Service: Electrical Engineering
University of Toronto
Robarts Library, Reading Room Renovation
The Robarts Library, renowned as an example of the 'Brutalist' style of architecture, stands as one of Canada's largest academic library buildings, serving as a cornerstone of scholarly pursuit at the University of Toronto.
HH Angus provided mechanical and electrical engineering services, as well as design consulting for IMIT and lighting, for the renovation of the Library's fourth floor Reading Room.
The project, aimed at modernizing the library's facilities to accommodate contemporary learning paradigms, posed several intricate challenges. One notable challenge involved the intricate design of cabling for security and telecoms within the limited capacity channels of the floor slab, while ensuring the preservation of the library's architectural integrity. Moreover, the integration of wireless thermostats for HVAC control demanded meticulous planning to guarantee effective functionality while maintaining the library's iconic aesthetic.
In response to the evolving needs of the campus community, the renovated space has been thoughtfully curated to foster a conducive environment for study, collaboration, and digital scholarship. Individual study areas, equipped with state-of-the-art digital stations and consultation rooms, offer students and faculty alike the resources they need to thrive academically. Additionally, the incorporation of light therapy zones underscores a commitment to promoting wellness and inclusivity within the Library's patrons.
Improved accessibility was a key aspect of this renovation, featuring new study spots with adjustable desk heights, versatile seating configurations, and customizable lighting options, ensuring that all user's needs are considered. As well, strategic wayfinding elements and clear sightlines have been implemented to facilitate seamless navigation throughout the revitalized space.
SERVICES
Mechanical Engineering | Electrical Engineering | IMIT Consultant | Lighting Consultant
PROJECT FEATURES
20,300 ft2 space | Accessible study areas | Integration of building systems
LOCATION
Toronto, Ontario
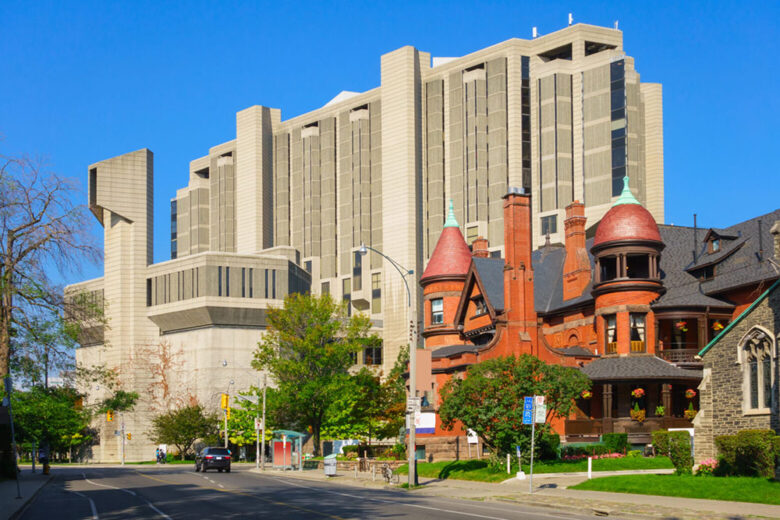
Enhanced environments
The Library renovation is a significant advancement in the modernization of an academic institution, and underscores UofT's dedication to enhancing the built environment for all users.
City of Mississauga
Burnhamthorpe Community Centre Renovation and Expansion
The Community Centre features a state-of-the-art aquatic centre as well as an equipment-based fitness centre. This is the first project designed and built to Mississauga's corporate Green Building standard. The project has also achieved Level 1 CGBS and incorporates net zero and passive house principles, a high-performance building envelope, triple glazing, and a green roof.
HH Angus played a key role in this project, providing mechanical and electrical engineering services, as well as security, IMIT, lighting, AV, and plumbing design. The addition includes a new 25-metre, 6-lane pool, therapeutic pool, fitness centre, and common areas, for a total of 43,000 ft2 of added amenities.
Renovations to the existing community centre encompass improvements across 65,000 ft2, repurposing and relocating multi-purpose program spaces, gymnasium, indoor arena, and upgrading facilities to meet accessibility and green development standards. Despite challenges posed in connecting to the existing building, the addition was situated on the northeast corner, utilizing space from the adjacent park.
To see more renovations, click here
SERVICES
Mechanical Engineering | Electrical Engineering | Plumbing Design | Lighting Design | Audio-Visual Design | Security Design | IMIT Design
PROJECT FEATURES
Green facility design to LEED Silver standard | State-of-the-art aquatic centre | Equipment-based fitness centre | Status: Completed 2024
LOCATION
Mississauga, Ontario
KEY SCOPE ELEMENTS
Project built to Mississauga's Green Building standard | Achieved Level 1 CGBC | Addition connected to existing recreation centre | Renovations and upgrades to existing building
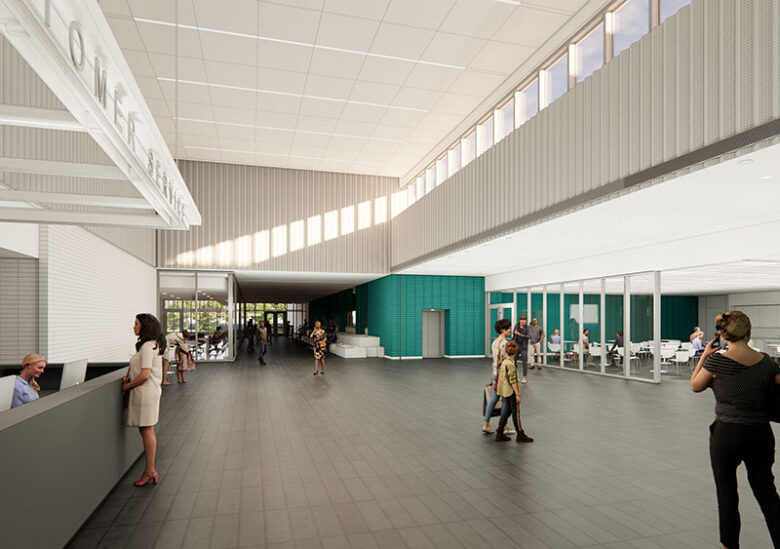
All images courtesy of CS&P Architects
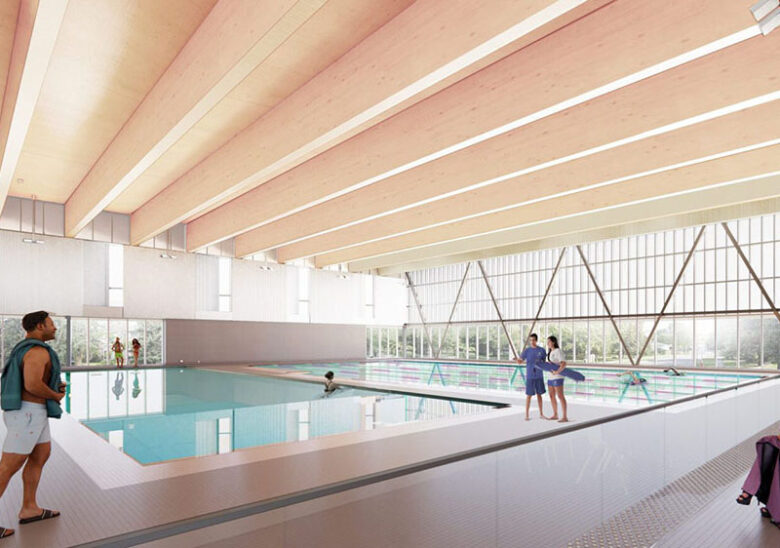
Toronto Western Hospital
New Patient and Surgical Tower
University Health Network’s (UHN) new $1 billion, 15-storey patient care and surgical tower will be built on Toronto Western Hospital’s (TWH) campus in downtown Toronto and enhance UHN’s capabilities caring for complex neurological and orthopedic cases.
We’re excited to be part of this important and transformative healthcare project for UHN. HH Angus, in partnership with DIALOG, is providing mechanical and electrical engineering and ICAT/IMIT design services for the new tower.
The new facility will be over 380,000 ft2 in size over 15-storeys and include 11 clinical program floors, 82 beds, and 20 operating rooms of which three will be hybrid ORs with cutting-edge imaging capabilities.
The new tower will feature many of the latest healthcare technological advancements. We have supported UHN in developing a Digital Strategy for this facility and, have incorporated technologies such as real-time locating systems for patient journey tracking, advanced audio-visual systems for information sharing, and surgical suite technologies to improve flow, communication and educational opportunities.
Among the electrical systems features, emergency generators sized for full backup and a central UPS will improve the resilience of this critical facility.
SERVICES
Mechanical Engineering | Electrical Engineering | ICAT/IMIT Consulting
PROJECT FEATURES
Size: 380,000 ft2 | Budget: $1 billion | 15-storeys | Downtown urban setting | 11 clinical program floors, 82 beds and 20 operating rooms
LOCATION
Toronto, Ontario
KEY SCOPE ELEMENTS
Targeting 32% energy reduction | Wastewater energy transfer (WET) system for heating, cooling, steam and domestic hot water
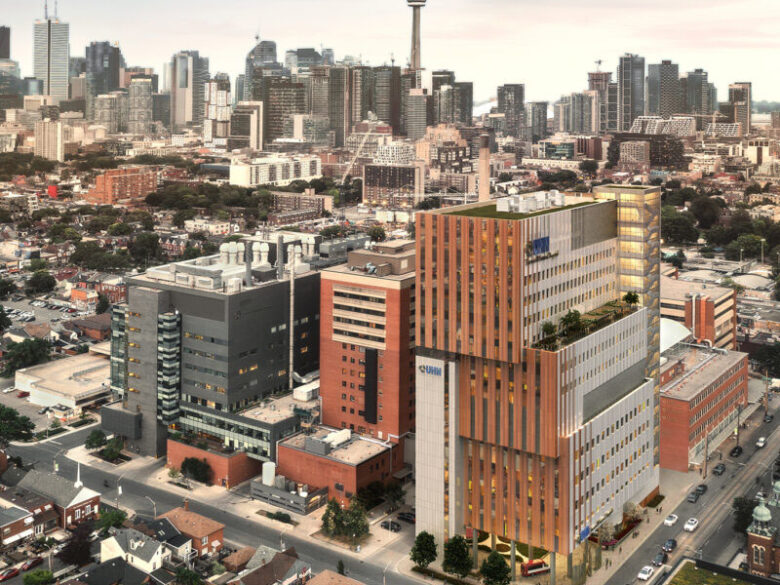
Sustainable Engineering
Building on our decarbonization and sustainability experience for healthcare clients across the country, TWH’s new tower strives to be Net Zero, targeting an overall 32% reduction in energy consumption from the OBC SB-10 (2017) reference model through a variety of initiatives, including integrating with UHN’s wastewater energy transfer system for heating, cooling, steam and domestic hot water. The mechanical design also includes energy recovery wheels on the ventilation system and considerations for predicted future climate conditions.
Proud Partnership
HH Angus is proud to continue collaborating with UHN – ranked number one on the 2023 list of Canada’s Top 40 Research Hospitals – a relationship that spans several decades working on many of their key facilities. Recent collaborations include a major upgrade at TWH’s Power House, which significantly improved the reliability of critical mechanical and electrical infrastructure in order to maintain the integrity of OR services, and the Rapid Assessment Centre Expansion at the Toronto General Hospital.
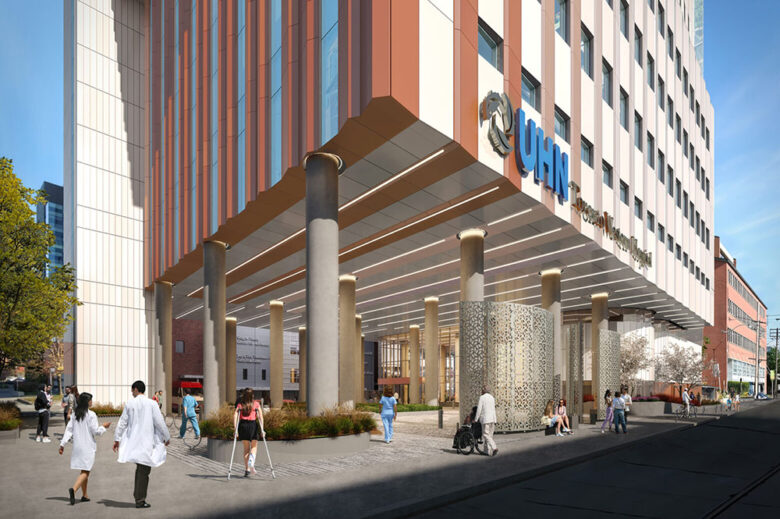
Great Canadian Entertainment
Great Canadian Casino Resort Toronto
The Casino Resort site features live gaming, horse racing, entertainment, and dining on a 33-acre site in the Greater Toronto area. The venue includes two hotels, a theatre, 240 gaming tables and over 2500 electronic gaming machines.
The project consisted of 8 major components, including casino and associated food service outlets (350,000 ft2)., main gaming floor and lobbies, VIP gaming space, support/office spaces, washroom blocks, OPP offices, security offices, etc. The gaming floors feature ~ 2,575 electronic gaming machines and 240 tables. The work also included parking lots, roadways and minor greenspaces, a theatre space and two hotels, each with 400 rooms.
30+ new food service areas meant an additional 1500 pieces of equipment had to be accommodated. This additional load required supplemental electrical connections and, with 33 acres of new build, a completely new electrical feeder from Toronto Hydro.
For telecommunications distribution, HH Angus added redundant site entrance facilities, 30+ new telecoms rooms, and 2 new distribution rooms. The new facility is linked to the existing Grandstand, with the transition of various systems into the new build. A new monitoring suite for the security and surveillance group houses more than 15 operators as well as a new DVR room to service the entire site.
The project required solutions to a number of challenges, chiefly the schedule was of paramount concern for the client. The team worked under tight deadlines to ensure the casino design was completed in a timely fashion in order to welcome customers as quickly as possible. To accommodate the accelerated schedule, strategies were developed to save time during design in order to speed construction.
The fast-tracked schedule challenged communications as well, in terms of turnaround time for decisions. The design team pushed forward to achieve deadlines, but also had to devise procedures to accommodate lagging feedback. This also applied to the construction teams. HH Angus’ deep experience with the client and site enabled a “short hand” which afforded us the flexibility to leave blank areas in the design and come back to these once a decision was made. This saved design resources, and the client appreciated that assumptions were made to allow the project to keep moving forward, and that it did not interfere with our ability to modify designs when decisions were finalized.
The main challenge for the IT and security components involved integrating all stakeholder requirements from the existing Grandstand into the new facility. As these groups have varied approaches to design, our previous projects and site knowledge helped to clarify the final requirements.
The client is developing multiple casino properties throughout Ontario concurrent with the Casino Toronto project, and wanted to apply lessons learned. This created an evolving security standard and, in order to accommodate this, the HH Angus design team deferred changes as long as possible (without impacting the site) in order to reduce the need to re-issue drawings and specifications.
SERVICES
Electrical Engineering | ICAT/Security Design | Lighting Design
PROJECT FEATURES
33 acres with over 1.4 million ft2 of indoor space | Status – Current phase completed 2023
LOCATION
Toronto, Ontario
KEY SCOPE ELEMENTS
Fast-track schedule| 30+new food service areas | Over two dozen new telecom rooms | Gaming floor engineering required the least possible impact on gaming machines to minimize downtime | IT and security components were integrated from existing grand-stand into new facility

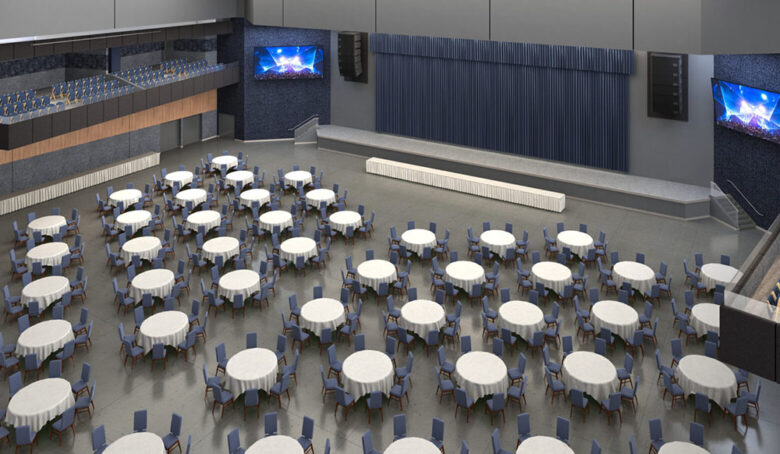
Multi-purpose 110,00 ft2 theatre
This space houses traditional stage events, and can accommodate trade shows and sports such as centre ring (boxing) events, conferences, and celebrations. In the traditional stage configuration, the theatre features 5000 seats. The space also houses several bars and a full event kitchen. The kitchen and bars have over 150 pieces of equipment requiring specialized electrical connections with flexibility for future bar installations.
Rest and relaxation for the whole family
The 600,000 ft2 parking structure is a 6-storey parkade, with 5,500 parking spots. Both the underground parking and the parkade include EV charging stations. The underground parking encompasses the entire lower level of the Casino, both hotels and the theatre, as well as the major mechanical, electrical and IT/Security spaces. There are 5 major high voltage rooms with various smaller electrical rooms throughout, and a generator room housing three 1500kW diesel generator units, with a separate generator synchronization switchboard room.
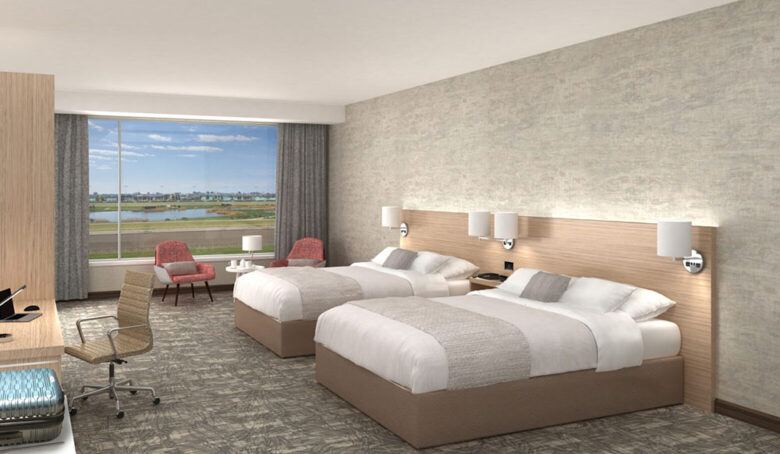
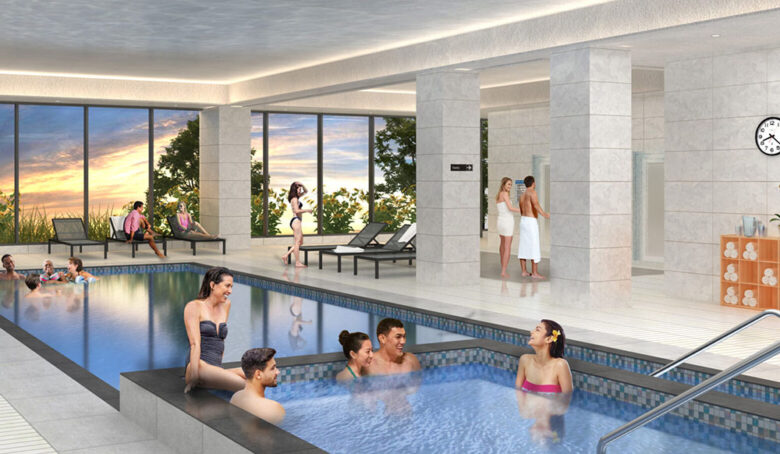
University Health Network
Toronto Western Hospital Critical Infrastructure Reliability Project
Toronto Western Hospital (TWH), part of the University Health Network, initiated a project to enhance the reliability of its critical mechanical and electrical (M&E) infrastructure. With aging equipment dating back to 1954, TWH partnered with HH Angus to undertake a comprehensive upgrade project aimed at ensuring the continuous operation of high-risk medical services.
As the prime consultant, HH Angus was responsible for assessing the condition of existing mechanical and electrical systems. Following the assessment, upgrades were made to the facility, including replacing emergency generators, and establishing a new electrical room serving the ORs and the broader hospital campus. Subconsultants, including architectural, civil, environmental, and cost consultants, played crucial roles throughout the project.
To determine suitable locations for generators, extensive investigations were conducted, including structure analysis, examination of building codes, and assessment of environmental impacts. This collaborative effort led to the approval of a new penthouse above the East Wing for generator placement. The final engineering package involved locating the emergency generators at grade in a new fenced area, alongside the supply and installation of two new 1100W emergency generators and upgrades to the electrical network and distribution systems within the powerhouse.
HH Angus leveraged reality capture workflows, utilizing photogrammetry and a Matterport Pro2 camera, to produce a digital 3D model of the powerhouse and infrastructure. Through the efforts of our BIM team, 3D scans were taken of mechanical and electrical spaces, including complex piping and ductwork, to generate point clouds for reference in Revit. These models accurately depict existing systems, including central steam, chilled water, and emergency power systems serving the hospital's ORs and surrounding campus.
Additionally, the project has been recognized for excellence, with the generator exhaust stack winning in the category of Steel Works – Sculptures – Outdoor Pavilions at the Canadian Institute of Steel Construction's Awards for Excellence. https://hhangus.com/award-for-excellence/
The Toronto Western Hospital Critical Infrastructure Reliability project exemplifies HH Angus's commitment to delivering reliable solutions for healthcare facilities.
SERVICES
Mechanical Engineering | Electrical Engineering | Reality Capture
PROJECT FEATURES
3D modeling of powerhouse |
Scans of mechanical and electrical (M&E) spaces using Matterport Pro2 Camera | Point clouds of complex spaces using ReCap Pro Status: Completed
LOCATION
Eastern Canada
KEY SCOPE ELEMENTS
Upgraded mechanical and electrical systems | Installed emergency generators | Ensured environmental compliance | Modernized the powerhouse infrastructure.