Service: Reality Capture
University Health Network
Toronto Western Hospital Critical Infrastructure Reliability Project
Toronto Western Hospital (TWH), part of the University Health Network, initiated a project to enhance the reliability of its critical mechanical and electrical (M&E) infrastructure. With aging equipment dating back to 1954, TWH partnered with HH Angus to undertake a comprehensive upgrade project aimed at ensuring the continuous operation of high-risk medical services.
As the prime consultant, HH Angus was responsible for assessing the condition of existing mechanical and electrical systems. Following the assessment, upgrades were made to the facility, including replacing emergency generators, and establishing a new electrical room serving the ORs and the broader hospital campus. Subconsultants, including architectural, civil, environmental, and cost consultants, played crucial roles throughout the project.
To determine suitable locations for generators, extensive investigations were conducted, including structure analysis, examination of building codes, and assessment of environmental impacts. This collaborative effort led to the approval of a new penthouse above the East Wing for generator placement. The final engineering package involved locating the emergency generators at grade in a new fenced area, alongside the supply and installation of two new 1100W emergency generators and upgrades to the electrical network and distribution systems within the powerhouse.
HH Angus leveraged reality capture workflows, utilizing photogrammetry and a Matterport Pro2 camera, to produce a digital 3D model of the powerhouse and infrastructure. Through the efforts of our BIM team, 3D scans were taken of mechanical and electrical spaces, including complex piping and ductwork, to generate point clouds for reference in Revit. These models accurately depict existing systems, including central steam, chilled water, and emergency power systems serving the hospital's ORs and surrounding campus.
Additionally, the project has been recognized for excellence, with the generator exhaust stack winning in the category of Steel Works – Sculptures – Outdoor Pavilions at the Canadian Institute of Steel Construction's Awards for Excellence. https://hhangus.com/award-for-excellence/
The Toronto Western Hospital Critical Infrastructure Reliability project exemplifies HH Angus's commitment to delivering reliable solutions for healthcare facilities.
SERVICES
Mechanical Engineering | Electrical Engineering | Reality Capture
PROJECT FEATURES
3D modeling of powerhouse |
Scans of mechanical and electrical (M&E) spaces using Matterport Pro2 Camera | Point clouds of complex spaces using ReCap Pro Status: Completed
LOCATION
Eastern Canada
KEY SCOPE ELEMENTS
Upgraded mechanical and electrical systems | Installed emergency generators | Ensured environmental compliance | Modernized the powerhouse infrastructure.
Confidential Client
BIM Laser Scanning
HH Angus was engaged to create a 3D Revit model (LOD 300), accurate to reality, of the existing structure and visible HVAC, plumbing and electrical infrastructure. This model was delivered to the client for their use in 3D coordination of their high voltage switchgear replacement project.
The 17,000 ft2 area was scanned using a Faro S70 Laser scanner, with the scans subsequently registered using Faro Scene software to create point clouds. Point clouds were then processed in Edgewise modeling software and used to automatically extract and model walls, structure, piping, conduit and ducts, before being imported into Revit. This efficient process resulted in a very significant 60% reduction in modeling time. The remaining MEP infrastructure was modeled in Revit, with special attention paid to the location of the entry and leave points within rooms for all MEP infrastructure, in response to the client’s requirement.
One of the challenges of the project was the lack of easily accessible data required to create the Revit model. Recap pro or Faro Scene software is needed to review the point clouds and images; this software required licensing and installation on individual machines, which prevented it from being easily accessible to everyone on the project team. The software also requires additional computing power to run smoothly, and this presented an issue for machines that did not meet the software requirements.
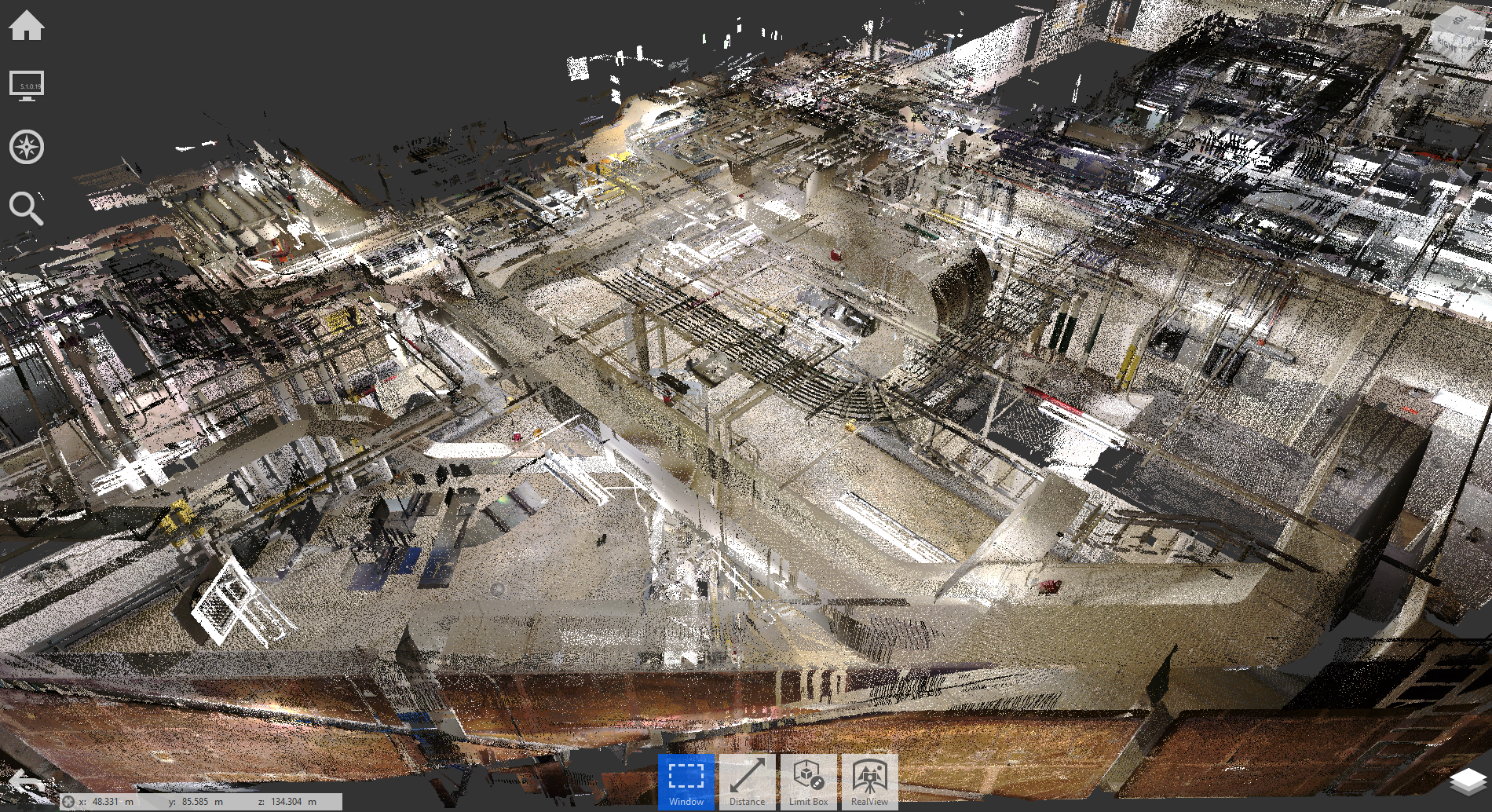
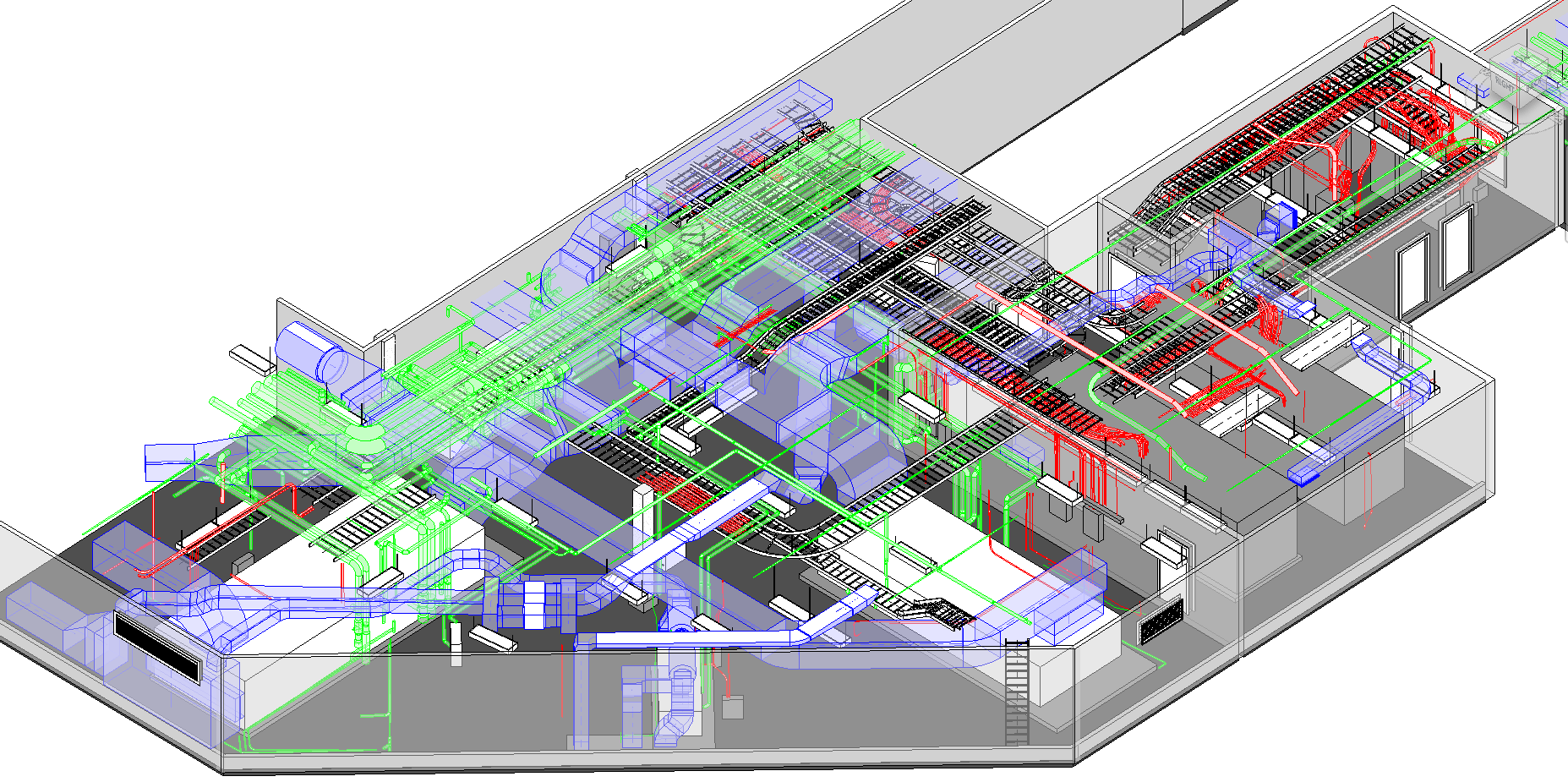
SERVICES
Prime Consultant | Scan to BIM provider
PROJECT FEATURES
Revit modeling of existing structure and visible HVAC, plumbing and electrical infrastructure
LOCATION
Toronto, Ontario
KEY SCOPE ELEMENTS
3D laser scanning
Confidential Client
Deodorizer Installation
HH Angus served as prime consultant for this new deodorizer processing plant. The new installation more than doubled the oil refining facility’s existing capacity.
Palm oil is the most widely-used edible oil in the world. Deodorizing is the final stage in refining the oil, and is required to remove odoriferous material, free fatty acids and other undesirable minor components, in order to produce a bland oil with a good shelf life.
The deodorizer tower is 30m high and 2m in diameter, with connected boilers, pumps, etc., that required connection to the existing production plant located adjacent to the expansion area. Due to the height and sectioning of the deodorizer, it had to be built in two stages.
One of the key challenges of the project was the site constraints. Two feasibility studies were produced as part of the investigation. It was determined that a new building was needed, rather than trying to install the deodorizer in the existing building.
In order to accommodate the electrical needs of the deodorizer process, a system upgrade was required to the switchgear. The upgrade allows the client the flexibility to install other major equipment in future.
Enabling projects for the deodorizer installation included a nitrogen tank installation, cooling water system, a new natural gas let down station, and new gas feed to the site.
SERVICES
Prime Consultant | Mechanical Engineering | Electrical Engineering
PROJECT FEATURES
Status: Completed 2017
KEY SCOPE ELEMENTS
Detailed Engineering Study | 3D modeling | 30m high deodorizer tower connected to existing plant within site constraints | Nitrogen tank installed | System upgrade to switchgear provided flexibility to install other major equipment in future
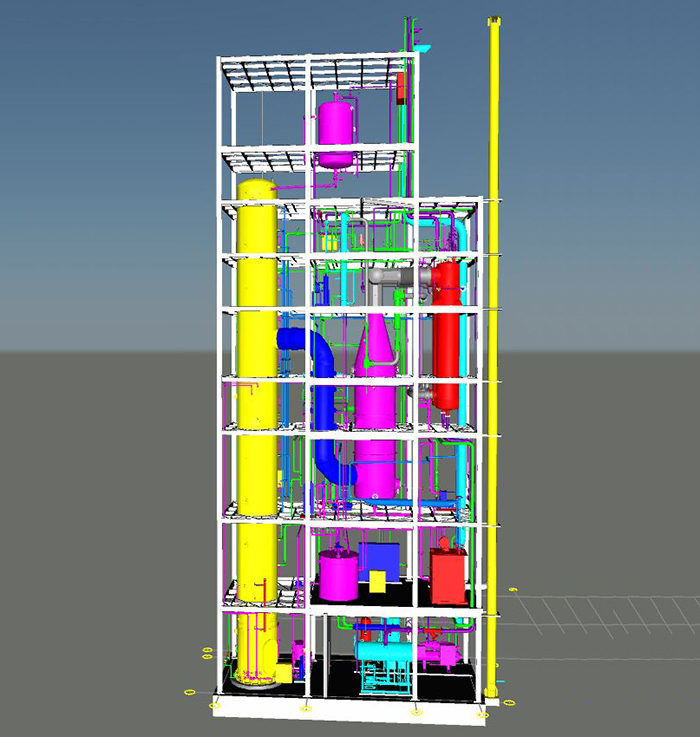
Modeling in 3D
As a special feature of the project, HH Angus modeled the installation using Plant 3D software. The installation was quite complex, and creating the model reduced both design time and the construction schedule. The contractor was able to see a comprehensive view of the design, confirming locations of pipes, etc.