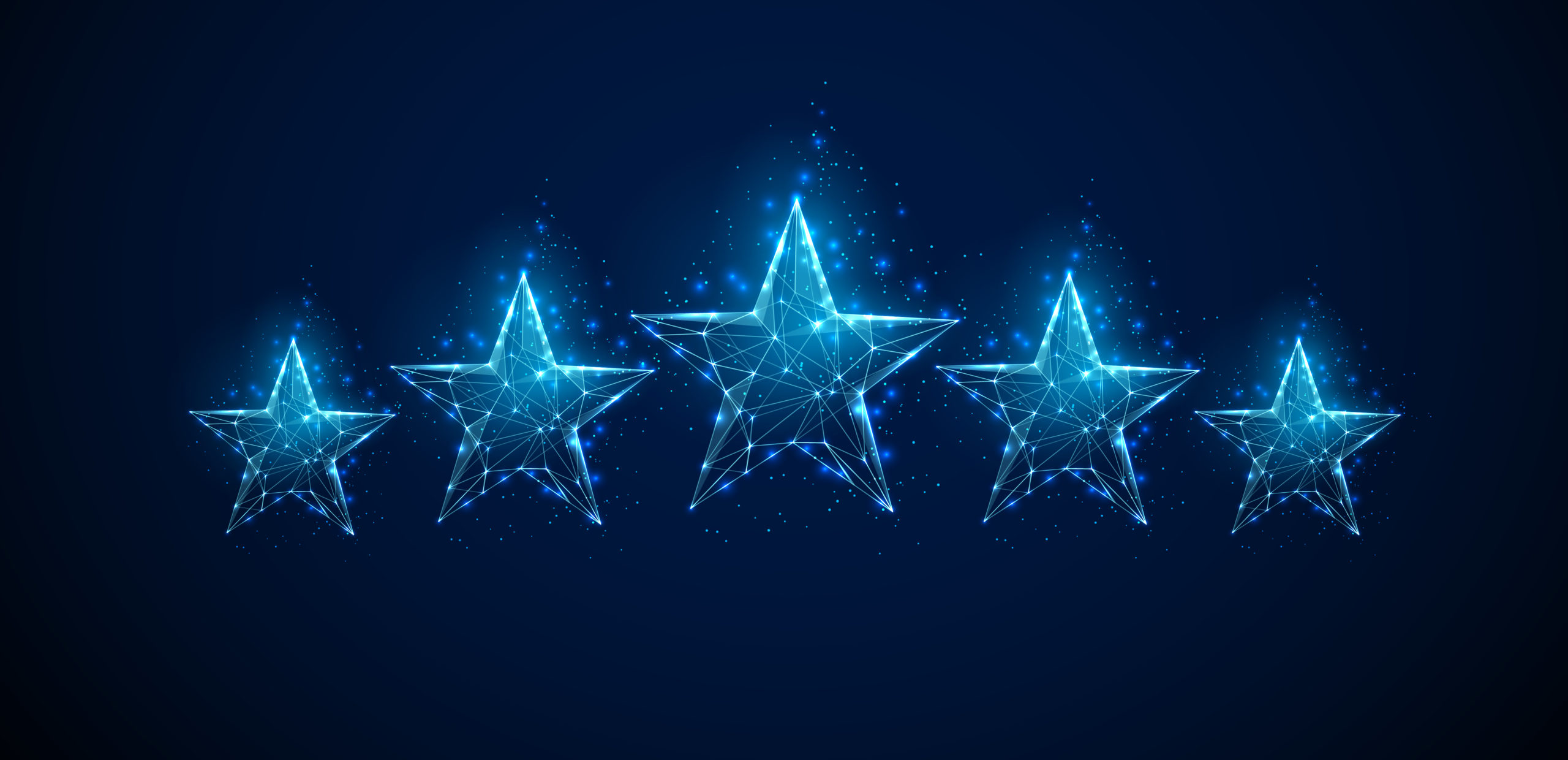
The Canadian Council for Public-Private Partnerships has announced the winners of its 2022 National Awards for Innovation and Excellence in Public-Private Partnerships. Three of our clients have been honoured and we congratulate them on receiving this prestigious award - Grandview Children’s Treatment Centre Redevelopment in Durham Region, Ontario Royal Inland Hospital in Kamloops BC; and Oakville Trafalgar Memorial Hospital in Oakville ON.
Project Development – Award of Merit: Grandview Children’s Treatment Centre Redevelopment Project, Ontario
This project, currently in development, will specialize in the care and support of children and youth with physical, communication and developmental needs, and their families. The new four-storey Treatment Centre, with a gross area of 94,733 ft2, will increase the centre’s ability to offer more services to a greater number of children and youth in the region. Construction is underway.
Partners: Infrastructure Ontario, Grandview Children’s Centre, and Children First Consortium (Amico Design Build Inc. and Sacyr Construction S.A)
Service Delivery – Award of Merit: Oakville Trafalgar Memorial Hospital, Ontario
In operation since 2015, this $2-billion DBFM hospital project is still one of the largest infrastructure projects in Ontario. The LEED®Gold facility, with 457 beds and shelled-in space to facilitate 602 beds by 2023, features multiple smart technology enhancements.
Partners: Infrastructure Ontario, Halton Healthcare Services Corp., and Hospital Infrastructure Partners (Carillion Canada Inc., EllisDon Corp. and Fengate Capital Management Ltd.)
Infrastructure – Award of Merit: Royal Inland Hospital - Phil & Jennie Gaglardi Tower, British Columbia
Opened in February 2022, this new $417-million, 300,000 ft2 patient care tower in Kamloops houses clinical, administrative and support spaces, including a surgical suite and neonatal ICU serving 220,000 residents in the region. The project used a DBFM model with a construction management agreement, resulting in an estimated savings of $64 million compared with traditional procurement.
Partners: Infrastructure BC, Interior Health Authority, and EllisDon Infrastructure Healthcare
HH Angus’ P3 experience includes both Proponent and PDC (Planning, Design and Compliance) work. Our portfolio includes Thunder Bay Correctional Facility in Ontario; Queen Elizabeth II Health Sciences Centre in Bayers Lake NS; Royal Columbian Hospital Redevelopment in BC; the largest P3 healthcare project in North America, the $2+ billion CHUM hospital in Montreal; as well as the $5.3 billion Eglinton Crosstown LRT in Toronto.
To see more examples of our experience on P3/DBFM and IPD procurement methods for project delivery, click here.
To see the full slate of CCPPP winners, click here.
About the Canadian Council for Public-Private Partnerships
Established in 1993, CCPPP is a national not-for-profit organization. Its mission is to collaborate with all levels of government and Indigenous communities to enable smart, innovative approaches to infrastructure development and service delivery.