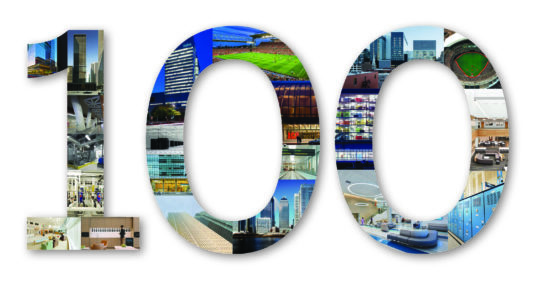
Toronto-based HH Angus and Associates is celebrating its 100th anniversary in 2019, and at the end of May the company announced that Paul Keenan, formerly director of its health division has been named president.
Keenan replaces Harry Angus, the third generation of the Angus family to lead the privately owned firm. Angus remains on as CEO and Chair of the Board.
A Queen’s University grad, Keenan has been with the firm for 25 years and served as director for the past decade. Also, within the past year, HH Angus was selected among Canada’s Best Managed Companies for 2019, an achievement received in its first year applying to the Deloitte program. And last fall the firm captured the Schreyer Award at the 2018 Canadian Consulting Engineering Awards for its work on the CHUM hospital in Montreal.
We spoke with Keenan to discuss HH Angus and where it goes from here.
You’re the firm’s first president not named Angus. What does that mean for the company?
I think it in part means we’re maturing. The firm has grown to over 250 people, and I think that as a bigger company you need inputs from different areas. The family legacy is important and it continues—Megan Angus, Harry’s daughter, is one of the senior leaders in the organization—and although I’m not part of the family. I’ve grown up in the HH Angus way, so we’re maintaining some of that family connection and we’re enhancing it as we go forward.
Describe the HH Angus culture?
We try to maintain the family feel of the business, and with that comes a responsibility to the staff and a social responsibility to the community. Our turnover has been historically very low—we have 40 or 50 employees with over 25 years service—and that longevity and feeling part of a group is
important for us.
What is your leadership style?
My experience here has always felt like a series of careers within one career. I started on small projects, gaining skills and transitioning naturally from project to project with larger challenges and increasing levels of responsibility.
I want to create those opportunities for our people. We’ve got to give them the opportunity to succeed or fail and go from there. At some point we all make decisions, and we need to believe in our decision making process based on the experiences we’ve had. Trust yourself, trust your team, make your decision and then move forward.
It’s important not to get stuck; we need to keep our momentum going.
How does a consulting firm foster creativity & innovation among its employees?
I think that’s a challenge for the entire industry, and we need to move more quickly now, to get from ideas to execution. One of the things we’ve done this year is create an Innovation Hub, which is a forum and a place to gather a range of ideas and have our people practice making presentations and share ideas, and then flesh them out, incubate them and then execute.
How has the firm changed over the years?
Traditionally, mechanical/electrical consulting engineering-led projects had been half of our business, and then the world changed. We did a lot of healthcare-related work in the ’90s and have become recognized as healthcare experts. As that market has matured we’ve responded and entered different areas, for example transit, data centres, and more commercial work. Our energy group, that traditionally has done a lot of industrial work, is focused on more low-carbon, sustainable energy projects.
We also have some sub-specialities, such as vertical transportation, lighting design, and our ICAT group that does communications and consulting around smart buildings. You need to be diversified enough to respond to what the market is telling you.
How will you measure your success?
One of our primary objectives is to continue to be an independent firm. That comes with its challenges, but it also comes with its rewards.
We’ve been on a steady trajectory of growth and fundamentally we need to continue to grow; growth is important to create opportunities for our employees and for the underlying strength of our business. We need to be strong enough to resist whatever economic forces come along; we need to grow geographically; and we need to grow our share of the market and do the kind of interesting work that motivates our people.
Which HH Angus project has impressed you the most?
There are many projects in the history of the firm that are impressive and set us on the path of wanting to continue doing projects that are special and iconic. Personally, the Sick Kids research tower, a 750,000 sq. ft. research building, is iconic in the City of Toronto and more fundamentally is a place where important things happen for the future of this community and this country.
Canadian Consulting Engineer
June/July 2019