Service: P3/Design Build/IPD
TD Bank Group
Project Lego, 77 Bloor Street West
Project LEGO* was a 225,600 ft2 renovation in a Class A downtown Toronto tower, and was delivered through a full Integrated Project Delivery (IPD) contract.
The project was heavily phased, as the scope covered twelve floors with, initially, only a single floor of swing space available.
A fully collaborative effort from all team members saw a 10% reduction in total project costs, which achieved the owner’s project goals and resulted in greater savings against an already-reduced target cost.
HH Angus worked closely with the mechanical subcontractor during the intensive schematic design phase to agree on design principles and installation elements and, in the process, reduced the mechanical build costs by 20%. These savings could be realized through a good collaboration with the TD Bank client, who was able to adjust and alter its accepted design standards during the validation process. The collaboration also helped the overall project achieve some aspirational goals that were initially considered as ‘nice to have’.
The IPD process of teaming with multiple user groups was very collaborative and worked well to identify solutions to issues. In the end, the team was successful in meeting the schedule and coming in under budget, which enabled the owner to fund added scope within the project and enhance the overall customer experience for their user groups.
IPD Partners in Project LEGO included: TD Bank - Owner | EllisDon - General Contractor | BGIS - Project Manager| HOK - Architect | HH Angus - Mechanical Engineering | Mulvey & Banani - Electrical Engineering | Modern Niagara - Mechanical Contractor | Symtech - Electrical Contractor | Teknion - Furniture Vendor.
* No actual LEGO® was involved in this project!
SERVICES
Mechanical Engineering
PROJECT FEATURES
Size: 225,600 ft2 | Status: Completed 2015
LOCATION
Toronto, Ontario
KEY SCOPE ELEMENTS
Twelve floors with only a single floor of swing space available | Integrated Project Delivery contract with nine-party team | Interior retrofit | Reduced mechanical build cost by 20%
North Bay Regional Health Centre
The first LEED® registered healthcare facility in Canada, North Bay Regional Health Centre was built on a greenfield site and replaced two general hospitals and a separate mental health facility. HH Angus provided mechanical, electrical, vertical transportation, specialty lighting and communications design consulting engineering for the project.
The gross building area is 725,000 ft2. The facility includes the full range of departments normally found in a regional acute-care, 275-bed hospital, plus a new facility for the Northeast Mental Health Centre. The mental health portion is significant, consisting of 150,000 ft2 and 113 beds, and also includes a significant forensic component.
Using a completely innovative approach, our staff developed 100% outdoor air systems with total enthalpy heat recovery wheels, the first time this system had been implemented in North America. A major advantage of this system is that there is no re-circulated air, which greatly reduces the possibility of infection transmission for patients, staff and visitors. As well, delivering 100% fresh air rather than re-circulated air reduced the need for as many air changes in patient rooms as had previously been the norm. And that change meant that smaller fans and less ductwork were possible, resulting in lower capital cost.
As a value added service, HH Angus constructed a mock patient room to verify airflow patterns for the air distribution system. This ensured that the design was flawless. In addition, reducing air volumes to patient rooms to four changes per hour resulted in changes in the CSA standard.
The project also included:
- Planned future remote cogeneration plant
- High efficiency central heating plant with hot water and steam boilers
- Centrifugal chillers supplemented with a 24/7 chilled water system
- Radiant ceiling panels for perimeter heating
- Enhanced building envelope to achieve energy performance
- Bi-fuel emergency generators with provision for dispatch lighting
- LED lighting
SERVICES
Mechanical Engineering | Electrical Engineering | Communications Design | Lighting Design | Vertical Transportation Consulting
PROJECT FEATURES
Size: 725,000 ft2 | The first modified Alternate Finance Partnership (AFP) in Ontario | Status: Completed 2010
LOCATION North Bay, Ontario
KEY SCOPE ELEMENTS
Greenfield hospital with new mental health centre | A North American first: 100% outdoor air supply with high efficiency total enthalpy heat recovery wheels throughout the hospital, resulting in reduced risk of infection and lower capital costs | One of Canada's first LEED® registered facilities
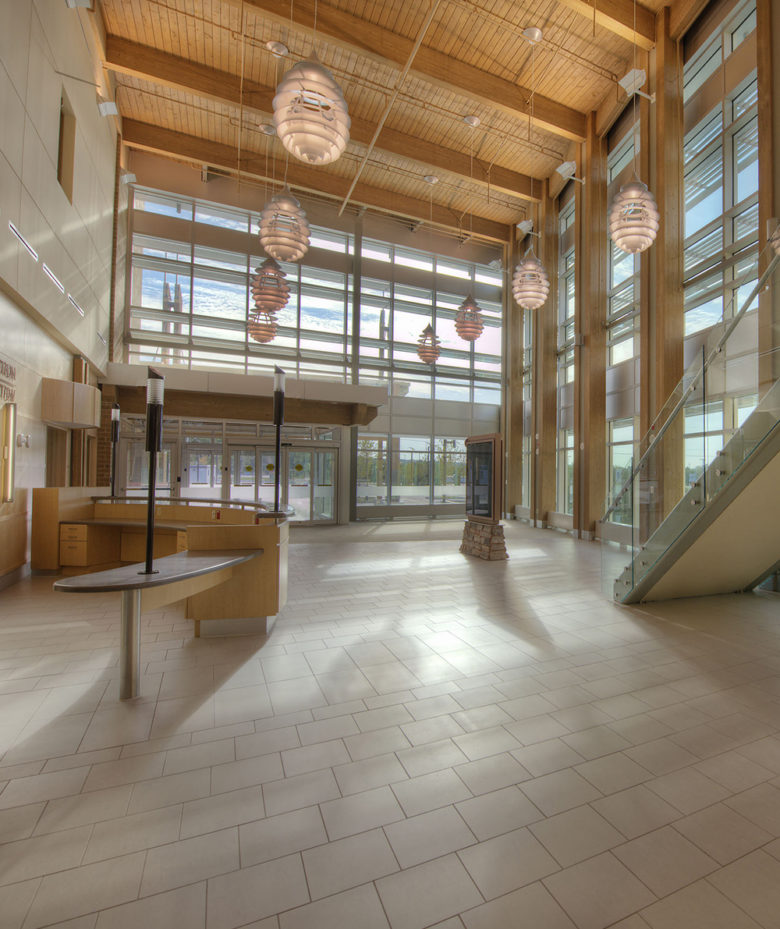
Custom electrical design
Specialized electrical systems features for the project included a centralized uninterrupted power system and an integrated communications systems platform used for all building operations and healthcare applications.
One of Canada’s first LEED® registered facilities
The main challenge with the design of this facility was performing energy modeling for LEED®. HH Angus’ design team included LEED® Accredited Professionals qualified to carry out a project that met LEED® standards for creation of an energy-efficient building.
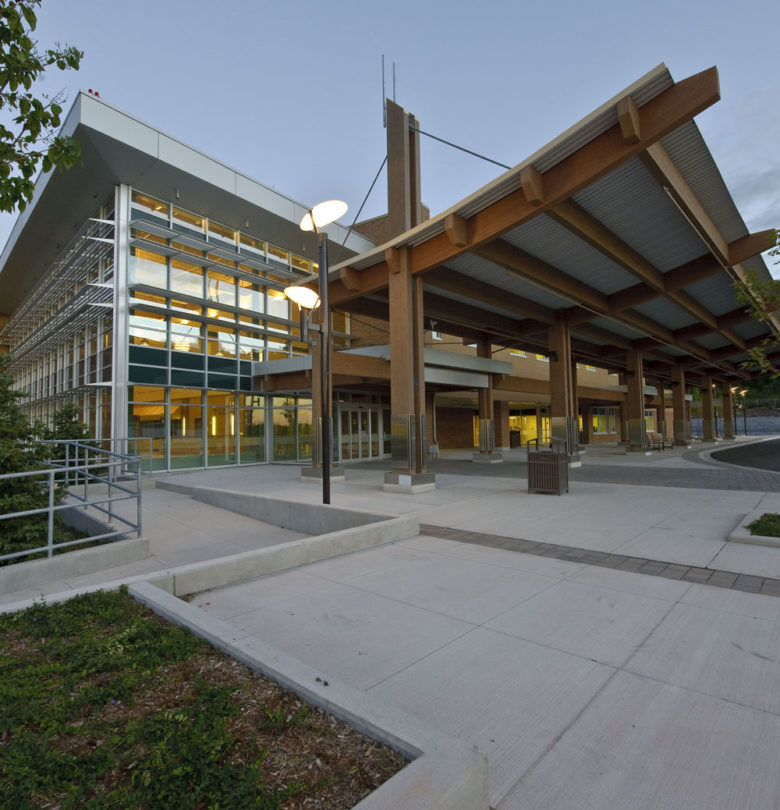

— Image courtesy of Evans Bertrand Hill Wheeler Architecture Inc.
Royal Jubilee Hospital
Patient Care Centre
HH Angus provided consulting engineering for all mechanical, electrical, vertical transportation, IMIT and commissioning services for this state-of-the-art 400,000 ft2, 500-bed acute care and psychiatric facility. The facility was certified LEED® Gold, delivering a high performance building that is both sustainable and green. Innovations include rainwater harvesting, 100% fresh air with heat recovery and user-controlled environment.
Most floors in the 8-storey building have a common floor plan, each accommodating two units of 36 beds. Eighty-three are psychiatric beds designed to be converted to acute care if required. The building also includes a highly secure forensic assessment unit. Our vertical transportation work included four passenger elevators and six service elevators.
The site features a smudging room, the ‘All Nations Healing Room’. Mechanically, the room was designed with a dedicated exhaust system to extract smoke and odours during Sweet Grass and Smudging ceremonies, in addition to regular room ventilation.
Working with the rest of the design/build team, HH Angus evaluated the existing central heating plant, determining it was feasible to entirely delete an anticipated boiler/chiller plant. This significantly reduced plant size and cost while improving site-wide energy efficiencies, operating flexibility and redundancy provisions. Lighting installations included the latest LED technology, with excellent results.
IMIT
The Patient Care Centre was British Columbia’s first truly digital hospital. With end-to-end IP-based network infrastructure, caregivers and patients are connected more reliably and securely than had previously been possible. Our design included real-time patient and equipment tracking, auto call up of patient records when staff enter a patient room, and integration of patient records onto TV sets...just some of the digital advances in patient care.
The communications systems feature reliable operation, flexibility, quality of service, convenience, and efficiency of operations. A broad variety of communications, monitoring and computer systems have been installed; for example:
- An intelligent wireless system provides support for wireless applications inside the facility and are strategically positioned to provide full coverage. To ensure reliability and uniform coverage to the entire facility, the Intelligent Wireless Access Points automatically adjust RF signal levels. The system provides full roaming.
- A wireless network infrastructure supports numerous security schemes simultaneously. Data Encryption, Secure Mobility Device and User Authentication are supported, keeping traffic private in a mobile environment.
- The security systems utilize a fully Integrated Multimedia Security Management System (IMSMS), providing a scalable, open architecture, client server-based security management solution, ideal for healthcare facilities. The Security Management System integrates the CCTV, Access Control, Intrusion Detection, Panic/Staff duress, Patient Wandering and Incident Reporting System. The IMSMS workstations allow security personnel to monitor and control all security sub-systems from a single user interface.
SERVICES
Mechanical Engineering | Electrical Engineering | Security Design | IMIT Engineering | Vertical Transportation Consulting | Lighting Design
PROJECT FEATURES
Size: 400,000 ft2 | Status: Completed 2010
LOCATION
Victoria, British Columbia
KEY SCOPE ELEMENTS
BC’s first digital hospital with end-to-end IP-based network infrastructure | Smudging room with dedicated exhaust system | Rainwater harvesting | LEED® Gold Certified | 4 passenger and 6 service elevators | Met aggressive schedule for concurrent design and construction
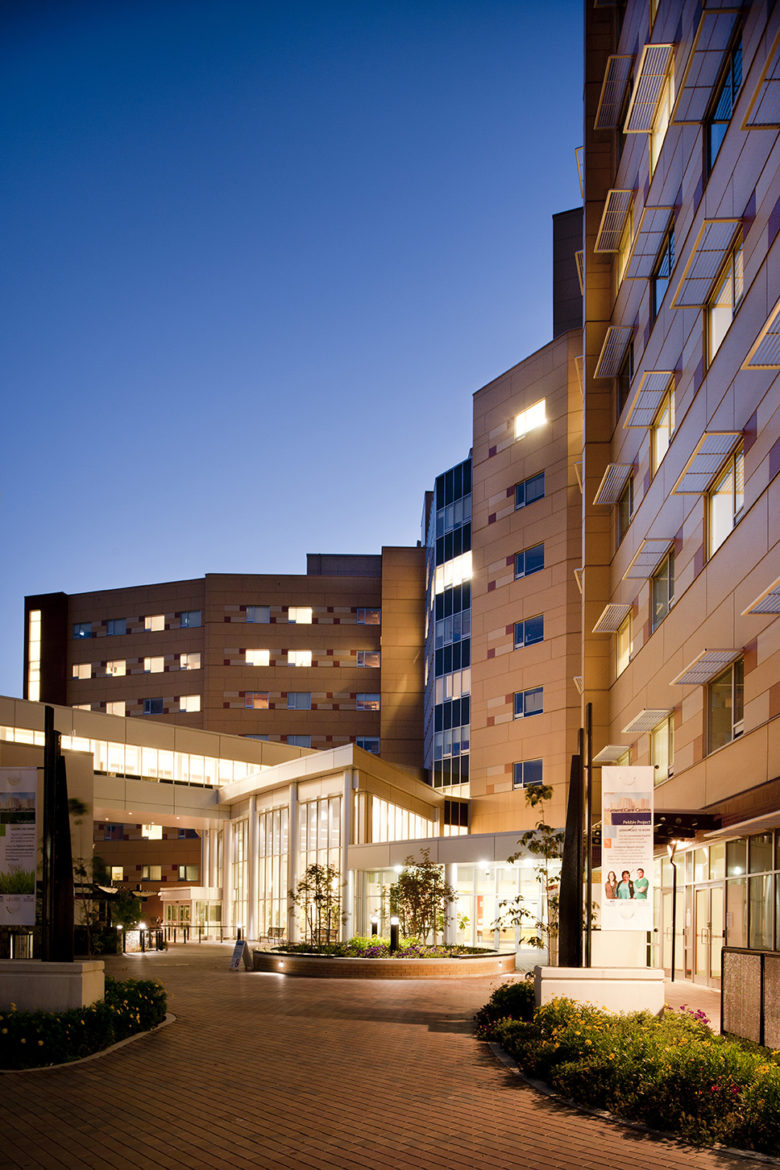
Working to tight timelines
This P3 project had an aggressive schedule for concurrent design and construction, calling on HH Angus’ project management expertise to achieve all milestones and deliver the industry-leading facility to Royal Jubilee Hospital on time and within budget.
Commissioning
HH Angus also provided Commissioning Authority oversight. The commissioning plan is in accordance with the CSA Standard Z318.0-05 – Commissioning of Health Care Facilities.
HH Angus developed and helped to administer the Mechanical and Electrical Commissioning plan for MEP with partner firm HWT. The combined team provided stringent third party commissioning and testing services, including a well-defined equipment start-up procedure, verification of physical installation to general conformance with contract documents, and validation of system performance.
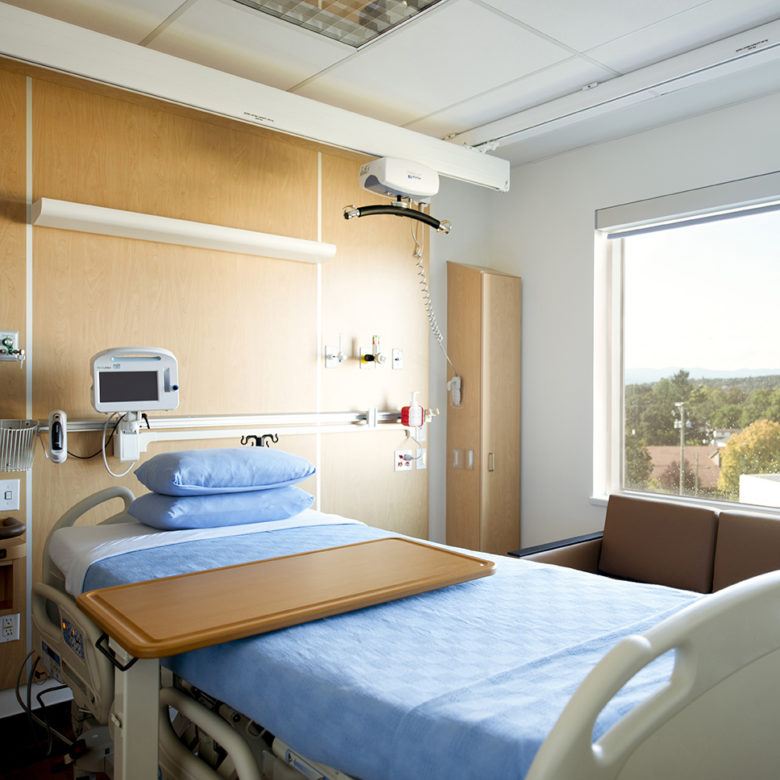
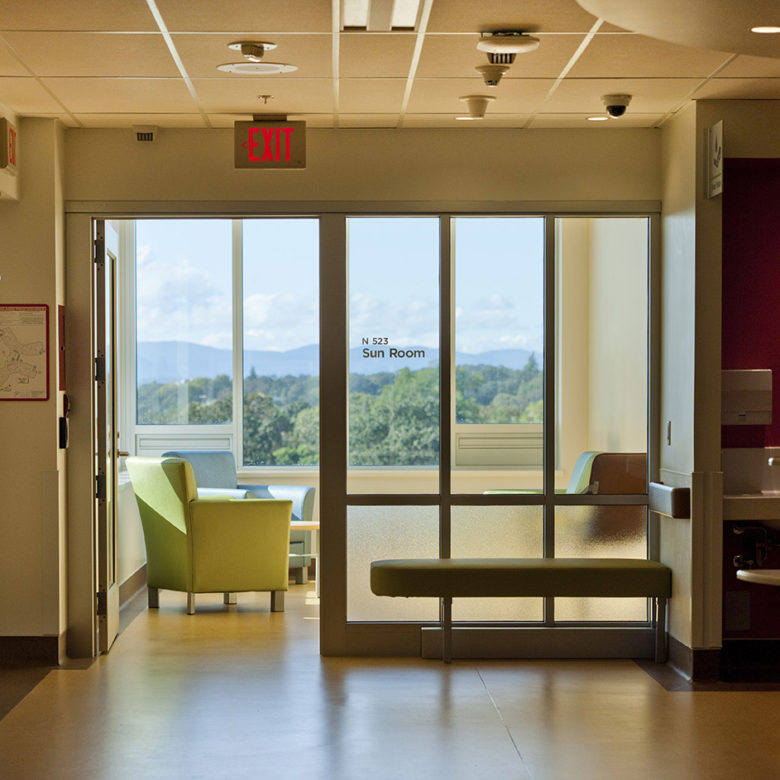
Training operations staff
HH Angus developed comprehensive System Operating Manuals (SOMs) for each system and provided enhanced training to building operators on both equipment and the integrated systems, in order to reduce learning-curve time and minimize life cycle cost of the installation.
Alberta Infrastructure
Calgary Courts Centre
Calgary Courts Centre is a major courthouse complex designed to accommodate both the Court of Queen’s Bench and Provincial Court. The complex consists of a 24-storey tower and a 20-storey tower, totalling 1 million ft2 in downtown Calgary.
The two towers are connected by a 26-storey glass atrium with catwalk bridges. The complex hosts 73 courtrooms, judicial chambers, and facilities for security, government, library and external agencies staff.
Rising approximately 125 metres, the structure was designed to be one of Calgary’s premier office buildings. The vertical transportation system includes 25 elevators and 8 escalators. From the public’s perspective, there are a total of 12 gearless traction elevators split into two banks of six elevators, in a low rise and high rise configuration. In addition to the Atrium elevators, the public uses eight atrium escalators to facilitate movement through the first five building levels which have high traffic flows.
Judiciary transportation
For the judiciary, a total of four gearless traction elevators (two per tower) serve all building levels (except the mechanical floor), including sub-basement levels. Given the secure nature of these units, provisions were incorporated to accommodate CCTV cameras, security card readers and remote monitoring and control.
Prisoner transportation
For prisoner movement, six elevators are provided, two of which are large capacity (4300 kg), special purpose units, sized to accommodate up to 15 prisoners plus associated guards. These oversized units serve between the sally-port and holding cell level.
For the prisoner elevators, special features included “Touch Screen” operation allowing the elevators to be sent to various floors from a remote location, without involvement from the guard.
General elevator transportation
For material handling functions, both towers are provided with a single 2270 kg capacity, gearless traction, “hospital” style elevator. A single staff parking shuttle is also provided to access the secure parking on the two lowest sub-grade levels.
SERVICES
Vertical Transportation Consultants
PROJECT FEATURES
Status: Completed 2008
LOCATION
Calgary, Alberta
KEY SCOPE ELEMENTS
25 elevators and 8 escalators along with 4 gearless traction elevators | Incorporated special features such as CCTV cameras, card readers and remote monitoring and control | Prisoner-level cars including touch screen operation allowing them to be sent remotely without guard involvement
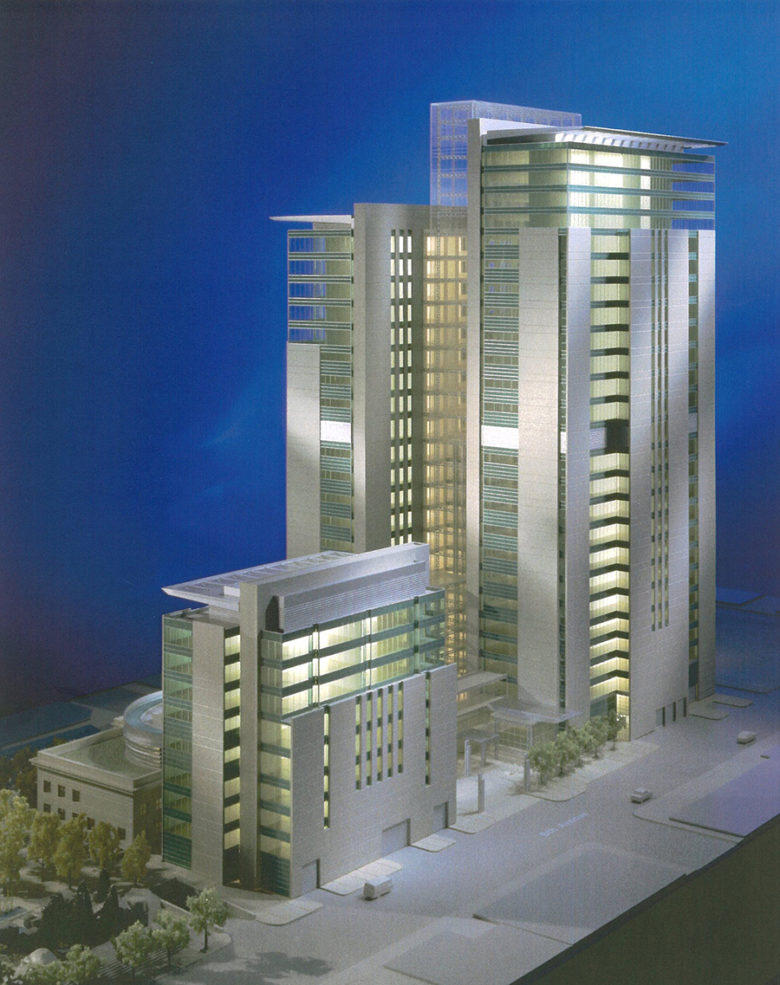
