Service: Mechanical Engineering
University Health Network
Toronto General Hospital Rapid Assessment Centre (RAC) Expansion
HH Angus was engaged to provide mechanical and electrical engineering, IMIT consulting, and lighting consulting services for this 20,000 ft2 phased renovation at Toronto General Hospital. The space now includes a Rapid Assessment Centre, Diagnostic Test Centre, and Admitting and Pre-Admission Clinics.
The emergency department (ED) was designed to serve ~ 20,000 patients annually but was receiving more than 55,000 patients To better manage these volumes, a dedicated Rapid Assessment Centre (RAC) was added so that ED staff can triage lower acuity patients to the new "fast track" area, enabling primary emergency areas to care for more complex patients. Our team worked in conjunction with the client and other consultants to perform a pre-tender constructability review. This review included potential approaches to minimize disruption outside areas of construction, identify potential installation challenges, and complete pre-demolition of the first phase of work to identify any unknown site conditions in advance of construction. Due to the age of the existing space, there was a high probability of building systems and equipment being beyond their service life, and a certainty that codes and standards relevant to the design of the new space had changed. To address this and mitigate any risks, HH Angus performed a pre-design review to identify any specific potential issues with the new space and recommend steps to further address the unknowns. Scanning and 3D captures were performed regularly throughout construction, using Matterport Pro 2 and a Theta V 360 Camera. This provided the client with regular site progress updates and, in future, will allow for dimensionally accurate references for locating MEP services behind walls and ceilings. It also allowed for a more focused presence on-site, as construction progress was made available remotely to a range of project stakeholders amid COVID-19 pandemic restrictions. The existing ventilation systems presented a significant gap for the project, as their capacity to support the new functions of the space was unknown. To address this, HH Angus investigated and presented several options for review, taking into consideration the client’s budget, schedule, and planned upgrades for existing infrastructure.
|
SERVICES
Mechanical Engineering | Electrical Engineering | IMIT Consultant | Lighting Consultant
PROJECT FEATURES
Accelerated project schedule | Status: Completed 2022
LOCATION
Toronto, Ontario
KEY SCOPE ELEMENTS
Phased renovation | Pre-tender constructability review and pre-design review | Scanning and 3D captures to document site progress and provide dimensionally accurate site references for future access
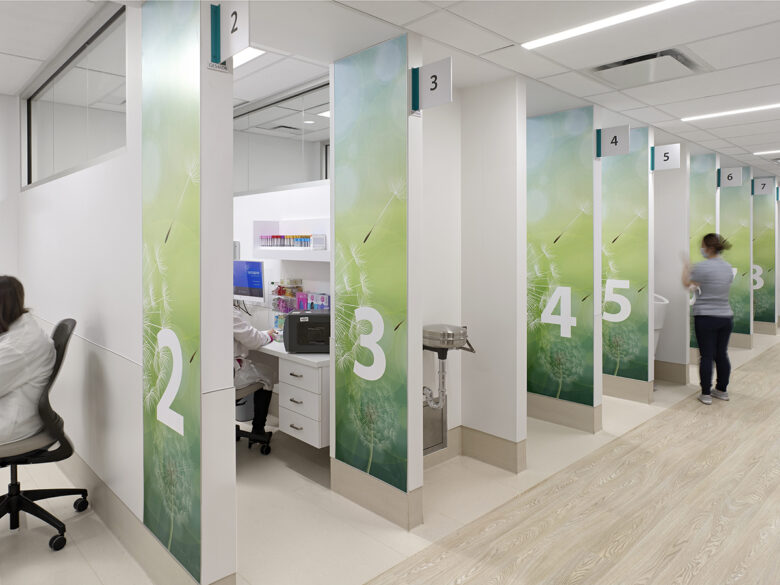
Accelerated schedule
The project schedule was aggressive, requiring close and efficient collaboration between HH Angus, the client, and all other consultants. All construction documents and constructability reviews were completed in 12 weeks.
Queen Elizabeth II Health Sciences Centre
Bayers Lake Community Outpatient Centre
The Outpatient Centre is part of the $2-billion redevelopment of the QEII Health Sciences Centre. The EllisDon Infrastructure Healthcare consortium led the P3 project. The Outpatient Centre was honoured as a Gold Winner by the 2024 Urban Design & Architecture Awards for its innovation and design excellence, and has also been certified LEED Gold under the LEEDv4 Healthcare rating system.
The Bayers Lake Community Outpatient Centre in Halifax was built as Nova Scotia’s first public-private partnership (P3) healthcare project and is its largest healthcare project to date. Its LEEDv4 Gold certification is the first in Nova Scotia and one of only approximately 50 facilities in the Canadian hospital sector to attain this status. Sustainability features include a stormwater retention pond to capture and filter 100% of rainfall, and an energy-efficient design that reduces energy consumption by 39%.
The Centre provides a range of patient services that do not require a hospital setting, including initial visits with specialists, post-surgery and post-treatment follow-up, blood collection, eye care clinic, physio and occupational therapy, diabetes and orthopedic assessments, rehabilitation services, 17 examination rooms, 24 dialysis stations, and diagnostic imaging (x-rays and ultrasounds). The Centre expects 28,000 clinic visits, and 30,000 x-ray and blood collection visits every year.
HH Angus provided mechanical consulting engineering to the project, which was completed on time and on budget. Kim Spencer, Director of HH Angus’ Healthcare Division, commented that “we were very pleased to be able to support this new facility with HH Angus’ deep experience in the P3 delivery model, and proven track record of thoughtful healthcare design.” HH Angus acted as the prime mechanical consultant, in affiliation with Dillon Consulting, a local sub-consultant. Our mechanical scope of work included HVAC design, with support from Dillon on plumbing and fire protection.
SERVICES
Mechanical Engineering
PROJECT FEATURES
P3 | 134,000 ft2 | 15-acre site | Part of a $2 billion redevelopment | Completed November 2023 | Gold Winner, 2024 Urban Design & Architecture Awards | LEEDv4 Gold certified
LOCATION
Eastern Canada
KEY SCOPE ELEMENTS
Prime mechanical consultant | HVAC | Fire protection | Plumbing design
Lonsdale Energy Corporation
Heat Recovery Feasibility Study
HH Angus conducted a study to evaluate the feasibility of exhaust air heat recovery from the Global Relay (GR) data centre facility at 22 Gostick Place in North Vancouver, BC.
Some of the key aspects of the study included:
- The location and footprint of the heat recovery system components were studied within the context of considerable site constraints. The study evaluated the design, construction, and cost considerations for the implementation of the proposed heat recovery system.
- We investigated available heat pump technologies that would be appropriate for recovering waste heat and would satisfy the LEC DES requirements.
- The energy recovered would be used by a water source heat pump to provide hot water to the local LEC District Energy System (DES).
- A water source heat pump system was proposed as the best solution to provide the ability to recover heat from the building ventilation system. The new system would recover heat from the GR facility and would transfer this recovered heat via a hot water loop to the local LEC DES.
- Heat recovery is feasible for the facility and can provide up to 1,100 kW of heating capacity to the LEC DES.
- Constraints to the design of the heat recovery system were also identified, and included:
(i) the quantity of air exhausted from the facility is not fixed and ranges at each exhaust plenum on a seasonal basis and depending on outdoor air temperature – this impacts how much heat can be recovered at a given time;
(ii) the minimum and maximum exhaust air temperatures range from 30°C to 43°C (86°F to 110°F) - the temperature of the exhaust air will influence how much heat can be recovered from the exhaust air; and,
(iii) the cross-sectional area available for the heat recovery coil - the more cross-sectional area that is available for a given amount of heat transfer, the less deep the coil must be (and less airside pressure drop penalty is incurred).
The study concluded that a purpose-built containerized heat pump system would be the most suitable solution to meet the needs of the project. This new containerized structure would be conveniently located adjacent to the GR facility and would exhibit the same architectural character as the existing facility. The proposed heat pump system would include one heat pump unit (based on Emerson Heat Pumps) and four heat recovery water pumps. Control valves, piping accessories, ventilation, lighting, and system controls would all be included in the proposed pre-fabricated containerized enclosure.
Outdoor hydronic piping would connect the heat pump enclosure to the GR facility and the proposed hydronic heat recovery coil system. The heat recovery coil system would consist of four new heat recovery coils placed within the existing facility exhaust air plenums. The existing exhaust fan motors would have to be upgraded in order to address the additional pressure drop introduced by the new heat recovery coils. This fan motor upgrade would also trigger upgrades to the existing electrical infrastructure.
SERVICES
Prime Consultant | Mechanical Engineering | Electrical Engineering
PROJECT FEATURES
Size: 5,600,000 ft2 | Status: Ongoing
LOCATION
Vancouver, British Columbia
KEY SCOPE ELEMENTS
Feasibility study | Heat recovery
Ministry of the Solicitor General | Infrastructure Ontario
Thunder Bay Correctional Complex (TBCC)
The TBCC involves replacement of aging jail and correctional facilities with a new 345-bed, multipurpose complex. Both the existing Thunder Bay Jail and Thunder Bay Correctional Facility are among the oldest provincially-run adult correctional facilities, built in 1928 and 1965 respectively.
The new TBCC updates automation and technology to address issues of health, safety and security, and introduces efficiencies around design, technology, and the use of space. HH Angus is providing mechanical consulting engineering and vertical transportation consulting to the EllisDon Infrastructure Justice design team.
The TBCC is targeting LEED Silver certification and LEED Resilient Design pilot credits through the United States Green Building Council. The design focuses on energy efficiency, healthy indoor environments and reduced greenhouse gas emissions. The complex will also include views of nature, allow ample natural light and feature dedicated Indigenous cultural spaces, such as smudging space and sweat and teaching lodges.
The new facility is the first of its kind for an Ontario correctional facility, incorporating design features that promote rehabilitation of inmates. It will also improve access to programming, living conditions and education, while updating automation and technology.
The TBCC project has presented several challenges to our design team, including a compressed schedule and the involvement of numerous stakeholders. It has also been interesting on a technical level: mechanically, the various modes of operation and interconnection of systems are quite complex, necessitating a high degree of flexibility within the capacity of the mechanical equipment. The building construction featured a precast exterior with block walls, requiring very close coordination with trades to align openings and allow access for equipment.
Due to the secure nature of the facility, the mechanical system was integrated seamlessly into the architectural features, all accessible equipment is provided in a secure location, and all building systems interact
with the BAS.
The facility will include a connection to an existing 50-inmate facility — the Thunder Bay Modular Built Facility — located southeast of the TBCC and currently under construction. The project also involves the design and construction of a 4,000 ft2 wastewater treatment facility to allow for a fully self-sufficient and self-contained facility.
SERVICES
Mechanical Engineering | Vertical Transportation
PROJECT FEATURES
$1.2 billion | 345-bed, multipurpose facility | 450,000 ft2 | Completion expected in 2026
LOCATION
Eastern Canada
KEY SCOPE ELEMENT
Design required careful consideration of all inmate-accessible areas | Compressed schedule | Close collaboration with trades to ensure pre-cast exterior elements align accurately with equipment access openings
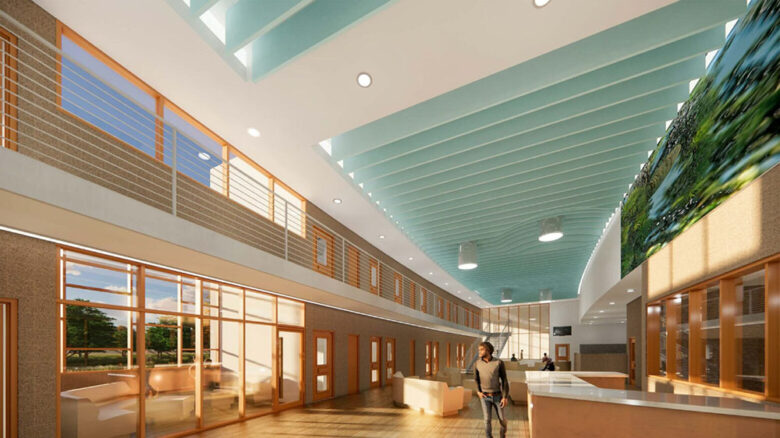
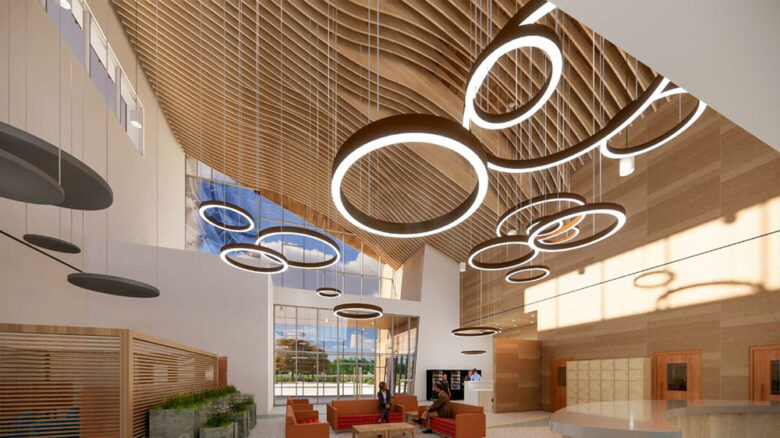
Images courtesy of Zeidler Architecture
Niagara Health System | Infrastructure Ontario
New South Niagara Hospital
New South Niagara Hospital is targeting LEED Silver certification and is being designed to be Canada’s first WELL-certified healthcare facility. The project was recently nominated for two CCPPP awards for excellence in public-private partnerships.
HH Angus is part of the design team under EllisDon Infrastructure Healthcare, the proponent to design, build, finance and maintain the new South Niagara Health Hospital project. The EllisDon Infrastructure Healthcare team includes:
- Leads: EllisDon Capital Inc. & Plenary Americas LP
- Design Team: Parkin Architects Ltd. & Adamson Associates Architects
- Construction Team: EllisDon Corporation
- Financial Advisor: EllisDon Capital Inc.
HH Angus is providing consulting services for conveyance systems (automated guided vehicles, autonomous mobile robots, and vertical transportation) and mechanical engineering as part of the design team. Of special note, we have designed the building’s mechanical HVAC systems to accommodate Indigenous ceremonies taking place not just in a few designated spaces, but throughout the patient care tower, so that patients do not have to be moved in order to take part in healing ceremonies.
The new facility will be a full acute care hospital with 24/7 Emergency Department, diagnostic, therapeutic, and surgical services. The latter will include medical, surgical, and intensive care inpatient beds. Also included will be ambulatory services; post-acute Complex Continuing Care (CCC) Inpatient services; and Centres of Excellence specializing in stroke, complex care, geriatric/psychogeriatrics, and wellness in aging.
The new hospital will integrate technology that supports innovation in and delivery of high-quality healthcare and will be designed to achieve LEED Silver certification. The design will also work toward being the first WELL™-certified healthcare facility in Canada.
Image courtesy of EllisDon Infrastructure Healthcare
SERVICES
Mechanical Engineering | Conveyance Systems Consulting (AGVs, AMRs and Vertical Transportation)
PROJECT FEATURES
Completion: Estimated for 2028 | Full acute care hospital | Targeting LEED Silver and WELL Certifications
LOCATION
Eastern Canada
KEY SCOPE ELEMENTS
~1.2 million ft2 | 469 beds, 8 ORs, 42 hemodialysis stations, 2 MRIs | AGV, AMR and VT planning and design | Mechanical engineering