Service: Lighting Design
Confidential Client
Quebec Data Centre
HH Angus provided comprehensive engineering services for the design, development, and implementation of a state-of-the-art data centre.
HH Angus was responsible for the design of the facility’s mechanical, plumbing, lighting, fire protection and building environmental control systems. This facility is split into critical and non-critical areas. The critical areas included mechanical and electrical rooms housing equipment supporting the main server spaces. The non-critical areas included administrative spaces such as meeting rooms, open offices, telecommunication service entry rooms, technical spaces housing servers supporting site operations, and a loading dock. Beyond the footprint of this building, our scope of services also extended to ancillary site structures such as the main gate guardhouse, water treatment buildings, fire pump buildings, and the deployment of private weather stations.
HH Angus implemented an evaporative cooling system to support critical IT servers. Our team designed a water treatment facility and rainwater harvesting system with a detailed metering scheme, giving the Owner visibility into water use. This made the facility water-neutral and self-sufficient year-round, eliminating reliance on municipal water for cooling.
SERVICES
Mechanical Engineering | Lighting Design | Fire Protection | Building & Environmental Systems
PROJECT FEATURES
N+1 redundant mechanical systems
to ensure continuous uptime | Completed March 2026
LOCATION
Confidential, Quebec
KEY SCOPE ELEMENTS
Feasibility study | Energy modeling | Facility design to eliminate reliance on municipal water for cooling
The Co-operators Calgary
Tenant Fitout
This project focused on a tenant renovation of two floors in The Co-operators' newly-acquired downtown Calgary office space, and comprised 40,000 square feet. The project has been certified WELL Gold.
Our approach included early coordination with the landlord to ensure handover conditions suited the client’s requirements, as well as close coordination with the construction manager in creating a pre-order due to a condensed construction schedule.
The construction schedule was a key challenge of the project along with the timing of tender. The completion date was an unmovable milestone as the client’s lease was expiring at their other location. At time of tender, product and material availability were fluctuating, which created uncertainty around delivery. To meet the deadline, our team was tasked to do everything possible to ensure the success of the project and keep the schedule on track.
To help ensure timely delivery, our team incorporated a pre-order package for the construction manager to tender, which allowed products to be reviewed and released ahead of the official tender. This effort was successful and was completed according to plan; however, some delivery delays were unavoidable, due to market conditions. To mitigate the impact, we were then tasked with contacting industry partners to help expedite deliveries. In addition, alternative temporary designs were implemented to ensure the move-in date could be met by planning the switchover date once the outstanding equipment arrived.
The Calgary office marks our fifth tenant improvement project for The Co-operators, following similar fitouts for their locations in Guelph ON and Regina SK, as well as pilot projects in Montreal QC and Burlington ON.
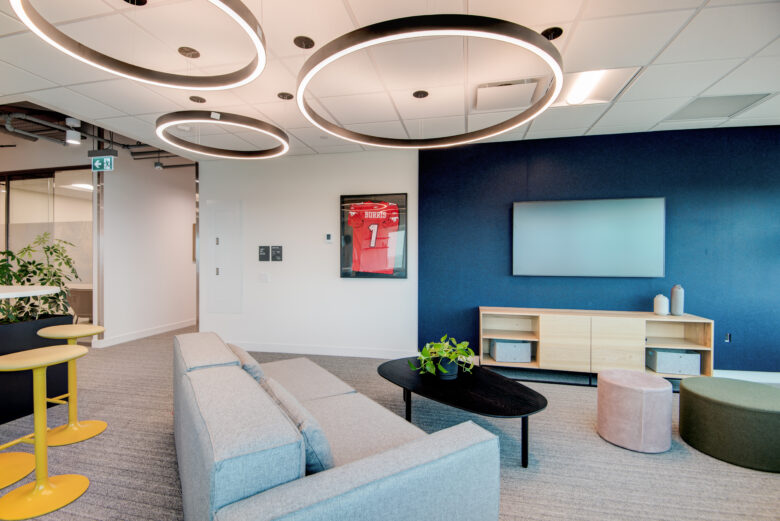
New Lutron lighting control design
New UPS N+1 Design and new LED Lighting Design
SERVICES
Mechanical Engineering | Electrical Engineering | Lighting Design | Communications & Security Design
PROJECT FEATURES
Size: 40,000 ft2 over two floors | Status: Completed 2023
LOCATION
Calgary, Alberta
KEY SCOPE ELEMENTS
Feasibility Study | Tenant renovation | Condensed construction schedule | WELL Gold certified
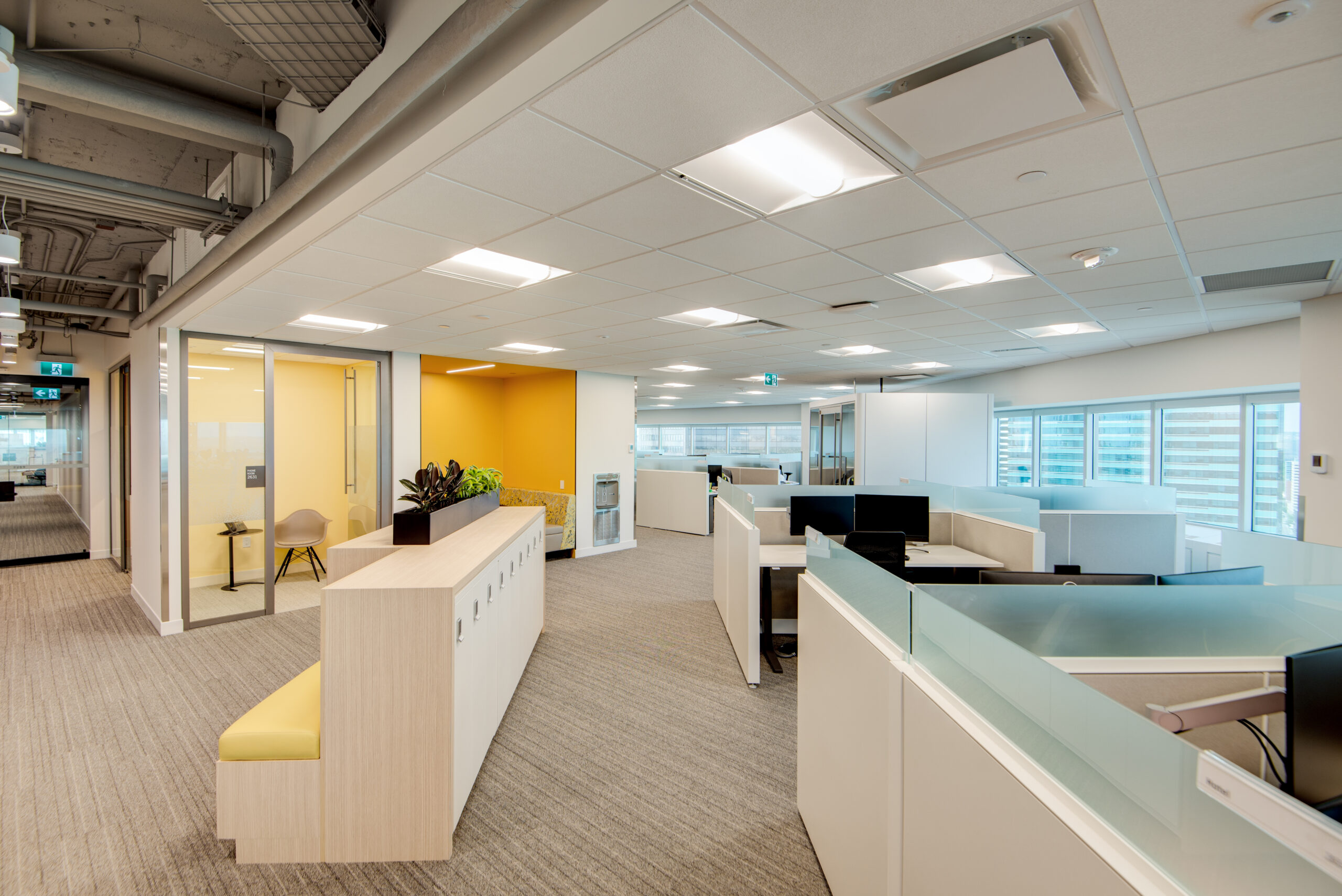
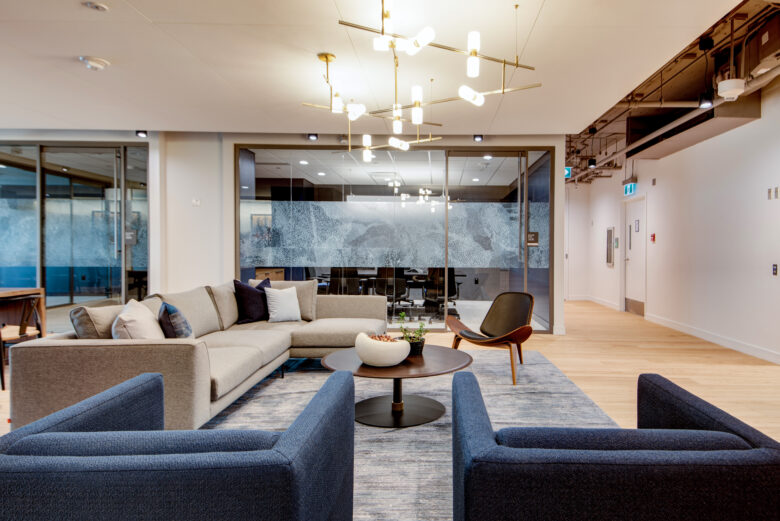
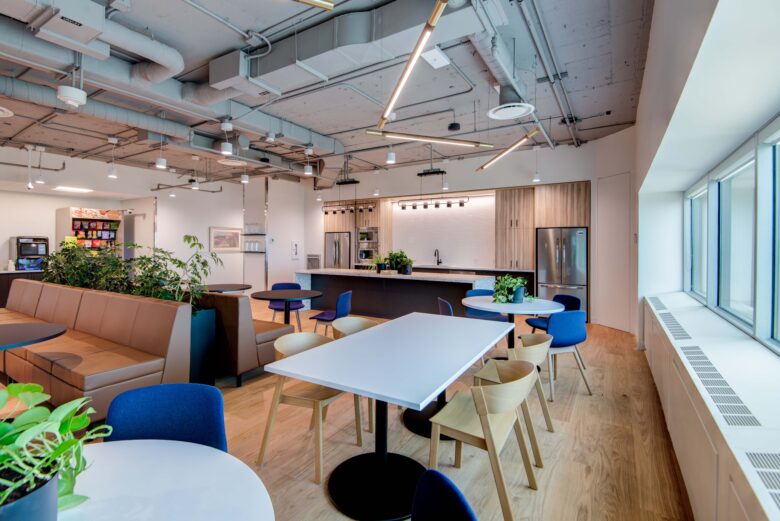
Waypoint Centre for Mental Health Care
Chigamik Community Health Hub
Waypoint Chigamik Mental Health Centre is part of a redevelopment project and replaces two older facilities in use since the 1800s.
The challenges of this project included the requirement that the entire building be completely designed in one stage, rather than proceeding with design packages, plus delays in funding during the design process which resulted in a requirement for both a base building package and a fitout package.
To accomplish this, HH Angus coordinated two tender packages and two building permit submissions. Some detailed specifications in each package were interchangeable for the mechanical and electrical tender process. Working with phased schedules ensured that equipment start-up was fully coordinated between the tender packages.
The project faced additional challenges to provide an energy-efficient HVAC system, due to compliance with CSA Z317.2 and budget restrictions, as well as a small mechanical service space. To overcome these challenges, extensive coordination was implemented throughout the project across all disciplines.
SERVICES
Mechanical Engineering | Electrical Engineering | Lighting Design | ICAT Commissioning
PROJECT FEATURES
Size: 40,000 ft2 | DBFM | Fully ducted HVAC system designed to comply with CSA Z317.2 | Status: Completed 2020
LOCATION
Midland, Ontario
KEY SCOPE ELEMENTS
Building has full back up power with generator sized to accommodate the entire load of the building on loss of utility power conditions
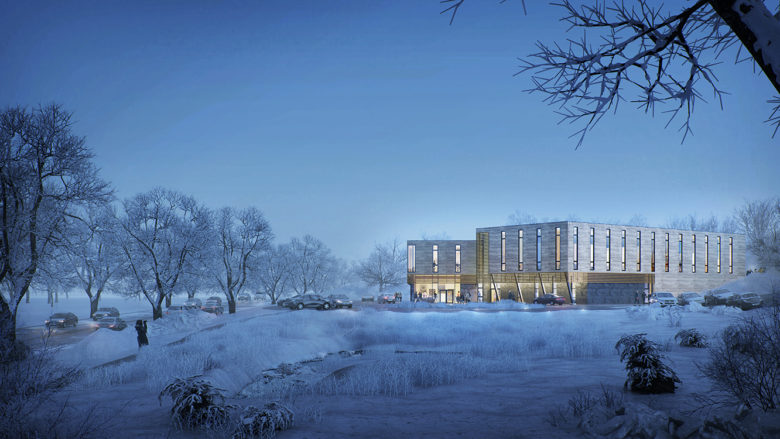
Efficient design
Several engineering designs were reviewed by the project team to ensure compliance with the owner’s goals and restrictions, while achieving an efficient design.
Customized spaces
The two-storey 40,000 ft2 mental health care facility has amenities for indigenous smudging ceremonies, physiotherapy, conferences, a community kitchen, gathering rooms, and a youth programming space.
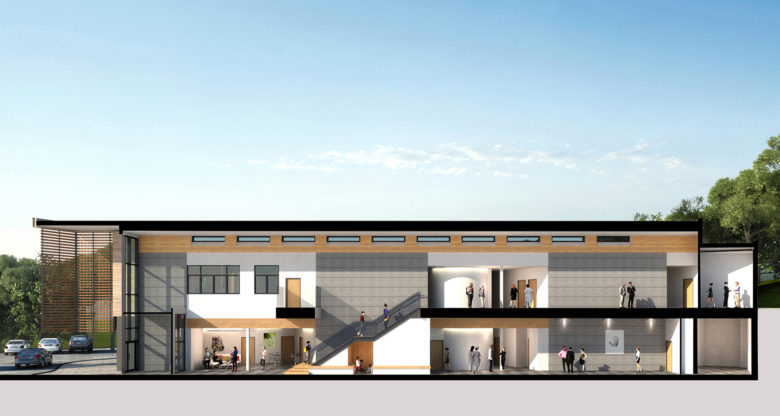
Renderings courtesy of Lett Architects Inc.
University of Toronto
Robarts Library, Reading Room Renovation
The Robarts Library, renowned as an example of the 'Brutalist' style of architecture, stands as one of Canada's largest academic library buildings, serving as a cornerstone of scholarly pursuit at the University of Toronto.
HH Angus provided mechanical and electrical engineering services, as well as design consulting for IMIT and lighting, for the renovation of the Library's fourth floor Reading Room.
The project, aimed at modernizing the library's facilities to accommodate contemporary learning paradigms, posed several intricate challenges. One notable challenge involved the intricate design of cabling for security and telecoms within the limited capacity channels of the floor slab, while ensuring the preservation of the library's architectural integrity. Moreover, the integration of wireless thermostats for HVAC control demanded meticulous planning to guarantee effective functionality while maintaining the library's iconic aesthetic.
In response to the evolving needs of the campus community, the renovated space has been thoughtfully curated to foster a conducive environment for study, collaboration, and digital scholarship. Individual study areas, equipped with state-of-the-art digital stations and consultation rooms, offer students and faculty alike the resources they need to thrive academically. Additionally, the incorporation of light therapy zones underscores a commitment to promoting wellness and inclusivity within the Library's patrons.
Improved accessibility was a key aspect of this renovation, featuring new study spots with adjustable desk heights, versatile seating configurations, and customizable lighting options, ensuring that all user's needs are considered. As well, strategic wayfinding elements and clear sightlines have been implemented to facilitate seamless navigation throughout the revitalized space.
SERVICES
Mechanical Engineering | Electrical Engineering | IMIT Consultant | Lighting Consultant
PROJECT FEATURES
20,300 ft2 space | Accessible study areas | Integration of building systems
LOCATION
Toronto, Ontario
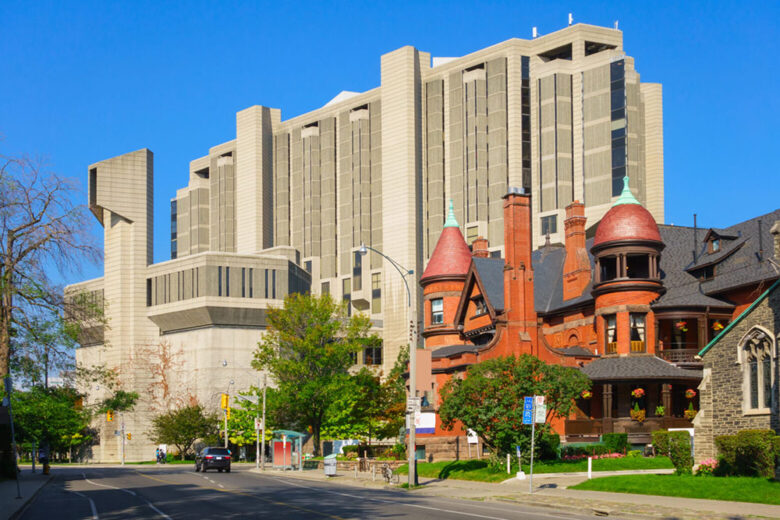
Enhanced environments
The Library renovation is a significant advancement in the modernization of an academic institution, and underscores UofT's dedication to enhancing the built environment for all users.
City of Mississauga
Burnhamthorpe Community Centre Renovation and Expansion
The Community Centre features a state-of-the-art aquatic centre as well as an equipment-based fitness centre. This is the first project designed and built to Mississauga's corporate Green Building standard. The project has also achieved Level 1 CGBS and incorporates net zero and passive house principles, a high-performance building envelope, triple glazing, and a green roof.
HH Angus played a key role in this project, providing mechanical and electrical engineering services, as well as security, IMIT, lighting, AV, and plumbing design. The addition includes a new 25-metre, 6-lane pool, therapeutic pool, fitness centre, and common areas, for a total of 43,000 ft2 of added amenities.
Renovations to the existing community centre encompass improvements across 65,000 ft2, repurposing and relocating multi-purpose program spaces, gymnasium, indoor arena, and upgrading facilities to meet accessibility and green development standards. Despite challenges posed in connecting to the existing building, the addition was situated on the northeast corner, utilizing space from the adjacent park.
To see more renovations, click here
SERVICES
Mechanical Engineering | Electrical Engineering | Plumbing Design | Lighting Design | Audio-Visual Design | Security Design | IMIT Design
PROJECT FEATURES
Green facility design to LEED Silver standard | State-of-the-art aquatic centre | Equipment-based fitness centre | Status: Completed 2024
LOCATION
Mississauga, Ontario
KEY SCOPE ELEMENTS
Project built to Mississauga's Green Building standard | Achieved Level 1 CGBC | Addition connected to existing recreation centre | Renovations and upgrades to existing building
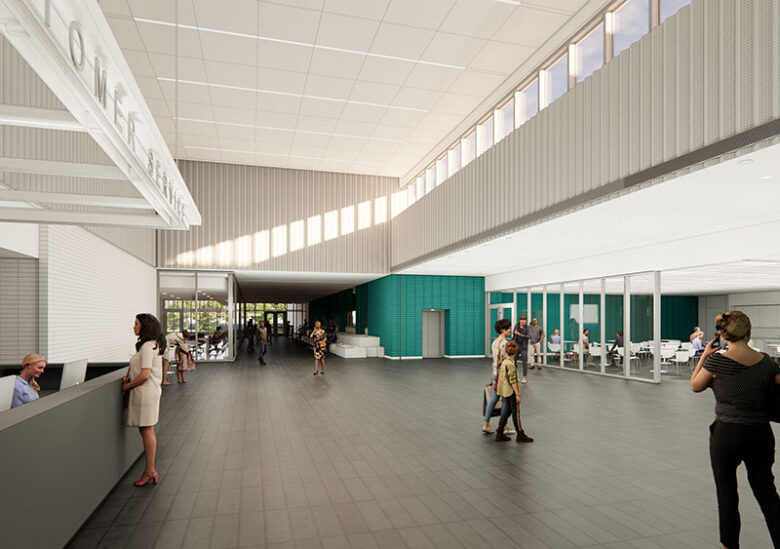
All images courtesy of CS&P Architects
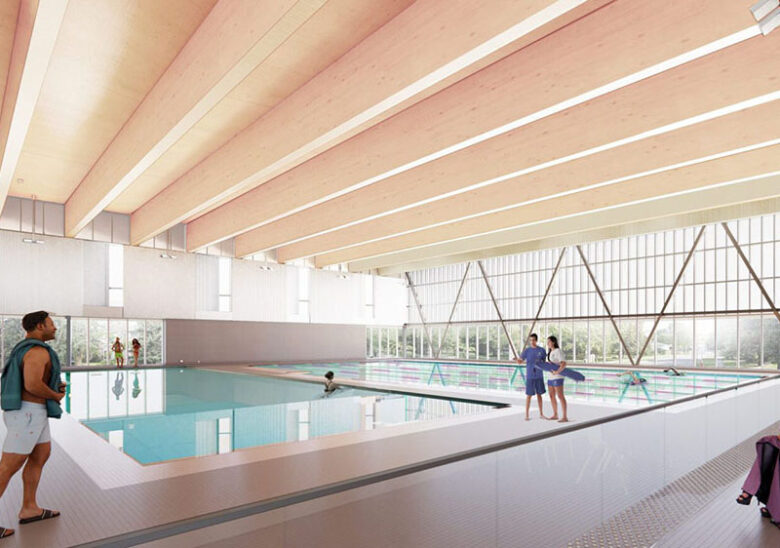