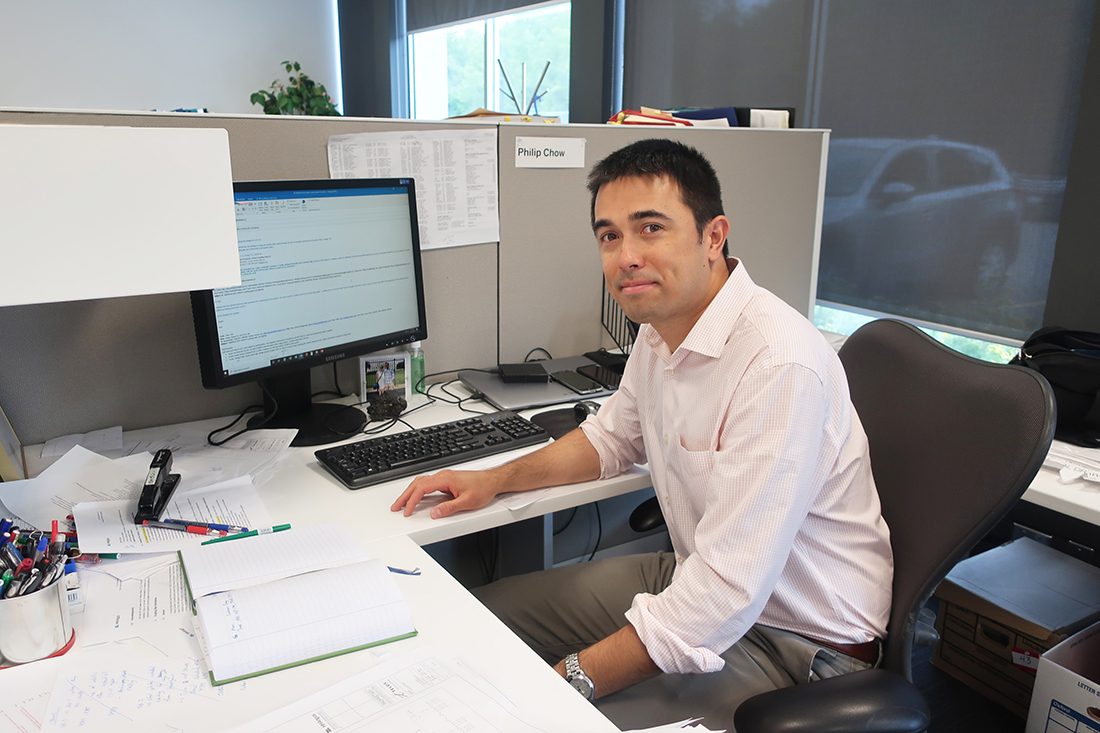
Philip joined HH Angus in 2006 and is currently a Senior Electric Engineer and Project Manager in our Technology Division.
What’s your favourite thing about working at HH Angus?
I like the diverse projects and diverse clients. I enjoy the work. It is satisfying to see things get built. I enjoy the travel aspect – working all over the place, different clients, different things.
Where do you travel for work?
So far, I’ve traveled around North America.
How do you personally contribute to design and construction?
I am the Lead Electrical Engineer on a number of projects, responsible for design, project management, and delivery of our design to our clients. We are often the prime consultant on projects, the head consultant. We retain an architect or a structural engineer directly, or select them on behalf of the client. In those cases, the client retains them but we manage overall the process. We also manage the procurement of equipment and services for the client.
How has working here helped you grow in your career?
It was the first job I had out of school, so I’ve grown quite a bit in my career.
“I've enjoyed diverse opportunities being able to work on multiple projects, with multiple clients, with multiple diverse models.”
Why did you want to become an engineer?
I was interested in technology and, I thought it would be interesting to have a career at that field.
What project are you most proud of?
I really felt good about the Sunnybrook High Voltage Emergency Project. That was one I designed and was the Electrical Lead. It was a project where we took a completely functional hospital and rebuilt their emergency power plant without compromising emergency power to the hospital the bew plant was built within the footprint of the exisiting plant. It was a very challenging project, which involved multiple phases of construction.
What are some of the things about the company that you really like?
I like the dedication over the years to the library collection. I thought that was pretty great. Some of the people who work in Records Management have a background in library science. The company has been dedicated to the knowledge behind engineering we have books from 20s. It speaks to the longevity of the company. Over the years, people have accumulated technical standards, books, journals and things pertinent to older systems and technologies. A lot of places don’t have a comparable knowledge base.
When you started with the company, did you have a time when a senior staff member helped you along?
When I started, they used to pair the new grads with an inspector and send them to construction projects. I spent probably 2 to 3 weeks doing that. You got to see the practical aspects of construction which puts a lot of things in perspective when you are designing. For me, that had a lasting impact. Additionally, I was fortunate that I had some projects that went into construction when I started. They had already been designed and I was tasked with looking after the contract administration. Seeing other people’s designs, how they were being built, some of the issues that come up, was very useful.
What inspires you?
Family, friends and doing good work.
What trends or technologies on the horizon excite you most?
I always tell younger staff, one of the best things ever invented was the digital camera. It may not seem all that great now because it is so prevalent. Also PDFs. When I started, the majority of submittals were paper. We would receive paper submittals, we would do our reviews, we would staple our reviews to them and courier it out. You’d do a large project with a wealth of information, and you would no longer have it at your fingertips because it was all on paper, which is now stored off site. But, nowadays, it’s all PDFs. You can keep a copy and everything is readily available. Same with digital cameras. Somebody can go to site and take photos of what they are working on. You’ll always have that reference to go back to later: “oh, this is what I did on the last job. Maybe it didn’t go exactly as planned – let’s do it a bit differently this time”. Today, the technology gives you accessibility that you didn’t have in the past.
What skills or traits helped you advance in your career from the new grad stage?
I always believed in making the product you are selling better in order to be more competitive. Have diverse experience. Obviously, getting licenses and certifications speak to a broader experience and broader knowledge base. When you are selling services, you want to make sure the clients understand they are paying for experience, for somebody who does this for a living. They don’t have people on staff to do the work, so they are hiring us.