Location: Eastern Canada
King Animal Hospital
Fitout and Peer Review
The King Animal Hospital is a state-of-the-art multidisciplinary referral and emergency hospital for small animals and equines, complete with MRI’s and medical gas systems.
HH Angus provided mechanical consulting services for the fitout of the King Animal Hospital. Our scope of work included a peer review and report identifying potential gaps between the base building mechanical infrastructure and the programming and capacity requirements for the state-of-the-art animal hospital. Following the peer review and report, we provided full mechanical design services for the fitout, from schematic design through to construction administration and project close-out.
The fitout included approximately 60,000 FT2 in a 4-storey greenfield facility, accommodating a wide range of program elements including 8 operating rooms, 12 exam rooms, an MDRD sterilization room, laboratory and pharmacy, diagnostic imaging (MRIs, CT Scan) suites, hydrotherapy, and physiotherapy, as well as support and administrative spaces.
The sub-cellar is home to an equine treatment area with CT equipment outfitted with robotic arms, and an MRI with an adjacent horse lift. An arena will be used for equine physiotherapy. A large heated ramp from grade was selected over an animal elevator to provide a safer, and less stressful, mode of transportation for the horses when moving between floors. The small animal services area of the sub-cellar features three aquatic treadmills, a hydrotherapy pool, and a hyperbaric oxygen chamber.
The cellar level includes the staff gym, lounge, meeting areas, and a dog quarantine with an exam room and 17+ dog runs. Oxygen connections to the cages and foot baths in the floor support infection prevention and control.
The ground floor features an equine surgical area, including recovery, dirty surgery area (two surgeries performed simultaneously), and an equine water treadmill. It also houses a treatment area for dogs, cats and exotics, including dentistry area, and a canine showcase area with three surgery, CT, x-ray and neurological rooms with MRI equipment.
The second floor houses staff meeting spaces and amenities. A multipurpose space doubles as a surgical support area, Learning Centre, and workshop.
The base building infrastructure was in place prior to HH Angus joining the project, which meant our team was tasked with working in the confines of a building shell that was already in place. This presented challenges at the cellar level, where the team had to design while accounting for low floor to floor heights.
The hospital had not yet retained any permanent staff during the design stage, and many of the programming elements relied on recommendations from other consultants/doctors/experts during the design-stage user group meetings. Once permanent staff were hired for key departments, the design team worked with the client to make adjustments to the layouts and equipment based on staff input.
Although an animal hospital does not fall under the same CSA standards required for human
hospitals, there is a trend towards meeting those standards in animal care facilities. HH Angus wrote design briefs for systems and features that the client chose for this facility, many of which aligned with CSA requirements for a state-of-the-art human hospital.
SERVICES
Mechanical Engineering | Peer Review
PROJECT FEATURES
Size: 60,000 ft2 | Status: Completed 2024
LOCATION
King City, Ontario
KEY SCOPE ELEMENTS
Spaces for diagnostic imaging, hydrotherapy, surgery, physiotherapy, and support and administrative space | Therapy arena and pools | Staff amenities
Waypoint Centre for Mental Health Care
Chigamik Community Health Hub
Waypoint Chigamik Mental Health Centre is part of a redevelopment project and replaces two older facilities in use since the 1800s.
The challenges of this project included the requirement that the entire building be completely designed in one stage, rather than proceeding with design packages, plus delays in funding during the design process which resulted in a requirement for both a base building package and a fitout package.
To accomplish this, HH Angus coordinated two tender packages and two building permit submissions. Some detailed specifications in each package were interchangeable for the mechanical and electrical tender process. Working with phased schedules ensured that equipment start-up was fully coordinated between the tender packages.
The project faced additional challenges to provide an energy-efficient HVAC system, due to compliance with CSA Z317.2 and budget restrictions, as well as a small mechanical service space. To overcome these challenges, extensive coordination was implemented throughout the project across all disciplines.
SERVICES
Mechanical Engineering | Electrical Engineering | Lighting Design | ICAT Commissioning
PROJECT FEATURES
Size: 40,000 ft2 | DBFM | Fully ducted HVAC system designed to comply with CSA Z317.2 | Status: Completed 2020
LOCATION
Midland, Ontario
KEY SCOPE ELEMENTS
Building has full back up power with generator sized to accommodate the entire load of the building on loss of utility power conditions
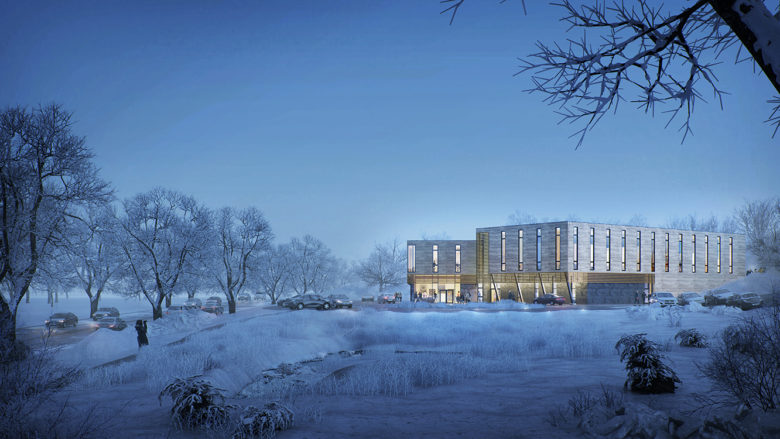
Efficient design
Several engineering designs were reviewed by the project team to ensure compliance with the owner’s goals and restrictions, while achieving an efficient design.
Customized spaces
The two-storey 40,000 ft2 mental health care facility has amenities for indigenous smudging ceremonies, physiotherapy, conferences, a community kitchen, gathering rooms, and a youth programming space.
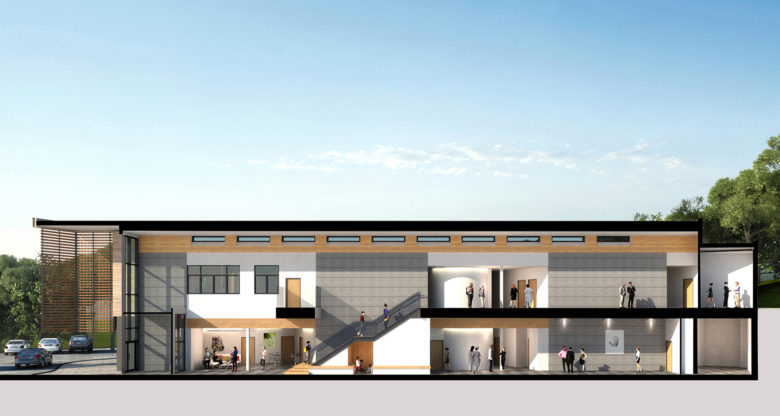
Renderings courtesy of Lett Architects Inc.
Enwave Energy Corporation
Pearl Street Energy Centre
The Pearl Street Energy Centre project has been honoured with an Award of Distinction at the Ontario Engineering Project Awards by the Association of Consulting Engineering Companies (ACEC).
Buildings in Toronto generate more than half of the city's greenhouse gas emissions. New technologies, like Enwave's expanded heat delivery system, will play a critical role in reducing our cumulative carbon footprint.
This project exemplifies cutting-edge engineering and design, integrating robust energy solutions that challenge traditional methods. Our focus on sustainable and efficient energy use through advanced engineering practices not only supports but advances the environmental goals of urban energy systems. HH Angus was the Prime Consultant and Mechanical and Electrical Design Engineers for the Pearl Street Energy Centre (PSEC) project. We also acted as the design team project managers.
When fully utilized, Enwave's low carbon heating facility will provide enough low-carbon heating to reduce emissions in Toronto by approximately 11,600 tCO2e, the equivalent of converting over 10 million square feet of office space to net zero.
As part of the TransformTO Climate Action Plan, which outlines ways to improve the city’s health, grow the economy and improve social equity, district energy was identified as a key strategy. In 2017, Enwave was selected as a partner by Toronto’s City Council to help accelerate the implementation of the plan to reduce greenhouse gas emissions and make the city more resilient.
Enwave’s district energy system is the largest in North America. It serves 180 buildings comprising more than 40 million square feet through 4 interconnected downtown plants and 40 kilometres of underground pipes. The addition of the PSEC to the district energy system will expand Toronto’s district heating and cooling distribution and capacity using low carbon technologies, by installing 3600 tons of cooling and 62,000 Mbh (thousand BTU’s per hour) of heating using water source heat pumps (heat reclaim chillers). Enwave’s ‘Green Heat’ offering is also being made possible by the installation of new assets that utilize waste heat while producing cooling and hot water.
The site offered some interesting complexities to be solved by the design team. The first was space constraints. As the existing Energy Centre did not have any space to house the new equipment, the only available space that could be used for the addition is a small corner on the lot where buried fuel oil tanks are present. A design was implemented to build over the tanks, one that would comply with the requirements of the Ontario Building Code and the Technical Standards and Safety Authority by leaving the ground level open for future removal of the tanks. All disciplines had to overcome many challenges due to space limitations, including structural, architectural, mechanical, and electrical.
A challenge for the mechanical design team centered on how to integrate the new heat pump system with the existing heating and cooling district system, as well as how to stage equipment without impacting Enwave’s existing customers and their stringent temperature requirements. Our solution was to design a false loading system to start and stage on additional heat pumps in order to avoid temperature spikes which would have negative impacts on customers’ critical data centre equipment.
According to the Canada Green Building Council, “it’s estimated that residential, commercial, and institutional buildings contribute 17% of Canada's greenhouse gas emissions today, and when building materials and construction are included, this level approaches 30%”. As the designers and engineers of these facilities, the AEC industry has an outsize role to play in ensuring the success of sustainable development.
HH Angus has a proven track record of promoting innovative and sustainable engineering solutions. We are committed to providing engineering solutions that reduce energy consumption and reduce or eliminate greenhouse gases.
SERVICES
Prime Consultant | Mechanical Engineering | Electrical Engineering
PROJECT FEATURES
Completed 2025 | New assets use waste heat while producing cooling and hot water | 3600 tons of cooling | 62,000 Mbh heating using water source heat pumps
LOCATION
Toronto, Ontario
KEY SCOPE ELEMENTS
Overcame site constraints through innovative design to comply with OBC and TSSA requirements | Integrated new heat pump system to existing system
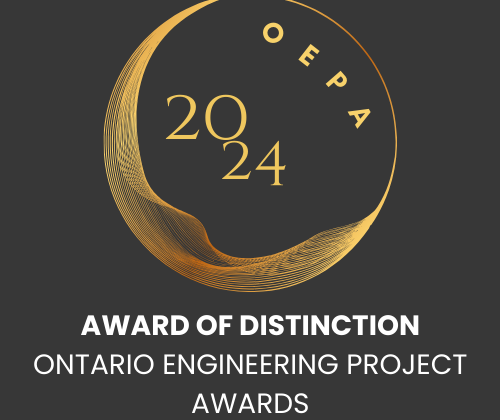
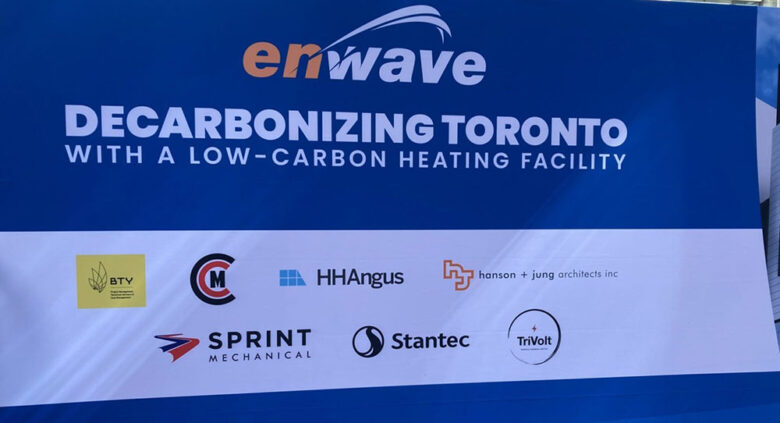
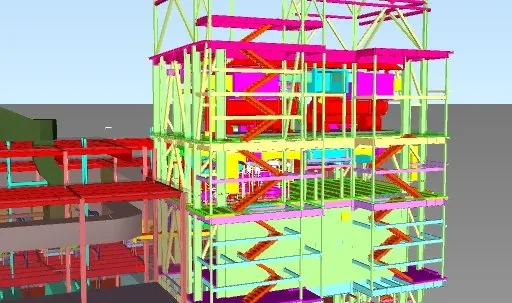
University of Toronto
Robarts Library, Reading Room Renovation
The Robarts Library, renowned as an example of the 'Brutalist' style of architecture, stands as one of Canada's largest academic library buildings, serving as a cornerstone of scholarly pursuit at the University of Toronto.
HH Angus provided mechanical and electrical engineering services, as well as design consulting for IMIT and lighting, for the renovation of the Library's fourth floor Reading Room.
The project, aimed at modernizing the library's facilities to accommodate contemporary learning paradigms, posed several intricate challenges. One notable challenge involved the intricate design of cabling for security and telecoms within the limited capacity channels of the floor slab, while ensuring the preservation of the library's architectural integrity. Moreover, the integration of wireless thermostats for HVAC control demanded meticulous planning to guarantee effective functionality while maintaining the library's iconic aesthetic.
In response to the evolving needs of the campus community, the renovated space has been thoughtfully curated to foster a conducive environment for study, collaboration, and digital scholarship. Individual study areas, equipped with state-of-the-art digital stations and consultation rooms, offer students and faculty alike the resources they need to thrive academically. Additionally, the incorporation of light therapy zones underscores a commitment to promoting wellness and inclusivity within the Library's patrons.
Improved accessibility was a key aspect of this renovation, featuring new study spots with adjustable desk heights, versatile seating configurations, and customizable lighting options, ensuring that all user's needs are considered. As well, strategic wayfinding elements and clear sightlines have been implemented to facilitate seamless navigation throughout the revitalized space.
SERVICES
Mechanical Engineering | Electrical Engineering | IMIT Consultant | Lighting Consultant
PROJECT FEATURES
20,300 ft2 space | Accessible study areas | Integration of building systems
LOCATION
Toronto, Ontario
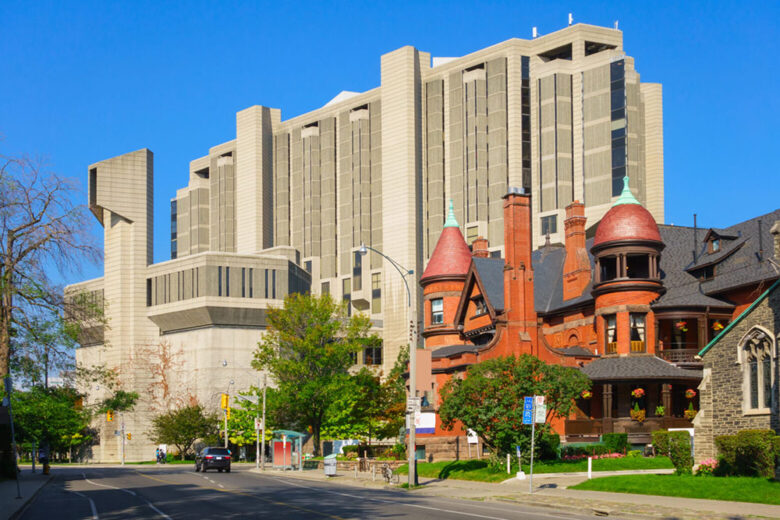
Enhanced environments
The Library renovation is a significant advancement in the modernization of an academic institution, and underscores UofT's dedication to enhancing the built environment for all users.
City of Mississauga
Burnhamthorpe Community Centre Renovation and Expansion
The Community Centre features a state-of-the-art aquatic centre as well as an equipment-based fitness centre. This is the first project designed and built to Mississauga's corporate Green Building standard. The project has also achieved Level 1 CGBS and incorporates net zero and passive house principles, a high-performance building envelope, triple glazing, and a green roof.
HH Angus played a key role in this project, providing mechanical and electrical engineering services, as well as security, IMIT, lighting, AV, and plumbing design. The addition includes a new 25-metre, 6-lane pool, therapeutic pool, fitness centre, and common areas, for a total of 43,000 ft2 of added amenities.
Renovations to the existing community centre encompass improvements across 65,000 ft2, repurposing and relocating multi-purpose program spaces, gymnasium, indoor arena, and upgrading facilities to meet accessibility and green development standards. Despite challenges posed in connecting to the existing building, the addition was situated on the northeast corner, utilizing space from the adjacent park.
To see more renovations, click here
SERVICES
Mechanical Engineering | Electrical Engineering | Plumbing Design | Lighting Design | Audio-Visual Design | Security Design | IMIT Design
PROJECT FEATURES
Green facility design to LEED Silver standard | State-of-the-art aquatic centre | Equipment-based fitness centre | Status: Completed 2024
LOCATION
Mississauga, Ontario
KEY SCOPE ELEMENTS
Project built to Mississauga's Green Building standard | Achieved Level 1 CGBC | Addition connected to existing recreation centre | Renovations and upgrades to existing building
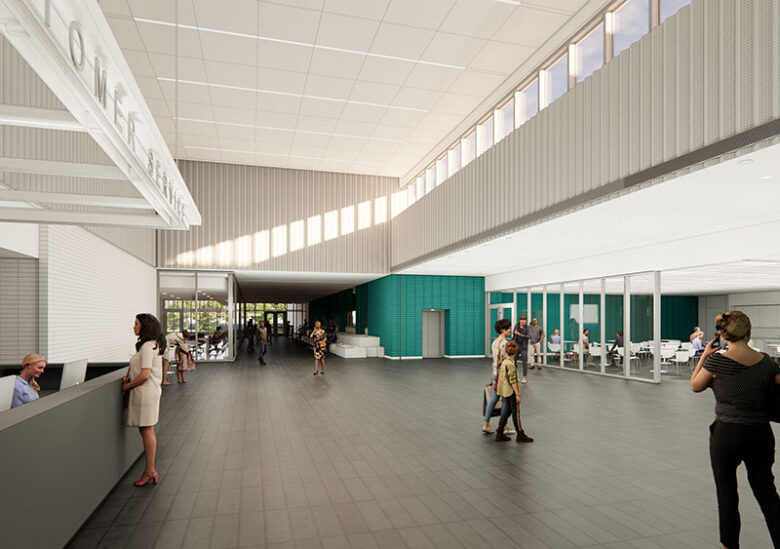
All images courtesy of CS&P Architects
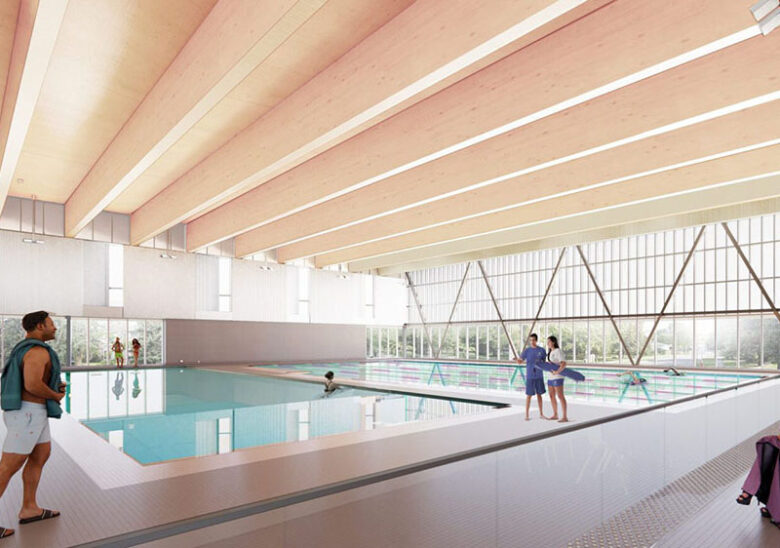