Service: Information and Communications Technology
Toronto Transit Commission
Toronto-York Spadina Subway Extension Pioneer Village & Finch West Station
The TTC’s 8.6 km line opened to the public in December 2017. All six stations are fully accessible and Wi-Fi equipped. The line is comprised of both tunnel and cut-and-cover sections. HH Angus provided mechanical and electrical consulting engineering for the Pioneer Village and Finch West stations.
Above ground, the new stations include a main entrance, secondary and automatic entrance and electrical substation. Our mechanical scope included ventilation and air conditioning of services spaces, sanitary and storm drainage for washrooms and service area, track drainage, fire protection systems, as well as incorporation of system-wide tunnel ventilation. In addition, it incorporated water-efficient plumbing fixtures and energy efficient HVAC systems.
Our electrical scope covered power distribution, lighting and communications systems. Design layouts were provided for power distribution of the subway station, as well as traction power for the trains.
SERVICES
Mechanical Engineering | Electrical Engineering | Lighting Design | Communications Consulting
PROJECT FEATURES
Status: Completed 2017
LOCATION
Toronto, Ontario
KEY SCOPE ELEMENTS
Underground subway stations with integrated bus terminals | Integrated traction power substation | Water-efficient plumbing fixtures and energy efficient HVAC systems
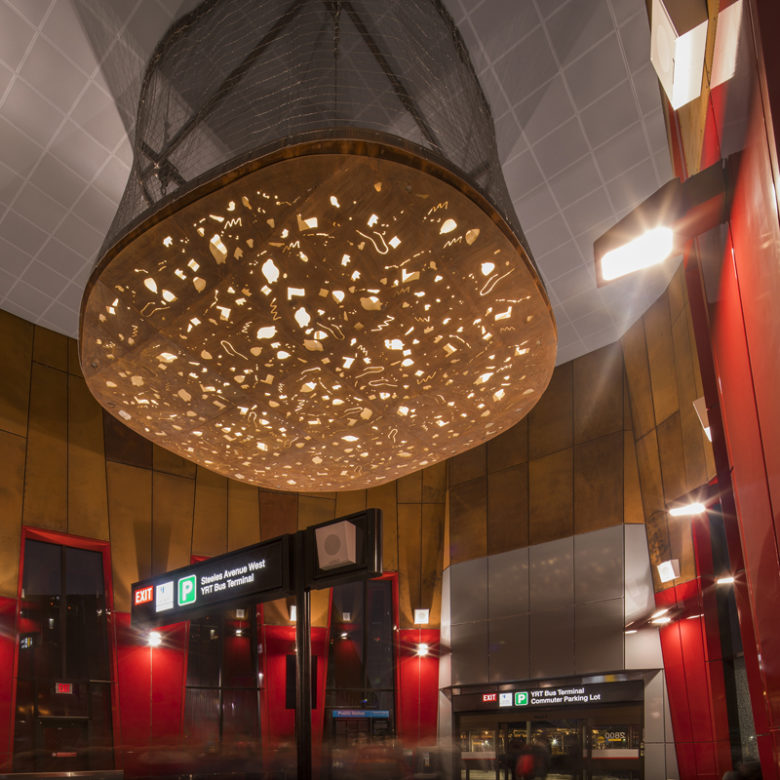
Custom transit lighting
The lighting design featured reduced power consumption. Lighting design for the exterior public zones incorporated increased daylight levels, LED lighting in pylon signs, and energy-efficient lighting in illuminated wayfinding signage.
Comprehensive communications design
The communications systems design included fire alarm protection, public address speakers, passenger intercom, TTC PAX telephones, public telephones and security systems, including closed circuit television.
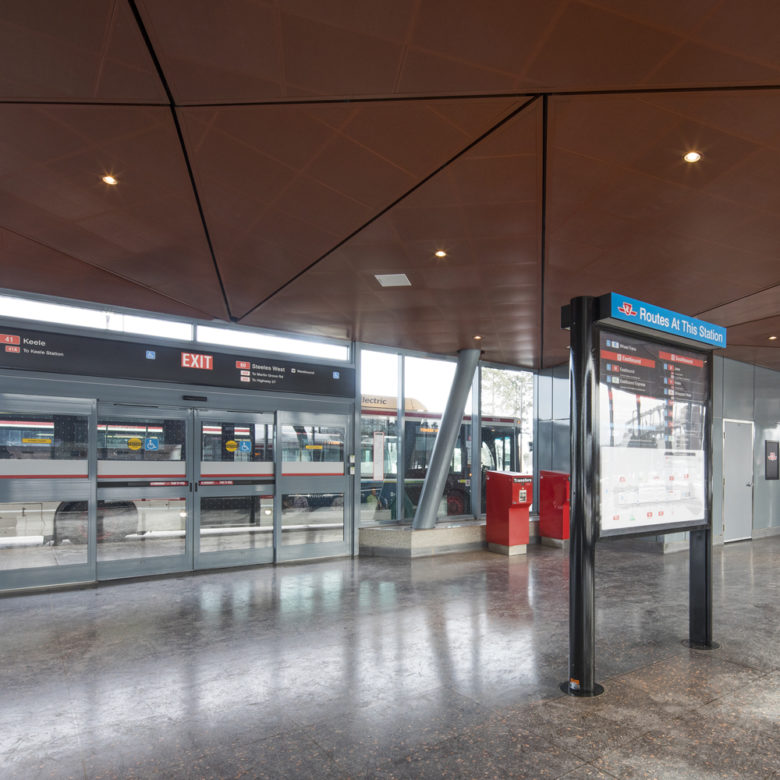
Fraser Health Authority
Lions Gate Hospital
The power plant on the Lion's Gate Hospital (LGH) campus was originally built in 1961 and had to be replaced since it was outdated. The new power plant will contain all new equipment for the steam and hot water generation, along with all the major mechanical, electrical, medical gas, water and other systems for the LGH campus.
HH Angus is replacing the existing power plant at Lions Gate Hospital with a new installation in an underground location. The existing steam-only power plant did not meet seismic requirements and was quite dated. The current project includes boilers, medical gas, plumbing and electrical equipment, as well as the routing of services through an existing tunnel system. This project will support the construction of the future Acute Care Facility to be built at the site.
The design provides a buried plant that is a hybrid of hot water and steam boilers; this design aids in reducing both energy and greenhouse gas emissions. The innovative design recovers heat from the power plant via a heat pump system and reject heat back into the reheat systems. An architectural feature boiler stack was also included in the design.
The original RFP required relocation of the bulk O2 system and, after a number of design iterations, the conclusion was to instead provide an Oxygen Concentrator system.
Implementation of Fraser Health Authority’S BIM standards was required for the project. This is the first time these standards were applied at HH Angus and the work helped to develop a baseline for future FHA projects.
Among the challenges of the project:
– With limited knowledge of the existing site, it was necessary to obtain all background information within a short time frame through access to existing drawings (dating back to 1960s) and performing multiple site reviews.
– To provide the best solution, HH Angus explored multiple options, above and beyond the requirements of the original RFP and, although the timeline for completion of design and implementation of new BIM standards was aggressive, all deliverables were met on time.
– When key members at the Hospital’s FMO team changed, the design was reintroduced multiple times, along with additional background information. In the end, our design was proven and accepted.
3D Views
Our 3D matterport scanner proved to be a great advantage for site reviews. The design team in Toronto was able to minutely reference the detailed 3D scan produced by our inhouse team and equipment.
SERVICES
Mechanical Engineering | Electrical Engineering | Lighting Design | IMIT Consultant
PROJECT FEATURES
Status: Completion 2020 | 3D Matterport modeling | Architectural feature stack | Oxygen concentrators | FHA BIM
LOCATION
Vancouver, British Columbia
KEY SCOPE ELEMENTS Replace power plant in underground location | Hybrid hot water/steam boilers | Heat recovery system | Architectural feature boiler stack | Enhance seismic resistance | FHA BIM standards applied to help develop future FHA projects
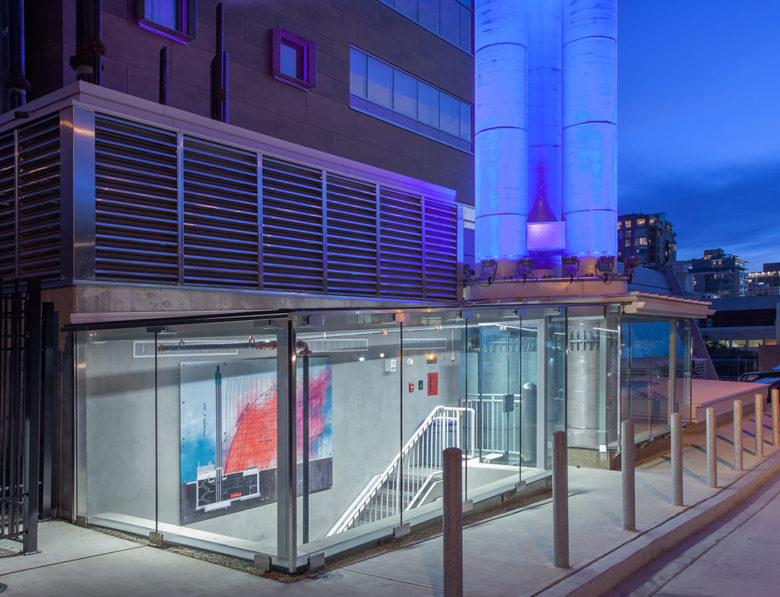
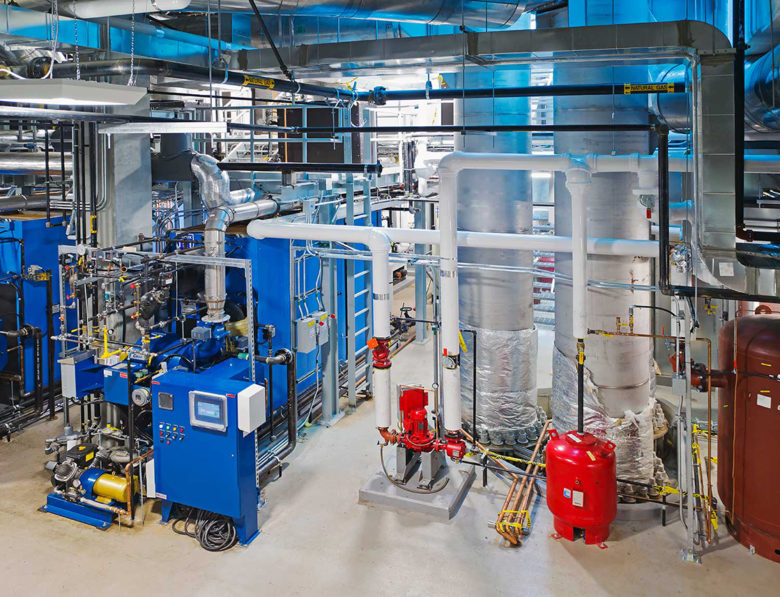
Centre hospitalier de l’Université de Montréal
(CHUM)
Designing the mechanical, electrical, and security systems for one of North America’s largest P3 acute-care hospitals required a comprehensive understanding of the crucial demands placed on a hospital’s electrical system; knowledge of the intent and intricacies of codes and standards; value-engineering approaches gleaned from alternate project delivery projects; and lessons learned from complex redevelopment projects.
The Centre hospitalier de l'Université de Montréal (translated as University of Montreal Health Centre, or CHUM) is a mega-hospital complex designed to replace three existing hospitals in Montreal. One of the largest P3 hospitals in North America, it occupies more than 2.5 city blocks with more than 334,000 m2 (3.5+ million ft2) of floor space.
The CHUM project has been honoured with ~30 awards, including Canada's top engineering award, the Schreyer Award 2018 for HH Angus, plus an ACEC Award of Excellence and three Illumination Engineering Society 2018 Awards for HH Angus’ lighting designs for the Passerelle Skybridge, the Steeple, and Interior Lighting.
The hospital complex consists of a main 20-storey acute care block, with five levels underground. The upper floors house 775 beds in single rooms, and the lower floors contain diagnostic and treatment functions, including a large emergency department, 39 operating rooms, 7 MRIs and a full cancer centre with 12 bunkers. Distinct blocks house ambulatory care clinics, office space and logistics. Our scope also included two large data centres.
The facility has been certified LEED® Silver. HH Angus responded to a number of restrictions and requirements in the RFP with alternative approaches that were subsequently implemented, benefitting the project in terms of better functional use of space, flexibility for the future, cost savings and significantly improved energy efficiency.
SERVICES
Mechanical Engineering | Electrical Engineering | Security Systems Design
PROJECT FEATURES
Size: 3,800,000 ft2 | Status: Phase 1 - 2017 | Ongoing renovations and upgrades | Winner - 2018 Schreyer Award, Canada's top engineering project award
LOCATION
Montréal, Quebec
KEY SCOPE ELEMENTS
Mechanical, electrical and security system designs were provided to facilitate concurrent development | More than 50 Revit® models linked | Project included components that would help future modification of the facility | Certified LEED Silver
A proven P3 approach
HH Angus developed an approach to deliver consistency and standardization of mechanical and electrical products with multiple contracts and installation contractors. To facilitate the concurrent development of multiple parts of the project, more than 50 Revit models were linked. This allowed work to proceed on construction documents for the core and shell of the building (including services), while design development continued in the clinical areas of the building.
Experience creates long-term efficiency
The RFP mandated a number of restrictions on the ventilation system that would have required two full intermediate mechanical floors and would have severely compromised future flexibility. We worked with CHUM and the proponent team to develop an alternative approach from which numerous benefits resulted, including the ability to modify occupancy and enable future renovations, which allowed an extra clinical floor to be constructed under the zoning height restriction.
Delivering more value
The RFP required a distinct air handling unit for each functional department, as well as restrictions on unit size and floors served. HH Angus proposed the use of larger, 100 percent outdoor air units serving multiple floors. We proved the merits of this approach to CHUM from an infection control perspective.
Proving a better solution to save energy
The RFP did not allow the use of heat recovery wheels due to perceived infection control concerns. We used 20+ years of successful experience with heat wheels to prove the approach to the client and compliance team. The RFP was modified to allow the use of heat wheels, enabling a much more cost effective and energy efficient solution.
Saving the client money
The RFP mandated a standby air handling unit for each critical care space, which would have required much higher capital and operating costs over the life of the building. We recommended manifolding a number of air handling units together to share the redundant capacity. This approach considerably increased overall reliability of the systems while reducing operating costs.
Robust, reliable, cost-effective electrics
Similar components in the electrical infrastructure were procured in separate equipment tender packages to obtain best pricing directly from the corresponding vendors. The installation scope was divided into sectors within the building and awarded to separate electrical contractors. This “carving up” of the design scope into multiple tender packages required a high degree of coordination with the DBJV, and was effective in keeping this massive ongoing project on track with budget and schedule.
Multifunctional security system design
Our Angus Connect Division designed a fully convergent IP-based (Internet Protocol) security system and the supporting IT infrastructure required for a large-scale Cisco high availability, medical grade network. We designed an IP-based integrated multimedia security system that includes several thousand IP-based cameras, intelligent card readers, and other security devices located throughout the hospital complex. This system includes PoE (Power over Ethernet)-controlled architectural door hardware connected to Cisco’s high availability medical grade network.
Discrete segments of the security system are reserved for clinical observation, parking control, visitor management, patient wandering and duress applications. Multiple control facilities were provided across the hospital, using multicasting over VLAN, configured on Cisco LAN.
The security system was designed to support sophisticated client “use and workflow cases”, providing interoperability, SOA (Service Oriented Architecture) and SOI (Service Oriented Infrastructure).
Angus Connect integrated all aspects of the security systems into a seamless and efficient operation, leveraging the most current technology wherever possible to improve efficiency, reliability and safety, thus simplifying information flow and access to users.
General Electric
Brilliant Factory
General Electric’s new state-of-the-art gas engine plant is one of the most advanced in GE’s global operations and the first of its kind in Canada. “It’s a plant that is reimagining how we manufacture. It incorporates all the concepts of lean: speed with excellent quality — coupled with everything that is now available and that is coming down the pipe in digital technology, with the latest in software developments.”*
— Elyse Allan, GE Canada CEO
HH Angus provided mechanical, electrical, plumbing, security, IT, lighting and vertical transportation consulting. The multi-modal plant, now owned by Advent International, manufactures gas engines that are coupled with either air or gas compressors, or with electric generators. The engines are distributed worldwide, primarily outside North America, in the oil and gas industry.
The plant runs three-dimensional machining simulations for CNC programs, gains real-time analytics to better understand the operating conditions of a machine or a test cell, operates lights-out machining, and combines all with advanced lean manufacturing practices.
Our IMIT scope included flexible structured cabling systems and supporting infrastructure, consisting of the latest shielded copper and fiber technologies, providing a transport platform for data, voice, video and other IP-based systems.
We also provided design for all low voltage technology systems. The factory uses equipment and machines embedded with sensors and connected to the high availability Industrial Internet Protocol-based network. Equipment data is streamed over secure links to the cloud for analysis.
Extensive design and installation of multiple audiovisual systems facilitate collaboration between global sites. Plant cabling design was provided per the most recent Industrial Premises standard. Working closely with the client’s IT, Security and AV groups, network-based systems were designed to the latest technology.
Our Angus Connect team was also involved in determining the performance requirements of client systems, product selection, preparation of working drawings and specifications, tender preparation and response evaluation.
SERVICES
Mechanical Engineering | Electrical Engineering | Security and IMIT Design | Vertical Transportation Consulting | Lighting Design
PROJECT FEATURES
Size: 450,000 ft2 | Status: Completed 2018
LOCATION
Welland, Ontario
KEY SCOPE ELEMENTS
Multi-model plant | Plant is fully air-conditioned to prevent "flash rust" | real-time analytics | Transport platform for data, voice, video and other IP-based systems | AV systems enable collaboration between global sites | Test cell scope added later | Met aggressive schedule for working drawings | LEED Silver Certified
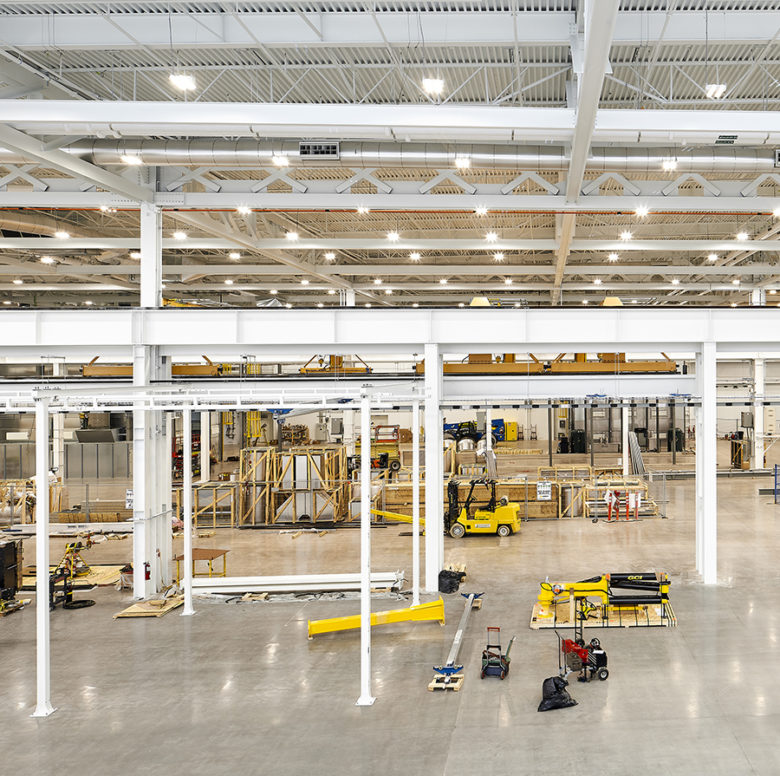
Custom HVAC control
The plant is fully air-conditioned to prevent ‘flash rust’, which can occur during machining of items such as crankshafts and connecting rods if humidity levels are not carefully controlled.
Industrial and support spaces
In addition to the main assembly and machine areas, three test cells, warehouse space, and paint areas, the plant also features front of house spaces such as offices, staff support, fitness centre, customer areas, hoteling for visiting customers and GE staff, conference rooms, etc.
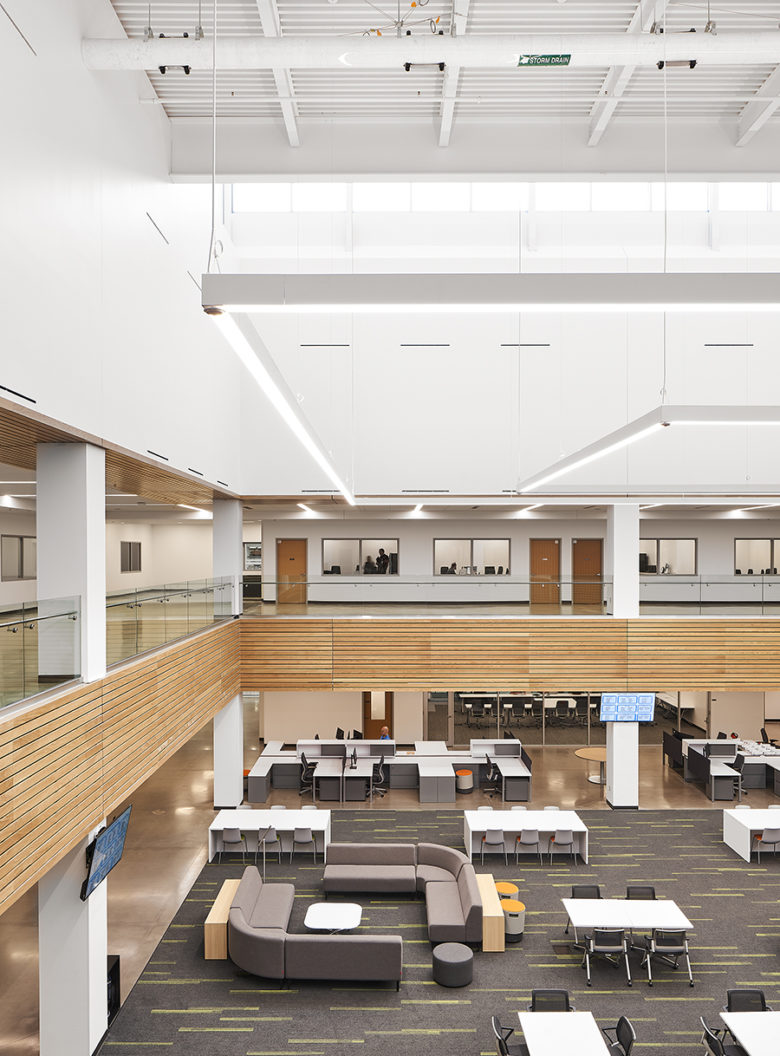
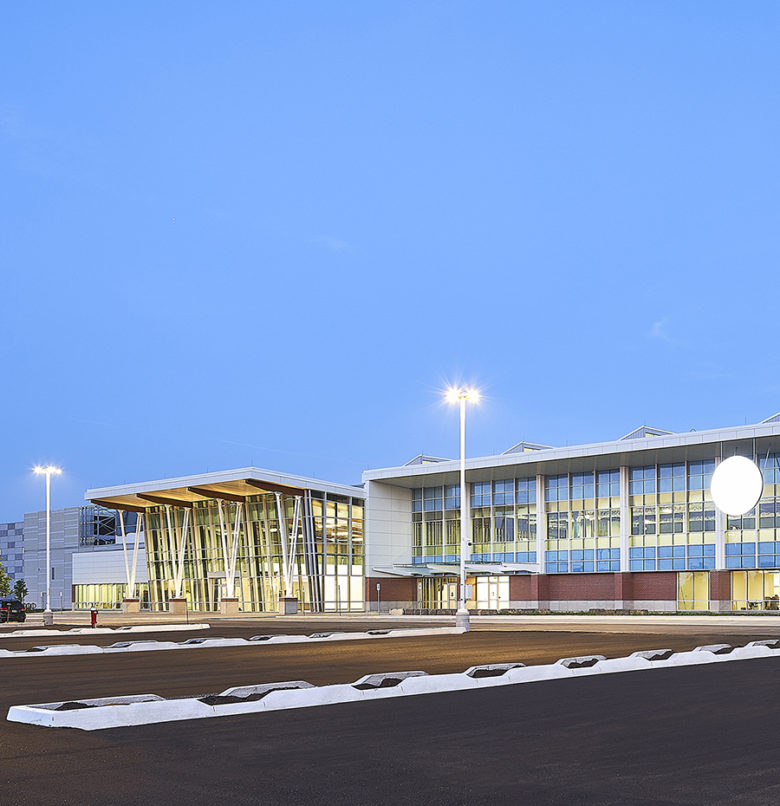
Expanding our scope
HH Angus’ project scope was increased to include the physical design of a significant new Test Cell addition to the plant, and to ensure Canadian compliance. The three test cells are connected to the main plant for testing engines prior to delivery. We met an aggressive schedule to produce working drawings for tender.
Mount Sinai Hospital
Lobby, Art Gallery, Security Renovations
Mount Sinai Hospital is world renowned as a research facility and acute care health sciences centre with numerous clinical strengths, including women’s and infants’ health, chronic disease management, specialized cancer care, emergency medicine, and geriatrics.
HH Angus’ scope of work for this renovation project included two new entrances, exterior pathway lighting, a showcase art gallery/healing centre, food court, security desk and waiting area. The work also incorporated part of the level above the main lobby.
The mechanical scope included a dedicated Air Handling Unit for the kitchen, an ecology unit with roof-mounted exhaust to serve kitchen hoods in the food court concessions, as well as the complete renovation of the HVAC, fire protection, and plumbing systems for the renovated area. This included mechanical services for concessions and the provision of DDC controls.
Our electrical scope included reworking the fire alarm and security system, new electrical infrastructure, and new custom lighting. A lighting control system was designed to manage lighting in a variety of spaces, including the new art gallery/healing centre, waiting area, food court, exterior pathways, and synagogue. Design for the two new main entrances provided power for revolving doors, along with custom interior and exterior lighting.
Several design changes were required during construction to satisfy owner-driven revisions. User meetings were held to confirm that the scope of work was clear before final drawings were submitted. We also provided review sets and cut sheets to ensure the design met the unique requirements of the end users.
SERVICES
Mechanical Engineering | Electrical Engineering | IT/Communications Design | Lighting Design
PROJECT FEATURES
Size: 34,000 ft2 | Status: Completed 2016
LOCATION
Toronto, Ontario
KEY SCOPE ELEMENTS
Main lobby renovation & new healing centre/art gallery | Lighting designed to accentuate gallery artwork | Complete renovation of HVAC, fire protection and plumbing systems |New electrical infrastructure and lighting control system
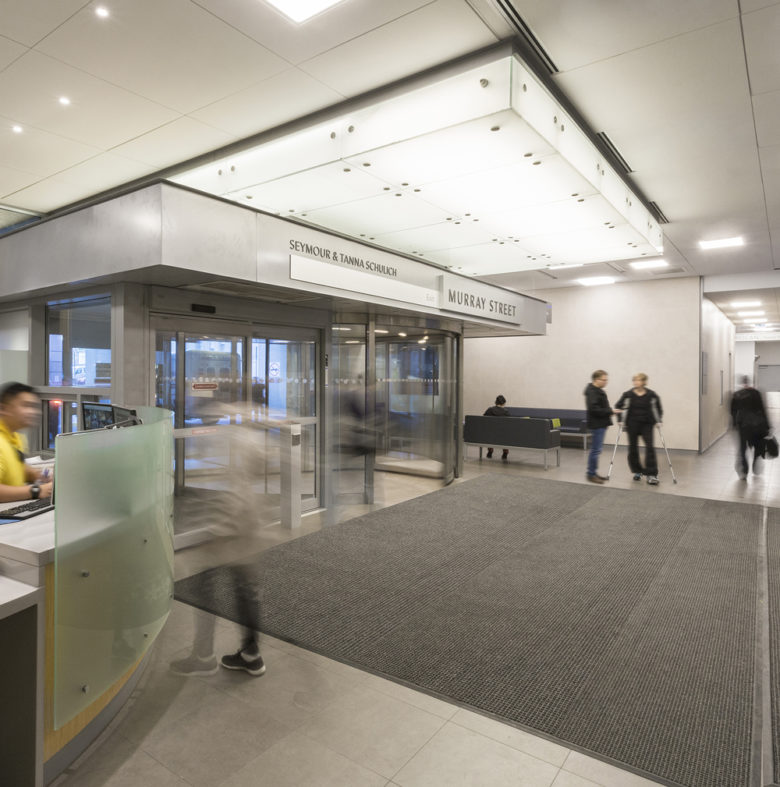
Continous operations
The project had to be executed in multiple phases because the Hospital’s main floor could not be closed to visitors and patients. HH Angus responded by providing close coordination with the prime consultant, the hospital and contractors on site in order to ensure smooth project delivery.
Listening to stakeholders
An interesting challenge for the lighting design team was the need for the custom lighting and controls package to incorporate the design requirements from the curator of the new art gallery, as well as from the Rabbi of the Hospital’s synagogue.
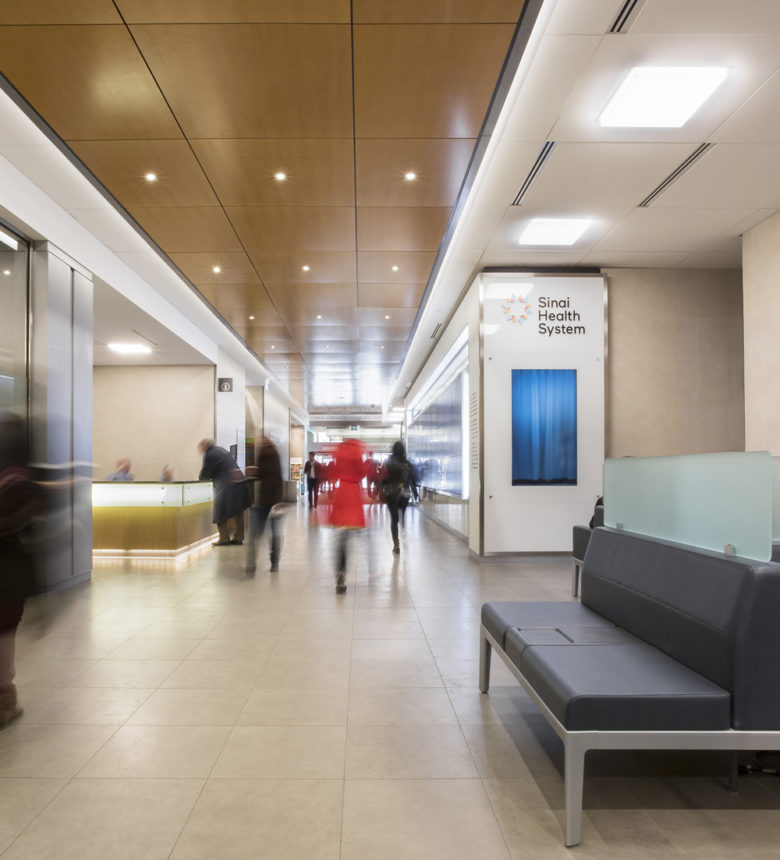