Service: Information and Communications Technology
Porter Aviation Holdings
Ottawa Airport Hangars
Porter Aviation Holdings Inc. has built two massive aircraft hangars at the Ottawa International Airport. At 150,000+ square feet and $65 million, the project was designed by Scott Associates Architects. PCL served as construction manager together with Span Construction & Engineering. HH Angus provided mechanical and electrical engineering to the project, as well as ICAT and security design.
The Porter hangars were constructed in two phases - the first was completed in late 2023, and the second in 2024 Q1. The complex is part of a series of projects to revitalize the Ottawa Airport to accommodate increased air travel demand in the National Capital Region, and will serve as a primary maintenance base, with 200 local hires, including 160 aircraft maintenance engineers, shop technicians and administrative support staff.
The hangars span approximately 86 metres, and house up to eight aircraft, along with various repair and parts modification shops.
One of the project’s key design criteria was to exceed current energy efficiency standards, in line with the airport’s commitment to net-zero operations by 2040 or sooner. The hangars were designed with sustainability in mind; for example, some of the important features include:
- A predominantly electric fleet of vehicles for towing and servicing aircraft, as well as ground support
- Design criteria exceeding current energy efficiency standards
- Constructed with approximately 35% recycled steel that can be recycled at the facility’s end of life
- Constructed from materials with 28% lower embodied carbon than conventional tilt-up assemblies
- City fire hydrant system is fully supplemented by an onsite underground water storage tank capturing approximately 1.2 million litres of excess rain/stormwater to avoid overstressing existing city mains.
HH Angus is also working with Scott Associates Architects on Porter Aviation's Saint-Hubert Airport Terminal project, a new zero-carbon terminal that will serve an estimated four million passengers annually. We were also involved with the original revitalization of the Billy Bishop Toronto City Airport that was completed in 2011, as well as its further expansion in 2014, and have been working with Porter Aviation since its inception.
Click here for a one-minute video of the hangar topping off.
SERVICES
Mechanical Engineering | Electrical Engineering | ICAT Design | Security Design
PROJECT FEATURES
Status: Completed 2024
LOCATION
Ottawa, Ontario
KEY SCOPE ELEMENTS
150,000+ square feet | Energy efficient design | Rain water capture system supplements city onsite fire hydrants
Image and video courtesy of Porter Airlines.
Mount Sinai Hospital
Phase 3A Redevelopment
Phase 3A represented the largest redevelopment in Mount Sinai's history. HH Angus was engaged to provide mechanical and electrical engineering for the Renew Sinai redevelopment.
HH Angus worked with the Hospital, Stantec Architecture and other consultants to develop the Functional Program and Blocks Schematics for Ministry of Health and Long-term Care [MOHLTC) stages 2 and 3.1 submissions.
As part of our scope, we were involved in the investigation of existing infrastructure and systems. The age of the existing facility, together with previous renovations and multiple facility architects and consultants provided a challenge in obtaining a complete set of existing design conditions. We were provided with drawings in various forms (eg: PDFs. scanned hand-drawn images, AutoCAD and part plans), ranging from the original build to the most current renovation projects. We translated the relevant information into AutoCAD and, in with numerous site investigations, assembled a comprehensive set of record drawings detailing the existing systems and functions.
The scope of the project included a new Surgery Department, renovated and expanded Emergency Department, Critical Care, Medical Device Reprocessing Department, Integrated Practice Unit, Ambulatory, and labs, as well as miscellaneous relocates and decants.
Some of the key challenges of this project included reworking the major mechanical and electrical infrastructure to upgrade systems to current standards, and the integration of disparate systems with existing facilities.
Extensive renovations were implemented. To address the challenges of implementing new infrastructure, HH Angus provided extensive background information and on-site investigation to mitigate risks to the Hospital.
Minimizing disruption to hospital services was of paramount concern in scheduling the renovations. To ensure continued hospital operations, our design solution included planned sequential shutdowns minimized inconvenience to staff, patients and visitors.
Under a standing offer with Mount Sinai, we served as Mechanical and Electrical Engineers of Record and were involved in a variety of projects for Phase 3, including: peer review, fluoroscopy unit. Maternity Clinic renovation, Mouse MRI Lab, Biorepository Lab, Roth Lab, Bremner Lab, Distributed Antenna Systems, lobby upgrade, art gallery/ security/office renovations, and IMIT Planning for Phase 3 Redevelopment and renovations to multiple departments.
SERVICES
Mechanical Engineering | Electrical Engineering
PROJECT FEATURES
New Surgery Department, renovated and expanded Emergency Department, Critical Care, ORs, MDRD, IPU, Ambulatory, Labs, as well as miscellaneous relocates and decants | Status: Completed 2024
LOCATION
Toronto, Ontario
KEY SCOPE ELEMENTS
Major redevelopment of hospital's main site | Integration of new and existing systems | Renovations to main lobby, art gallery and security IMIT
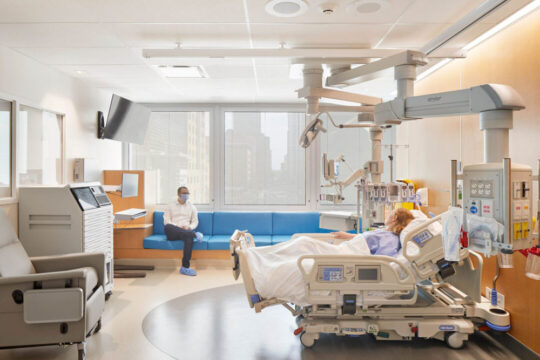
Mount Sinai Endoscopy and ICU
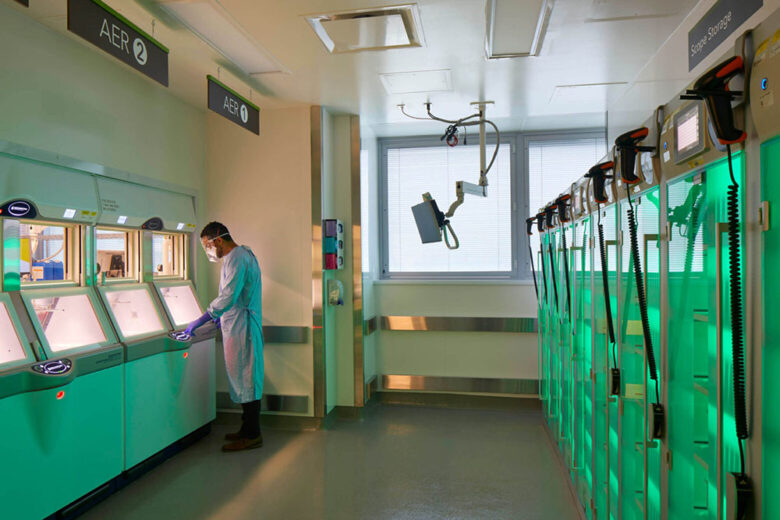
The Co-operators
National Headquarters
The Co-operators’ Headquarters in Guelph, Ontario has been certified a 'Zero Carbon Building' by the Canada Green Building Council. The project is also pursuing LEED Gold, WELL Platinum and BOMA Best certifications.
The project covers three floors totaling 226,000 ft2, and includes a data centre, cafeteria, fitness centre, conference rooms, and three-storey open atrium. HH Angus provided mechanical and electrical consulting engineering, as well as IMIT and lighting design.
The building features an all-electric design to eliminate direct carbon emissions from any on-site source. This means that the company did not need to undertake any retrofits or decarbonization plans to achieve net zero targets. The building has been designed to be highly energy-efficient and to minimize indirect annual carbon emissions from electricity.
Any remaining emissions will be offset through high-quality carbon offsets or carbon-free renewable energy sources. The construction process was also meaningfully reduced, offsetting “embodied carbon” emissions resulting from the manufacture, transportation, and disposal of all building materials.
The Canada Green Building Council has identified the building sector as Canada’s third-largest emitter of greenhouse gases (GHG). Presently, residential, commercial, and institutional buildings are responsible for 17% of Canada’s GHG emissions, and this figure approaches 30% when building materials and construction processes are taken into account.
Despite an aggressive construction schedule, the project overcame the challenges of integrating an all-electric design and achieving Zero Carbon Building certification. It also intended to surpass goals for energy and GHG savings beyond the Ontario Building Code’s all-electric baseline and heating load reduction minimum for new builds. The building features a rooftop solar array and a high-efficiency water source, showcasing innovative approaches to sustainable design.
The building’s low-impact features include:
- Energy and GHG savings 40% greater than the Ontario Building Code’s all-electric baseline
- 60% reduced heating load, surpassing the minimum code requirement for new office builds requirement for new office builds
- A 282 kW rooftop solar array that is expected to produce ~9% of the building’s annual total energy
- Automatic window tinting to reduce glare and save energy
- A highly-insulated and airtight envelope to conserve energy
- High-efficiency water source technology to recover and redistribute heat throughout the building
- Award-winning lighting design, including LED lighting equipped with occupancy and daylight harvesting sensors that turn on only when needed
Read CaGBC's feature article about The Co-operators Guelph Headquarters.
See Interior Design Magazine's feature on The Co-operators HQ,
The Co-operators Guelph Head Office project awards:
Illumination Engineering Society 'Award of Merit' 2025
Honourable Mention in the “Best New Build Project” category of the 2024 EM Honours Awards Program, which celebrates excellence in energy efficiency, proactive energy management and decarbonization
2025 Grand Valley Construction Association's 'Building Excellence' award, 'Specialty Award' for Innovation and Sustainability
SERVICES
Mechanical Engineering | Electrical Engineering | IMIT Consulting | Lighting Design
PROJECT FEATURES
226,000 ft2 | Status: Completion 2024 | Certified ‘Zero Carbon Building by CaGBC | Targeting LEED Gold and WELL Platinum certifications | LED lighting | Daylight harvesting
LOCATION
Guelph, Ontario
KEY SCOPE ELEMENTS
Energy and GHG savings 40% greater than all-electric OBC standard | Building designed to achieve net-zero through all-electric design, without retrofits or decarbonization | Targeting reduced embodied carbon emissions during construction, minimizing carbon footprint
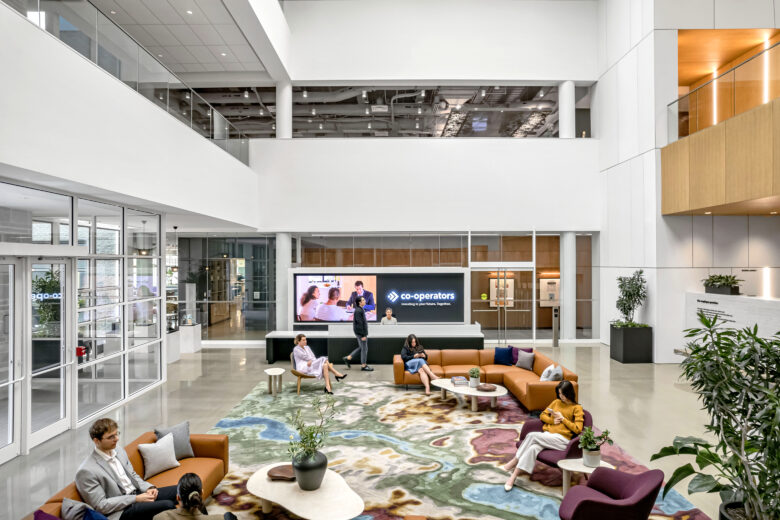
Zero carbon building
The building has attained the ‘zero carbon building design standard’ certification and is pursuing LEED Gold and WELL Platinum certifications.
Carbon offsets
The company will be offsetting embodied carbon emissions resulting from construction, manufacturing, transportation and disposal of all building materials.
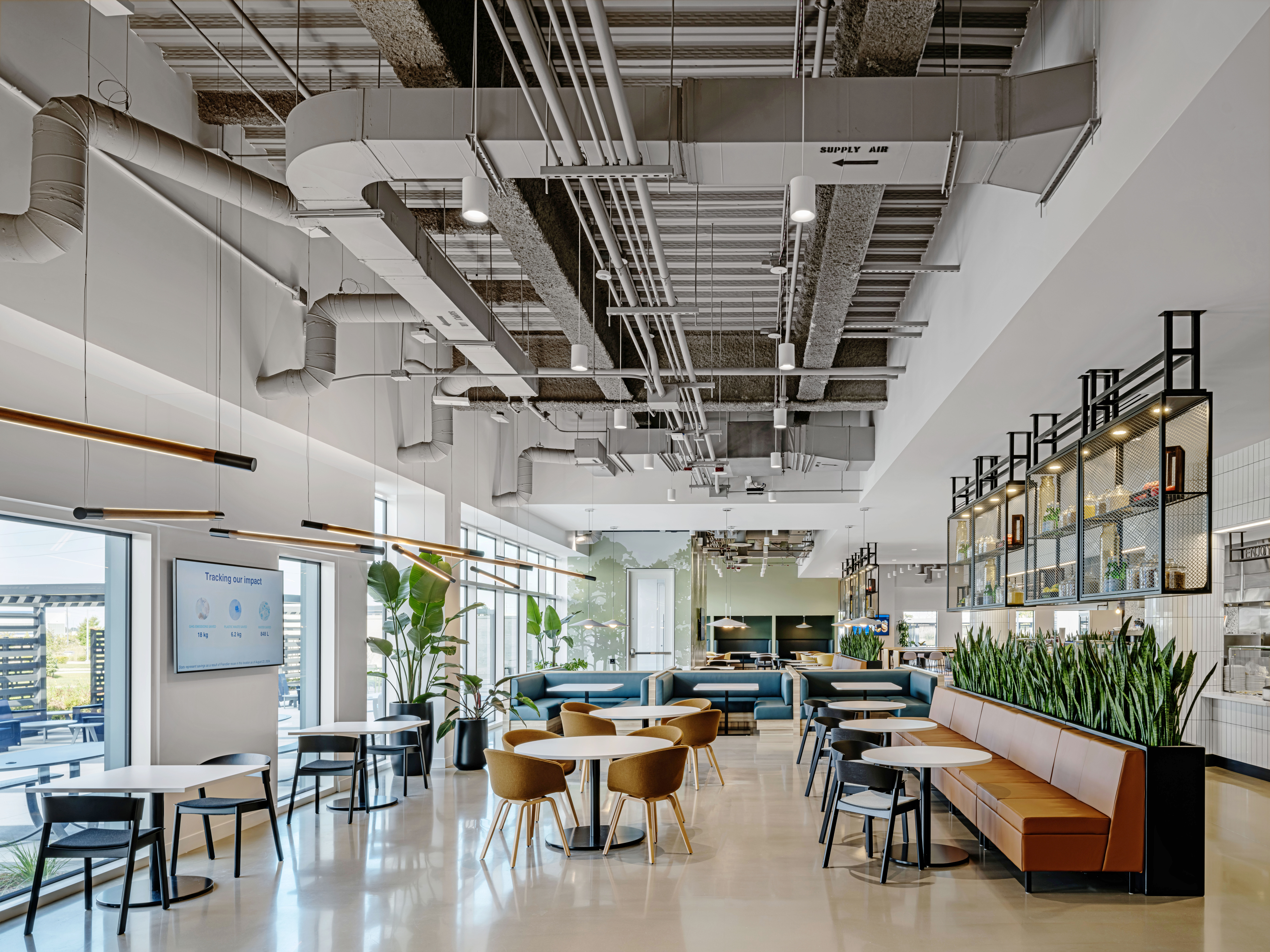
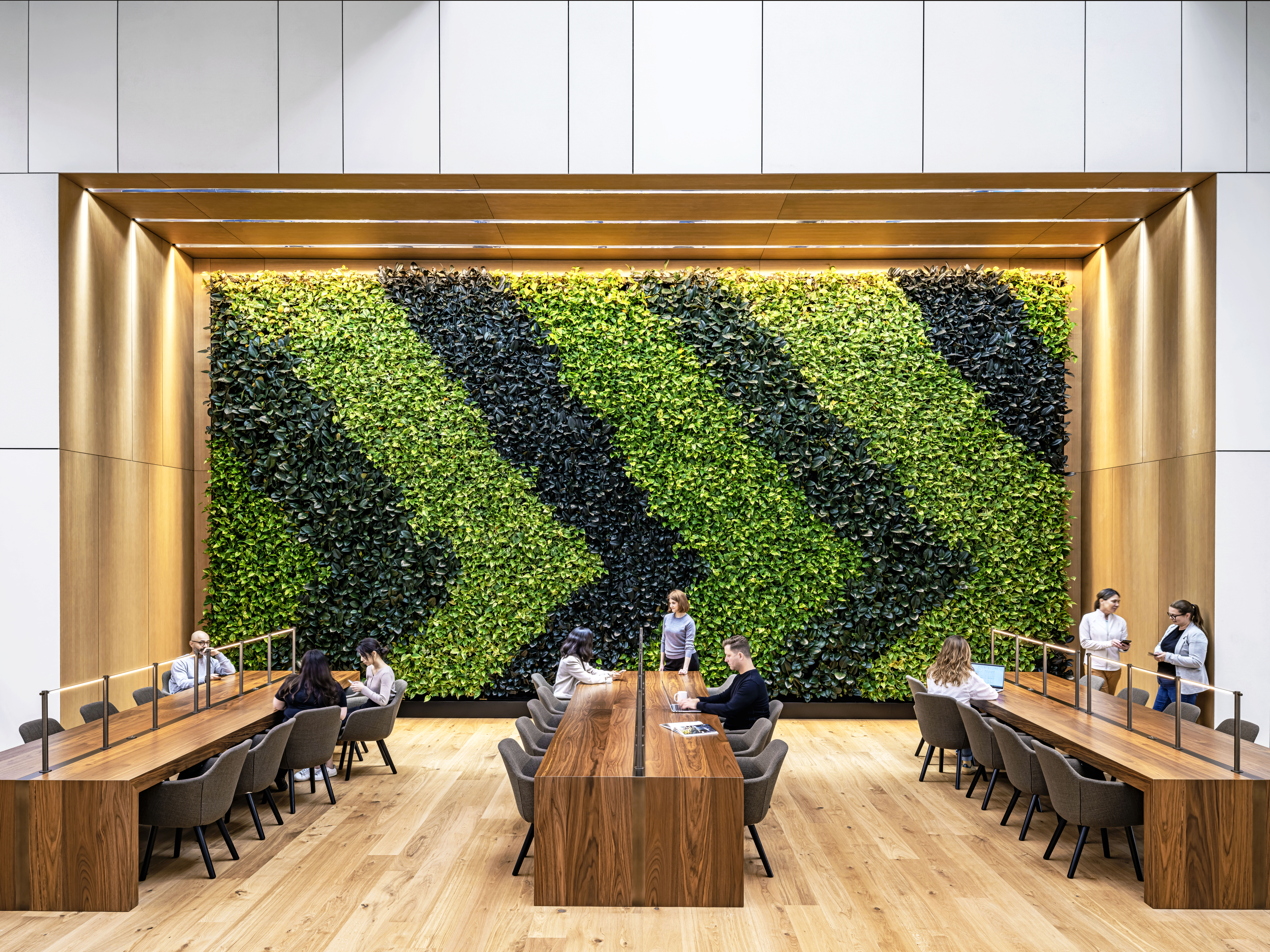
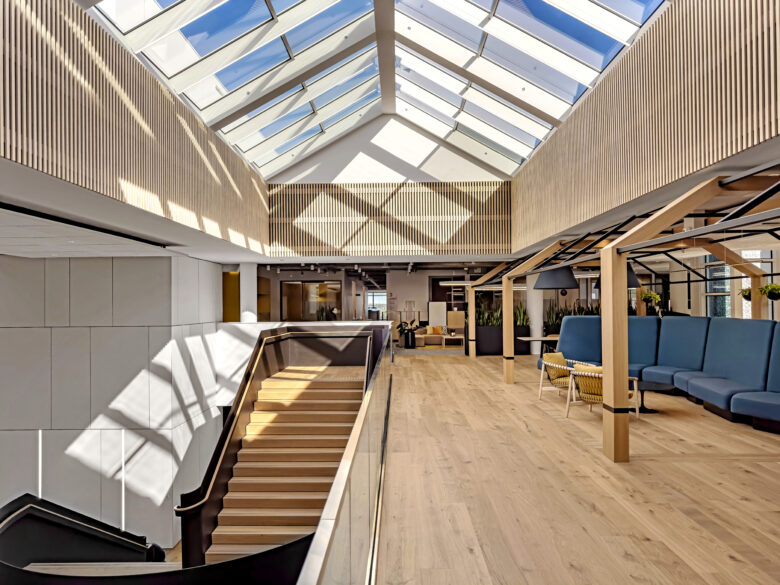
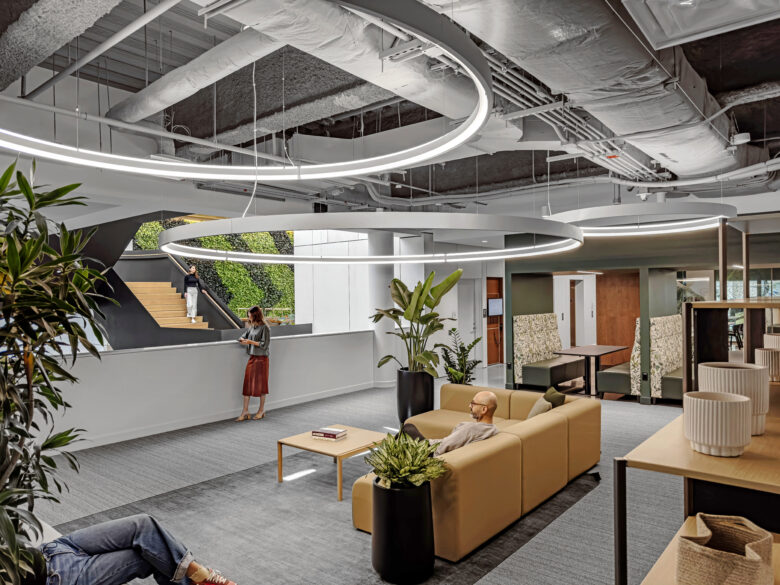
*Source: HOK Canada
Hudson Pacific Properties
Burrard Exchange
Burrard Exchange adds to HH Angus’ growing portfolio of commercial, healthcare and mission critical work in Vancouver and the broader BC region.
In September 2021, Hudson Pacific Properties, in partnership with Blackstone Real Estate, unveiled plans for the addition of a hybrid mass timber 16-storey office and retail development to downtown Vancouver’s Bentall Centre, adding 450,000 ft2 of office and retail space within the complex.
Once approved, the new building, called Burrard Exchange, will be one of North America’s tallest exposed mass timber office buildings. The mass timber construction technique will support the project’s sustainability goals and reduce embodied carbon.
HH Angus is providing mechanical and electrical engineering, IT/communications, and energy modeling consulting services for this exciting new commercial project. Kohn Pedersen Fox Associates is the design architect and Adamson Associates Architects is the architect of record.
"Our team is excited to be part of this project for a number of reasons." said Kevin O’Neill, Commercial Division Director at HH Angus: "That the project will set a new benchmark for green construction in Vancouver and the innovative use of mass timber are key highlights for us. We’re thrilled to be working with Hudson Pacific Properties, KPF and Adamson Associates on this development."
To read Hudson Pacific Properties’ full press release, click here.
HH Angus provided consulting engineering services to another timber project completed in 2020 – Oakville Fire Station 8 – which used cross-laminated timber in its construction. One of the special considerations of using timber is that it requires both expertise and unusually close coordination between the M&E designers and the structural designers since, unlike drywall, wood openings cannot be adjusted once cut.
SERVICES
Mechanical Engineering | Electrical Engineering | IT/Communications Design | Energy Modeling
PROJECT FEATURES
Size: 450,000 ft2 | Office/Retail Development | Reduced embodied carbon when operational | Status: Completion TBA
LOCATION
Vancouver, British Columbia
KEY SCOPE ELEMENTS
Hybrid mass timber |16 storeys
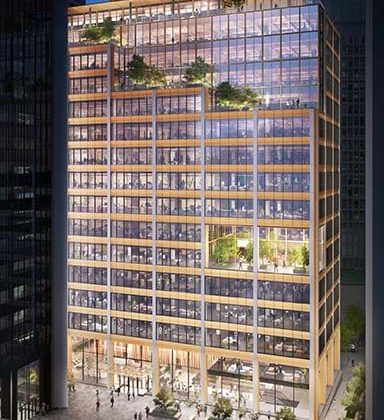
Mass Timber Construction
Burrard Exchange will be Hudson Pacific Properties’ first mass timber development and builds on the momentum of other mass timber projects in British Columbia.
Renderings courtesy of Hudson Pacific Properties
AstraZeneca
Tenant Fitout
“The goal of AstraZeneca’s iWORK workplace strategy is to create facilities that meet expectations of how a great place to work should look and feel.”
AZ Workplace Strategy Guidelines
A further goal of the fitout was to use available space more efficiently to create more collaborative, vibrant working environments to achieve a science-driven, patient-focused culture and mindset.
HH Angus provided M&E consulting engineering and IMIT communications design to the project, which presented a number of interesting challenges requiring thoughtful solutions. Among the challenges was an aggressive schedule. The team worked efficiently and collaboratively to meet the project deadlines.
The project did not allow for core drilling to feed workstations or standalone furniture. To address this, the design team and engineers had to be strategic in using perimeter and under-carpet raceways to conceal wiring. A new lighting design was implemented throughout the 5th floor, and provided a sophisticated wireless lighting control system, complete with daylight harvesting and an occupancy setting, independent of the base building control system.
During the schematic design phase, our team noted several deficiencies within the existing base building system affecting the project’s location. We requested the team have a complete site audit done by a local air balancing contractor, which identified several issues with duct connections, system operation and controls. Through this process, we were able to rectify many issues prior to the close-out phase of our project. This resulted in an efficient transition for the client, saving them both time and money.
SERVICES
Mechanical Engineering | Electrical Engineering | IMIT Consulting
PROJECT FEATURES
Size: 72,000 ft2 designed for two floors of tenant fitout (one floor constructed) | Status: Completed 2021
LOCATION
Mississauga, Ontario
KEY SCOPE ELEMENTS
Open floor layout accommodated despite base building risers | Base building deficiencies identified, saving client time and money | Team exceeded contract obligations in protecting client from added costs due to COVID pandemic and to ensure timely project completion
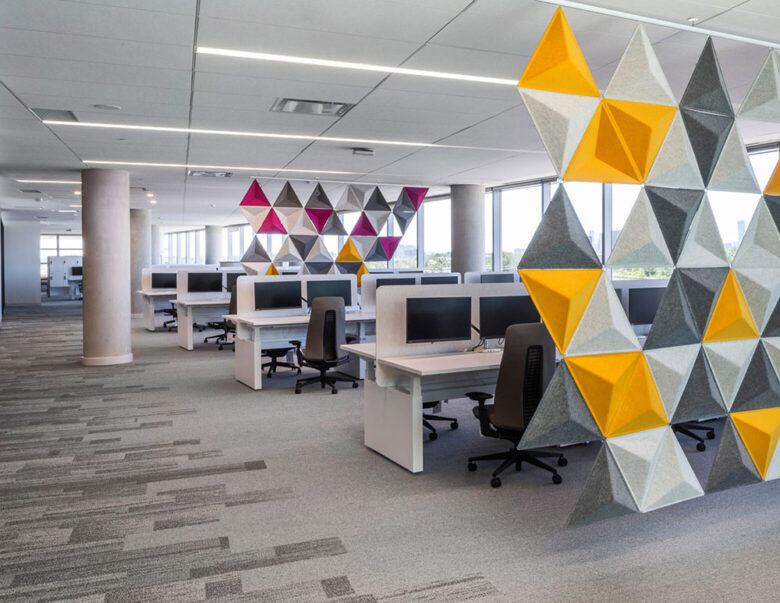
Open concept design
The client had expressed a preference for an open floor layout; however, several of the base building risers were in locations not conducive to the planned interior design. In order to accommodate the client’s wishes, we proactively identified a new shaft location, and re-routed various systems to deliver the floor layout desired by the client.
Pandemic response
The COVID 19 pandemic began in the midst of construction. The project team reacted immediately during these challenging times by providing effective and responsive coordination virtually. The team worked through construction-related delays, and helped mitigate supply distribution delays by using local contacts to expedite shipping to meet the client-requested deadlines.
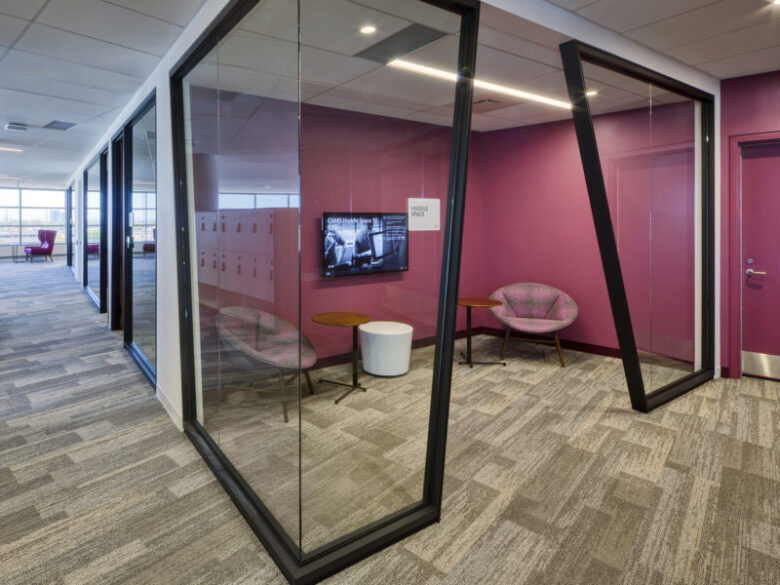
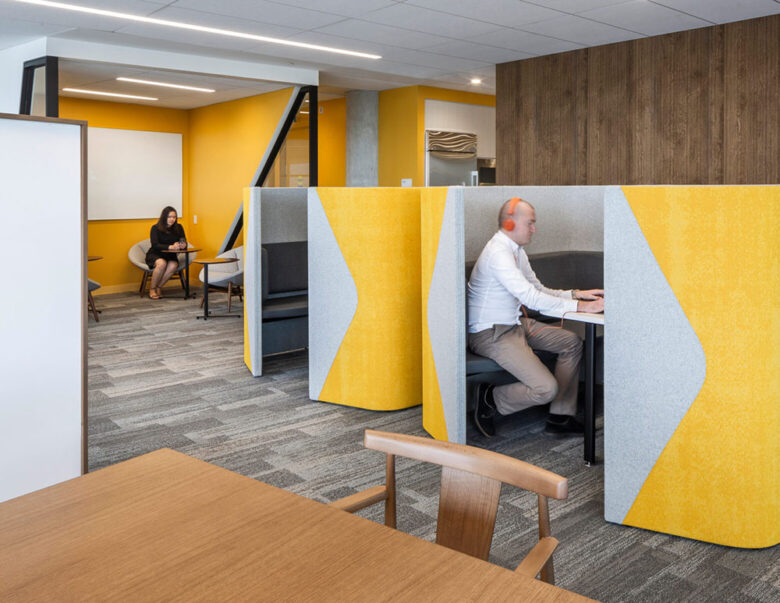
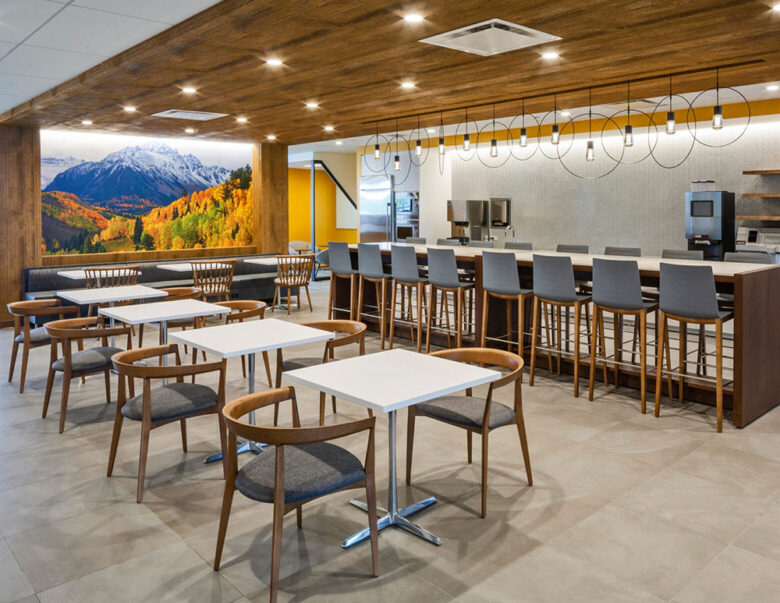