Service: Mechanical Engineering
Siemens Canada
Algonquin College Trigeneration Plant
HH Angus was retained to design a trigeneration plant for Ottawa’s Algonquin College. Our scope included review of Siemens’ PSUI application to IESO, and assisting with their application. Because the existing central utility plant (CUP) was not large enough to accommodate new plant systems, our team developed a pre-engineered building to be built adjacent to the existing CUP.
As Prime Consultant, HH Angus retained Milman and Associates to undertake the required structural engineering, including a roof design to accommodate the cooling towers, rad cooler and transformer. An additional mezzanine was added to house auxiliary equipment.
In order to maximize the usable heat during summer months, a 350 ton absorption chiller, using double effect flue gas and hot water, was detailed. The 2 MW reciprocating trigeneration plant features selective catalytic reduction units and a heat recovery boiler.
Some project challenges included:
- Integrating and commissioning a trigeneration system into an operating facility
- Noise constraints due to proximity of CUP to College operations
- Space constraints due to pre-engineered building
- Footprint was maxed out based on site restrictions; HH Angus had to take into account future co-gen, chiller and ancillaries
- Ongoing upgrades in CUP heating and cooling, which HH Angus coordinated with another consultant
- Operating flexibility required for both parallel and island operation
- Solutions included: designed mezzanines in the existing CUP to house equipment and accommodate new, pre-engineered building for the second cogen and chiller; and rigorous scheduling coordination with Utility and College operations staff
SERVICES
Prime Consultant | Mechanical Engineering | Electrical Engineering
PROJECT FEATURES
Status: Completed 2017
LOCATION
Ottawa, Ontario
KEY SCOPE ELEMENTS
Review of PSUI application to IESO | 350-ton absorption chiller | 2 MW reciprocating trigen plant with selective catalytic reduction units & heat recovery boiler
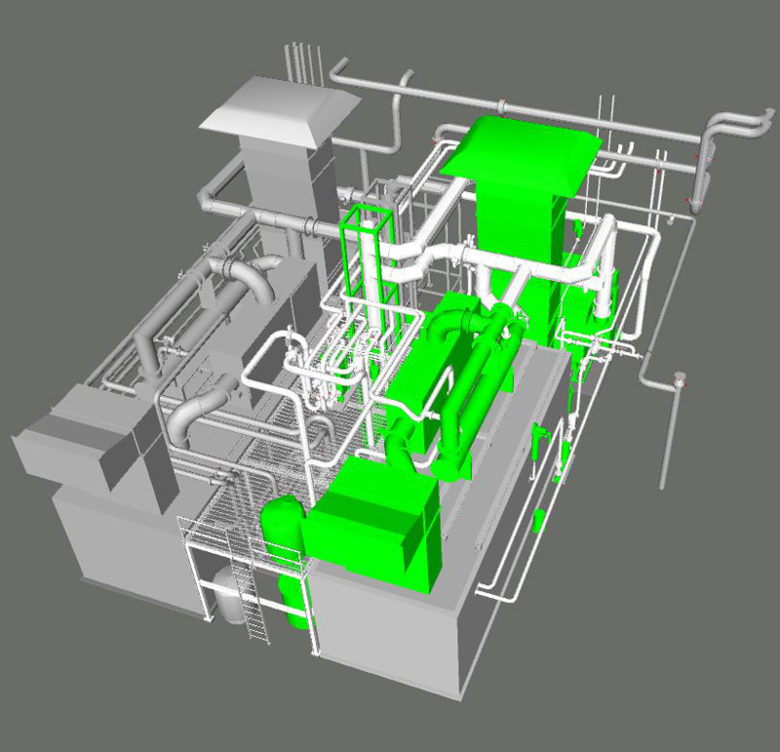
Minimizing Disruption
All new equipment was connected to existing systems, with electrical connections restricted to well-planned shutdowns, resulting in minimal disruption to the ongoing operations of the campus.
SickKids
Peter Gilgan Centre for Research & Learning, ICAT
Creative solutions were required to accommodate the extremely intense and sophisticated computer systems within the architectural constraints of this building.
Angus Connect provided a Canadian first — the design and implementation of an HPC-High Performance data centre in a healthcare research facility.
Our recommended technical solution involved an overhead communications wiring system design, using multiple cable trays with an integral cable access management system. This innovative system design solution resulted in considerable space savings over a conventional system. A conventional raised floor communications cabling system was not an option due to space restrictions.
This Data Centre, which supports data cabinets with high performance servers that use 60 KW load, required very large and fully redundant Uninterruptible Power Supplies (UPS) and emergency generator systems to support the critical loads.
The facility has been certified LEED® Gold. The shell and core design were already well along when the Hospital’s High Performance computing group announced their intention to locate all of their high performance computing equipment into the new Data Centre.
SERVICES
Mechanical Engineering | Electrical Engineering | IT Communications Design | Lightining Design
PROJECT FEATURES
Size: 740,000 ft2 | Status: Completed 2013
LOCATION
Toronto, Ontario
KEY SCOPE ELEMENTS
Introduced innovative system solutions for urban-space saving, along with sophisticated computer systems | LEED Gold Certified
20 King St West, Toronto
Damage Investigation & Remediation
Following a hydro vault explosion and fire at 20 King Street West, HH Angus was engaged to provide consulting services for the subsequent investigation, restoration and rehabilitation of the base building core and shell.
20 King Street West is a 250,000 ft2 office building in Toronto’s downtown core. It consists of 15-storeys above grade, including the mezzanine, truss, upper truss and penthouse, as well as two levels below grade.
HH Angus completed a remediation and renewal of all mechanical and electrical components and major equipment that had been severely contaminated or damaged by the fire.
SERVICES
Mechanical Engineering | Electrical Engineering
PROJECT FEATURES
Size: 250,000 ft2 | Status: Ongoing
LOCATION
Toronto, Ontario
KEY SCOPE ELEMENTS
Consulting services for investigation, restoration and rehabilitation of base building core and shell | Remediation and renewal of all mechanical and electrical components and major equipment
Teknion
Tenant Office Fitout
HH Angus’ scope of work required that all design for this ultra modern Toronto office space and showroom target LEED®-CI Gold certification.
A key design challenge for our team was the client’s strong preference for clean ceilings. This meant the design had to minimize conduit runs, devices, etc. Underfloor systems were used in the engineering design to ensure the majority of the mechanical and electrical infrastructure was concealed. The mechanical distribution under the raised floor used Camino systems.
SERVICES
Mechanical Engineering | Electrical Engineering | Lighting Design
PROJECT FEATURES
Size: 10,750 ft2 | Status: Completed 2016
LOCATION
Toronto, Ontario
KEY SCOPE ELEMENTS
Tenant fitout | LEED-CI Gold Certified | WELL Certified Underfloor systems to conceal services | Statement lighting
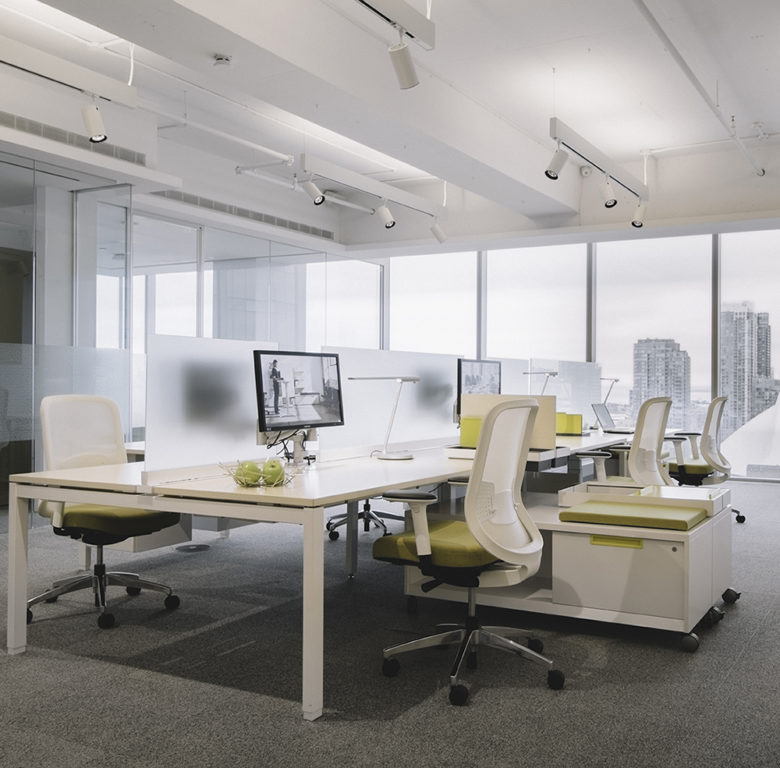
Site-specific design
Our design team was challenged in locating services and systems, given both raised floors and exposed ceilings. The ceilings featured suspended direct/indirect lighting throughout the space.
Statement lighting design
Speciality and decorative lighting played an important role in this project, from selection of fixtures and providing samples and budgets for client approval, to photometrics to meet showroom conditions.

All Seniors Care Living Centres
HH Angus is providing mechanical and electrical engineering and lighting design to greenfield sites in Kingston, Ontario. The seniors’ care facility feature 170 residential units, plus ground-floor amenities including pool, commercial kitchen, gym, and multi-use spaces.
HH Angus has both long standing and recent experience in the retirement and elder care sectors, including long-term care facilities, complex continuing care, dementia centres, seniors’ homes, hospices, and similar facilities that combine a healthcare setting with a residential component. Over the years, we have developed a sensitivity to the design nuances associated with these facilities.
Our scope includes complete design for the building systems, inclusive of generator site services within five feet of the building, plus complete plumbing and HVAC design.
The building has been classified B3 under the Ontario Building Code, an unusual ‘tall building’ designation for a building of this style and height. This OBC classification required additional ventilation options compared to those required for similar mid-rise apartment buildings.
Effective coordination between disciplines was paramount in order to achieve the high ceilings the client desired. We worked closely with the interior design team, structural engineers and architects in order to deliver this design feature for the client.
SERVICES
Mechanical Engineering | Electrical Engineering | Lighting Design
PROJECT FEATURES
Status: Completion 2020
LOCATION
Kingston, Ontario
KEY SCOPE ELEMENTS
Designed multi-storey long term care residential facility | B3 ‘tall building’ OBC classification | 170 residential units | Introduced multiple options for mechanical system together with estimated ROI
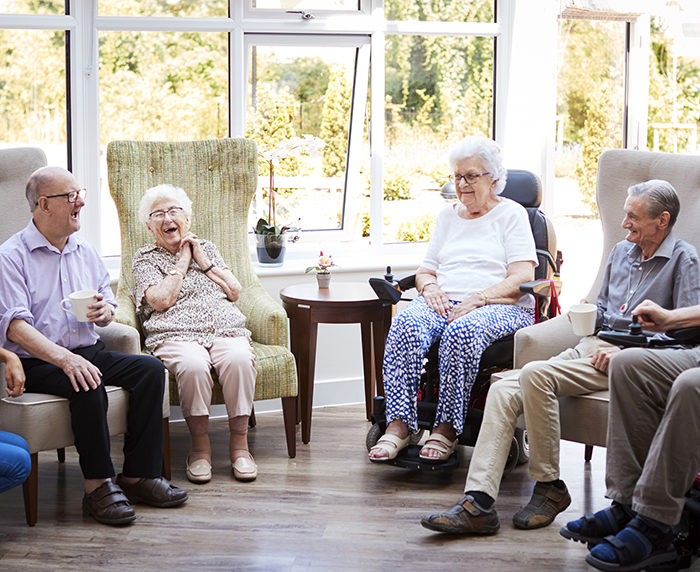
Sharing Expertise with Clients
HH Angus provided multiple options for the mechanical system, together with the estimated ROI for each, to assist the client in selecting the most appropriate equipment for this application.
We are also working with All Seniors Care on their new facility in Hamilton, Ontario.