Service: Prime Consultant
Enwave Energy Corporation
District Energy System Cogeneration Plant
District energy is a key component of Toronto’s climate action plan, to reduce emissions from buildings and help the City reach its greenhouse gas (GHG) reduction target of 80% by 2050. Buildings currently generate about half of the GHG emissions in Toronto.
Enwave is the largest District Energy Systems in North America. The system has enough power to supply over 180 office buildings.
This project started in 1962 with an original feasibility study and culminated in the design and construction of a central plant and distribution system with an installed capacity of 800,000 lbs. of steam per hour.
The deep lake cooling system was added later, and makes use of the 40°F/4°C water in Lake Ontario. It has a total capacity of 75,000 tons of refrigeration, which is sufficient to air condition 3.2 million m2 / ~34 million ft2 offices.
Clients with whom we have worked on the Enwave District Energy System include:
- Hudson Bay Company
- Bank of Nova Scotia
- Cadillac Fairview Toronto Dominion Tower Plaza
- Royal Bank Plaza
- Mt. Sinai Hospital
- Toronto General Hospital
- Women’s College Hospital
- The Hospital for Sick Children
- Li Ka Shing Knowledge Institute
- St. Michael’s Hospital
SERVICES
Prime Consultans | Project Mangeres | Electrical Engineers | Mechanical Engineers
PROJECT FEATURES
Status: Complete 2019
LOCATION
Toronto, Ontario
KEY SCOPE ELEMENTS
Provided technical advisory for heating and colling systems | Introduced over 5 miles of piping for high-pressure steam district heating | The deep lake cooling system makes use of 40°F/4°C water in Lake Ontario
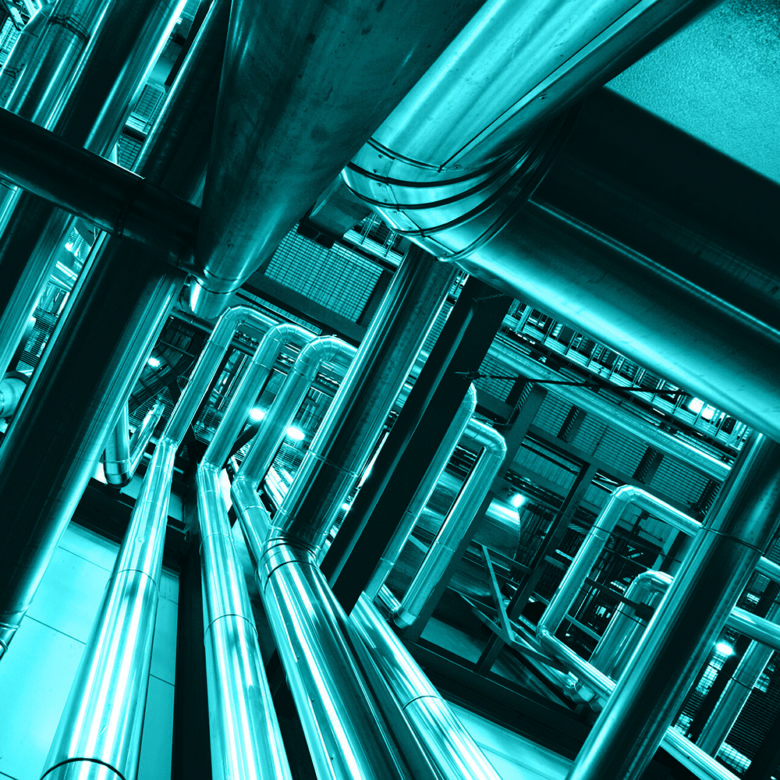
Supplying miles of steam
The system supplies high-pressure steam for district heating via an underground distribution system of over five miles of piping in downtown Toronto.
Trusted advisor
HH Angus has served as a technical advisor to Enwave over many years, consulting on various engineering aspects of the heating and cooling systems.
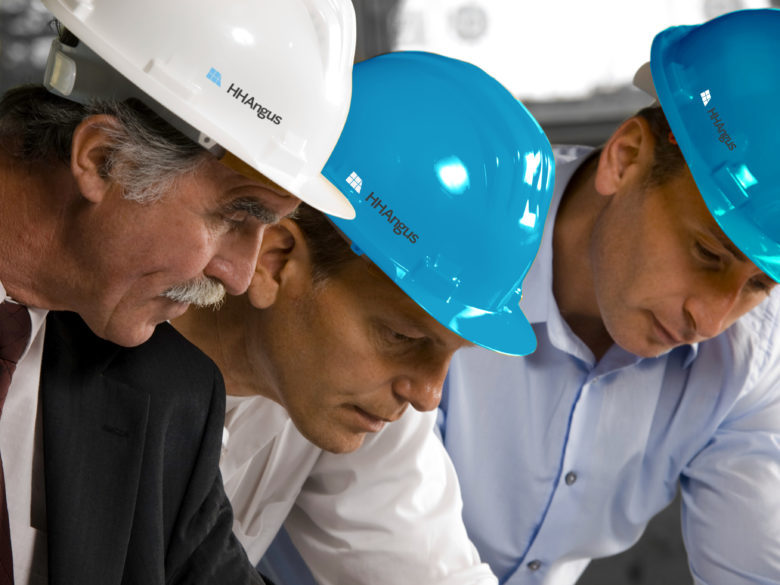
Confidential Client
Deodorizer Installation
HH Angus served as prime consultant for this new deodorizer processing plant. The new installation more than doubled the oil refining facility’s existing capacity.
Palm oil is the most widely-used edible oil in the world. Deodorizing is the final stage in refining the oil, and is required to remove odoriferous material, free fatty acids and other undesirable minor components, in order to produce a bland oil with a good shelf life.
The deodorizer tower is 30m high and 2m in diameter, with connected boilers, pumps, etc., that required connection to the existing production plant located adjacent to the expansion area. Due to the height and sectioning of the deodorizer, it had to be built in two stages.
One of the key challenges of the project was the site constraints. Two feasibility studies were produced as part of the investigation. It was determined that a new building was needed, rather than trying to install the deodorizer in the existing building.
In order to accommodate the electrical needs of the deodorizer process, a system upgrade was required to the switchgear. The upgrade allows the client the flexibility to install other major equipment in future.
Enabling projects for the deodorizer installation included a nitrogen tank installation, cooling water system, a new natural gas let down station, and new gas feed to the site.
SERVICES
Prime Consultant | Mechanical Engineering | Electrical Engineering
PROJECT FEATURES
Status: Completed 2017
KEY SCOPE ELEMENTS
Detailed Engineering Study | 3D modeling | 30m high deodorizer tower connected to existing plant within site constraints | Nitrogen tank installed | System upgrade to switchgear provided flexibility to install other major equipment in future
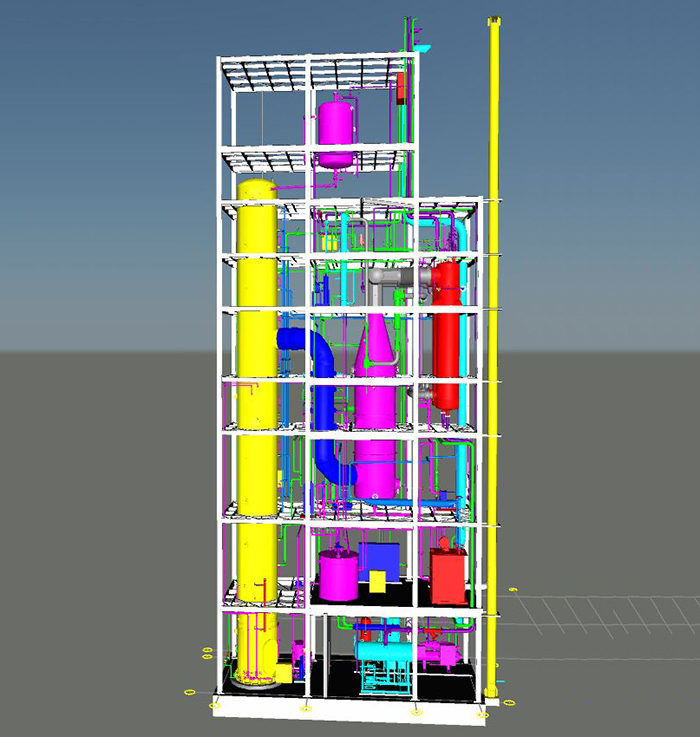
Modeling in 3D
As a special feature of the project, HH Angus modeled the installation using Plant 3D software. The installation was quite complex, and creating the model reduced both design time and the construction schedule. The contractor was able to see a comprehensive view of the design, confirming locations of pipes, etc.
McMaster University
Trigeneration Plant
HH Angus was initially engaged to perform a Detailed Engineering Study to determine the viability of installing a natural gas-fired turbine for power and steam generation, and the use of absorption cooling to balance out steam production in the warmer months.
For a full year, we reviewed heating, cooling and electrical power loading at McMaster University. We also reviewed operating costs covering maintenance, operating and natural gas costs, and completed a sensitivity analysis of gas and power pricing variances. Capital and Operating budgets were also prepared to determine ROI on the proposed investment.
Following the Detailed Engineering Study, we were engaged to design the new trigeneration plant using a gas turbine (5.4 MW) coupled with an HRSG (Heat Recovery Steam Generator), natural gas compressor, absorption chiller (1000 tons) and centrifugal chiller (2500 tons). The plant was installed in the existing central utility plant room, and significant demolition of redundant equipment was undertaken to generate the space for this system upgrade.
There were a number of interesting challenges associated with the work:
- Selective demolition of two existing steam boilers, two existing incinerators and one 5,000 ton electric centrifugal chiller including isolation of services and asbestos abatement to not impact existing plant operations
- Fitting this large equipment into an area with significant space constraints
- Creating a path of ingress for the equipment from outside into the sub-grade basement level of the plant for installation during winter months where the weather would be unpredictable
- Minimizing the impact on daily operations within the plant during the demolition and construction phases.
- Integration and coordination with a switchgear replacement project running in parallel with the cogeneration project
- Targeting a completion date of October, 2017 to ensure the client would receive full IESO funding for the project
Some of our solutions included:
- Thorough surveys of existing equipment and services to ensure the equipment slated for demolition could be isolated from the operating plant with minimal to no service interruption
- Engaging with equipment suppliers at an early date to ensure required footprints were allocated
- Coordinating with the structural engineers to design a removable roof cap that could be installed prior to the existing roof being cut open to allow equipment installation
- On-going coordination with plant staff during the design phase to get buy-in of any modifications required to the existing plant
- Pre-tendering long lead item equipment to ensure on-site delivery dates would meet the construction schedule
By designing to eliminate potential interferences or issues with installation, we were able to meet the delivery targets and deliver a successful project.
SERVICES
Prime Consultant | Mechanical Engineering | Electrical Engineering
PROJECT FEATURES
Status: Completed 2017
LOCATION
Hamilton, Ontario
KEY SCOPE ELEMENTS
Year-long detailed engineering study | Reviewed heating, cooling and electrical power loading | Study included sensitive analysis of gas and power pricing variances | Introduced new design for trigeneration plant usage, a gas turbine (5.4MW) coupled with an HRSG, natural gas compressor, absorbtion chiller and centrifugal chiller
Casino Rama
Power Infrastructure Upgrade
“The installation of protective electric equipment designed and specified by HH Angus is working amazingly, and has afforded us the confidence that we no longer need to pre-start all three of our 1 MW generators during every looming lightening storm”.
— John Haley, Director of Engineering and EVS Casino Rama
Casino Rama features over 2,500 state-of-the-art electronic gaming machines. The popular facility is owned by the Chippewa’s of Rama First Nation and the Ontario Lottery and Gaming Corporation. It welcomes over three million visitors annually.
Because power quality issues occasionally damaged sensitive electronics in gaming machines, Casino Rama gave HH Angus a mandate to find a solution that would protect equipment while minimizing games downtime, as well as shutdowns required to implement the solution.
HH Angus analyzed Casino Rama’s existing power distribution systems, critical loads, plans for future electrical load growth, and building infrastructure, including available service space and mechanical infrastructure.
A number of recommendations were presented, with varying degrees of risk mitigation and cost. Casino Rama opted for a 1.2 MW centralized uninterruptible power supply (UPS) for the portion of the existing emergency generator powered distribution system dedicated to their electronic gaming machines.
In addition to providing protection against power quality disturbances, the centralized UPS provides gamers with an uninterrupted playing experience during a utility power outage. The UPS bridges the gap between the onset of a utility power outage and the time it takes the onsite 3 MW emergency generators to come online and support the critical loads.
Implementing the centralized UPS system had its own unique challenges. Available service space had to be identified. The system had to be integrated with the facility’s electrical system in a way that minimized the time required for machine shut-downs and tie-ins. Additional air conditioning units were provided to ensure that the stipulated ambient temperatures were maintained. Structural reinforcement was also needed to ensure the floor slab could support the added weight of the battery banks. All these requirements had to be taken into account when designing the project.
SERVICES
Prime Consultant | Electrical Engineering
PROJECT FEATURES
Status: Completed 2012
LOCATION
Orillia, Ontario
KEY SCOPE ELEMENTS
1.2 MW central UPS dedicated to 2500+ gaming machines | Power distribution analysis | Integration with existing electrical system | Eliminated power quality issues
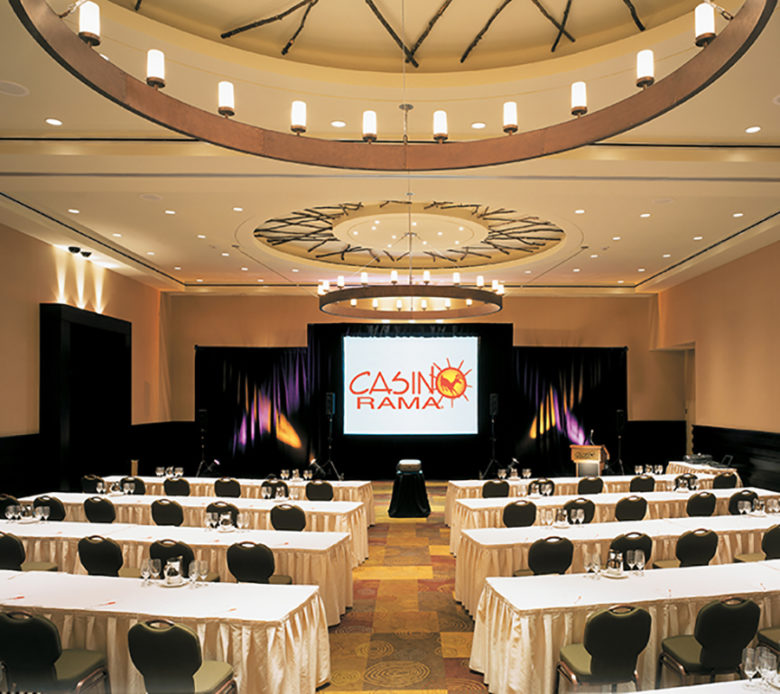
Zero Power Quality Issues
Since the installation of the centralized UPS system, Casino Rama has had no power quality incidents affecting their sensitive electronic gaming machines. In addition, electrical distribution fault-related downtime has been eliminated, resulting in a substantial reduction in annual maintenance costs.
Quote source: Casino Rama hires HHA to help with power infrastructure
— Photos courtesy of WZMH Architects
Sunnybrook Health Sciences Centre
High Voltage Emergency Power Renewal
HH Angus has been providing mechanical and electrical engineering at the Sunnybrook campus since 1945. The complex now totals more than 2,000,000 ft2. In that time, a great many individual projects have been successfully delivered. The high voltage emergency power renewal described below was a large infrastructure improvement project. Other large project examples from our work at Sunnybrook include M Wing and the Toronto Sunnybrook Cancer Centre.
High Voltage Emergency Power Renewal
The renewal project involved replacement and upgrades of existing forty-year-old standby generators and associated infrastructure. The specifics included: installation of 8.75MW of diesel generators, new medium voltage switchgear, a selective catalytic reduction system for each new generator (for emissions control), fuel oil system upgrades and replacement of a campus-wide PLC-based load management system. The selective catalytic reduction systems allow Sunnybrook to use their plant for offsetting peak loads during summer months and to realize savings in annual hydro expenditures.
The high voltage emergency power renewal project replaced the existing 4160V generating capacity of 4.3MW with 8MW of new 4160V generating capacity. A 600V, 750kW generator replaced an existing 400kW generator.
SERVICES
Mechanical Engineering | Electrical Engineering | Prime Consultant
PROJECT FEATURES
Status: Completed 2015
LOCATION
Toronto, Ontario
KEY SCOPE ELEMENTS
Large infrastructure improvement project involving architectural and structural design for a building plenum expansion | Installed 8.75MW diesel generator | Added selective catalytic reduction system for each new generator | Multi-phase project to ensure service redundancy for critical functions
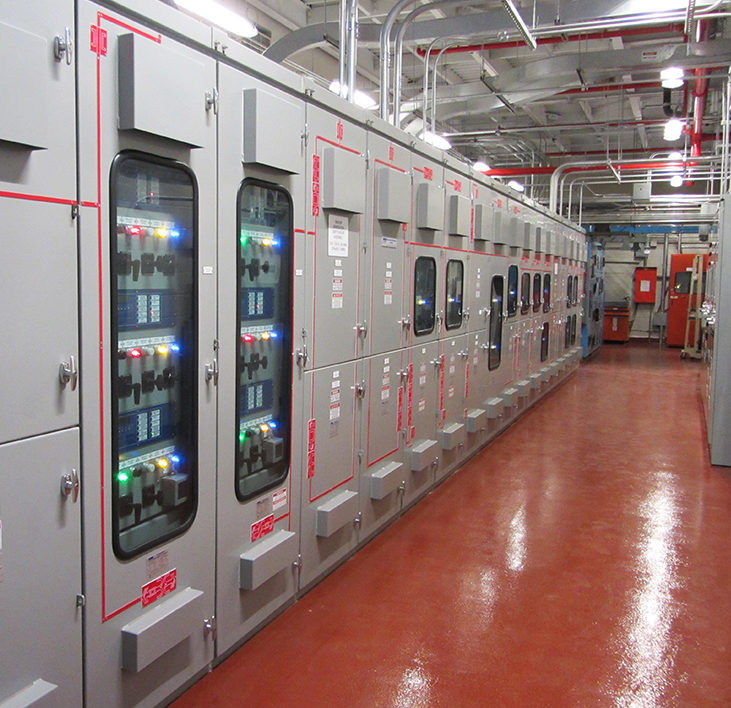
Prime consulting services
HH Angus was the Prime Consultant, as well as the electrical and mechanical engineer for the project. We retained the services of an architect and structural engineer to design a building plenum expansion for the new diesel generators. The general trades work included extensive structural steel work, excavation and concrete work.
HH Angus managed equipment procurement for the project and helped Sunnybrook Health Sciences select an equipment supplier to provide a .9 million CDN (2013) equipment package.
Phasing for service redundancy
The project was multi-phased to allow temporary power to maintain service redundancy for critical healthcare functions while existing diesel generators were decommissioned and the new structure constructed and plant equipment installed.
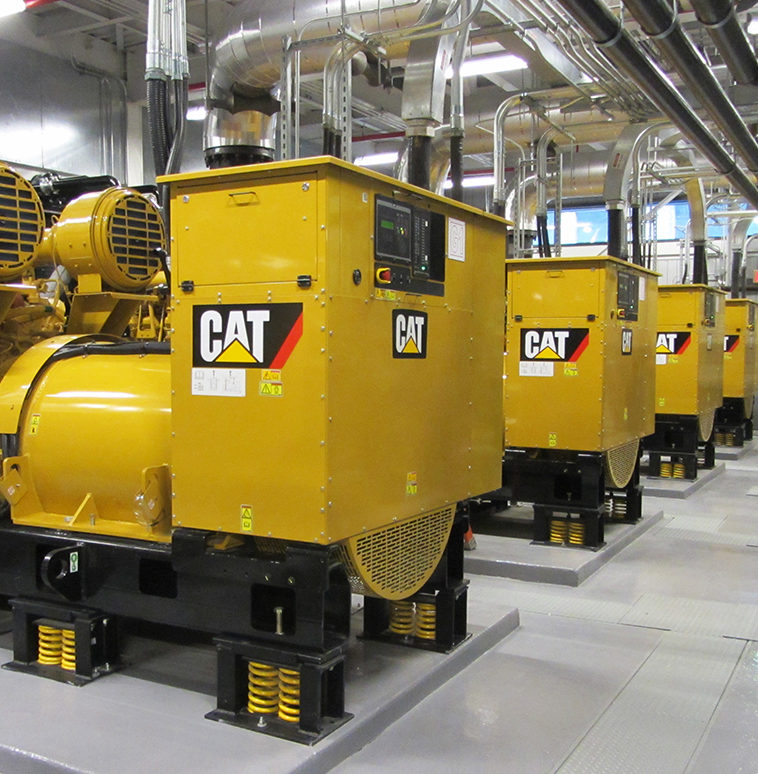