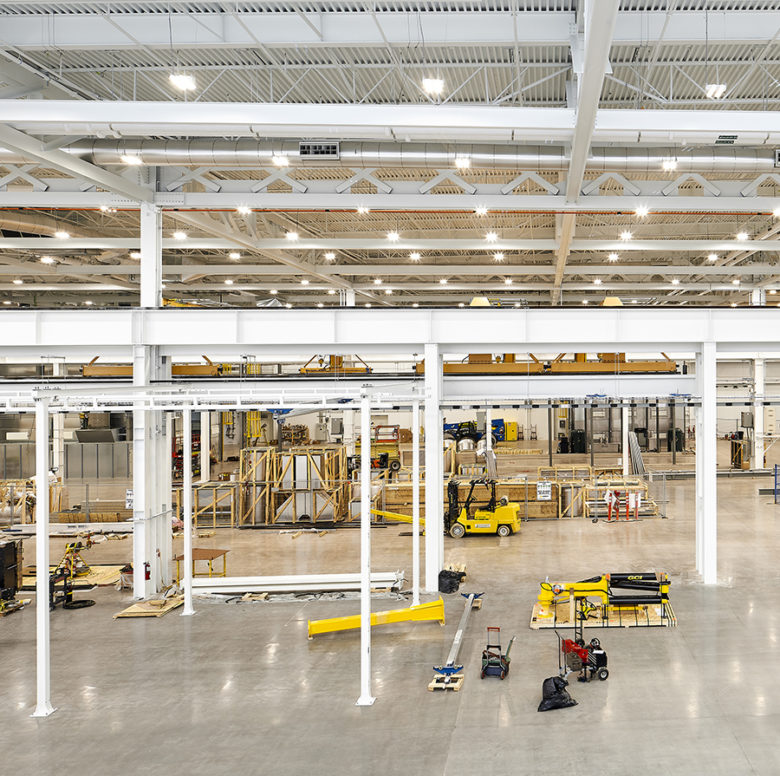
Custom HVAC control
The plant is fully air-conditioned to prevent ‘flash rust’, which can occur during machining of items such as crankshafts and connecting rods if humidity levels are not carefully controlled.
Industrial and support spaces
In addition to the main assembly and machine areas, three test cells, warehouse space, and paint areas, the plant also features front of house spaces such as offices, staff support, fitness centre, customer areas, hoteling for visiting customers and GE staff, conference rooms, etc.
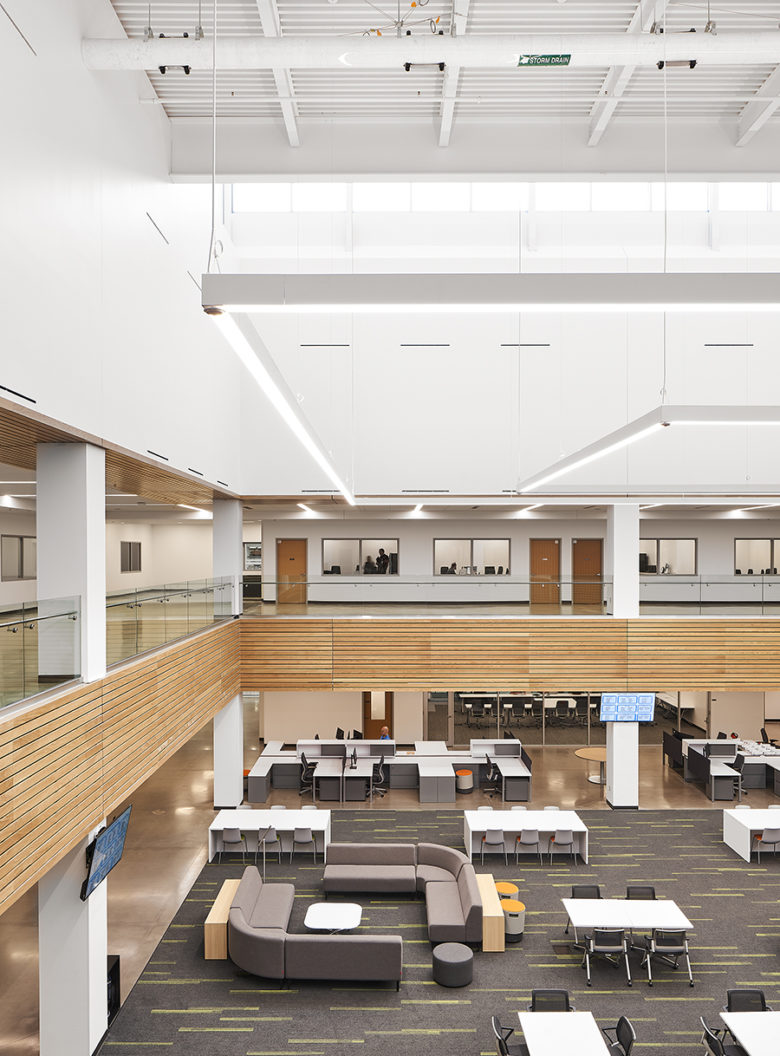
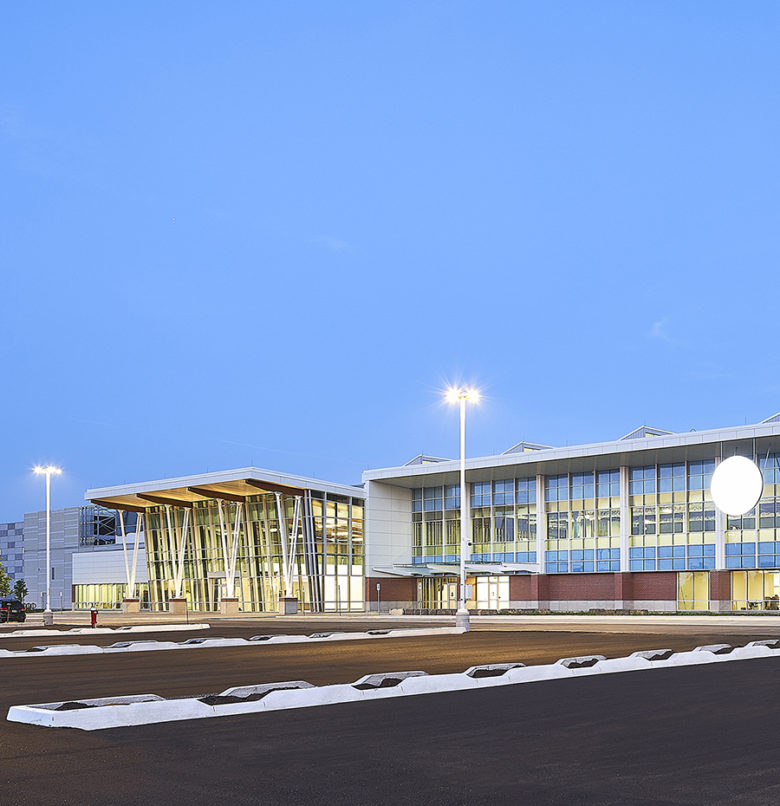
Expanding our scope
HH Angus’ project scope was increased to include the physical design of a significant new Test Cell addition to the plant, and to ensure Canadian compliance. The three test cells are connected to the main plant for testing engines prior to delivery. We met an aggressive schedule to produce working drawings for tender.
Siemens Canada
Algonquin College Trigeneration Plant
HH Angus was retained to design a trigeneration plant for Ottawa’s Algonquin College. Our scope included review of Siemens’ PSUI application to IESO, and assisting with their application. Because the existing central utility plant (CUP) was not large enough to accommodate new plant systems, our team developed a pre-engineered building to be built adjacent to the existing CUP.
As Prime Consultant, HH Angus retained Milman and Associates to undertake the required structural engineering, including a roof design to accommodate the cooling towers, rad cooler and transformer. An additional mezzanine was added to house auxiliary equipment.
In order to maximize the usable heat during summer months, a 350 ton absorption chiller, using double effect flue gas and hot water, was detailed. The 2 MW reciprocating trigeneration plant features selective catalytic reduction units and a heat recovery boiler.
Some project challenges included:
- Integrating and commissioning a trigeneration system into an operating facility
- Noise constraints due to proximity of CUP to College operations
- Space constraints due to pre-engineered building
- Footprint was maxed out based on site restrictions; HH Angus had to take into account future co-gen, chiller and ancillaries
- Ongoing upgrades in CUP heating and cooling, which HH Angus coordinated with another consultant
- Operating flexibility required for both parallel and island operation
- Solutions included: designed mezzanines in the existing CUP to house equipment and accommodate new, pre-engineered building for the second cogen and chiller; and rigorous scheduling coordination with Utility and College operations staff
SERVICES
Prime Consultant | Mechanical Engineering | Electrical Engineering
PROJECT FEATURES
Status: Completed 2017
LOCATION
Ottawa, Ontario
KEY SCOPE ELEMENTS
Review of PSUI application to IESO | 350-ton absorption chiller | 2 MW reciprocating trigen plant with selective catalytic reduction units & heat recovery boiler
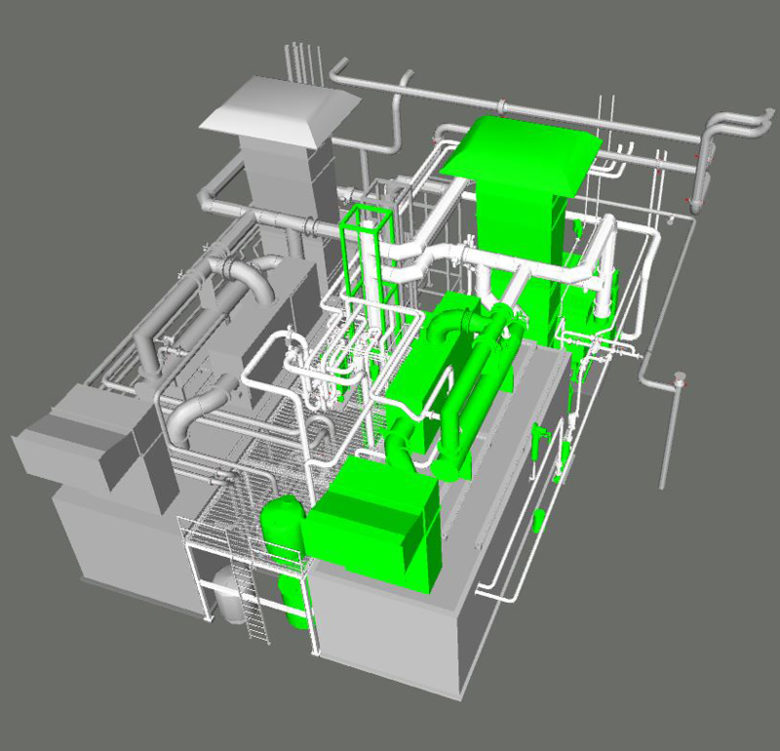
Minimizing Disruption
All new equipment was connected to existing systems, with electrical connections restricted to well-planned shutdowns, resulting in minimal disruption to the ongoing operations of the campus.
Confidential Client
Manufacturing Relocation
HH Angus’ Energy Division completed a very fast track refurbishment project to an existing building in order to accommodate the relocation of this manufacturing facility to Newmarket, Ontario from their existing facility in Toronto.
The client is an original equipment manufacturer of innovative and high quality electronic products serving a variety of technology markets. The Newmarket location produces aerospace components. HH Angus acted as the Prime Consultant, responsible for managing and providing the mechanical, electrical, architectural and structural design to suit the required production spaces. New HVAC, plumbing, fire protection and electrical infrastructure was added, as well as production services including process chilled water, compressed air and nitrogen systems.
SERVICES
Prime Consultant | Electrical Engineering | Mechanical Engineering
PROJECT FEATURES
Status: Completed 2018
LOCATION
Newmarket, Ontario
KEY SCOPE ELEMENTS
Provided innovative design for various components to suit the production space | New HVAC, plumbing, fire protection and electrical infrastructure
Public Works & Government Services Canada
Tunney’s Pasture
HH Angus was engaged as Prime Consultant on a chiller plant installation for this public building in Ottawa. The project installation serviced nineteen buildings with a total floor space of ~3,170,000 ft2 and was comprised of two chillers @3500 tons.
Tunney’s Pasture is a 49-hectare (121 acre) mixed-use campus in Ottawa, including government services, commercial offices and residential buildings. Its existing steam-driven chillers were at end of life and operating with R22 refrigerant, the import and production of which is banned as of January 2020. Also, the use of river water for free cooling needed improvement and the river water pumping system was not operating efficiently.
HH Angus, in joint venture with Goodkey Weedmark, was retained to undertake conceptual studies to evaluate changing the chillers from steam power to electrical power. We also made recommendations for improving the free cooling aspects of river water and making more effective use of the river water pumping system.
HH Angus provided conceptual evaluation of replacing the chillers, in terms of efficiency, physical location and necessary steps required to change from steam to electrical power. Once the chiller concept was resolved, we evaluated optimization of the river water pumps to undertake the condenser water cooling and considered how to efficiently use the free cooling available from the river in low load conditions.
Optimizing free cooling and condenser water, using river water instead of cooling towers, resulted in energy efficiency and reduced carbon footprint for this installation. We also identified benefits to the client through improvement in chiller efficiency using the latest technology, and the elimination of boiler operation during the summer months.
SERVICES
Prime Consultant | Mechanical Engineering | Electrical Engineering
PROJECT FEATURES
Status: Completed: 2017
LOCATION
Ottawa, Ontario
KEY SCOPE ELEMENTS
Evaluation to optimize river water pumps to undertake condenser water cooling & efficient use of free cooling from the river in low load conditions | Consulted on technology that would eliminate boiler operations during summer months
Confidential Client
Deodorizer Installation
HH Angus served as prime consultant for this new deodorizer processing plant. The new installation more than doubled the oil refining facility’s existing capacity.
Palm oil is the most widely-used edible oil in the world. Deodorizing is the final stage in refining the oil, and is required to remove odoriferous material, free fatty acids and other undesirable minor components, in order to produce a bland oil with a good shelf life.
The deodorizer tower is 30m high and 2m in diameter, with connected boilers, pumps, etc., that required connection to the existing production plant located adjacent to the expansion area. Due to the height and sectioning of the deodorizer, it had to be built in two stages.
One of the key challenges of the project was the site constraints. Two feasibility studies were produced as part of the investigation. It was determined that a new building was needed, rather than trying to install the deodorizer in the existing building.
In order to accommodate the electrical needs of the deodorizer process, a system upgrade was required to the switchgear. The upgrade allows the client the flexibility to install other major equipment in future.
Enabling projects for the deodorizer installation included a nitrogen tank installation, cooling water system, a new natural gas let down station, and new gas feed to the site.
SERVICES
Prime Consultant | Mechanical Engineering | Electrical Engineering
PROJECT FEATURES
Status: Completed 2017
KEY SCOPE ELEMENTS
Detailed Engineering Study | 3D modeling | 30m high deodorizer tower connected to existing plant within site constraints | Nitrogen tank installed | System upgrade to switchgear provided flexibility to install other major equipment in future
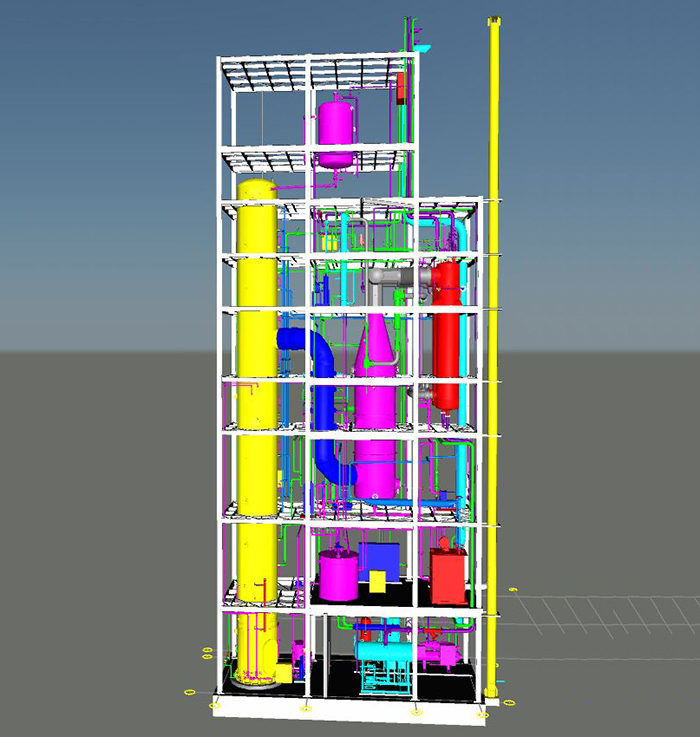
Modeling in 3D
As a special feature of the project, HH Angus modeled the installation using Plant 3D software. The installation was quite complex, and creating the model reduced both design time and the construction schedule. The contractor was able to see a comprehensive view of the design, confirming locations of pipes, etc.