Sector: Industrial
General Motors of Canada
Welder Water System, Car Assembly & Truck Plants
HH Angus designed the Welder Water System for the car assembly and GMT 800 C/K Truck plants in Oshawa. These systems provide cooling water for all the robot welders, circulating cooling water to the tips of the welders to prevent overheating.
C/K Truck Plant
This plant’s welder water system consisted of a cooling tower system and cooling distribution system. The pumps re-circulate tower water from the indoor sump through heat exchangers and up to the cooling towers. The cooling tower system featured five main components: Cooling towers, indoor sump, recirculation pumps, plate heat exchangers and centrifugal filter units.
The two vital conditions that had to be maintained were temperature and differential pressure. A temperature sensor on the hot side of the heat exchanger (closed loop side) controlled the staging of the cooling towers and the speed of the variable speed drive cooling tower fans. Pressure differential transducers located at the index runs staged the cooling water pumps to maintain differential pressure. The welder tips are extremely sensitive to differential pressure, so very tight pressure tolerances have to be maintained at all times.
Car Assembly Plant
In the Car Plant, renovations required the relocation of the welder water system, together with the supply and installation of three new cooling tower pumps and three new circulation pumps.
The three cooling tower pumps were each 100 horsepower, electrically driven, and with a flow rate of 2670 US gallons per minute. The three circulating pumps were each 150 horsepower.
The distribution piping system extended over 3,000 feet, serving welding robots throughout the car assembly plant. The heat transfer, between the circulating (robot cooling) water and the tower cooling water, takes place in four plate-type heat exchangers.
SERVICES
Mechanical Engineering
PROJECT FEATURES
Status: Completed 2008
LOCATION
Oshawa, Ontario
KEY SCOPE ELEMENTS
Cooling tower system | Sensor-controlled temperature and differential pressure | Three cooling tower pumps @ 100hp with a flow rate of 2670 USGPM | Over 3000 feet of distribution piping serving robots throughout the car assembly plant
— Photos courtesy of General Motors of Canada
Ford Motor Company of Canada
Fuel Cell Building
This building was designed to house Ford’s ‘Fumes-to-Fuel’ technology, which converts toxic volatile organic compounds (VOCs), generated during the painting process, into electricity that powers the plant’s operations.
The Oakville system began with a 120KW internal combustion engine that was installed as part of this project. Ford had plans to add additional power generating equipment.
HH Angus served as Prime Consultant for a new, state-of-the-art, 10,000 ft2 building to house a patented process for the capture of VOCs from spray booths.
This engineered industrial building, with a height of 35.5 feet, was constructed adjacent to the existing Ford plant, but is not linked to the plant. The building contains a public viewing area for Ford’s green energy system, a training room, offices, warehouse and washrooms. All public spaces were air-conditioned. A steam boiler provides heating for both the fuel cell process and the building. The electrical feed to the building supports both the process and building. It was connected to an existing electrical substation located inside the existing plant.
As Prime Consultant, we were responsible for all architectural, engineering and structural disciplines for the building, as well as site services and associated utilities for the fuel cell process to function properly.
SERVICES
Prime Consultant | Mechanical Engineering | Electrical Engineering
PROJECT FEATURES
Size: 10,000 ft2 | Status: Completed 2008
LOCATION
Oakville, Ontario
KEY SCOPE ELEMENTS
Engineered industrial building - with a height of 35.5 feet | Prime Consultant for all disciplines (architectural, structural, mechanical & electrical) as well as site services and associated utilities for the fuel cell process to function properly
General Motors of Canada
Truck Plant Fluids Tank Farm
HH Angus redesigned the pump house and storage tank farm providing automotive fluids to the vehicles in the truck assembly plant.
Our project scope covered replacing ten 50,000 litre and three 25,000 litre storage tanks. The system also required seven new truck offload pumps and twelve new plant delivery pumps. Because it was not an option to shut down the plant to facilitate the work, co-ordination and timing between the construction activities and plant operations was critical to the success of the project.
A steam-heated glycol loop heating system was provided for the storage tanks containing high viscosity fluids. Glycol was pumped through a closed loop system and controlled via temperature control valves in each tank.
Due to the flammable and combustible fluids stored at this facility, a four zone Aqueous Film Forming Foam (AFFF) fire protection system was used. The total calculated flow was greater than 3,000 USGPM. The fire protection system was interlocked electrically to the process function, and connected directly to both the in-house and municipal fire brigade to assure maximum protection and safety.
SERVICES
Mechanical Engineering | Electrical Engineering
PROJECT FEATURES
Status: Completed 2005
LOCATION
Oshawa, Ontario
KEY SCOPE ELEMENTS
Replacement of ten 50,000 litre and three 25,000 litre storage tanks | Continuous plant operation required, necessitating high degree of coordination and precise timing | Tanks for high viscosity fluids required steam heated glycol loop | AFFF fire protection system
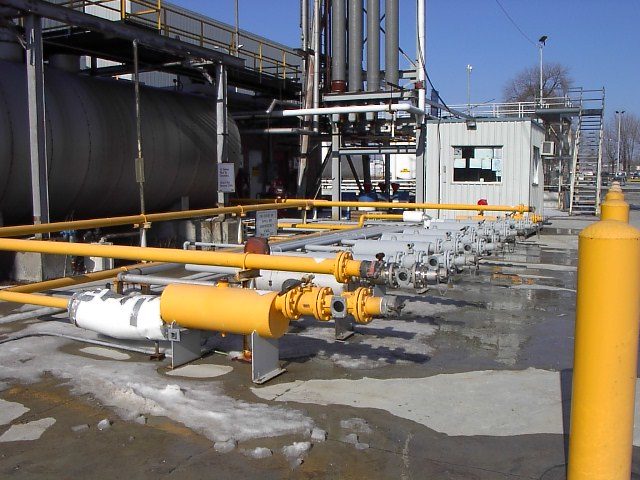
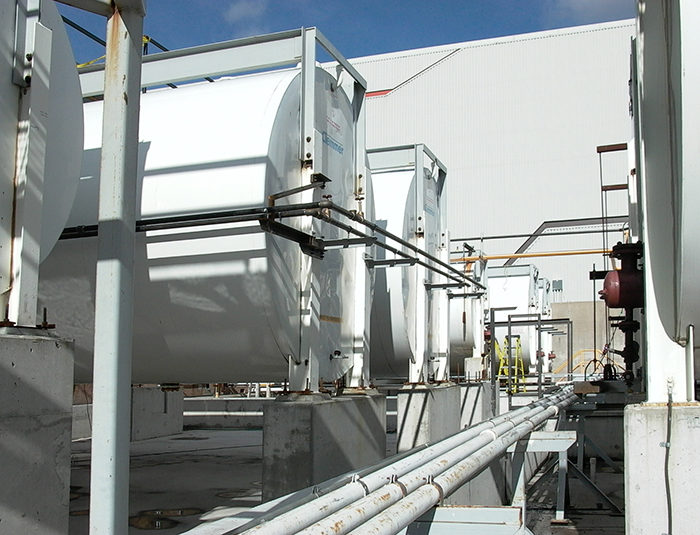
General Motors Canada
Paint Shop Process Waste
This automotive plant project involved combining the process waste flow from two paint shops into a common process gravity sewer system leading to the onsite waste treatment plant.
The calculated maximum combined flow was, in fact, greater than the 1900 USGPM capacity of the existing gravity sewer, which necessitated flow control measures to meter the flows. Since flows from both plants fluctuated with shift loads, storage head tanks were installed to allow the metered flow to function effectively.
Another challenge was the difference in flow velocity. The new paint shop process water was being pumped, while the process waste from the existing paint shop flowed by gravity. In order to discharge the pressure and velocity energy from the pumped process waste, a two-compartment underground concrete quiescent chamber was designed and installed between the pumped and gravity sewers. This allowed the two waste streams to mix and flow to the waste treatment plant much more effectively.
SERVICES
Mechanical Engineering
PROJECT FEATURES
Status: Completed 2003
LOCATION
Oshawa, Ontario
KEY SCOPE ELEMENTS
Waste flow from two paint shops combined into common process gravity sewer system | Two compartment underground quiescent chamber designed to allow two different waste stream technologies to mix and flow
— Image courtesy of General Motors Canada
General Motors of Canada
Plant Additions
HH Angus has served as the Prime Consultant for a variety of automotive plant additions and renovations for General Motors. These are three of many projects for this valued client.
C/K* Truck Plant
HH Angus coordinated the 1,800,000 ft2 addition to both the building and building services for the new modular paint shop, body shop, paint oven enclosure and elpo phosphate process.
This project included the installation of three 633-ton chillers and one 250-ton chiller for building and process chilled water loads.
* C/K: C indicates 2-wheel drive trucks and K refers to 4-wheel drive.
GMT 800 Oshawa Truck Plant
This was a 300,000 ft2 addition to the existing C/K Truck Plant in Oshawa. Our project scope included coordinating architectural and structural design, mechanical/electrical design, and contract administration. The building is a 35 foot high, single-storey structure with insulated metal siding and 42,000 ft2 mezzanines with washrooms and one mezzanine for the welder water system. The project included a new 8,000 ft2 room and a quality measurement laboratory. The project included electrical bus duct distribution to process loads, as well as a quadruple-ended paralleled welding distribution system for welding robots.
Renovations to C/K Truck Plant
This project consisted of a four-bay addition with four levels to the existing paint shop facility at the Oshawa Truck Plant to house a new primer surfacer spray booth, accumulator conveyor, prep booth, freight elevator, storage, clean room and all associated building services.
SERVICES
Prime Consultant | Mechanical Engineering | Electrical Engineering
PROJECT FEATURES
Size: 1,800,000 ft2 | Status: Completed 1999
LOCATION
Oshawa, Ontario
KEY SCOPE ELEMENTS
1,800,000 ft2 addition | Installation of three 633-ton chillers and one 250-ton chiller | Prime Consultant for 300,000 ft2 plant addition
— Image courtesy of General Motors of Canada