Service: Information and Communications Technology
Toronto Western Hospital
New Patient and Surgical Tower
University Health Network’s (UHN) new $1 billion, 15-storey patient care and surgical tower will be built on Toronto Western Hospital’s (TWH) campus in downtown Toronto and enhance UHN’s capabilities caring for complex neurological and orthopedic cases.
We’re excited to be part of this important and transformative healthcare project for UHN. HH Angus, in partnership with DIALOG, is providing mechanical and electrical engineering and ICAT/IMIT design services for the new tower.
The new facility will be over 380,000 ft2 in size over 15-storeys and include 11 clinical program floors, 82 beds, and 20 operating rooms of which three will be hybrid ORs with cutting-edge imaging capabilities.
The new tower will feature many of the latest healthcare technological advancements. We have supported UHN in developing a Digital Strategy for this facility and, have incorporated technologies such as real-time locating systems for patient journey tracking, advanced audio-visual systems for information sharing, and surgical suite technologies to improve flow, communication and educational opportunities.
Among the electrical systems features, emergency generators sized for full backup and a central UPS will improve the resilience of this critical facility.
SERVICES
Mechanical Engineering | Electrical Engineering | ICAT/IMIT Consulting
PROJECT FEATURES
Size: 380,000 ft2 | Budget: $1 billion | 15-storeys | Downtown urban setting | 11 clinical program floors, 82 beds and 20 operating rooms
LOCATION
Toronto, Ontario
KEY SCOPE ELEMENTS
Targeting 32% energy reduction | Wastewater energy transfer (WET) system for heating, cooling, steam and domestic hot water
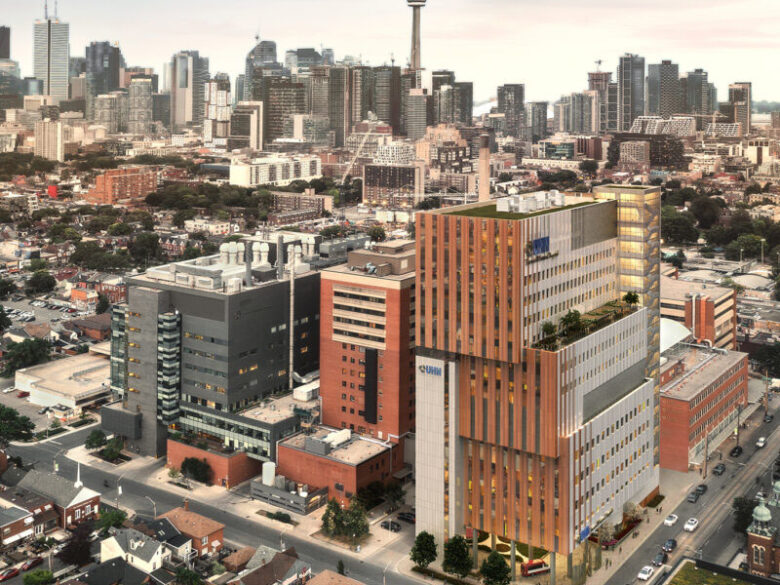
Sustainable Engineering
Building on our decarbonization and sustainability experience for healthcare clients across the country, TWH’s new tower strives to be Net Zero, targeting an overall 32% reduction in energy consumption from the OBC SB-10 (2017) reference model through a variety of initiatives, including integrating with UHN’s wastewater energy transfer system for heating, cooling, steam and domestic hot water. The mechanical design also includes energy recovery wheels on the ventilation system and considerations for predicted future climate conditions.
Proud Partnership
HH Angus is proud to continue collaborating with UHN – ranked number one on the 2023 list of Canada’s Top 40 Research Hospitals – a relationship that spans several decades working on many of their key facilities. Recent collaborations include a major upgrade at TWH’s Power House, which significantly improved the reliability of critical mechanical and electrical infrastructure in order to maintain the integrity of OR services, and the Rapid Assessment Centre Expansion at the Toronto General Hospital.
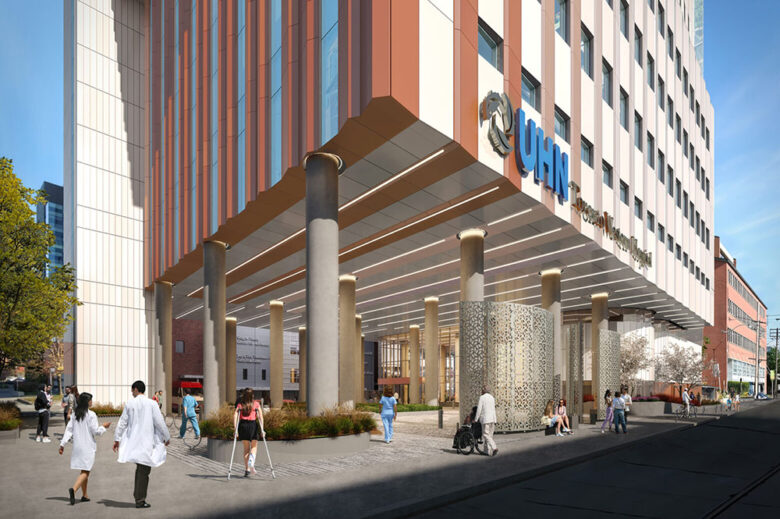
Great Canadian Entertainment
Great Canadian Casino Resort Toronto
The Casino Resort site features live gaming, horse racing, entertainment, and dining on a 33-acre site in the Greater Toronto area. The venue includes two hotels, a theatre, 240 gaming tables and over 2500 electronic gaming machines.
The project consisted of 8 major components, including casino and associated food service outlets (350,000 ft2)., main gaming floor and lobbies, VIP gaming space, support/office spaces, washroom blocks, OPP offices, security offices, etc. The gaming floors feature ~ 2,575 electronic gaming machines and 240 tables. The work also included parking lots, roadways and minor greenspaces, a theatre space and two hotels, each with 400 rooms.
30+ new food service areas meant an additional 1500 pieces of equipment had to be accommodated. This additional load required supplemental electrical connections and, with 33 acres of new build, a completely new electrical feeder from Toronto Hydro.
For telecommunications distribution, HH Angus added redundant site entrance facilities, 30+ new telecoms rooms, and 2 new distribution rooms. The new facility is linked to the existing Grandstand, with the transition of various systems into the new build. A new monitoring suite for the security and surveillance group houses more than 15 operators as well as a new DVR room to service the entire site.
The project required solutions to a number of challenges, chiefly the schedule was of paramount concern for the client. The team worked under tight deadlines to ensure the casino design was completed in a timely fashion in order to welcome customers as quickly as possible. To accommodate the accelerated schedule, strategies were developed to save time during design in order to speed construction.
The fast-tracked schedule challenged communications as well, in terms of turnaround time for decisions. The design team pushed forward to achieve deadlines, but also had to devise procedures to accommodate lagging feedback. This also applied to the construction teams. HH Angus’ deep experience with the client and site enabled a “short hand” which afforded us the flexibility to leave blank areas in the design and come back to these once a decision was made. This saved design resources, and the client appreciated that assumptions were made to allow the project to keep moving forward, and that it did not interfere with our ability to modify designs when decisions were finalized.
The main challenge for the IT and security components involved integrating all stakeholder requirements from the existing Grandstand into the new facility. As these groups have varied approaches to design, our previous projects and site knowledge helped to clarify the final requirements.
The client is developing multiple casino properties throughout Ontario concurrent with the Casino Toronto project, and wanted to apply lessons learned. This created an evolving security standard and, in order to accommodate this, the HH Angus design team deferred changes as long as possible (without impacting the site) in order to reduce the need to re-issue drawings and specifications.
SERVICES
Electrical Engineering | ICAT/Security Design | Lighting Design
PROJECT FEATURES
33 acres with over 1.4 million ft2 of indoor space | Status – Current phase completed 2023
LOCATION
Toronto, Ontario
KEY SCOPE ELEMENTS
Fast-track schedule| 30+new food service areas | Over two dozen new telecom rooms | Gaming floor engineering required the least possible impact on gaming machines to minimize downtime | IT and security components were integrated from existing grand-stand into new facility

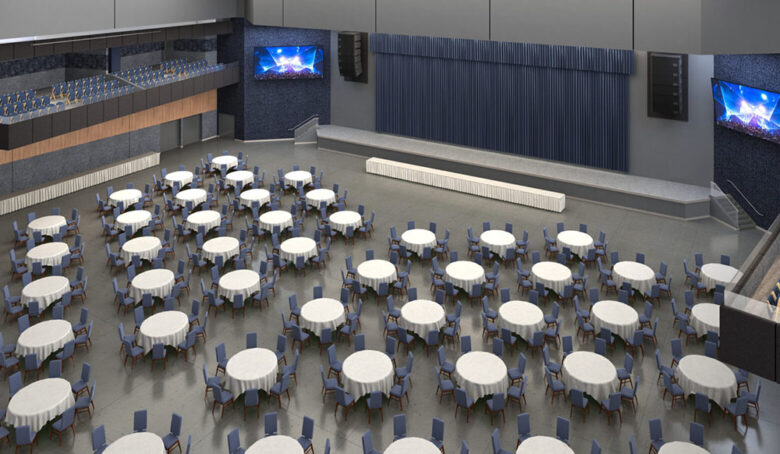
Multi-purpose 110,00 ft2 theatre
This space houses traditional stage events, and can accommodate trade shows and sports such as centre ring (boxing) events, conferences, and celebrations. In the traditional stage configuration, the theatre features 5000 seats. The space also houses several bars and a full event kitchen. The kitchen and bars have over 150 pieces of equipment requiring specialized electrical connections with flexibility for future bar installations.
Rest and relaxation for the whole family
The 600,000 ft2 parking structure is a 6-storey parkade, with 5,500 parking spots. Both the underground parking and the parkade include EV charging stations. The underground parking encompasses the entire lower level of the Casino, both hotels and the theatre, as well as the major mechanical, electrical and IT/Security spaces. There are 5 major high voltage rooms with various smaller electrical rooms throughout, and a generator room housing three 1500kW diesel generator units, with a separate generator synchronization switchboard room.
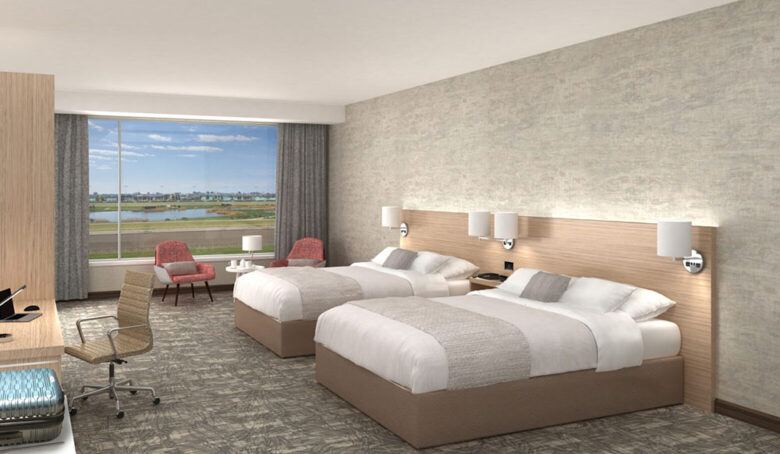
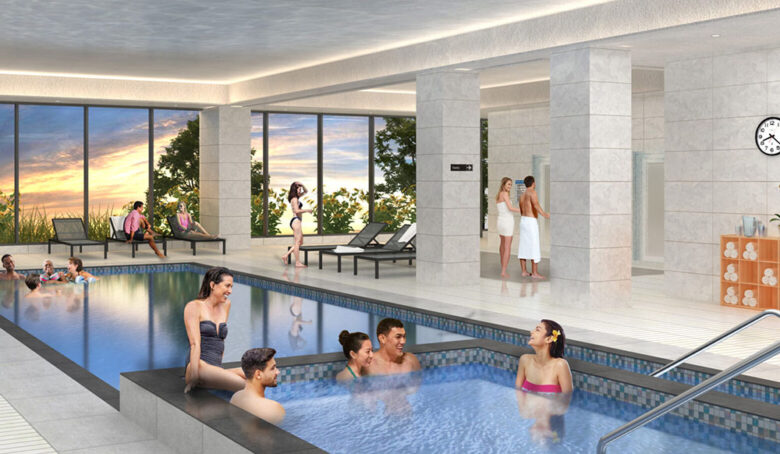
Fanshawe College
IoT Data Lake
The College’s overarching goal was to streamline their data management process by consolidating disparate IoT platforms into a single accessible platform for measurement and research.
Fanshawe College needed a comprehensive data lake for all campus IoT data, beginning with two solar panel arrays. Their existing process involved physically going to each building’s measurement platform to download its data, merge the information in Excel format and perform a manual analysis.
HH Angus served as smart building consultants to the project, providing digital design services. We reprogrammed the PLCs (programmable logic controllers) of the solar panel arrays, enabling data transmission to AWS IoT core. The resulting data is now stored in a data lake where it is presented with analysis on a centralized dashboard, providing a unified and efficient solution to the College’s data management challenges.
One of the challenges of the project centered on communications and technical access. Collaboration with multiple academic and IT departments proved challenging due to communication issues with various stakeholders involved in the original solar panel array. To address this, our team coordinated multi-department troubleshooting meetings, fostering a collaborative atmosphere that was focused on progress.
Also, gaining access to the PLCs for essential programming changes became complicated due to staff turnover at the client. An unintended consequence of this was that new staff members were unfamiliar with the PLCs. To remedy this, our team assumed more of a technical advisory role than had been anticipated originally, to the point of involving technical support from the PLC manufacturer to assist the College’s technicians. Solving these issues underscores the project team’s adaptability in overcoming unexpected challenges.
SERVICES
Smart Building Consultants
PROJECT FEATURES
Comprehensive data lake for all campus IoT data | Centralized dashboard provides data analysis and data management | Status: Completed 2023, with ongoing maintenance contract
LOCATION
London, Ontario
KEY SCOPE ELEMENTS
Hardware-free data retrieval from solar panels | Reprogrammed PLCs for AWS data transmission | Advanced data analysis with local utility rates
University Health Network
Toronto General Hospital Rapid Assessment Centre (RAC) Expansion
HH Angus was engaged to provide mechanical and electrical engineering, IMIT consulting, and lighting consulting services for this 20,000 ft2 phased renovation at Toronto General Hospital. The space now includes a Rapid Assessment Centre, Diagnostic Test Centre, and Admitting and Pre-Admission Clinics.
The emergency department (ED) was designed to serve ~ 20,000 patients annually but was receiving more than 55,000 patients To better manage these volumes, a dedicated Rapid Assessment Centre (RAC) was added so that ED staff can triage lower acuity patients to the new "fast track" area, enabling primary emergency areas to care for more complex patients. Our team worked in conjunction with the client and other consultants to perform a pre-tender constructability review. This review included potential approaches to minimize disruption outside areas of construction, identify potential installation challenges, and complete pre-demolition of the first phase of work to identify any unknown site conditions in advance of construction. Due to the age of the existing space, there was a high probability of building systems and equipment being beyond their service life, and a certainty that codes and standards relevant to the design of the new space had changed. To address this and mitigate any risks, HH Angus performed a pre-design review to identify any specific potential issues with the new space and recommend steps to further address the unknowns. Scanning and 3D captures were performed regularly throughout construction, using Matterport Pro 2 and a Theta V 360 Camera. This provided the client with regular site progress updates and, in future, will allow for dimensionally accurate references for locating MEP services behind walls and ceilings. It also allowed for a more focused presence on-site, as construction progress was made available remotely to a range of project stakeholders amid COVID-19 pandemic restrictions. The existing ventilation systems presented a significant gap for the project, as their capacity to support the new functions of the space was unknown. To address this, HH Angus investigated and presented several options for review, taking into consideration the client’s budget, schedule, and planned upgrades for existing infrastructure.
|
SERVICES
Mechanical Engineering | Electrical Engineering | IMIT Consultant | Lighting Consultant
PROJECT FEATURES
Accelerated project schedule | Status: Completed 2022
LOCATION
Toronto, Ontario
KEY SCOPE ELEMENTS
Phased renovation | Pre-tender constructability review and pre-design review | Scanning and 3D captures to document site progress and provide dimensionally accurate site references for future access
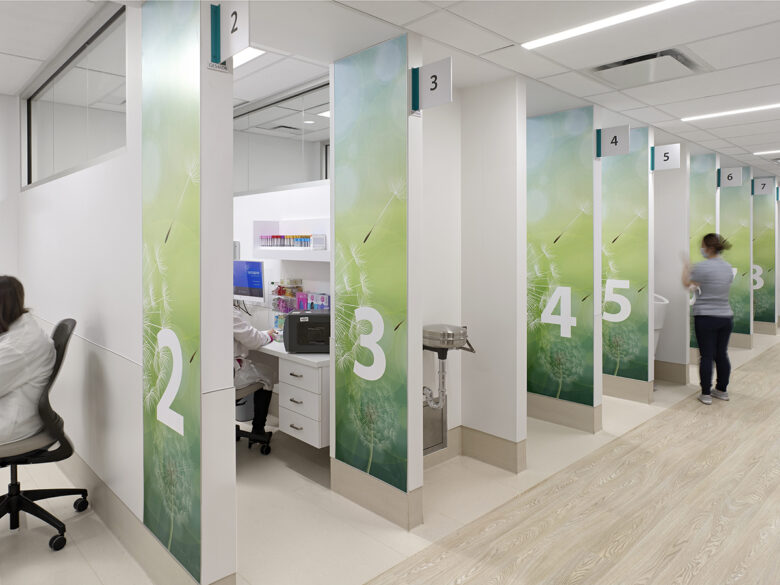
Accelerated schedule
The project schedule was aggressive, requiring close and efficient collaboration between HH Angus, the client, and all other consultants. All construction documents and constructability reviews were completed in 12 weeks.
WPP
Toronto Waterfront Campus
WPP Group's building is part of the largest urban revitalization project in North America, bringing together new businesses, restaurants, and transport connections.
Work Design Magazine March 28, 2023
This cutting-edge project on Toronto’s downtown waterfront represents an evolution in commercial office development and reinvents how employees work together in Toronto’s rapidly evolving creative and technology sectors. The new space merges a large number of WPP’s operating companies and 2,000 employees into the top seven floors of the Waterfront Innovation Centre at the city’s iconic ‘Sugar Beach’. HH Angus provided engineering consulting services for this 250,000 ft2 tenant fitout project. WPP is the anchor tenant for the Waterfront Innovation Centre.
The fitout included raised floors for underfloor HVAC systems and is targeting LEED Platinum certification. On each floor, the design features a café, hub and IT equipment room, with one single Main Communications Room.
The 8th floor has a custom production area with very specific acoustic requirements. Our mechanical team worked closely with the acoustical consultant to provide a design that meets the strict acoustic requirements for video and audio production and recording. This was achieved through careful placement of fan-powered boxes equipped with silencers. The production area includes multimedia studios, photo studios and a print lab. Lighting control for these rooms is enhanced with tunable lighting, allowing users to adjust the colour temperature in real time.
The 10th floor is the client-facing floor and includes meeting rooms with fully-integrated AV, smart lighting control, open ceiling design concept (industrial design), a large point-of-sale catering kitchen with back of house facilities and an outdoor terrace.
Our communications team designed several interconnecting fibre risers to provide the client with the most cost effective solution and full redundancy to meet their current and future needs, and to ensure the system will continue to operate in the event of external critical failures.
SERVICES
Mechanical Engineering | Electrical Engineering | Communications Design
PROJECT FEATURES
250,000 ft2 colocation project unifying 28 different companies | Seven-floor fitout | Status: Completed 2022
LOCATION
Toronto, Ontario
KEY SCOPE ELEMENTS
WELL design principles | Pressurized raised floor systems with underfloor HVAC systems | Rigorous acoustic requirements for audio and video recording | Redundant interconnecting communications fibre risers to ensure system will operate in the event of external critical failures
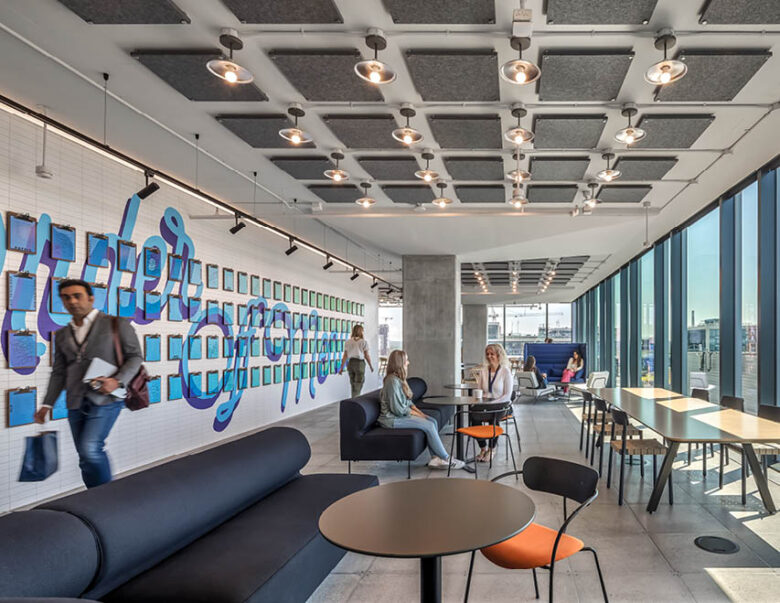
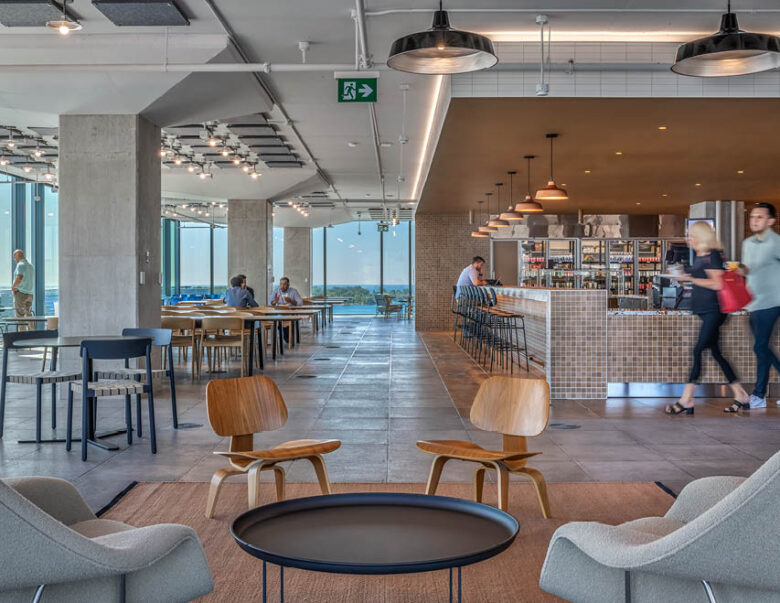