Service: Prime Consultant
MAN Diesel
Bonaire, 14 MWe Power Station
The island of Bonaire (formerly the Netherlands Antilles), has been a special municipality of the Netherlands since 2010. It lies in the Leeward Antilles chain of Caribbean islands, with an area of 288 square kilometers (111 sq.mi.)
With the commissioning of its sophisticated new sustainable wind-diesel hybrid power plant, Bonaire became the first Caribbean island capable of 100% renewable energy. This project’s aim was to transform today’s largely fossil fuel-based energy supply infrastructure in Bonaire into one based on the application of 100% sustainable energy sources within five years (bio diesel extracted from algae).
The Bonaire project featured a 14 MWe turnkey power station with site work, roads and electrical connections. HH Angus was responsible for all mechanical, electrical, civil structural engineering, including various piping systems (heavy fuel oil, light fuel oil, lubricating oil, compressed air, etc), high and low voltage distribution, and PLC control systems. All mechanical detailing was completed with 3D CAD software, with related materials captured in Excel for the bill of material procurement.
Our design scope covered a capacity increase to 20 MW (designed for future use) and was based initially on Heavy Fuel Oil (HFO) as the principal fuel, and light fuel oil (LFO) as an alternative. The plant was designed with the capability to be converted to operate on biofuel in future. Also included in the project was an extensive tank farm with storage of HFO, LFO and lubricating oil.
The plant consists of 5 X2.85 MWe MAN Diesel generating sets at 11kV, and was designed as a base load plant with parallel displacement production from a windfarm generating system. Each genset is selectable to dual busbar systems that each step up to 30kV for island distribution.
This is the only power plant on the island. The diesels supply voltage regulation, as well as VARs and power production to supplement the island’s needs when wind production has been harvested to maximum benefit.
Special care had to be taken to integrate the control systems of the wind turbines and the diesel engines, as the grid performance has to be maintained through fluctuations of the wind resource. The diesel engines have to respond to the changes in output from the wind turbines in order to maintain electrical grid balance.
SERVICES
Prime Consultant | Mechanical Engineering | Electrical Engineering
PROJECT FEATURES
Status: Completed 2010
LOCATION
Leeward Antilles, The Caribbean Islands
KEY SCOPE ELEMENTS
Wind-diesel hybrid power plant | 100% renewable energy | 14 MWe turnkey power station | Piping system, civil structure, high and low voltage distribution and PLC control systems | Capacity increase to 20MW | Heavy fuel oil as principal fuel & light fuel oil as alternative | Extensive tank farm with storage of HFO, LFO and lubricating oil
Brantford Power
Landfill & WWTP Cogeneration 5.4 MW
HH Angus was retained to provide a turnkey natural gas fired cogeneration plant to take in landfill gas and digester gas and, in turn, produce electricity to feed to the Ontario power grid.
The cogen plant also transfers heat back to the digesters for process treatment of municipal liquid waste. In a future phase of the project, heat would be distributed to a district energy system.
Brantford is unique in that its solid waste landfill and the municipal wastewater treatment plant (WWTP) are adjacent to each other. Based on the available methane from the WWTP and the landfill, two 2.7MWe engines were provided (5.4MWe total), with a provision for an additional set as the landfill continues to grow.
The engine hot water is 95˚C and designed to be distributed to the adjacent WWTP. The design allowed for future exhaust gas recovery when the planned district energy system was developed.
The electrical output is 42% of the energy input, and the overall efficiency of the system was designed to be 88%, assuming that full thermal recovery would be implemented in a future district energy phase.
The station service load is supplied by the utility at 347/600V; however, the power is generated at 4160V and steps up to 27.6kV to supply into the grid. Synchronization is at 4160V.
SERVICES
Prime Consultant | Mechanical Engineering | Electrical Engineering
PROJECT FEATURES
Status: Completed 2010
LOCATION
Brantford, Ontario
KEY SCOPE ELEMENTS
Prime Consultant for Design-Build | |Provided two 2.7MWe engines based on available methane | Integrated 42% of electrical output | Overall efficiency designed for 88% at implementation of full thermal recovery
University of Waterloo
Humanities Chiller Plant
HH Angus provided prime consulting engineering services for mechanical, electrical and structural design, project management, and construction administration services for this new Chiller Plant at the University of Waterloo.
The installation included two new 1000 ton, low-pressure centrifugal chillers, two new 1000 ton induced draft cooling towers, associated ancillary equipment, an emergency refrigeration ventilation system, and a chiller plant control system.
The electrical design featured new electrical infrastructure to accommodate the addition of new switch gear, transformers and electrical distribution to all ancillaries.
We used Bentleys Autoplant 3D software for the mechanical piping and ventilation design to ensure the functionality of the equipment and piping layout design. We also provided our client with documentation for pre-tendering of chillers and assisted in evaluation of the tenders.
As Prime Consultant, we engaged a structural engineer to design the necessary infrastructure on the roof to support the new cooling towers.
SERVICES
Prime Consultant | Mechanical Engineering | Electrical Engineering | Contract Administration
PROJECT FEATURES
Status: Completed 2011
LOCATION
Waterloo, Ontario
KEY SCOPE ELEMENTS
Installation of two new 1000 ton low pressure centrifugal chillers | Two new 1000 ton induced draft cooling towers | Emergency refrigeration ventilation system | Structural design to support new infrastructure for cooling towers | Bentleys Autoplant 3D to ensure functionality
Toronto Community Housing
341 Bloor Street West, Senator David A. Croll Apartments
“The system brings enormous value to the facility. Not only does it increase the emergency power load to near peak load, but also it reduces emissions and eliminates transmission losses, thus reducing the need for expanded power generation.”
- Paul Isaac, Principal in Charge, HH AngusThe Senator David A. Croll Apartment building, formerly Rochdale College, is a typical multi-unit residential building managed by the Toronto Community Housing Corporation.
This 335 kW combined heat and emergency power (CHeP) project was built to avoid the cost of replacing a diesel generator, with a significant saving of $300,000. Conventional emergency on-site generation uses dedicated equipment that is rarely operated, yet has a very high capital cost (known as a ‘stranded asset’). HH Angus converted this stranded asset to provide an economic benefit to the facility. The benefit comes from recovering heat so that the overall efficiency rose from 33% to 83%, as well as the use of natural gas, which is cheaper than diesel.
The new generator produces enough electricity for the entire building load on most days. The heat generated by the engine is captured and used to heat the domestic hot water system and building spaces, thereby producing a highly efficient use of the fuel - greater than 90%!
The most important benefit for the building’s occupants is the increased emergency power load capabilities. Instead of powering just a minimum of elevator and emergency lighting services during power outages, the CHeP system provides a power load that runs all regular systems, including heating and air-conditioning systems.
SERVICES
Prime Consultant | Mechanical Engineering | Electrical Engineering
PROJECT FEATURES
Status: Completed 2008
LOCATION
Toronto, Ontario
KEY SCOPE ELEMENTS
Combined Heat and Emergency Power (CHeP) | Co-generation tied into a network system, a first for Toronto | Stranded asset converted to economic benefit - heat recovery efficiency rose from 33% to 83%
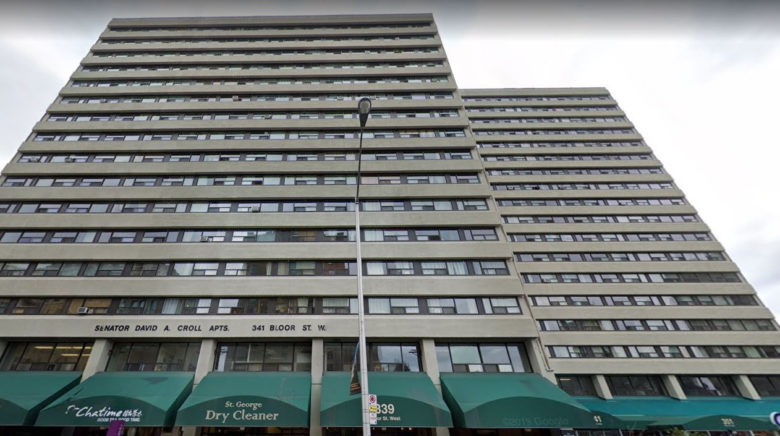
A Toronto ‘first’!
The 341 Bloor Street system was a first in Toronto and was carried out with funding assistance from the Toronto Atmospheric Fund and Natural Resources Canada.
General Motors of Canada
Welder Water System, Car Assembly & Truck Plants
HH Angus designed the Welder Water System for the car assembly and GMT 800 C/K Truck plants in Oshawa. These systems provide cooling water for all the robot welders, circulating cooling water to the tips of the welders to prevent overheating.
C/K Truck Plant
This plant’s welder water system consisted of a cooling tower system and cooling distribution system. The pumps re-circulate tower water from the indoor sump through heat exchangers and up to the cooling towers. The cooling tower system featured five main components: Cooling towers, indoor sump, recirculation pumps, plate heat exchangers and centrifugal filter units.
The two vital conditions that had to be maintained were temperature and differential pressure. A temperature sensor on the hot side of the heat exchanger (closed loop side) controlled the staging of the cooling towers and the speed of the variable speed drive cooling tower fans. Pressure differential transducers located at the index runs staged the cooling water pumps to maintain differential pressure. The welder tips are extremely sensitive to differential pressure, so very tight pressure tolerances have to be maintained at all times.
Car Assembly Plant
In the Car Plant, renovations required the relocation of the welder water system, together with the supply and installation of three new cooling tower pumps and three new circulation pumps.
The three cooling tower pumps were each 100 horsepower, electrically driven, and with a flow rate of 2670 US gallons per minute. The three circulating pumps were each 150 horsepower.
The distribution piping system extended over 3,000 feet, serving welding robots throughout the car assembly plant. The heat transfer, between the circulating (robot cooling) water and the tower cooling water, takes place in four plate-type heat exchangers.
SERVICES
Mechanical Engineering
PROJECT FEATURES
Status: Completed 2008
LOCATION
Oshawa, Ontario
KEY SCOPE ELEMENTS
Cooling tower system | Sensor-controlled temperature and differential pressure | Three cooling tower pumps @ 100hp with a flow rate of 2670 USGPM | Over 3000 feet of distribution piping serving robots throughout the car assembly plant
— Photos courtesy of General Motors of Canada