Service: Mechanical Engineering
Toronto Transit Commission
Downtown Relief Line South (Ontario Line)
“The proposed Relief Line South, a 7.5km long planned subway line with 8 stations, was intended to connect the Yonge-University-Spadina Subway (Line 1) downtown to the Bloor-Danforth Subway (Line 2). The Relief Line South was conceived to relieve crowding on Line 1 south of Bloor, at the Bloor-Yonge Station, and on the surface transit routes coming in and out of downtown.”*
HH Angus was engaged to produce preliminary systems design for two subway stations on the line: Gerrard Station, an in-line station, and Pape, one of the interchange stations, in this case with the existing Bloor/Danforth Line.
Funding and plans for transit relief lines are under review.
* Quote source: Reliefline.ca
SERVICES
Mechanical Engineering | Electrical Engineering | Vertical Transportation
PROJECT FEATURES
Size: 7.5km | Status: Ongoing
LOCATION
Toronto, Ontario
KEY SCOPE ELEMENTS
Preliminary Design
Toronto Dominion Bank
TD 23
TD Bank Group was awarded the world’s first WELL™ Gold certification for their TD23 pilot project. This ground-breaking achievement was a milestone in the development, growth and expansion of the WELL™ Certification program.
HH Angus is proud to have participated in the first project to be certified WELL Gold by the International WELL™ Building Institute (IWBI) through version 1 of its WELL Building Standard (WELL). We congratulate TD Bank Group for the success of their pilot project – the 23rd Floor of Tower One at the Toronto Dominion Centre. The project provided us with an excellent understanding of the WELL™ certification process.
The WELL™ Building Standard is the first of its kind to focus on the health and wellness of building occupants. It identifies performance metrics, design strategies and policies that can be implemented by owners, designers, engineers, contractors, users and operators of buildings. We believe the Standard has the potential to be widely embraced and adopted in conjunction with current LEED practice, so we were delighted to be involved with WELL™ in its early stages.
SERVICES
Mechanical Engineering | Electrical Engineering
PROJECT FEATURES
Status: Completed 2018
LOCATION
Toronto, Ontario
KEY SCOPE ELEMENTS
Canada's 1st Integrated Project Delivery (IPD) for commercial interior | LEED Platinum certified | WELL™ | Gold Certified
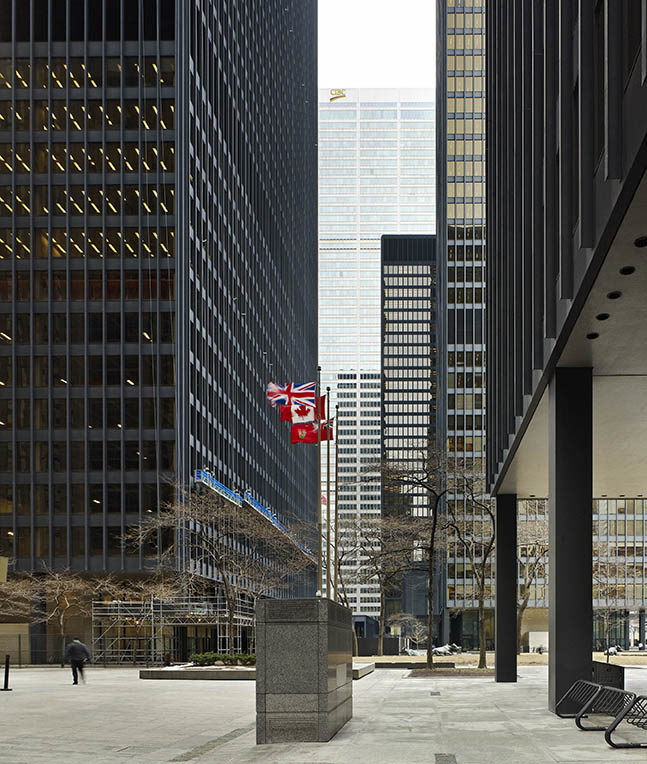
Optimizing infrastructure renewal
HH Angus’ Commercial Division has worked with TD Bank Group on portfolio optimization for several years. This work has been geared to implementing a broad infrastructure renewal. The Optimization project also represented Canada’s first Integrated Project Delivery (IPD) contract for a commercial interior, and was the first TD corporate interior to obtain LEED Platinum Certification.Maple Leaf Sports and Entertainment
BMO Field ExpansionHH Angus and Associates provided mechanical and electrical consulting engineering for renovations to BMO Field. Home to the TFC, Toronto’s MLS football team, the existing facility quickly outgrew its amenities, a testament to the team’s popularity.
The BMO Field facility expansion featured: 8,400 additional seats, new washrooms and concession stands; 12 new executive suites; 2 party suites; a loge box; new full-service kitchen for restaurants, suites and clubs; 2 new private clubs (accommodating 230 / 420 patrons); expansion of the Rogers Club from 500 to 750 patrons, plus upgraded finishes and improved food, beverage and washroom facilities; a new, larger full HD video board; new loading dock; support spaces; and a new concourse at the south end of the stadium, creating one continuous concourse on the upper level. The project was drafted in REVIT, although it is not a true BIM project.
Some of the project challenges included coordination of the design package with the realities of site constraints and energy goals. HH Angus had dealt with these challenges in the past and had a depth of experience in Construction Management, P3, and Integrated Project Delivery methods, as well as having a firm grasp of the complexities associated with coordinating the design across multiple Revit models and with multiple firms.
The accelerated construction schedule presented a significant challenge. Work that traditionally occurs sequentially had to be delivered concurrently, which put pressure on the design team to accommodate not only increased coordination, but also a high number of changes from the original design intent.
One of the unique engineering considerations was the winterization of washrooms and concession areas. These areas are exposed directly to the elements during the winter and the facility management team did not want to drain the domestic system at the end of every season, as they had to do with the existing concourse areas.
SERVICES
Mechanical Engineering | Electrical Engineering | Energy Modeling | Lighting Design | Security and Communications Design
PROJECT FEATURES
Size: 150,700 ft2 | Status: Completed Phase 1 - 2015 & Phase 2 - 2016
LOCATION
Toronto, Ontario
KEY SCOPE ELEMENTS
Renovation and expansion | Unique considerations included winterization of washrooms and concession areas to eliminate draining the domestic system at the end of each year
Halton Healthcare
Oakville Trafalgar Memorial Hospital
As a large super hospital, this greenfield ~ 1.5 million ft2 facility features ORs, Emergency Department, Diagnostic Imaging, Mental Health, Long term Critical Care, and Dialysis services. There is also a large central kitchen and central Sterile Processing department. The hospital has been certified LEED Gold NC, exceeding its target of LEED Silver NC.
The central utility plant provides 4200 tons of cooling, 1500 bhp of hot water and 1500 bhp of steam. There is 15 MW of generator capacity onsite, along with 72 hours of fuel oil storage and a large fuel oil distribution system.
Some of the complexity inherent in this project was due to the design work being split between multiple engineering companies, which significantly increased the amount of coordination required. A key challenge was simply the scale of the new hospital, which increased the complexity of all of the systems. It required integration of systems across multiple engineering companies who were producing different portions of the design.
Another challenge was the extremely tight project schedule. This meant that tasks, which are normally completed sequentially, had to be done concurrently. This required very exacting planning and accelerated design work. Regular meetings with multiple engineering and architecture disciplines allow parties to bring their issues and design requirements to the table and to work through them in a collaborative way.
The vertical transportation design scope included 33 elevators servicing the main hospital building and 3 providing service to the parking garage.
The project co. required commissioning support for the contracting team in order to achieve milestones. HH Angus assembled a separate team of technical personnel to blitz specific systems in a 7-week period. With little preparation time, HH Angus leveraged members of the design team to train the commissioning personnel prior to going to site.
SERVICES
Mechanical Engineering | Vertical Transportation Consultant | Commissioning Support
PROJECT FEATURES
Size: 1.5 million ft2 | Completed 2015 | Greenfield super hospital project | LEED Gold
LOCATION
Oakville, Ontario
KEY SCOPE ELEMENTS
Central Utility Plant provides 4200 tons of cooling, 1500 bhp of hot water and 1500 bhp of steam | 36 elevators serve the hospital and parking facilities
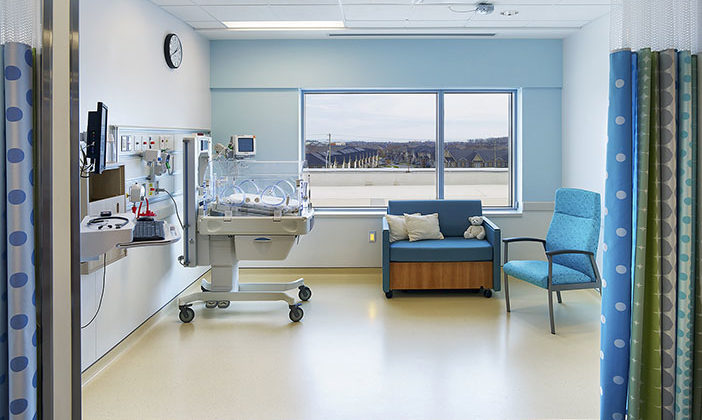
Alternate approach to Cx
Through a cycle of improvements in methodology, HH Angus was able to improve productivity on site by more than 100% with an alternate approach to commissioning, which was shared with other onsite commissioning groups.
SickKids
Peter Gilgan Centre for Research & Learning
“This investment in the Research and Learning Tower will help ensure that Canada remains a world leader in health research, and that we will continue to make discoveries that benefit children around the world.”
– Gary Goodyear, Minister of State for Science and Technology
HH Angus provided mechanical and electrical consulting engineering for this 740,000 ft2 high-rise research and educational facility. This building enhanced the overall campus of SickKids, which totals over 2,500,000 ft2. SickKids is a landmark hospital and renowned internationally as a world-class institution.
The facility has been certified LEED® Gold. Energy modeling indicated a significant improvement over the minimum energy performance required by the program. Systems were segregated to achieve significant thermal reuse within the facility. The option to integrate a waste heat recovery system from the neighbouring district heating provider was incorporated into the design to realize even greater energy efficiency in future.
The building services design supported the main objectives for the new facility:
- Consolidate the Research Institute into a cohesive unit
- Integrate research functions with the hospital
- Provide flexibility for future change
- Maximize functionality and efficiency
- Share support functions
- Utilize current technologies and infrastructure, including a plan for increased security for highly specialized spaces such as Containment Level 3
- Incorporate exemplary sustainable “Green” building design concepts and system
- Create a high-tech, cost-effective space for evolving state-of-the-art technologies
The interesting design challenges inherent in this high-rise lab building contributed to both the complexity and enjoyment of the design process, including a 1½ storey vivarium and 40,000 ft2 of educational space.
Quote source: SickKids
SERVICES
Mechanical Engineering | Electrical Engineering | IT & Communication Design | Vertical Transportation | Lighting Design
PROJECT FEATURES
Size: 740,000 ft2 with 40,000 ft2 educational space | Status: Completed 2013
LOCATION
Toronto, Ontario
KEY SCOPE ELEMENTS
Complex systems design for a tight downtown urban space | 1.5 storey vivarium | LEED Gold Certified | Incorporated options to permit a future waste heat recovery system