Service: Mechanical Engineering
Ernst & Young
100 Adelaide Tower, Multi-Floor Fitout
“Throughout the tower...elements of wellness enhance the EY experience for employees, including quiet spaces for recharging, changing rooms for getting ready on the go, showers, bike parking and more.”
– EY@Work
The downtown Ernst & Young (EY) Tower is Toronto’s first Triple A office building constructed to LEED Platinum standards. The 255,000 ft2 tenant project was an 11-floor fitout designed to be the epitome of the modern flexible work environment, to reflect EY’s new ‘Workplace of the Future’. Amenities include tech-enabled boardrooms, collaborative meeting areas, a dynamic event space and EY Toronto’s Innovation Centre. The building has received Toronto’s second WELL Gold certification. (HH Angus is proud to have been involved in both of these WELL Gold-certified projects).
Features of the project include a new interconnecting stairway between two floors; a café/hub, IT equipment room, and Main Communications Room on each floor; Reception and client-facing floor; intricate lighting design with high-end luminaires, requiring complex design coordination by the lighting team; new guest washrooms; catering kitchen; a conference floor with the design intent that spaces be multipurpose; executive suite; training facility; mail room; office services; and IT on-site services.
SERVICES
Mechanical Engineering | Electrical Engineering | Lighting Design
PROJECT FEATURES
Size: 255,000 ft2 | Status: Completed 2018
LOCATION
Toronto, Ontario
KEY SCOPE ELEMENTS
Toronto's first Triple A office building constructed to and certified LEED Platinum | WELL Gold certified | Intricate lighting design | Flexible work spaces
Billy Bishop Toronto City Airport
Expanded Air Terminal Building
When the new 150,000 ft2 terminal first opened to the public in 2010, the airline expected to almost double the number of passengers from the year before. Phase Two included 10 bridged aircraft gates and two additional passenger lounges. The terminal includes a mix of retail, food services, duty-free, car rentals and other amenities.
The large arrivals hall area, along with the increasing number of people using it, required a specialized heat recovery system. HH Angus designed a high efficiency enthalpy heat wheel system using outdoor air supply.
Among the benefits of this heat recovery system are reduced operating costs from recovering heat that would otherwise be lost by venting to the outside. In turn, this allows for a reduction in the size and capacity needed for the heating and cooling plant that serves the system.
An exterior sprinkler system for the apron area was included in our mechanical design. This system protects building occupants in the event of a jet fuel fire on the tarmac.
Some of the interesting design challenges on this project included the integration of the sanitary sewage system with the existing Terminal system. The Toronto Islands site has no gravity drainage and requires a pumping system for sanitary sewage. Also, the site is a live airport operation, which presented unique challenges regarding phasing of services.
Our elevator system designs responded to user needs for accessibility, safety, reliability and operational efficiency. Based on anticipated traffic numbers, plus luggage, a single large roped-hydraulic elevator (2,270 kgs) serves travelers in the corridor leading from the Ferry Building. Adjacent to this elevator, three reversible escalators serve the large numbers of passengers travelling without luggage, or with small carry-on baggage. These escalators are direction-based upon dynamic requirement.
The terminal’s airside area is separated into domestic and trans-border. Each has been fitted with a single, smaller roped-hydraulic passenger elevator (1590 kgs), and a single reversible escalator for passengers with carry-on bags only, again direction-based on dynamic requirement.
SERVICES
Mechanical Engineering | Vertical Transportation
PROJECT FEATURES
Size: 150,000 ft2 | Status: Completed 2011
LOCATION
Toronto, Ontario
KEY SCOPE ELEMENTS
High efficiency enthalpy heat wheel system using outdoor air supply for arrival hall area | Engineered 10 bridged aircraft gates, 2 new passenger lounges along with a mix of retail, food services, duty-free, car rentals and other amenities | Geothermal heat rejection for cooling plant | Implemented recapture and reuse of all rainwater | Reversible escalator | Exterior sprinkler system for the apron area to protect against fuel fires
eBay Canada
Heritage Building Office Renovation
There were several interesting engineering challenges in designing building systems for these downtown Toronto heritage buildings and connecting corridor bridge.
The first challenge was the heritage designation, which limited what changes could be made without municipal approval. In addition, the building interior is all wood, and it was important to maintain the character of the site. Plus, in order to make the low-height floors look as large as possible, all existing mechanical ductwork had been removed.
The interior design called for open ceilings, so the appearance of the ductwork had to suit the design concept. The first order of business was to establish at what height and location the ductwork could be installed. Adding to the constraints, the ducts needed to be located over the workstations, close to the support columns, and the main corridors kept free.
Another challenge facing the team was fresh air, or rather the lack of it. The floor density of 116 ft2 per person, 242 workstations, 17 meeting rooms, plus a large gathering room and a shopping showcase room pushed the existing building fresh air over its limits. To solve this, an additional fresh air make-up air system had to be installed. Because no additional shafts were possible, we located a courtyard next to the connecting bridge and ran ductwork over the roof and down the back of the building, almost out of sight.
The existing electrical supply consisted of two 200 amp panels at 600 volts, with no power upgrade possible. Our team worked the electrical design to balance the loads and “make the system work”, taking into account the new roof fresh air unit and additional AC systems required for LAN and conference rooms. All of these added to the existing electrical load. A basket tray system at high level looping the furniture was used for wiring and cabling. Our fire protection specialists ensured code compliance for all hoses and sprinklers. They also designed the plumbing, which brought its own challenges as the landlord had stipulated no visible piping.
SERVICES
Mechanical Engineering | Electrical Engineering | Lighting Design | Fire Protection
PROJECT FEATURES
Size: 31,300 ft2 | Status: 2014
LOCATION
Toronto, Ontario
KEY SCOPE ELEMENTS
Work completed within heritage designation | Electrical load balancing to meet additional power load without possibility of power upgrade | Code compliance for all fire protection systems | Landlord restrictions met regarding plumbing and HVAC design
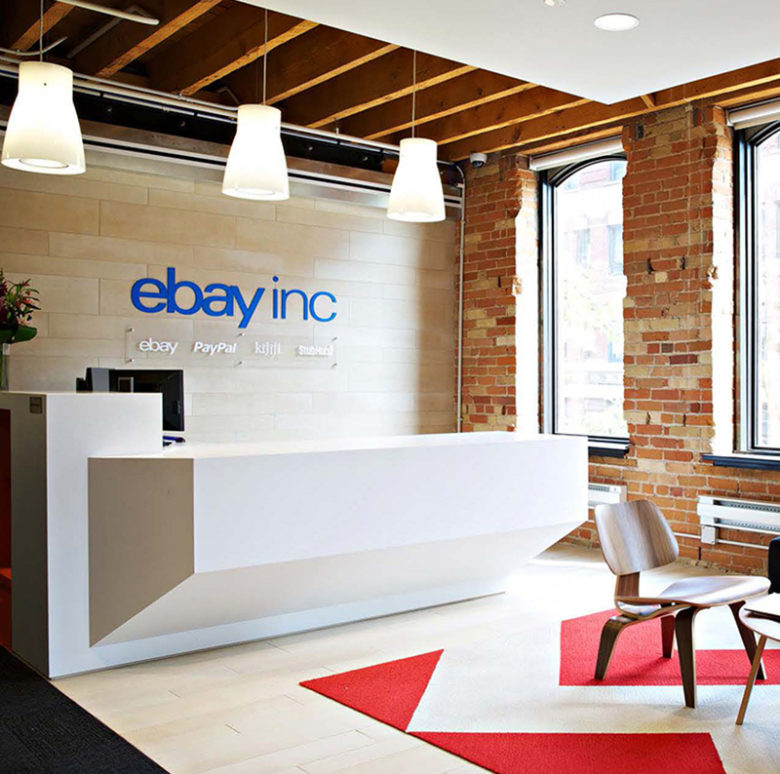
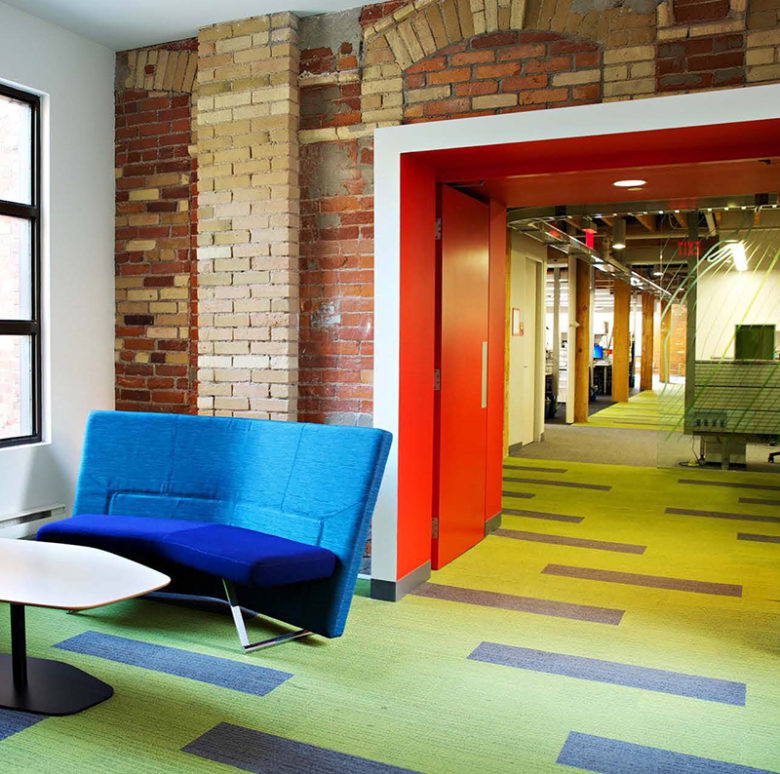
— Images courtesy of Sirlin Giller & Malek Architects
Humber College
Student Welcome & Resource Centre
The Student Welcome and Resource Centre at Humber College provides a high-visibility landmark gateway to the campus, and a highly accessible focal gathering place for students and the public.
The campus gateway is a standalone facility at Colonel Samuel Smith Park, an historic agricultural parkland on the shores of Lake Ontario.
As the mechanical and electrical engineering consultant on the Planning, Design and Compliance (PDC) team, HH Angus contributed to the development of a detailed space program, room layouts and adjacencies, including space data sheets.
Our project scope included developing the design brief and schematic plans for a comprehensive PSOS (Project Specific Output Specifications). The PDC team reviewed all design submissions to ensure full compliance with the original schematic design and PSOS.
The PDC team submitted all necessary planning documents to facilitate development. This included completion of massing and setback drawings to support discussions with city planning to obtain feedback to inform the RFP. The team also attended public meetings and open houses to represent Humber’s interests and answer design-related questions.
SERVICES
Mechanical Engineering | Electrical Engineering | PDC team
PROJECT FEATURES
Size: 43,500 ft2 | Status: Completed 2017
LOCATION
Toronto, Ontario
KEY SCOPE ELEMENTS
Detailed space program, room layouts and adjacencies, including space data sheets | Design brief and schematic plan for comprehensive PSOS | Sustainable design strategies included green roof and large areas of landscaping | Certified LEED silver
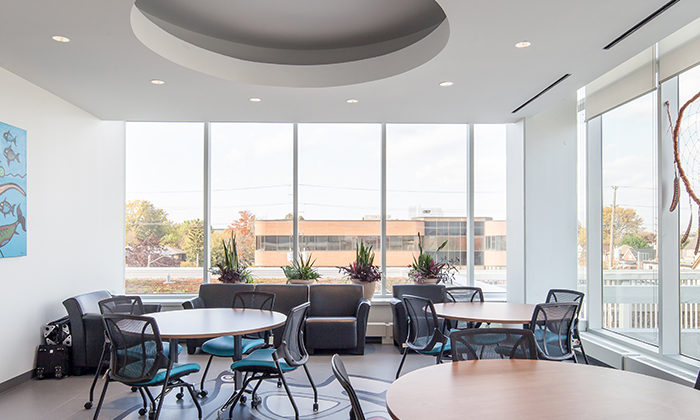
Engineering for occupant comfort
Certified LEED Silver, the four-story structure houses 43,500 ft2 of space for student services, cultural facilities, and wellness programs.
Working with nature
Sustainable design strategies included a green roof and large areas of landscaping. Full-height glazing on the east and north elevations maximize daylight harvesting while metal sunscreens and shade trees reduce solar gain in summer.
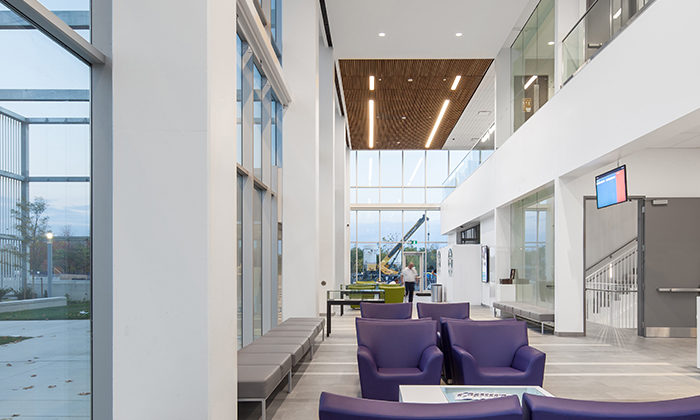
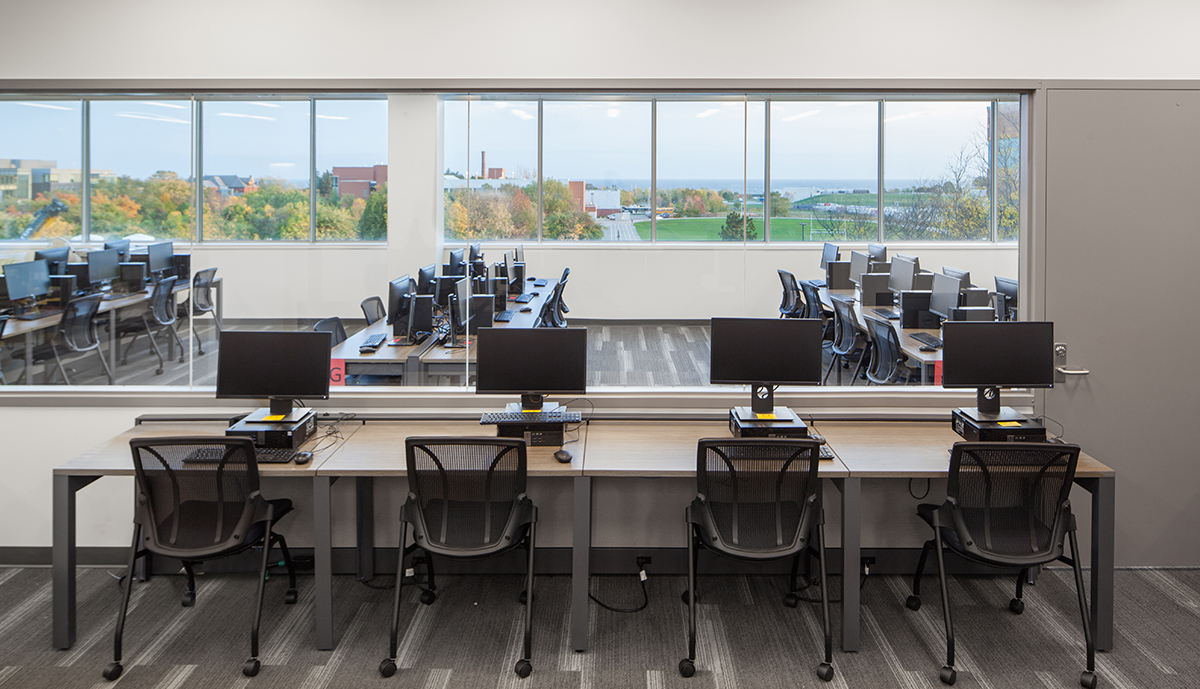
Mount Sinai Hospital
Lobby, Art Gallery, Security Renovations
Mount Sinai Hospital is world renowned as a research facility and acute care health sciences centre with numerous clinical strengths, including women’s and infants’ health, chronic disease management, specialized cancer care, emergency medicine, and geriatrics.
HH Angus’ scope of work for this renovation project included two new entrances, exterior pathway lighting, a showcase art gallery/healing centre, food court, security desk and waiting area. The work also incorporated part of the level above the main lobby.
The mechanical scope included a dedicated Air Handling Unit for the kitchen, an ecology unit with roof-mounted exhaust to serve kitchen hoods in the food court concessions, as well as the complete renovation of the HVAC, fire protection, and plumbing systems for the renovated area. This included mechanical services for concessions and the provision of DDC controls.
Our electrical scope included reworking the fire alarm and security system, new electrical infrastructure, and new custom lighting. A lighting control system was designed to manage lighting in a variety of spaces, including the new art gallery/healing centre, waiting area, food court, exterior pathways, and synagogue. Design for the two new main entrances provided power for revolving doors, along with custom interior and exterior lighting.
Several design changes were required during construction to satisfy owner-driven revisions. User meetings were held to confirm that the scope of work was clear before final drawings were submitted. We also provided review sets and cut sheets to ensure the design met the unique requirements of the end users.
SERVICES
Mechanical Engineering | Electrical Engineering | IT/Communications Design | Lighting Design
PROJECT FEATURES
Size: 34,000 ft2 | Status: Completed 2016
LOCATION
Toronto, Ontario
KEY SCOPE ELEMENTS
Main lobby renovation & new healing centre/art gallery | Lighting designed to accentuate gallery artwork | Complete renovation of HVAC, fire protection and plumbing systems |New electrical infrastructure and lighting control system
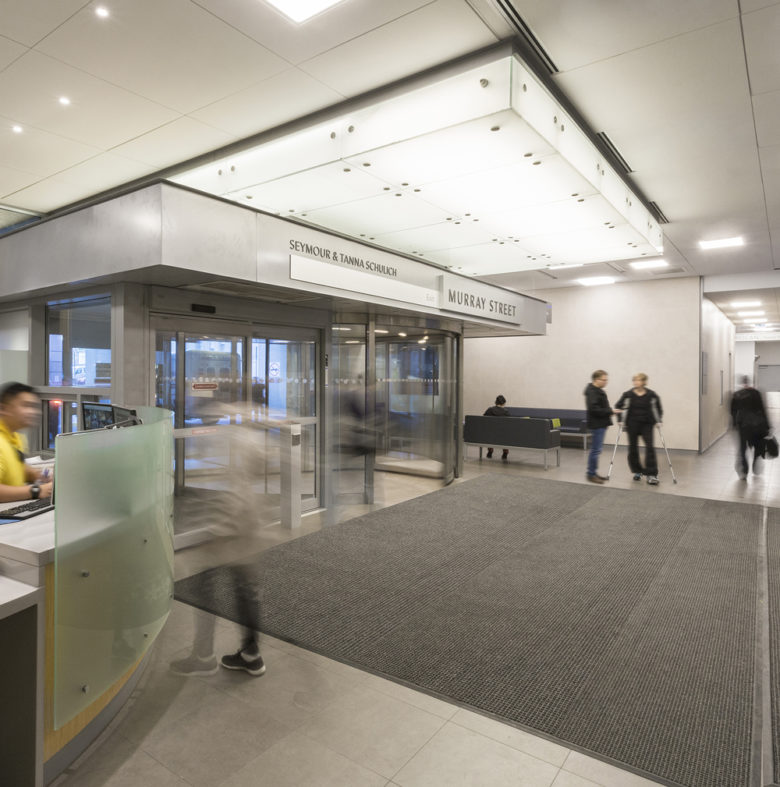
Continous operations
The project had to be executed in multiple phases because the Hospital’s main floor could not be closed to visitors and patients. HH Angus responded by providing close coordination with the prime consultant, the hospital and contractors on site in order to ensure smooth project delivery.
Listening to stakeholders
An interesting challenge for the lighting design team was the need for the custom lighting and controls package to incorporate the design requirements from the curator of the new art gallery, as well as from the Rabbi of the Hospital’s synagogue.
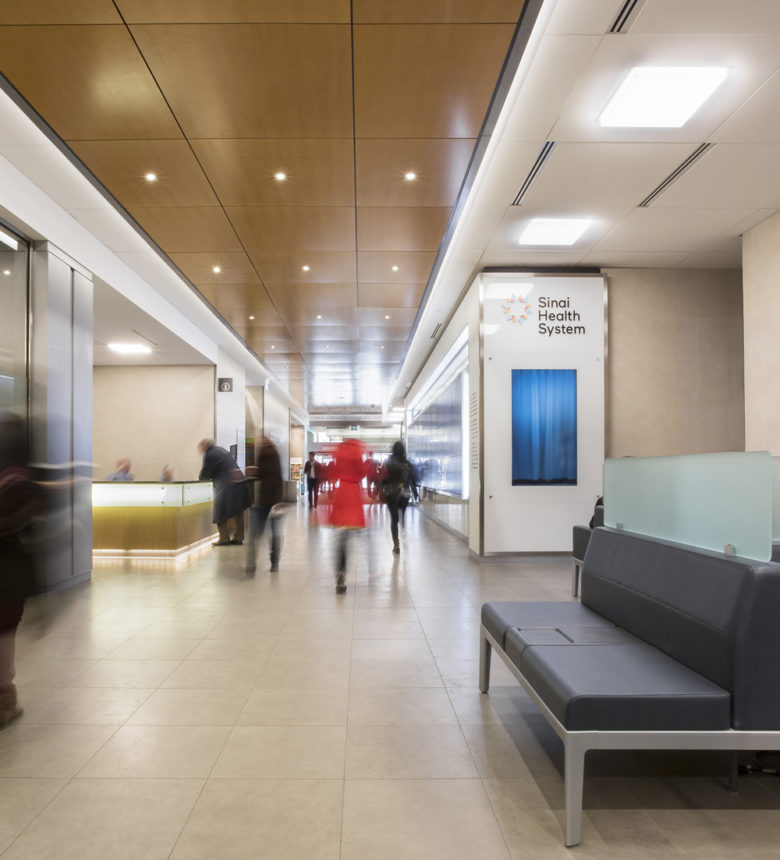