Service: Prime Consultant
Sunnybrook Health Sciences Centre
Space Optimization Study Using AWS QuickSight
Sunnybrook Health Sciences Centre, a leading healthcare provider in Toronto, was seeking to address challenges in medical space utilization. With a diverse array of clinical services and bookable exam rooms, Sunnybrook faced challenges understanding a perceived shortage of space. Yet, intermittent observations suggested that many exam rooms were frequently empty.
M6 – Multipurpose Clinical Space | Yuval & Lori Barzakay Brain Health Clinic Study
To gain a clearer understanding of space utilization and identify potential inefficiencies, Sunnybrook partnered with HH Angus, leveraging our expertise in digital solutions and innovative engineering. The goal was to implement a robust monitoring system to capture accurate data on room usage, enabling informed decisions on resource allocation.
This project reflects Sunnybrook’s commitment to operational efficiency, ensuring that resources are optimally allocated to improve patient care and support staff needs.
SERVICES
Prime Consultant
PROJECT FEATURES
Digital monitoring system to inform clinical resource allocation | Enhanced operational efficiency | Patient privacy | Scalable design | Predictive analytics
LOCATION
Toronto, Ontario
KEY SCOPE ELEMENTS
Space utilization measurement and analysis | Data acquisition through sensor deployment | Security and connectivity | Data aggregation and storage | Visualization and insights
Solving Space Utilization Challenges
Sunnybrook’s medical staff expressed concerns about limited space availability, particularly for bookable exam rooms. However, casual observations indicated that some rooms appeared to remain empty. Sunnybrook needed a reliable solution to measure actual room usage accurately while addressing two significant concerns:
Privacy: Ensuring patient privacy was paramount, particularly in sensitive clinical settings.
Accurate Detection: Existing solutions struggled to detect minimal motion, such as during procedures like blood transfusions, where patients may remain largely still.
HH Angus was engaged to design and implement a solution capable of addressing these challenges while delivering actionable insights.
Solution | Smart Sensors and AWS Integration
Our Digital Services team developed an innovative solution leveraging cutting-edge sensors and AWS services:
Sensor Deployment:
-
- mmWave Sensors: Initial deployment involved mmWave sensors capable of detecting micro-motions, such as breathing, to confirm room occupancy. These sensors were equipped with cellular SIM cards to operate independently of Sunnybrook’s network.
- 3D Stereoptic Sensors: To further expand the data gathered from the various clinics, the move to 3D-stereoptic sensors was used to provide not just occupancy status of exam rooms, but also the near real-time occupancy count data. Enhancing scalability, these sensors could monitor multiple rooms simultaneously, offering greater hardware efficiency.
Security and Connectivity:
-
- mmWave sensors utilized mTLS (mutual Transport Layer Security) for secure data transmission.
- Custom authorization for 3D-stereoptic sensors was implemented using AWS Lambda.
Data Aggregation and Storage:
-
- Data was streamed via Amazon Data Firehose and AWS IoT Core, stored in AWS S3, and processed through AWS Lambda.
- A centralized S3 data lake provided a secure, scalable repository for all processed data.
Visualization and Insights:
-
- Data queries were conducted using AWS Athena, while AWS QuickSight offered intuitive 2D dashboards for near-real-time analysis with minimal latency.
This comprehensive approach ensured seamless integration, robust data security, and actionable insights for Sunnybrook.
Outcome | Actionable Insights and Future Expansion
The solution provided Sunnybrook with detailed, data-driven insights into space utilization:
Initial Findings: The installation was completed in December 2024, and data collection began in January 2025. Analysis of the 11 monitored exam rooms in Sunnybrook’s M-Wing, conducted from January to March 2025, revealed a surprising utilization rate of only 33%. This insight challenged initial staff assumptions and highlighted opportunities for more efficient space planning.
Future Outlook: New medical clinics, which opened in January 2025, will contribute additional data to further refine Sunnybrook’s understanding of space usage and inform future expansion strategies.
Through this project, Sunnybrook is well-positioned to optimize its clinical spaces, ensuring that resources are allocated effectively to enhance both staff workflows and patient care delivery.
Key Outcomes Summary
Accurate Space Utilization Data: Revealed underutilization of monitored exam rooms, providing actionable insights.
Efficient Resource Allocation: Enabled informed decisions about space planning and allocation.
Scalability: Designed for expansion, with sensors deployed to additional clinics.
Improved Patient Care: Enhanced operational efficiency supports better patient care delivery.
Predictive Analytics: Tool for staff to forecast resourcing needs based on the day of the week using historical trends
Privacy Assurance: Leveraged secure sensor technologies to maintain patient confidentiality.
AWS Services Used
AWS S3 (Simple Storage Service): Acted as the central repository for storing and
retrieving large datasets, facilitating data analysis and accessibility.
AWS IoT Core: Enabled secure, scalable connectivity for IoT devices, allowing for efficient data collection and integration into the cloud.
AWS Athena: Offered an interactive query service to analyze data in Amazon S3 using SQL, simplifying the extraction of actionable insights from complex datasets.
AWS QuickSight: Provided visualization tools and dashboards for business intelligence, enabling Manulife to derive and act upon insights from their data effectively.AWS Lambda: Supported serverless computing, automating data processing and transformation tasks without the need for server management.
Amazon Data Firehose: Streamlined the capture, transformation, and loading of streaming data, ensuring efficient data flow from IoT devices to storage and analysis tools.
AWS IoT Events: Monitored sensor data for specific conditions, facilitating real-time alerting and response mechanisms to optimize building operations.
AWS Step Functions: Orchestrated complex data processing workflows, coordinating the various components of the ETL pipeline for streamlined operation and maintenance.
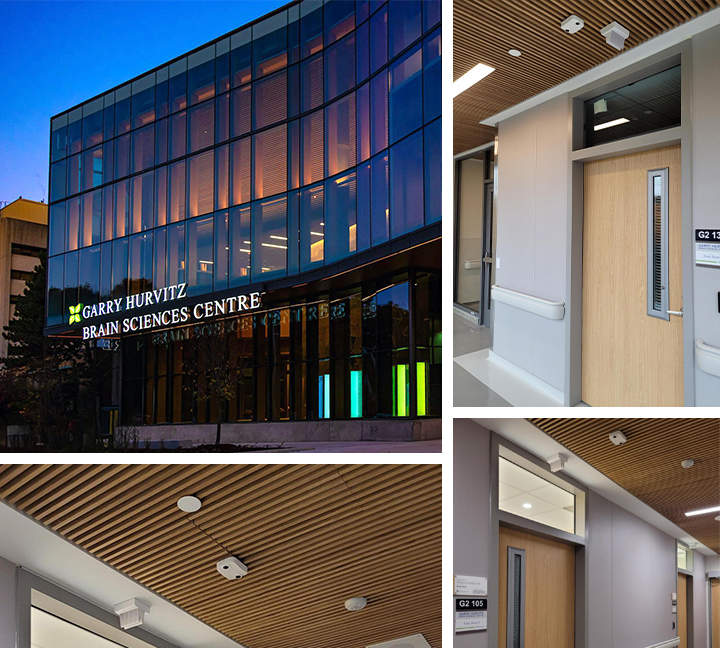
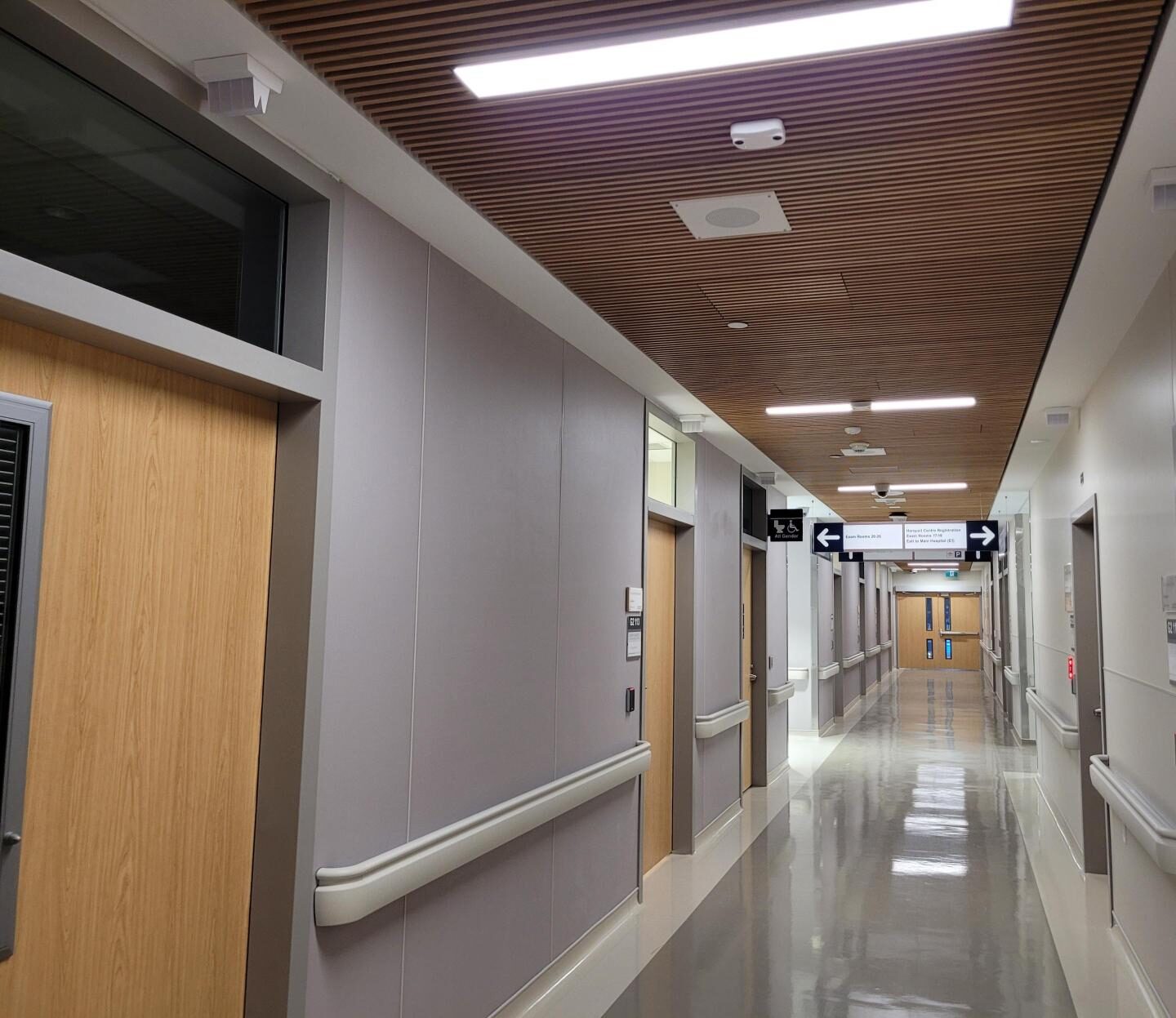
Enwave Energy Corporation
Pearl Street Energy Centre
The Pearl Street Energy Centre project has been honoured with an Award of Distinction at the Ontario Engineering Project Awards by the Association of Consulting Engineering Companies (ACEC).
Buildings in Toronto generate more than half of the city's greenhouse gas emissions. New technologies, like Enwave's expanded heat delivery system, will play a critical role in reducing our cumulative carbon footprint.
This project exemplifies cutting-edge engineering and design, integrating robust energy solutions that challenge traditional methods. Our focus on sustainable and efficient energy use through advanced engineering practices not only supports but advances the environmental goals of urban energy systems. HH Angus was the Prime Consultant and Mechanical and Electrical Design Engineers for the Pearl Street Energy Centre (PSEC) project. We also acted as the design team project managers.
When fully utilized, Enwave's low carbon heating facility will provide enough low-carbon heating to reduce emissions in Toronto by approximately 11,600 tCO2e, the equivalent of converting over 10 million square feet of office space to net zero.
As part of the TransformTO Climate Action Plan, which outlines ways to improve the city’s health, grow the economy and improve social equity, district energy was identified as a key strategy. In 2017, Enwave was selected as a partner by Toronto’s City Council to help accelerate the implementation of the plan to reduce greenhouse gas emissions and make the city more resilient.
Enwave’s district energy system is the largest in North America. It serves 180 buildings comprising more than 40 million square feet through 4 interconnected downtown plants and 40 kilometres of underground pipes. The addition of the PSEC to the district energy system will expand Toronto’s district heating and cooling distribution and capacity using low carbon technologies, by installing 3600 tons of cooling and 62,000 Mbh (thousand BTU’s per hour) of heating using water source heat pumps (heat reclaim chillers). Enwave’s ‘Green Heat’ offering is also being made possible by the installation of new assets that utilize waste heat while producing cooling and hot water.
The site offered some interesting complexities to be solved by the design team. The first was space constraints. As the existing Energy Centre did not have any space to house the new equipment, the only available space that could be used for the addition is a small corner on the lot where buried fuel oil tanks are present. A design was implemented to build over the tanks, one that would comply with the requirements of the Ontario Building Code and the Technical Standards and Safety Authority by leaving the ground level open for future removal of the tanks. All disciplines had to overcome many challenges due to space limitations, including structural, architectural, mechanical, and electrical.
A challenge for the mechanical design team centered on how to integrate the new heat pump system with the existing heating and cooling district system, as well as how to stage equipment without impacting Enwave’s existing customers and their stringent temperature requirements. Our solution was to design a false loading system to start and stage on additional heat pumps in order to avoid temperature spikes which would have negative impacts on customers’ critical data centre equipment.
According to the Canada Green Building Council, “it’s estimated that residential, commercial, and institutional buildings contribute 17% of Canada's greenhouse gas emissions today, and when building materials and construction are included, this level approaches 30%”. As the designers and engineers of these facilities, the AEC industry has an outsize role to play in ensuring the success of sustainable development.
HH Angus has a proven track record of promoting innovative and sustainable engineering solutions. We are committed to providing engineering solutions that reduce energy consumption and reduce or eliminate greenhouse gases.
SERVICES
Prime Consultant | Mechanical Engineering | Electrical Engineering
PROJECT FEATURES
Completed 2025 | New assets use waste heat while producing cooling and hot water | 3600 tons of cooling | 62,000 Mbh heating using water source heat pumps
LOCATION
Toronto, Ontario
KEY SCOPE ELEMENTS
Overcame site constraints through innovative design to comply with OBC and TSSA requirements | Integrated new heat pump system to existing system
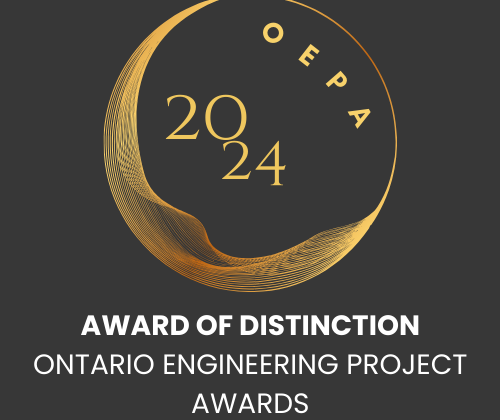
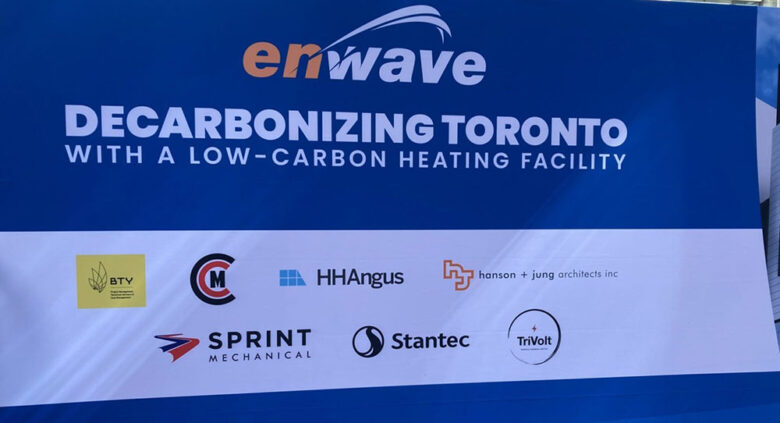
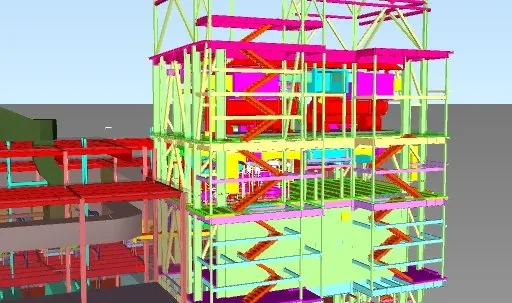
Lonsdale Energy Corporation
Heat Recovery Feasibility Study
HH Angus conducted a study to evaluate the feasibility of exhaust air heat recovery from the Global Relay (GR) data centre facility at 22 Gostick Place in North Vancouver, BC.
Some of the key aspects of the study included:
- The location and footprint of the heat recovery system components were studied within the context of considerable site constraints. The study evaluated the design, construction, and cost considerations for the implementation of the proposed heat recovery system.
- We investigated available heat pump technologies that would be appropriate for recovering waste heat and would satisfy the LEC DES requirements.
- The energy recovered would be used by a water source heat pump to provide hot water to the local LEC District Energy System (DES).
- A water source heat pump system was proposed as the best solution to provide the ability to recover heat from the building ventilation system. The new system would recover heat from the GR facility and would transfer this recovered heat via a hot water loop to the local LEC DES.
- Heat recovery is feasible for the facility and can provide up to 1,100 kW of heating capacity to the LEC DES.
- Constraints to the design of the heat recovery system were also identified, and included:
(i) the quantity of air exhausted from the facility is not fixed and ranges at each exhaust plenum on a seasonal basis and depending on outdoor air temperature – this impacts how much heat can be recovered at a given time;
(ii) the minimum and maximum exhaust air temperatures range from 30°C to 43°C (86°F to 110°F) - the temperature of the exhaust air will influence how much heat can be recovered from the exhaust air; and,
(iii) the cross-sectional area available for the heat recovery coil - the more cross-sectional area that is available for a given amount of heat transfer, the less deep the coil must be (and less airside pressure drop penalty is incurred).
The study concluded that a purpose-built containerized heat pump system would be the most suitable solution to meet the needs of the project. This new containerized structure would be conveniently located adjacent to the GR facility and would exhibit the same architectural character as the existing facility. The proposed heat pump system would include one heat pump unit (based on Emerson Heat Pumps) and four heat recovery water pumps. Control valves, piping accessories, ventilation, lighting, and system controls would all be included in the proposed pre-fabricated containerized enclosure.
Outdoor hydronic piping would connect the heat pump enclosure to the GR facility and the proposed hydronic heat recovery coil system. The heat recovery coil system would consist of four new heat recovery coils placed within the existing facility exhaust air plenums. The existing exhaust fan motors would have to be upgraded in order to address the additional pressure drop introduced by the new heat recovery coils. This fan motor upgrade would also trigger upgrades to the existing electrical infrastructure.
SERVICES
Prime Consultant | Mechanical Engineering | Electrical Engineering
PROJECT FEATURES
Size: 5,600,000 ft2 | Status: Ongoing
LOCATION
Vancouver, British Columbia
KEY SCOPE ELEMENTS
Feasibility study | Heat recovery
Confidential Client
BIM Laser Scanning
HH Angus was engaged to create a 3D Revit model (LOD 300), accurate to reality, of the existing structure and visible HVAC, plumbing and electrical infrastructure. This model was delivered to the client for their use in 3D coordination of their high voltage switchgear replacement project.
The 17,000 ft2 area was scanned using a Faro S70 Laser scanner, with the scans subsequently registered using Faro Scene software to create point clouds. Point clouds were then processed in Edgewise modeling software and used to automatically extract and model walls, structure, piping, conduit and ducts, before being imported into Revit. This efficient process resulted in a very significant 60% reduction in modeling time. The remaining MEP infrastructure was modeled in Revit, with special attention paid to the location of the entry and leave points within rooms for all MEP infrastructure, in response to the client’s requirement.
One of the challenges of the project was the lack of easily accessible data required to create the Revit model. Recap pro or Faro Scene software is needed to review the point clouds and images; this software required licensing and installation on individual machines, which prevented it from being easily accessible to everyone on the project team. The software also requires additional computing power to run smoothly, and this presented an issue for machines that did not meet the software requirements.
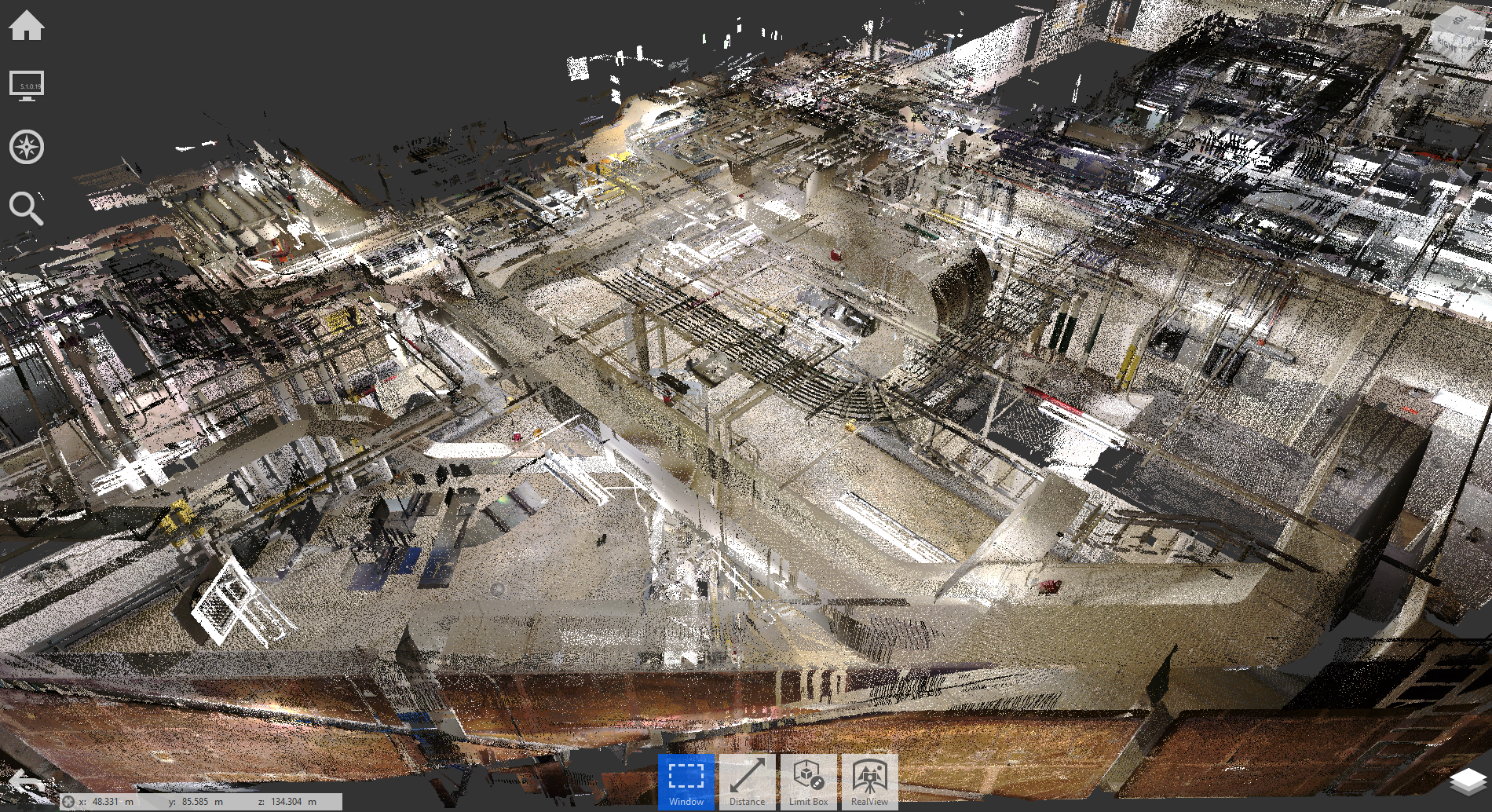
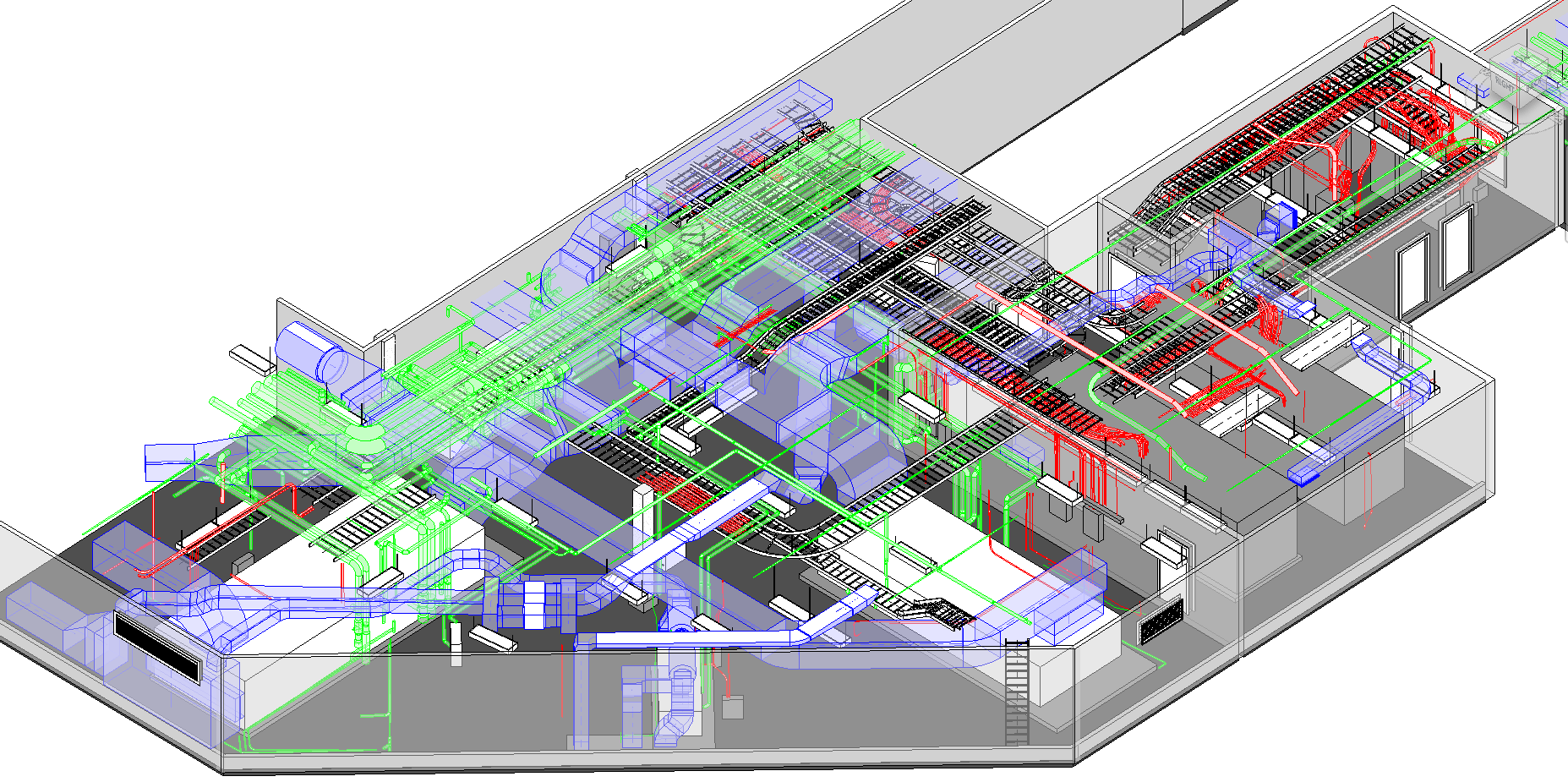
SERVICES
Prime Consultant | Scan to BIM provider
PROJECT FEATURES
Revit modeling of existing structure and visible HVAC, plumbing and electrical infrastructure
LOCATION
Toronto, Ontario
KEY SCOPE ELEMENTS
3D laser scanning
Seneca College of Applied Arts and Technology
Garriock Hall Mechanical Retrofit
Located on the King City campus, Garriock Hall renovations are part of Seneca’s on-going expansion. The retrofitted heating system provides improved comfort for the campus’ 5,200 students.
HH Angus was engaged as prime consultant for a retrofit at one of the campus’ main academic buildings. Our scope included replacement and upgrade to:
- Twelve fan coil units, complete with additional coil elements
- Approximately 30 hot water cabinet unit heaters located throughout the building, along with additional Building Automation System (BAS) integration
- Dual-duct terminal boxes for approximately 2/3’s of the building. The terminal boxes themselves were upgraded from pneumatically controlled to digital controlled complete with BAS integration.
- Domestic hot water system
- Pool heating system
The project used low temperature heating water from a ground-source heat pump system. This increased the physical size of the replacement heaters, which required accompanying structural and architectural modifications.
Domestic hot water preheat was implemented to take advantage of the low temperature heating water from the heat pump system, and was implemented as part of the domestic hot water system replacement and upgrade. The upgrades included a new high efficiency condensing water heater paired with a heating water to domestic water heat exchanger.
The pool heating system was not operational prior to the project. It was made functional and upgraded to take advantage of the low temperature heating water available from the heat pump system, by replacing the heat exchanger and adding additional controls.
Dual duct terminal boxes upgrades included replacing the terminal boxes to implement Variable Air Volume (VAV) control. In a few areas, existing single duct VAV terminal boxes were replaced with those equipped with reheat coils to facilitate occupant comfort.
The project timeline was aggressive, with engineering design starting late May 2019 and tendering in late August 2019. The project took advantage of the 2019 Christmas break to complete the majority of construction in order to minimize impacts to the occupants.
Image courtesy of Google Maps
SERVICES
Prime Consultant | Mechanical Engineering
PROJECT FEATURES
Twelve fan coil units | ~ 30 hot water cabinet unit heaters | Additional BAS integration | Dual-duct terminal boxes, upgraded from pneumatically controlled to digital control, complete with BAS integration | Domestic hot water system | Pool heating system
LOCATION
King City, Ontario
KEY SCOPE ELEMENTS
Heating plant uses ground source heat pump to deliver low temperature heating water | Compressed project schedule to meet heating season deadline | Unique dual-duct HVAC system being modernized and upgraded for re-use