Service: Sustainability
Cadillac Fairview
Toronto Dominion Centre
HH Angus has been working at this site since the earliest days of the Toronto Dominion Centre, Canada’s first skyscraper. We provided complete mechanical and electrical engineering services to the Toronto Dominion Bank and Cadillac Fairview (CF) in the construction of the first four towers, which total 5,600,000 ft2.
Those original iconic towers (now six) and the interconnecting below-ground shopping concourse comprise office space, underground parking and a retail and restaurant complex in the heart of downtown Toronto.
With the certification of 95 Wellington as Gold Level WELL Core, the entire TD Centre is now WELL certified, the largest real estate complex in Canada to have achieved this designation.
We have been involved in numerous technical infrastructure upgrades, including the installation of heat exchangers to the cooling plant in order to link to the Deep Lake Cooling system. We have provided detailed redesign of the service floors so that the space previously occupied by the cooling plant can be upgraded.
The Toronto Dominion Tower, the tallest at fifty-five stories, employs a perimeter induction heating and cooling system; all other buildings, which were designed later, employ variable air volume systems. Each building has a number of air handling plant room floors located approximately every twelve floors. This helped to minimize the size of individual pieces of equipment and the on-floor shaft sizes required.
Steam is used as the prime heating and humidification source for the Centre. Supplied from the Enwave District Energy System, the steam demand is rated at more than 70,000 kg/hr. The cooling load of over 49,000 kW is supplied by the Deep Lake Cooling system.
As part of the ongoing evaluation and revision of existing mechanical and electrical systems for this property, CF has invested in a new luminaire and ceiling combination. This investment provides tenants with base building illumination of a high quality while reducing the total lighting power density for building operations. This new luminaire system, in combination with accurate metering and appropriate building automation, is contributing to CF’s success in meeting and exceeding the ASHRAE 90.1 energy standards.
SERVICES
Mechanical Engineering | Electrical Engineering
PROJECT FEATURES
Size: 5,600,000 ft2 | Status: Ongoing
LOCATION
Toronto, Ontario
KEY SCOPE ELEMENTS
Ongoing technical infrastructure upgrades | Installed heat exchangers to link the cooling plant to the Deep Lake cooling system | LEED Gold
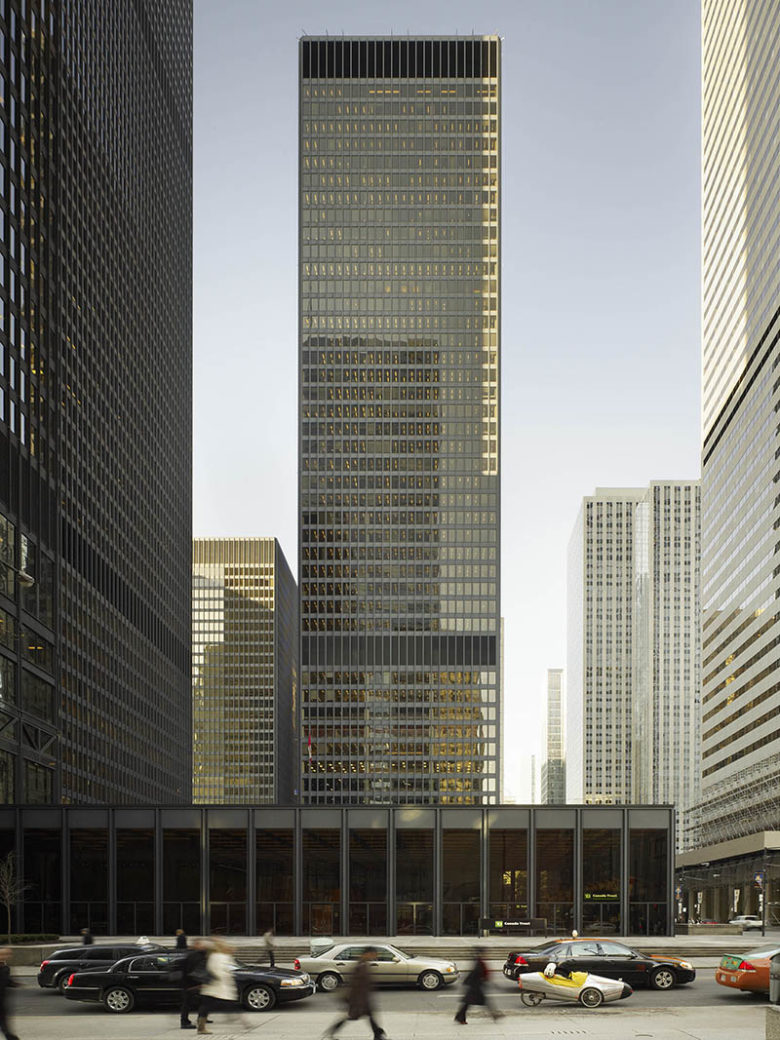
The imperative of good service
“The volume of work which you perform here at the TDC, I believe, is a direct reflection of your team’s reliability, high performance, and value.”
Adrian Sluga, Former Senior Manager, Tenant Projects, Cadillac Fairview
A lasting impression
TD Centre Heritage Designation:
The TD Centre in Toronto was designed by Ludwig Mies van der Rohe and, from 1967 to 1972, was the tallest building in Canada. A leading example of the International style, the TD Centre altered the city’s skyline while influencing many subsequent buildings across the nation.*
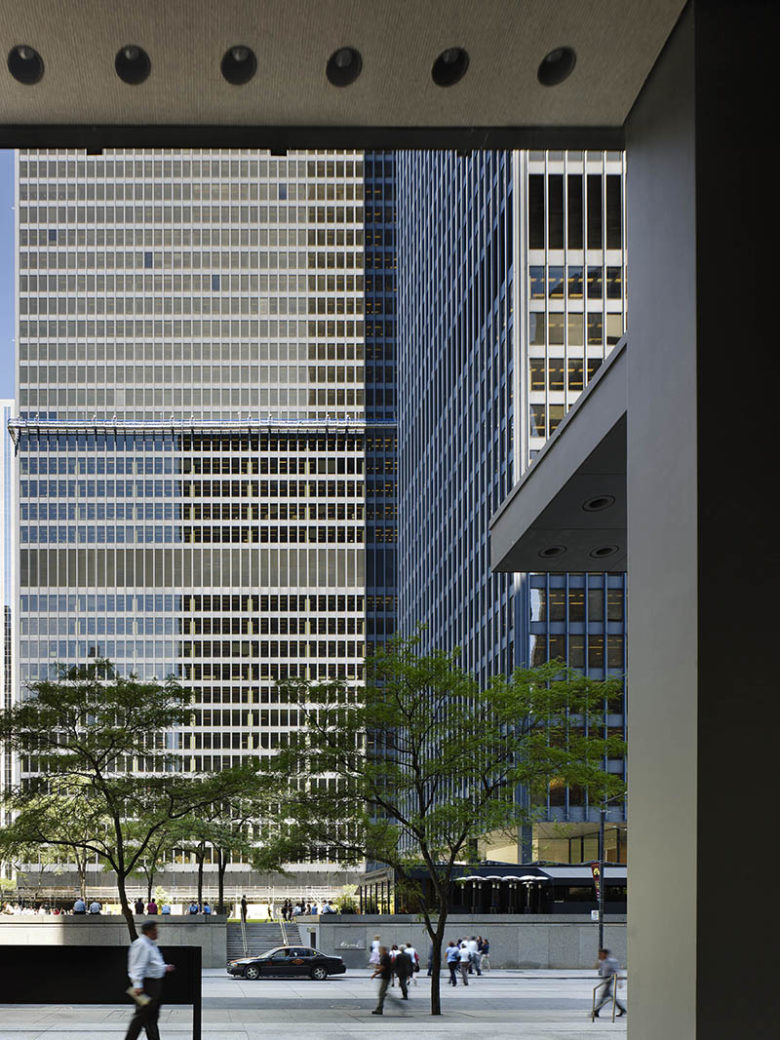
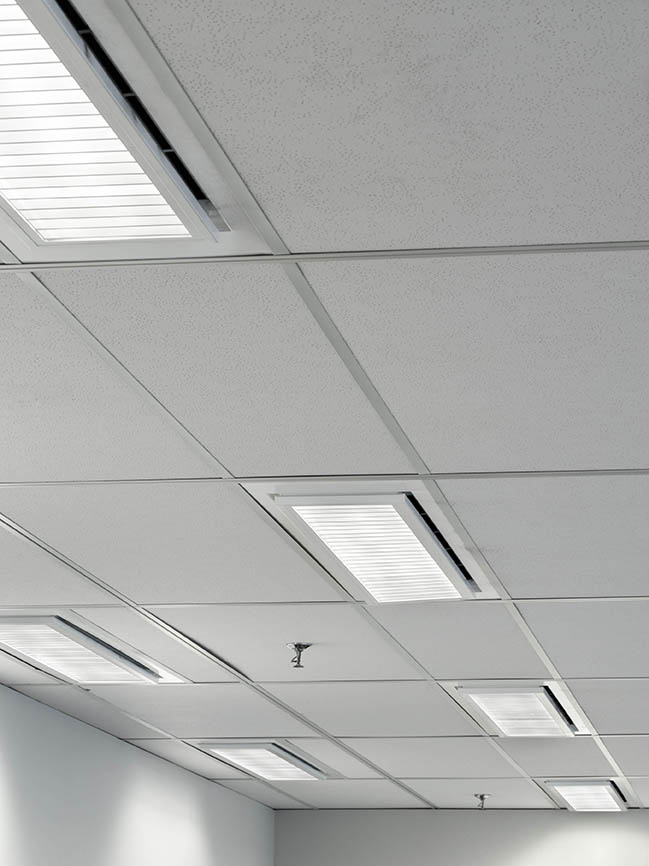
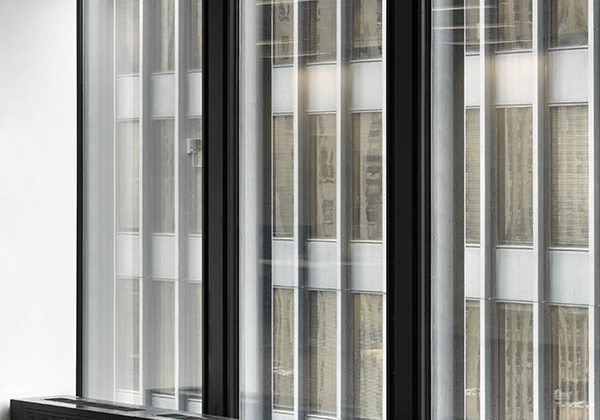
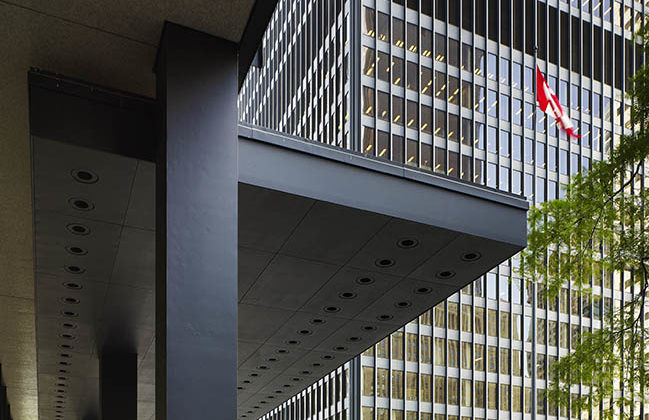
Infrastructure Ontario/Metrolinx
Eglinton Crosstown Light Rail Transit
This project is the largest transit expansion in Toronto’s history, and one of the largest P3 projects in North America. When complete, it will move people 60% faster than existing bus service and will accommodate ten times as many passengers.
The new light rail transit line runs along Eglinton Avenue between Mount Dennis Station (Weston Road) in the west and Kennedy Station in the east. The 19-kilometre corridor includes a 10-kilometre underground portion between Keele Street and Laird Drive. The line features 25 stations and stops, with links to bus routes, 3 subway stations and various GO Transit lines. HH Angus is providing mechanical and electrical consulting engineering for three stations – Mt. Pleasant, Leaside (Bayview) and Laird.
HH Angus’ mechanical scope includes ventilation and air conditioning of services spaces, sanitary and storm drainage throughout the station, track level and specialty trackwork drainage, fire protection systems for retail and service areas, water efficient plumbing fixtures and energy efficient HVAC systems.
Electrical scope covers power distribution, lighting and communications systems. Design layouts are provided for power distribution of the subway station, as well as traction power for the trains.
The lighting design features reduced power consumption. Exterior public areas lighting designs incorporate increased daylight levels, LED lighting in pylon signs, and energy efficient lighting in illuminated wayfinding signage to minimize power consumption.
Communications systems design includes fire alarm protection, public address speakers, passenger intercom, TTC pax telephones, public telephones and security systems including closed circuit television.
SERVICES
Mechanical Engineering | Electrical Engineering | Communications and Security Design
PROJECT FEATURES Status: Completion 2022
LOCATION
Toronto, Ontario
KEY SCOPE ELEMENTS
Mechanical, electrical, security and communication design was provided for 3 LRT stations | Design included ventilation, sanitary and storm drainage, fire protection, plumbing and energy-efficient HVAC systems, lighting, security and communications systems | Largest transit expansion in Toronto’s history
Bermuda International Airport
Redevelopment and New Terminal
The L.F. Wade International airport is the world’s gateway to Bermuda, and the redevelopment of its existing Passenger Terminal Building (PTB) was a high priority for the small island country. Because the current terminal is prone to flooding, it is susceptible to damage from major Atlantic storms, which could seriously impact Bermuda’s vital tourism industry.
The PTB redevelopment was undertaken as a P3 project. HH Angus provided mechanical engineering and vertical transportation design for all systems serving the airside and the PTB, working with a local affiliate to deliver contract administration services during construction.
The vertical transportation scope for the project included five new machine-room-less (MRL) traction passenger elevators and four escalators.
Some of the interesting challenges of the project included its profile as an international project on an island; adapting to local authorities having jurisdiction; resistance to hurricanes; flood mitigation; and the island’s water strategy–Bermuda's building code requires that all rainwater be captured and re-used, and the new PTB represents the largest roof area in the country. Also, salt-laden air and accelerated corrosion require the use of non-traditional materials as compared, for example, to similar buildings in Canada.
Among the features of the engineering design, the high water table easily allowed for geo-thermal heat rejection for the cooling plant.
SERVICES
Mechanical Engineering | Vertical Transportation
PROJECT FEATURES
Size: 2,886,902 ft2 (26,820 m2) | Status: Completion 2020
LOCATION
St. George's, Bermuda
KEY SCOPE ELEMENTS
Five new machine-room-less (MRL) traction passenger elevators and four escalators | Innovative mechanical design | Geothermal heat rejection for cooling plant | Mandated rainwater reuse for largest roof area in the country
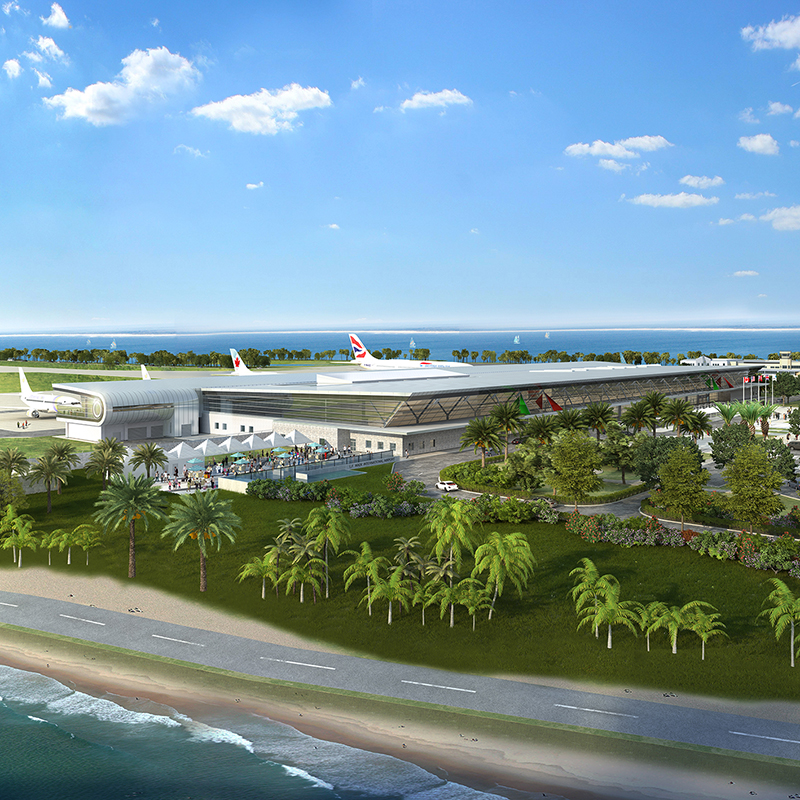
Innovation and Excellence Award
The Bermuda airport project was awarded a 2021 Gold Award for Innovation and Excellence in P3s, from the Canadian Council for Public-Private Partnerships. It is only the second international project recognized by the
CCPPP in its history.
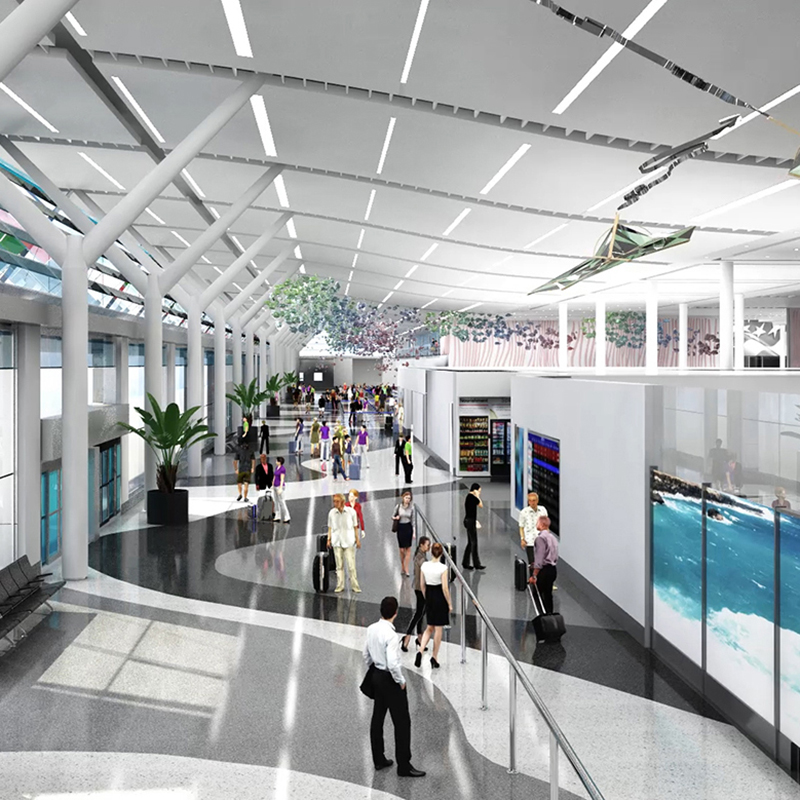
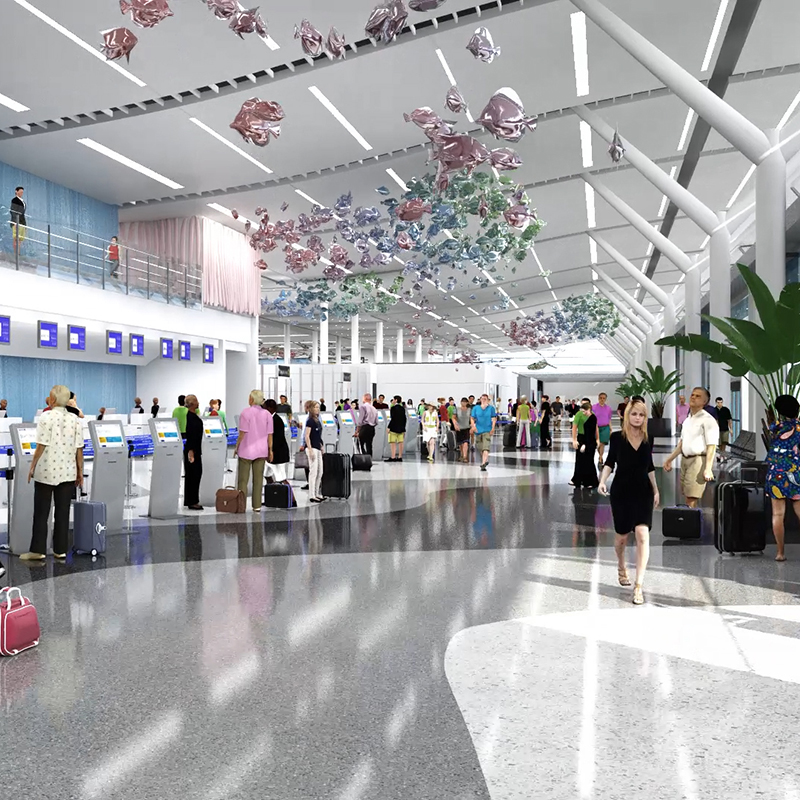
— Renderings courtesy of Scott Associates Architects Inc.
Fraser Health Authority
Royal Columbian Hospital Redevelopment
The Royal Columbian Hospital is the oldest hospital in the province of B.C. and one of the busiest in the Fraser Health Authority. Royal Columbian provides expert care to the province's most seriously ill or injured. It is the only hospital in B.C. that caters to trauma, cardiac care, neurosurgery, high-risk, obstetrics, neonatal intensive care, and acute mental health care all on one site.
HH Angus and Associates is serving as the Planning, Implementation and Closeout Consultant for the Fraser Health Authority’s large, multi-phase redevelopment for Royal Columbian Hospital (RCH) in New Westminster, BC.
RCH is British Columbia’s oldest hospital, and one of only two adult trauma centres in the Lower Mainland. The plan, rolling out in three proposed phases over a decade, will see a major expansion of the acute care campus, with upgrades to critical infrastructure.
Phase 1 included a number of projects to help prepare the hospital’s infrastructure for future expansion. These were a new energy centre; a five-storey, 75-bed mental health and substance abuse facility; underground parking for 450 cars; and a regional data centre which will serve all Fraser Health sites, including 12 hospitals and a large group of community healthcare centres serving a population of 1.6 million.
Phase 1 design challenges included the site itself, which is a steeply sloped, truncated triangle constrained on four sides by roadways. Working closely with CannonDesign, we developed an Indicative Design to ensure the site would work for a mental health building while accommodating the energy centre.
Other challenges included complex scheduling issues to maintain reliable services to the site as the new Energy Centre replaced the old one, and the design of a new, large heating, cooling and electrical plant to serve the current and future RCH campus. HH Angus engineers drew on their deep experience in delivering large healthcare projects to project the future heating, cooling and electrical demands on the Energy Centre that would support the long-term needs of RCH for buildings not yet designed.
Phase 2’s new Acute Care Tower will house a number of services, including emergency, surgery, intensive care and inpatient rooms. Expansion and renovations to the existing buildings will follow in Phase 3. New buildings will be designed to LEED Gold green building standards, and incorporate BC wood, as part of Fraser Health's and the Province's commitment to sustainability.
Image courtesy of Fraser Health.
SERVICES
PDC - Mechanical Compliance Engineering | Electrical Compliance Engineering | Vertical Transportation Compliance
PROJECT FEATURES
Status: Phase 1 – work is finished, Phase 2 – ongoing | Buildings being designed to LEED Gold
LOCATION
New Westminster, BC
KEY SCOPE ELEMENTS
Planning, Implementation and Closeout Consultant | Phase 1 includes a number of projects to help prepare hospital infrastructure for future expansion | Phase 2 Acute Care Tower
Toronto Dominion Bank
TD 23
TD Bank Group was awarded the world’s first WELL™ Gold certification for their TD23 pilot project. This ground-breaking achievement was a milestone in the development, growth and expansion of the WELL™ Certification program.
HH Angus is proud to have participated in the first project to be certified WELL Gold by the International WELL™ Building Institute (IWBI) through version 1 of its WELL Building Standard (WELL). We congratulate TD Bank Group for the success of their pilot project – the 23rd Floor of Tower One at the Toronto Dominion Centre. The project provided us with an excellent understanding of the WELL™ certification process.
The WELL™ Building Standard is the first of its kind to focus on the health and wellness of building occupants. It identifies performance metrics, design strategies and policies that can be implemented by owners, designers, engineers, contractors, users and operators of buildings. We believe the Standard has the potential to be widely embraced and adopted in conjunction with current LEED practice, so we were delighted to be involved with WELL™ in its early stages.
SERVICES
Mechanical Engineering | Electrical Engineering
PROJECT FEATURES
Status: Completed 2018
LOCATION
Toronto, Ontario
KEY SCOPE ELEMENTS
Canada's 1st Integrated Project Delivery (IPD) for commercial interior | LEED Platinum certified | WELL™ | Gold Certified
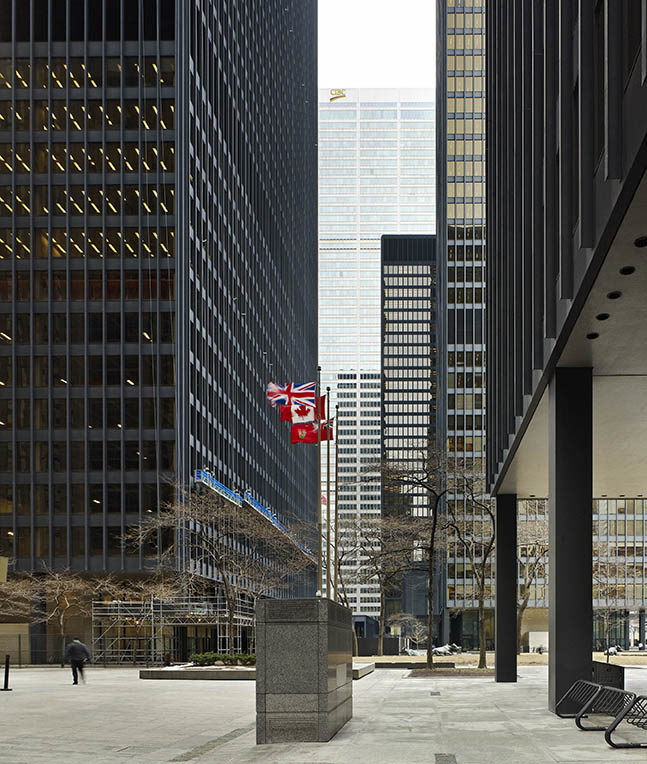