Service: Sustainability
Royal Inland Hospital
New Patient Care Tower
Royal Inland Hospital is a tertiary level acute care hospital serving a catchment area of approximately 220,000 residents in the city of Kamloops and throughout the Thompson, Cariboo and Shuswap regions of British Columbia.
The 290,625 ft2 new Phil & Jennie Gaglardi Patient Care Tower (PCT) is a nine-storey building that includes a surgical floor, 13 operating suites, patient floors for mental health and medical/surgical beds, a neurosciences and trauma unit, perinatal centre, labour and delivery rooms, and neonatal intensive care unit. There are also two underground parking levels, administrative and clinical spaces on three lower floors, an intermediate mechanical floor, and 3 inpatient levels topped by a penthouse containing the heating, cooling, and emergency power plant.
Phase 2 consists of a number of renovations within the existing facility, including a completely renovated Emergency Department. Phase 1, which opened in July 2022, has achieved LEED Gold certification. HH Angus provided mechanical and electrical design services for the PCT, which was constructed adjacent to the existing hospital under a P3 contract.
Designed with direct input from local healthcare workers, the PCT streamlines access to hospital services through a single main entrance. A new post-anaesthetic recovery room in the adjacent existing facility’s renovated space will be constructed in Phase 2. Other clinical spaces include a substance use inpatient unit, a child and adolescent mental health crisis intervention program, maternal and child services, and respiratory therapy services. Non-clinical spaces include reception, patient registration, a rooftop helipad, underground parkade, retail space and a new home for the Royal Inland Hospital Foundation.
The mechanical design included energy-efficient heating and cooling systems with a variety of heat recovery features. The project had an ambitious energy use target and HVAC systems were designed with this benchmark in mind. Current estimates predict 24% savings in energy costs.
HH Angus was able to solve a problem the Hospital was having with the existing distributed hot water boilers by upsizing the new plant to serve the majority of the hospital campus. The ventilation design includes redundant capability and outbreak control, and exhaust air heat recovery, as well as providing for future flexibility.
The Health Authority expressed an interest in the ability to conduct smudging ceremonies in any patient room without having to make significant modifications to the current ventilation design and infrastructure included in the project. HH Angus found a means for using the ventilation system as originally designed and applying a unique operational sequence to minimize capital cost changes while providing the ability to undertake smudging activities in any of the patient rooms on the Medical/Surgical and Mental Health Adaptive inpatient units.
A central focus of the design team was to work with the commissioning team to ensure proper operation of the new facility. The design team is now helping monitor ongoing operations to recover and reuse as much waste heat as possible. This effort concentrates on the heat recovery chiller plant operation to meet as much of the building’s heating load as possible using waste heat. This contributes to minimizing the production of GHGs from heating energy sources and, in turn, improves decarbonization for the new facility. New electrical services include a 25 KV service from BC Hydro serving a new outdoor substation powering the existing campus and PCT. New redundant 25kV to 600V FR3 transformers feeding the new tower were provided in the new main electrical room. Three new 2MVA diesel generators provide emergency power backup to the new patient care tower and the rest of the existing campus if utility power is lost. 600V distribution on both utility and generator power are provided with high resistance grounding to increase resiliency and reliability in the event of a single ground fault. Numerous low voltage systems were provided including fire alarm, lighting control system complete with daylight harvesting, circadian rhythm tunable lighting in the Neo-natal ICU, and electrical metering.
SERVICES
Mechanical Engineering | Electrical Engineering
PROJECT FEATURES
Size: 290,625 ft2 | Status: Phase 1 completed 2022
LOCATION
Kamloops, British Columbia
KEY SCOPE ELEMENTS
Ongoing technical infrastructure upgrades | Installed heat exchangers to link the cooling plant to the Deep Lake cooling system | LEED Gold certified
Helipad Design
The rooftop helipad is served by a number of mechanical and electrical systems to help keep the pad surface clear of snow and ice and to provide appropriate safety lighting to meet all requirements. Fire protection and life safety systems, such as foam suppression, were carefully coordinated and designed to ensure full coverage and containment in the event of a discharge.
Systems Integration
Integration with the existing hospital systems was a significant challenge and required numerous connections to the adjacent facility. Requiring multiple site visits, it was determined the two facilities could be successfully integrated by enclosing an outdoor courtyard between them, transforming it into a four-season space that will benefit patients, staff and visitors. On the electrical side, backfeeding the existing facility with new 600V HRG generator backup required careful analysis of existing distribution to ensure compatibility for all existing equipment to the new 3 wire distribution on emergency power. A detailed sequence of operations for black start sequence and retransfer of automatic transfer switches to normal was developed and commissioned to ensure proper operation for different failure scenarios.
TD Bank
Living Roof“The Green Council [tenant representatives] has made it clear, through a commitment to action, that sustainability is a core value of TD Centre tenants.”
David Hoffman, then-General Manager. TD Centre
At the TD Centre’s iconic towers in downtown Toronto, TD Bank’s Living Roof offers both environmental benefits and some much-needed green relief from the usual hardscape views had by occupants of the Centre’s towers. It covers 22,000 ft2 and is planted with creek sedge grasses, a hardy semi-evergreen native species tough enough to survive the extremes of Toronto’s climate. Annual energy savings from the green roof are approximately $23,000. This is achieved by reducing summer cooling and winter heat loss by 25%.
HH Angus provided mechanical and electrical engineering for the green roof installation and irrigation system, as well as the project’s preliminary Feasibility Study. To avoid over-watering, the irrigation system features a sensor that shuts down the irrigation system when it rains. This sensor also reduces irrigation when the water received during previous rainfalls or irrigation has not yet evaporated.
In order to evaluate the requirements for mechanical and electrical design for the irrigation system, the ceiling plenum for the single story building below had to be surveyed. The storm water drainage system was original and would need modification and updating. The existing plumbing was modified to allow connection of the new irrigation.
Installation of dedicated electrical circuits and automated controls was required in order to operate the self-draining irrigation system. The controls were ceiling mounted with remote computer access. Rain spray heads, valves, head sensors, pattern nozzles, valve boxes, and stainless roof drains were incorporated.
Before the design could be executed, rainwater calculations were carried out based on Environment Canada data, along with spreadsheets detailing storm water run-off. These calculations assisted in sizing the storm water piping and locating roof drains and spray nozzles.
A roof leak detection system was also designed, along with a new soil pipe vent stack through the Pavilion roof, and a gooseneck conduit for rooftop wiring. A new replacement filter rack was added to the roof air vents.
SERVICES
Feasibility Study Plumbing Design | Mechanical Engineering | Electrical Engineering
PROJECT FEATURES
Size: 22,000 ft2 | Status: Completed 2015 | Annual energy savings through reduction in summer cooling requirements and in winter heat loss
LOCATION
Toronto, Ontario
KEY SCOPE ELEMENTS
Feasibility study | Rainwater calculations | Plumbing design with supporting mechanical and electrical design and engineering | Roof leak detection system
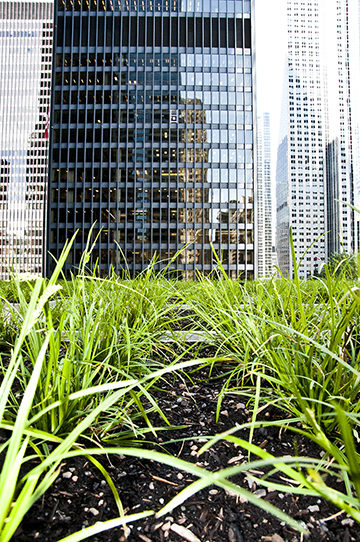
Sustainable
design
TD Bank's Living Roof represents tenant values and is a bold expression of collaboration in support of environmental stewardship
Honouring the design
The green roof’s grid pattern mimics Mies van der Rohe’s original design for the pavilion roof. This was done to respect the ‘designated heritage site’ aspect of the TD Centre.
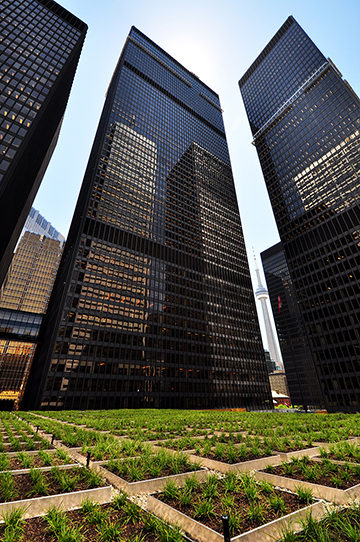
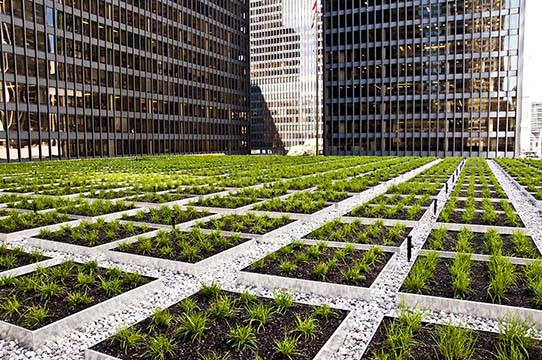
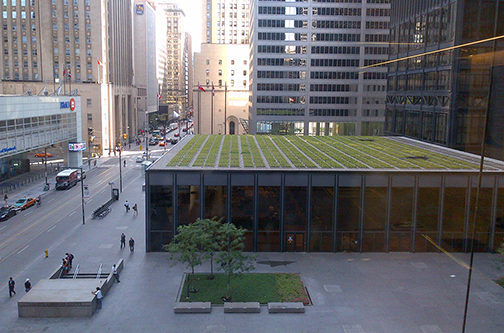
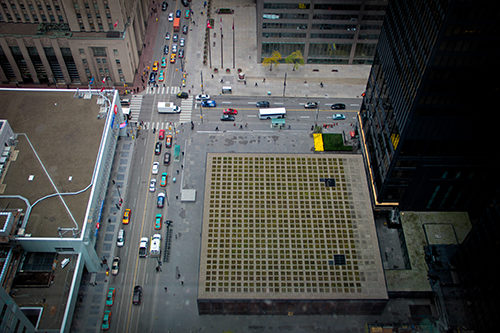
Images courtesy of Flynn Canada
St. Michael’s Hospital
Barlo MS Centre
Canada has the highest rate of multiple sclerosis in the world; in fact, the disease is known internationally as ‘Canada’s Disease’. St. Michael's Hospital in Toronto is one of North America's busiest MS centres. It has been caring for people with MS since 1981, and now treats 7,000 patients.
The new Barlo MS Centre offers one-stop care, bringing together neurologists, nurses, social workers, neuropsychologists, physiotherapists, occupational therapists and speech therapists in a world-leading treatment and research centre for multiple sclerosis. The 25,000 ft2 clinic has been constructed on the top two floors of the new Peter Gilgan Patient Care Tower.
HH Angus’ mechanical scope for the fitout of the shelled space included ventilation, plumbing, medical gas, heating & fire protection, and controls. Our electrical scope covered power, lighting, communications and security.
Unique aspects of the project's design included: presentation to the client of a number of ventilation strategies to address the shortage of air supply available to the design, and a reworked ventilation strategy under a very aggressive schedule to redistribute and extend air to the clinic from an existing air handling unit that was previously feeding another floor.
Some of the project challenges included:
- The addition of a compounding pharmacy late in the design, for which additional requirements had to be vetted to meet NAPRA. The team took advantage of early works to investigate available shaft space for running new biological exhaust to the roof.
- Design activities had to be scheduled concurrently with testing and commissioning still underway at the time for the main Patient Care Tower.
- Ceiling construction and new structural constraints limited accessibility. The team used 3D imaging and Revit to coordinate all ceiling elements requiring accessibility, in order to integrate services into areas with wooden slatted ceilings.
- The team took advantage of early works to coordinate structural openings for future ventilation in order to limit ceiling interference for the fitout design.
SERVICES
Mechanical Engineering | Electrical Engineering | Lighting | Plumbing | Communications Systems | Security Systems
PROJECT FEATURES
Size: 25,000 ft2 | Status: Completion 2021
LOCATION
Toronto, Ontario
KEY SCOPE ELEMENTS
Two floor clinic fitout | Variety of room types and functions | Custom smoke venting and fire alarm zoning to accommodate feature staircase

Achieving the design vision
We worked closely with the architect to modify the existing fire alarm zoning and smoke venting strategy in order to accommodate a new mezzanine on Level 17. This allowed the architect to achieve the design vision for the feature staircase without the use of smoke baffles.
Variety of functions
The space includes a variety of room types, including exam rooms, gym, medical infusion centre, group physiotherapy studio, auditorium, cognitive lab and a pharmacy.
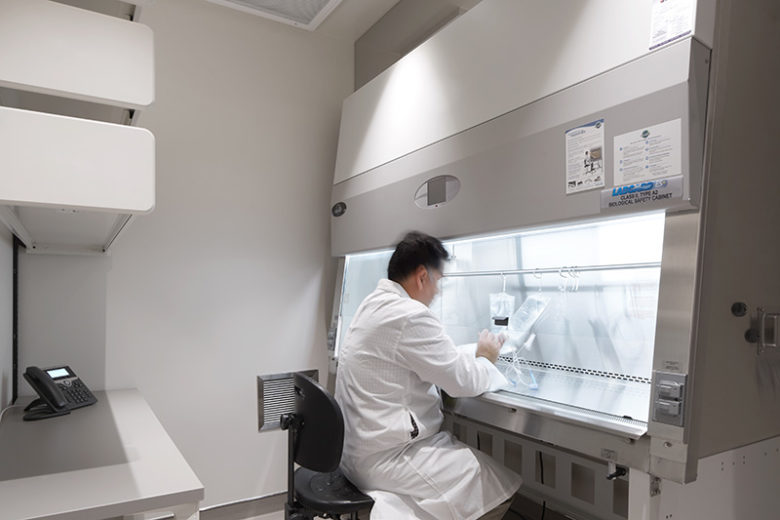
Click here for the St. Michael’s Hospital video feature on the Barlo MS Clinic.
Mirvish Village
Central Utility Plant
Mirvish Village is reimagining a 4.5 acre section of Toronto's Bloor/Bathurst neighbourhood, including the former site of the the iconic Honest Ed's store, a beloved Toronto landmark. Featuring four high-rise, one low-rise and twelve heritage buildings*, the mixed-use site will be home to more than 2000 residents.
HH Angus is working with Creative Energy Developments to provide mechanical and electrical engineering services for the Mirvish Village central utility plant, which includes a combined heat and power plant (CHP), a boiler plant, and a cooling plant. The CHP plant will include an 800 KW generator set with auxiliaries and heat recovery system. The generator is expected to run continuously to provide power to the complex.
Heat recovery consists of two systems: High Temperature to provide heat to buildings, and Low Temperature to provide additional heating for a winter snow melting system and swimming pool heating. The boiler plant will include installation of four condensing hot water boilers, with the option for two additional boilers in future. All boilers will have an output of 3.1 MW.
The cooling plant will include installation of two water-cooled chillers, operating at 1200 tons each. One chiller is a magnetic bearing chiller with variable frequency drive (VFD), and the other is a centrifugal chiller with VFD. As well, two cooling towers at 1200 tons each will be installed on the roof.
Central distribution piping from the plant will provide hot water and chilled water to multiple energy transfer stations, with heating, cooling, and domestic hot water heat exchanges for each building within the complex.
The photo-voltaic solar system will have a capacity of 103KW, 480V. HH Angus is providing direction for locating the installation, coordinating with the PV supplier for modeling the panel direction and angle for optimal PV output, developing technical connection requirements with Toronto Hydro, and identifying requirements for parallel generation with the central utility plant.
We also assisted the client with a successful incentive funding application. Ultimately, the incentive was not applicable due to schedule changes, which meant the project could not meet the incentive deadline.
* The World Architecture News Awards
This international organization recognized Mirvish Village with a Bronze Award in their 2023 world-wide competition. The project won in the category of 'Future Projects'. According to the judges, "Integrating old and new, small-scale buildings and towers, it proposes a dynamic, dense and diverse micro-city with the perfect scale to enjoy as a pedestrian."
Renderings courtesy of Westbank Corp.
SERVICES
Mechanical Engineering | Electrical Engineering
PROJECT FEATURES
Status: Completion 2022
LOCATION
Toronto, Ontario
KEY SCOPE ELEMENTS
Combined Heat and Power Plant | Boiler Plant | Cooling Plant | High Temperature and Low Temperature Heat Recovery Systems | Photo Voltaic System
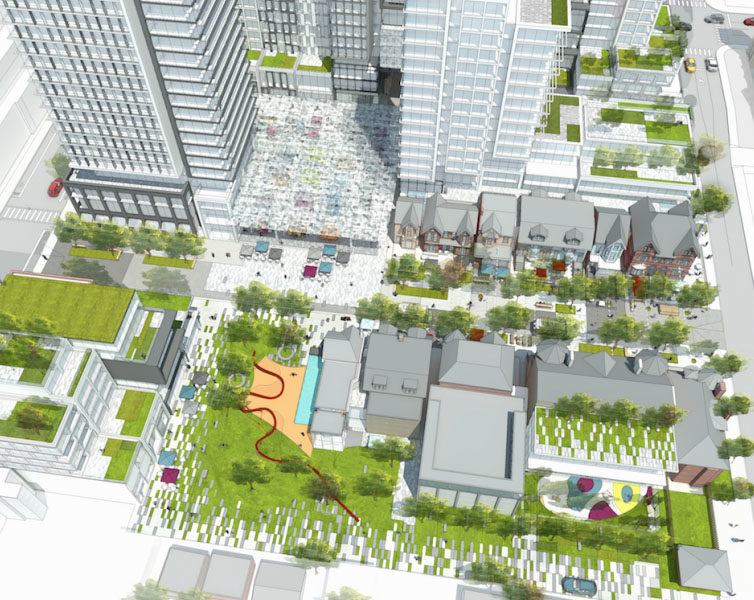
Metering Strategies
Our scope also included developing thermal and electrical metering strategies within a microgrid system, design of operation for gas-fired emergency generators in electrical peak shaving mode, and the design of a roof mounted PV solar system.
Sustainable design
Mirvish Village is being designed to meet LEED® Platinum ND standards, and will feature sustainable transportation options.
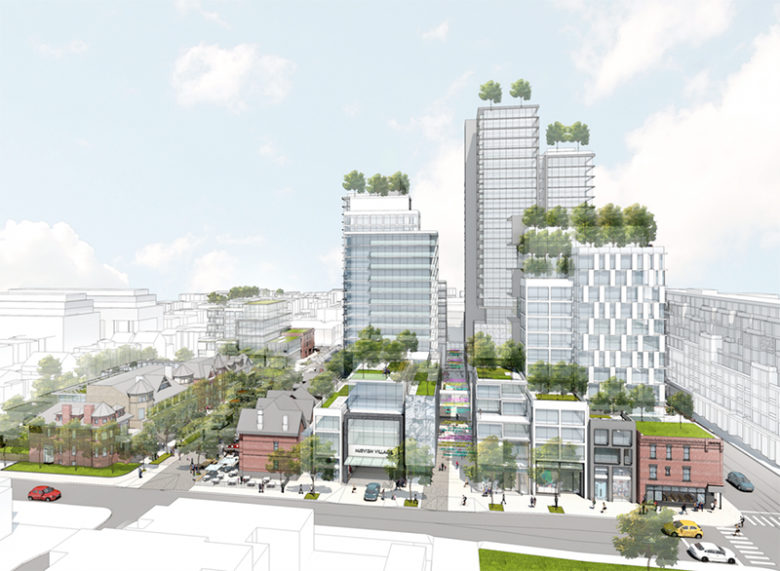
Town of Oakville
Fire Hall #8
This project was designed and constructed under the Integrated Project Delivery procurement model, a methodology that, in our experience, provides excellent results for our clients, as well as fostering greater collaboration within the project team.
Oakville’s new fire station and amenities have been designed to serve a growing population. LEED Silver certified, the 1.5 storey facility was almost fully constructed from glue laminated and cross laminated timber (CLT). CLT is a relatively new construction material in North America; CLT panels/walls are fabricated off site, where all M&E openings and penetrations are cut out, and then subsequently assembled on site. This approach required extremely close coordination between the structural designers and the M&E designers since, unlike drywall, wood openings cannot be adjusted once cut. The modular construction approach also helped meet the aggressive schedule for this project.
HH Angus’ mechanical scope included variable refrigerant flow, energy recovery ventilators, infrared tube heaters, and vehicle exhaust system. Electrical systems include natural gas backup generator, daylight harvesting sensors, provision for solar PV, CCTV and card access, and fire locution (radio system for 911 dispatch). Special provisions were made to allow speakers to be installed strategically throughout the building to support the locution/fire alerting system, with additional provisions for the radio antenna. In 2021, the project was honoured with the Toronto IES Illumination Section Award.
The fire hall floor plan consists of three fire truck bays - two drive-through and one back-in bay, gymnasium, dormitory, kitchen, offices, meeting rooms, IT room, and many specialized service spaces. Fire Hall #8 is designated as a “post disaster building”; hence, the M&E systems are very robust.
Perhaps ironically, the new fire station is clad in charred wood. Shou Sugi Ban charred siding, made from logs reclaimed from Ontario and Quebec waterways, offers many safety and operational advantages: it is ultra-low maintenance, naturally resistant to insects, moisture and rot, has proven fire resistance qualities, and is sun and water repellent. At end of life, the siding can be disposed of safely, without environmental damage.
The project team, under the IPD procurement model, included the Town of Oakville - Owner | Chandos - Builder/IPD Lead | LETT - Architect | HH Angus - Mechanical and Electrical Engineer | Bering Mechanical - Mechanical Contractor | Plan Group - Electrical Contractor | Gillam Group - Construction Management | Element 5 - Wood Structure Fabrication | LEA Consulting - Structural Engineer | Tresman Steel - Steel Structure Contractor | Groundworks Construction - Early Works and Landscape | Fluent - LEED Consultant | Husson - Stormwater Management.
Construction time-lapse: https://youtu.be/2dydglnYkRM
SERVICES
Mechanical Engineering | Electrical Engineering | Lighting Design | Communications Design | Security Design
PROJECT FEATURES
Status: Completion 2020 | 11,500 ft2 | Integrated Project Delivery | Mass timber construction | LEED Silver certified| Designated 'post disaster' building
LOCATION
Oakville, Ontario
KEY SCOPE ELEMENTS
Net Zero provisions for future conversion, with high efficiency M&E | Shou Sugi Ban charred wood cladding | Provision for future photo voltaic installation | locution/fire alerting system
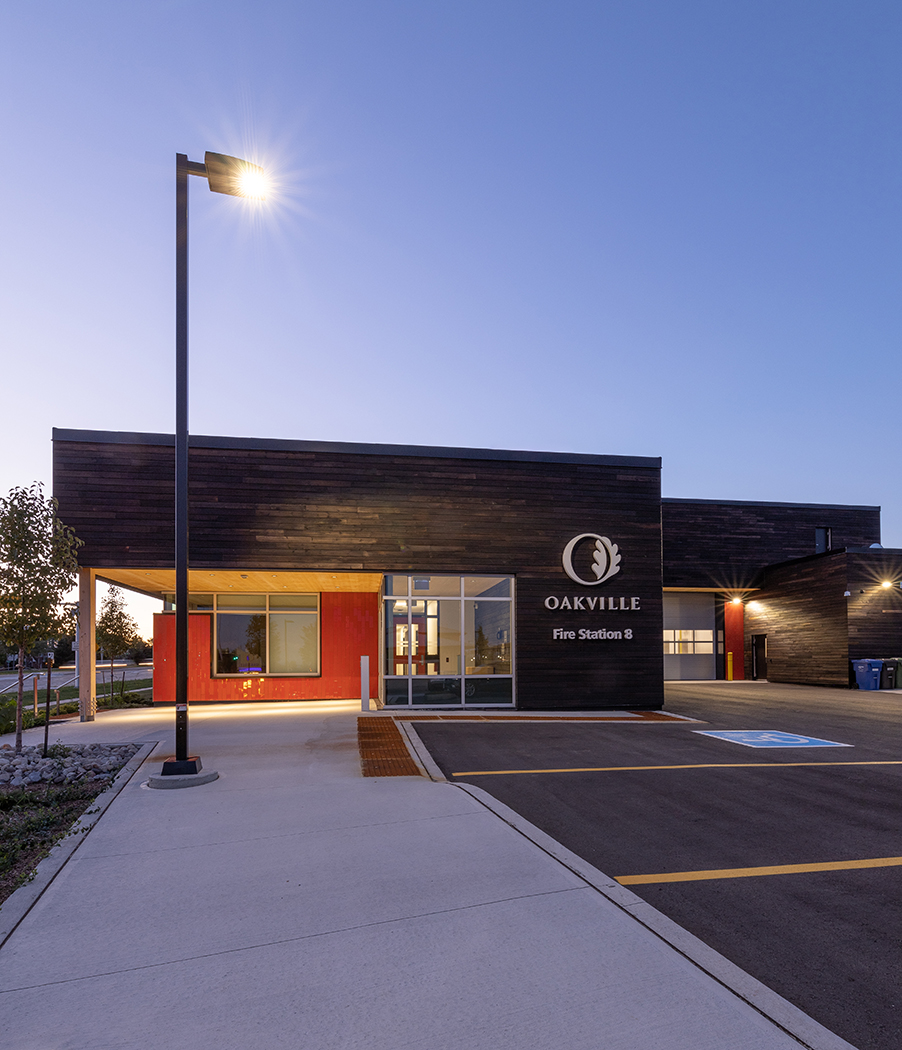
Net Zero Conversion
Highly efficient M&E systems provide for future Net Zero conversion. The Fire Hall is designed to accommodate a 40kW Solar PV system to offset and displace energy usage.
Site Challenges
The Fire Hall was built adjacent to an existing EMS Station and shares the road entrance and utilities. This presented a challenge in planning for construction, service entrances and operations. The team had to ensure that the Fire Hall does not impede EMS' emergency response process.
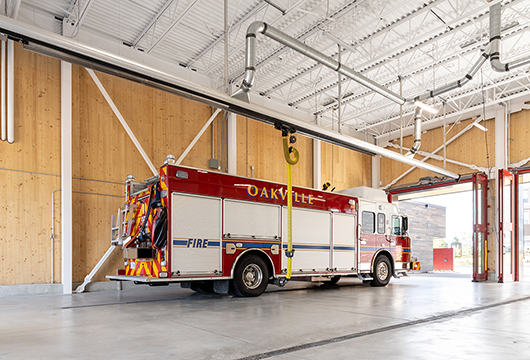
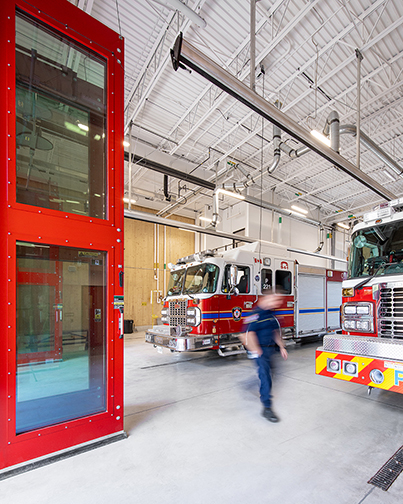
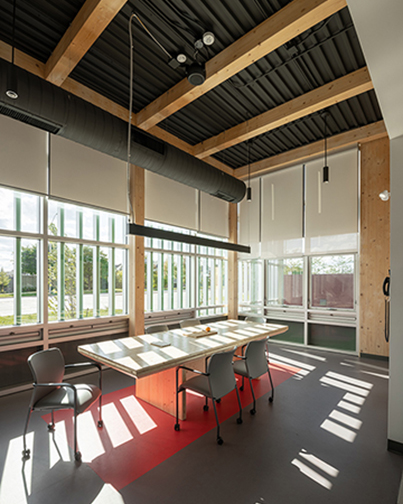