Service: Vertical Transportation
SickKids
Peter Gilgan Centre for Research & Learning, ICAT
Creative solutions were required to accommodate the extremely intense and sophisticated computer systems within the architectural constraints of this building.
Angus Connect provided a Canadian first — the design and implementation of an HPC-High Performance data centre in a healthcare research facility.
Our recommended technical solution involved an overhead communications wiring system design, using multiple cable trays with an integral cable access management system. This innovative system design solution resulted in considerable space savings over a conventional system. A conventional raised floor communications cabling system was not an option due to space restrictions.
This Data Centre, which supports data cabinets with high performance servers that use 60 KW load, required very large and fully redundant Uninterruptible Power Supplies (UPS) and emergency generator systems to support the critical loads.
The facility has been certified LEED® Gold. The shell and core design were already well along when the Hospital’s High Performance computing group announced their intention to locate all of their high performance computing equipment into the new Data Centre.
SERVICES
Mechanical Engineering | Electrical Engineering | IT Communications Design | Lightining Design
PROJECT FEATURES
Size: 740,000 ft2 | Status: Completed 2013
LOCATION
Toronto, Ontario
KEY SCOPE ELEMENTS
Introduced innovative system solutions for urban-space saving, along with sophisticated computer systems | LEED Gold Certified
Ministry of the Attorney General/Infrastructure Ontario
Thunder Bay Consolidated Courthouse
This multi-storey building features 15 courtrooms, 4 conference/settlement suites, and Ontario’s first aboriginal conference settlement suite. It is LEED® Silver-certified, with barrier-free design, infrared hearing assistance and barrier-free witness stands and jury boxes.
HH Angus provided electrical engineering design, vertical transportation engineering and lighting design for the 8-storey building (seven above grade and one below grade for parking and holding cells). The electrical design features 100% emergency generator backup, UPS (uninterrupted power supply) and inverter lighting systems.
Lighting design included interior lighting, exterior building perimeter and parking. Exterior lighting was designed to be ‘dark sky compliant’, and all lighting design and luminaires targeted LEED® Silver. Custom lighting was designed for the aboriginal conference settlement suite, and featured low energy metal halide T5 fluorescent uplighting for the domed ceiling surfaces and LED downlights for general lighting.
Vertical transportation systems were designed to provide dedicated service for each of the primary forms of facility traffic: public, private (judicial), prisoner and building services. There are twelve elevators in total, the majority of which are Machine-Room-Less (MRL) gearless traction type. This elevator type represented the latest technological advance for energy efficiency and operational performance for low-to-medium rise buildings. Custom cab finishes for the public and private elevators complement the building’s interior design, while the prisoner elevators include an interior partition for the safe movement of accused by security staff.
SERVICES
Electrical Engineering | Lighting Design | Vertical Transportation Design
PROJECT FEATURES
Status: Completed 2014
LOCATION
Thunder Bay, Ontario
KEY SCOPE ELEMENTS
Designed transportation system to provide dedicated service for each form of facility traffic | Custom lighting design for specific conference suite featured low metal halide T5 fluorescent uplighting| MRL gearless traction type was used for - the majority of the elvators| LEED Silver
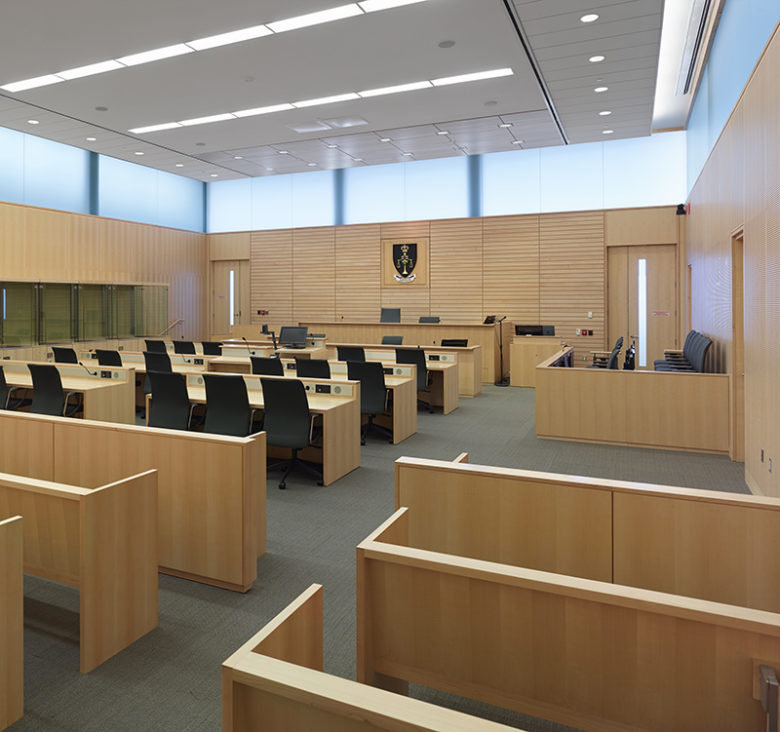
Built to last
The Courthouse was a design-build-finance-maintain project, with life-cycle repair and renewal responsibilities that ensure the courthouse (including heating and cooling systems, windows, floors, roofing structures and hard landscaping) is kept in excellent working condition over the 30-year period.
Northern Health Authority
Fort St. John Hospital & Peace Villa
HH Angus participated in the integrated and sustainable design process, assessing several different mechanical concepts focusing on heat recovery, improved space air distribution and high-efficiency equipment. Considering the climate, extensive consideration was given to balancing the use of 100% outdoor air systems with total enthalpy heat recovery wheels, with the need to reduce energy consumption.
Mechanical and electrical engineering for this new build acute care community hospital included related services such as laundry and food services, and a replacement residential care facility. The hospital provides 58 inpatient beds with full diagnostic and treatment facilities, three operating rooms, endoscopy suite, and 124 residential care beds. Part of our scope, via our affiliate ACML, was to provide the hard Facilities Management for this project.
The project has been certified LEED® Gold and includes specific energy saving elements as a key component of the design. We worked extensively with all other design team members to meet aggressive energy consumption targets without increasing capital costs.
Also notable was the design and construction of the complex and high-efficiency heating plant featuring a series of condensing hot water boilers piped in a cascading temperature arrangement. The focus was on delivering a well-sealed and insulated building to reduce building envelope energy losses and allow the heating boilers to run at peak energy efficiency. This will provide the client with long-term energy savings, as heating costs have traditionally been very high.
The specification of the pad-mounted generator enclosures saved both time and money. Unconventionally, the generators were pre-fabricated and installed in sound-attenuated enclosures before being shipped to site. This allowed for quick ‘plug and play’ installation when these units arrived on site.
Lighting strategies were crucial, with a target of 30% energy reduction below ASHRAE standards while still meeting CSA light level requirements. Implementation of an extensive low voltage lighting control system further reduced energy consumption.
Vertical transportation elements included three passenger elevators and six service elevators.
For the IMIT scope, the Angus Connect team designed a new wired/wireless system, network and infrastructure to help improve workflow with the introduction of RFID tagging to help with inventory and distribution, as well as laying a robust foundation for a future Real Time Location System. Additional major systems included telephone, nurse call, public address, patient entertainment, intercoms, video conferencing and patient monitoring. Our team also planned for and added the infrastructure for the new digital modalities and connection to a centralized PACs system, which improved diagnosing and reporting, and facilitated consultations between staff members.
SERVICES
Mechanical Engineering | Electrical Engineering | IMIT and Security Consulting | Vertical Transportation | Lighting Design
PROJECT FEATURES
Size: 330,000 ft2 | Status: Completed 2012
LOCATION
Fort St. John, British Columbia
PROJECT FEATURES
REVIT MEP provided design and documentation | Centralized UPS | Integrated communications systems platform for all building operations and healthcare applications | LEED® Gold Certified
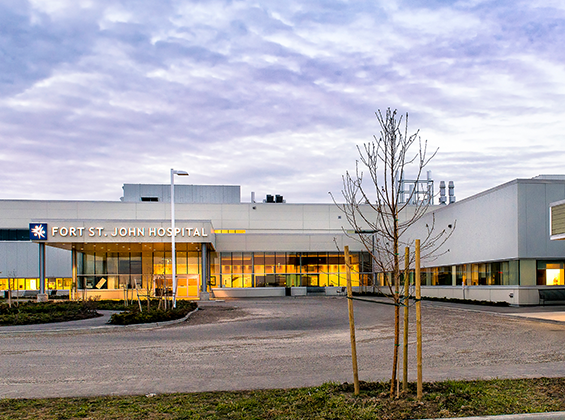
Respecting Indigenous ceremonies
The two spiritual rooms were designed to accommodate Sweet Grass and Smudging ceremonies, with dedicated exhaust to extract smoke and odours generated from the ceremonies.
— Image courtesy of Fort St. John Hospital Foundation
St. Michael’s Hospital
Li Ka Shing Knowledge Institute
The Li Ka Shing Knowledge Institute is home to some 200 researchers, working in sophisticated laboratories and front-line clinical settings to explore both the basic dynamics of disease and the best ways to improve patient outcomes. Research is carried out in such diverse areas as multiple sclerosis, pregnancy, pediatrics and musculoskeletal disease.
A 9-storey 335,000 ft2 facility, the Li Ka Shing Knowledge Institute comprises the Keenan Research Centre and the Li Ka Shing Centre in Healthcare Education. This concrete structure is enveloped in a double-layer glass curtain wall, with a profile that reflects the academic excellence and leading-edge technology of the research and education programs within.
The research component is housed on the 209 Victoria Street site and the education component is on the 38 Shuter Street site. Linking the two sites over the Victoria Laneway is a connection housing elevators, a feature stairway, double-height lounges, conference rooms and kitchenette spaces, all designed as collision points in the building to promote information interactions and exchanges of knowledge and ideas.
The animal facility (vivarium) for larger animals includes environmentally-controlled holding areas. The animal waste disposal system cage contains washing and operating facilities, as well as an isolation area for animals entering the facility.
- Total Wet Lab Area - 3 floors at 15,000 ft2 each = 45,000 ft2
- Approximately 30% of the Research building is Wet Lab
- Vivarium on 8th floor - approximately 20,000 ft2
- Approximately 12% of research building is vivarium.
Rather than constructing small individual labs, the laboratory spaces are open concept in design, with high ceilings, to improve user comfort and access to daylight. We met the engineering challenge of designing for installation of ductwork in greatly reduced ceiling space, while still ensuring adequate air volume changes. Centrally located alcoves for dry bench work included fume hoods and lab space, designed with flexibility in mind for future uses. Likewise, the cooling system allows for spot cooling to accommodate varying equipment loads, depending on use of the space.
The vertical transportation work at Li Ka Shing featured eight passenger elevators (two being future cars and one a parking shuttle), as well as one service elevator.
SERVICES
Mechanical Engineering | Electrical Engineering | Vertical Transportation | Communications | Security | Lighting Design | Vertical Transportation Design
PROJECT FEATURES
Size: 335,000 ft2 | Status: Completed 2011
LOCATION
Toronto, Ontario
KEY SCOPE ELEMENTS
9 storey facility | Double-layer glass curtain wall | 20,000 ft2 animal vivarium for large animals |45,000 ft2 of wet lab space | Special lighting design incorporated for grand staircase and bridge connecting Li Ka Shing to St. Michael's Hospital | Vertical transportation featured 8 passenger elevators and one service elevator
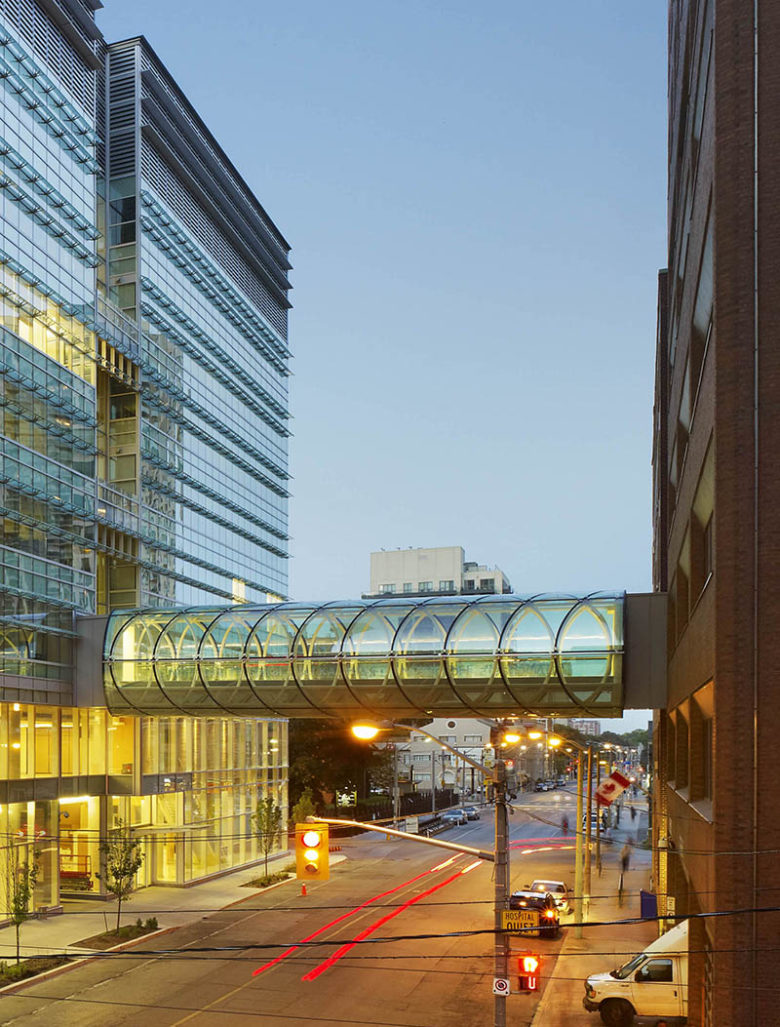
Lighting to maximize common spaces
Special lighting design features for the building included the grand staircase and the bridge connecting Li Ka Shing to St. Michael’s Hospital. The lighting is controlled by a building-wide automation system.
Bangalore (Kempegowda)
International Airport
The Bangalore (Kempegowda) International Airport airport expansion will increase the airport’s capacity to at least 65 million passengers per annum. Phase 1A of the new Terminal currently includes an estimated 46 elevators, 29 escalators, and 17 moving walks.
In addition to the new Terminal, a multi-level car park is being constructed to accommodate an estimated 2438 passenger vehicles after Phase 2. In addition to the vehicle stalls, there is capacity for an estimated 450 taxi’s after Phase 2. A Metro connection to the Terminal is also planned following Phase 2 expansion, for which elevating provisions are currently being made.
HH Angus’ client is Skidmore, Owings & Merrill LLP (SOM) from New York, with whom we worked previously on a joint-venture architectural team with Adamson Associates and Moshe Safdie on Terminal 1 at Toronto Pearson International Airport.
SERVICES
Vertical Transportation
PROJECT FEATURES
Status: Ongoing
LOCATION
Bangalore, India
KEY SCOPE ELEMENTS
46 elevators | 29 escalators | 17 moving walks for new Terminal Building and multi-level car parkade for 1724 vehicles, with Phase 2 planned expansion to 2438 passenger vehicles