Service: Mechanical Engineering
McMaster University
Trigeneration Plant
HH Angus was initially engaged to perform a Detailed Engineering Study to determine the viability of installing a natural gas-fired turbine for power and steam generation, and the use of absorption cooling to balance out steam production in the warmer months.
For a full year, we reviewed heating, cooling and electrical power loading at McMaster University. We also reviewed operating costs covering maintenance, operating and natural gas costs, and completed a sensitivity analysis of gas and power pricing variances. Capital and Operating budgets were also prepared to determine ROI on the proposed investment.
Following the Detailed Engineering Study, we were engaged to design the new trigeneration plant using a gas turbine (5.4 MW) coupled with an HRSG (Heat Recovery Steam Generator), natural gas compressor, absorption chiller (1000 tons) and centrifugal chiller (2500 tons). The plant was installed in the existing central utility plant room, and significant demolition of redundant equipment was undertaken to generate the space for this system upgrade.
There were a number of interesting challenges associated with the work:
- Selective demolition of two existing steam boilers, two existing incinerators and one 5,000 ton electric centrifugal chiller including isolation of services and asbestos abatement to not impact existing plant operations
- Fitting this large equipment into an area with significant space constraints
- Creating a path of ingress for the equipment from outside into the sub-grade basement level of the plant for installation during winter months where the weather would be unpredictable
- Minimizing the impact on daily operations within the plant during the demolition and construction phases.
- Integration and coordination with a switchgear replacement project running in parallel with the cogeneration project
- Targeting a completion date of October, 2017 to ensure the client would receive full IESO funding for the project
Some of our solutions included:
- Thorough surveys of existing equipment and services to ensure the equipment slated for demolition could be isolated from the operating plant with minimal to no service interruption
- Engaging with equipment suppliers at an early date to ensure required footprints were allocated
- Coordinating with the structural engineers to design a removable roof cap that could be installed prior to the existing roof being cut open to allow equipment installation
- On-going coordination with plant staff during the design phase to get buy-in of any modifications required to the existing plant
- Pre-tendering long lead item equipment to ensure on-site delivery dates would meet the construction schedule
By designing to eliminate potential interferences or issues with installation, we were able to meet the delivery targets and deliver a successful project.
SERVICES
Prime Consultant | Mechanical Engineering | Electrical Engineering
PROJECT FEATURES
Status: Completed 2017
LOCATION
Hamilton, Ontario
KEY SCOPE ELEMENTS
Year-long detailed engineering study | Reviewed heating, cooling and electrical power loading | Study included sensitive analysis of gas and power pricing variances | Introduced new design for trigeneration plant usage, a gas turbine (5.4MW) coupled with an HRSG, natural gas compressor, absorbtion chiller and centrifugal chiller
Durham Region Transit
Oshawa Bus Maintenance Facility
Durham Region needed to accommodate the repair/maintenance requirements of its fleet of buses with a facility that would be integrated into an existing building. The project is on track for LEED® Silver Certification.
The project features a state-of-the-art Transit Control Centre on the second floor for regional bus and GTAA connection communications. Highlights include state-of-the-art ventilation and exhaust systems, fuel/fluid dispensing, a vacuum cleaning system, parts dispensing, tire storage/ servicing, lubrication stations, paint booths and a bus wash station. The mechanical design scope included plumbing, fire protection, HVAC, controls and process systems and services. The building was designed to reduce energy and water demand and includes for rainwater storage facilities.
The electrical scope included normal and emergency power systems, fire alarm, state-of-the-art LED lighting and integrated IT System (incorporating time management, clock system, Presto system, communication systems and various radio systems). Durham Region building standards also required design of a lightning protection scheme.
SERVICES
Mechanical Engineering | Electrical Engineering | IT | Security and Communications Design | Lighting Design
PROJECT FEATURES
Size: 60,000 ft2 - 5500 m2 | Status: Completed 2016
LOCATION
Oshawa, Ontario
KEY SCOPE ELEMENTS
State of the art ventilation and exhaust | Controls & process systems and services | Additional design for lighting protection scheme | Energy use reduction strategies | Rainwater storage | Designed to achieve LEED Silver
Queen’s University
Richardson Stadium Revitalization
HH Angus has a long and valuable relationship with Queen’s University, covering numerous projects across a range of buildings and services at the campus, including new build, renovations, expansions and district energy scopes of service.
In 2014, Queen’s began a revitalization of its premier sports facility, Richardson Stadium, and engaged HH Angus to provide mechanical and electrical engineering to the Revitalization project.
Our scope of work included mechanical and electrical design for the new East Building and renovated West Building; and electrical power design for the East and West Buildings, plus field lighting.
The Stadium work was executed in two phases: Phase One was the Feasibility Study and Phase Two covered the project implementation. To launch Phase One, system options and minimal requirements were confirmed with the University’s Facilities team in Kingston. There was also a series of meetings with the Construction Manager and primary trades to confirm the basis of the original estimates and to discuss the impact of system options.
Phase Two incorporated a value engineering exercise to develop alternative project phasing plans to maintain the budget. A final mechanical and electrical Schematic Design report was prepared following the value engineering exercise. Under Phase Two, HH Angus was retained to carry the project through from Design Development to Construction Administration.
SERVICES
Mechanical Engineering | Electrical Engineering
PROJECT FEATURES
Status: Completed 2016
LOCATION
Kingston, Ontario
KEY SCOPE ELEMENTS
Electrical power design & field lighting for East and West buildings | Work executed in two phases, Feasibility Study (Phase 1) and Project Implementation (Phase 2)
Penguin Random House
Tenant Fit-out
One of the key challenges of this project was meeting a very aggressive renovation/fitout schedule. The client’s lease was expiring at their existing location, which meant we had to meet a pre-determined target in order to achieve their move-in date for their new facility at 320 Front Street.
This high-end office space totals 45,000 ft2 and occupies 2 ½ floors.
HH Angus’ lighting design included the selection of special fixtures. Our design considerations covered both dropped and decorative ceilings, as well as LEDs in shelving units, along with upgraded lighting controls.
We also designed a new mechanical cooling loop for a large IT room, as well as multiple UPSs.
SERVICES
Mechanical Engineering | Electrical Engineering | Lighting Design | Communications Design
PROJECT FEATURES
Size: 45,000 ft2 over 2 1/2 floors | Status: Completed: 2015
LOCATION
Toronto, Ontario
KEY SCOPE ELEMENTS
Lighting design considerations included dropped and decorative ceilings | Upgraded lighting controls | Added a new mechanical cooling loop for a large IT room and multiple UPS
Tyndale University College & Seminary
Mother House Renovations
This project centred on the renovation of an existing structure that dated from the late 1950s for new occupancy. The building was formerly home to a Catholic nunnery. Vatican approval was required to transfer the campus from Catholic to Protestant hands, and a key reason for the approval was Tyndale’s commitment to continue to protect the nunnery’s aesthetically significant chapel as “sacred space”.
HH Angus’ scope for this project included upgrades to major mechanical and electrical infrastructure, addition of a fire protection system, and life safety system upgrades. Existing vertical transportation systems were upgraded to meet current standards.
Upgrades to the mechanical infrastructure systems were designed to accommodate future capacity increases, and are expandable to suit planned renovations and additions in other areas of the building.
A chiller replacement was required as the first stage of the renovation. This was necessary due to the phase out of R-11 refrigerant, as well as the chiller being at life cycle end. The replacement was fast-tracked and equipment pre-purchased in order to meet the schedule.
The chilled water plant was provided with an optimization control package and integrated with cooling tower and circulating pumps variable speed drives for improved operational efficiency.
Among the challenges of this project was a short construction schedule. Access to the site was very limited, due to presence of occupants, which limited survey work. As well, the budget was firmly set, so creative solutions were required to ensure that the building would be ready for occupancy when the academic year began. These solutions included:
- Hybrid heating system utilizing existing steam and hot water generation
- Temporary power to permit continued occupancy during construction
- Pre-tendering all long lead components
- Phasing planning and upfront design for future building expansion and renovation
SERVICES
Mechanical Engineering | Electrical Engineering | Vertical Transportation Consultant
PROJECT FEATURES
Size: Mother House: approx. 286,540 ft2; Tyndale High School: approx. 83,680 ft2 | Status: Completed 2015
LOCATION
Toronto, Ontario
KEY SCOPE ELEMENTS
Upgrades to major mechanical and electrical infrastructure | Addition of fire protection (sprinkler) system & life safety system upgrades
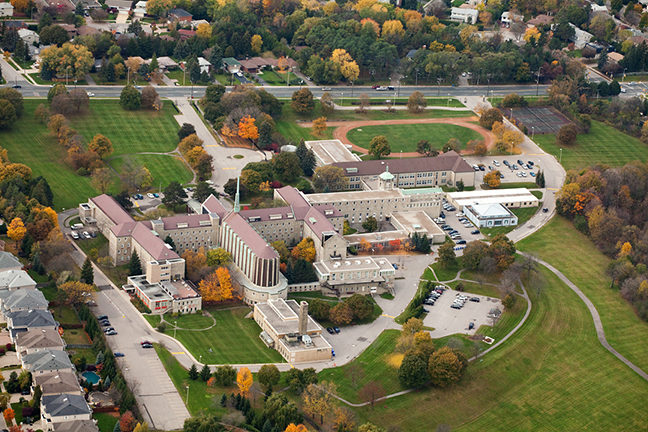
Ensuring continued operations
The Administration wing of building remained occupied and fully operational during construction.
Rebate application assistance
HH Angus applied for incentives with Toronto Hydro on the Owner’s behalf. The project was eligible for a rebate from the Save-ON-Energy program.
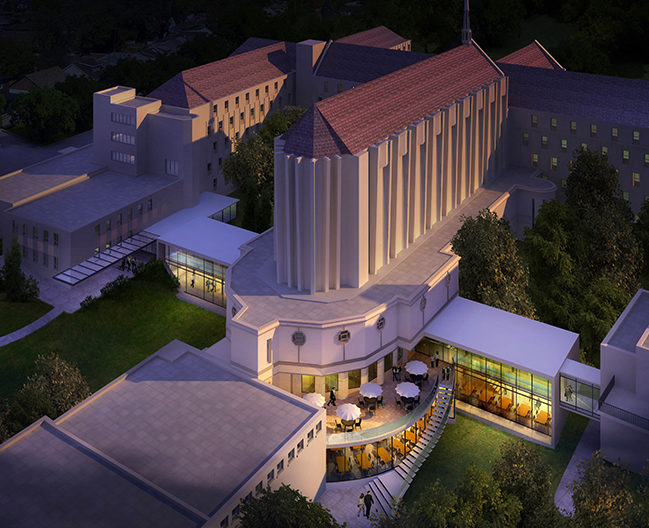
— Photos courtesy of CS&P Architects