Service: Sustainability
SickKids
Peter Gilgan Centre for Research & Learning
“This investment in the Research and Learning Tower will help ensure that Canada remains a world leader in health research, and that we will continue to make discoveries that benefit children around the world.”
– Gary Goodyear, Minister of State for Science and Technology
HH Angus provided mechanical and electrical consulting engineering for this 740,000 ft2 high-rise research and educational facility. This building enhanced the overall campus of SickKids, which totals over 2,500,000 ft2. SickKids is a landmark hospital and renowned internationally as a world-class institution.
The facility has been certified LEED® Gold. Energy modeling indicated a significant improvement over the minimum energy performance required by the program. Systems were segregated to achieve significant thermal reuse within the facility. The option to integrate a waste heat recovery system from the neighbouring district heating provider was incorporated into the design to realize even greater energy efficiency in future.
The building services design supported the main objectives for the new facility:
- Consolidate the Research Institute into a cohesive unit
- Integrate research functions with the hospital
- Provide flexibility for future change
- Maximize functionality and efficiency
- Share support functions
- Utilize current technologies and infrastructure, including a plan for increased security for highly specialized spaces such as Containment Level 3
- Incorporate exemplary sustainable “Green” building design concepts and system
- Create a high-tech, cost-effective space for evolving state-of-the-art technologies
The interesting design challenges inherent in this high-rise lab building contributed to both the complexity and enjoyment of the design process, including a 1½ storey vivarium and 40,000 ft2 of educational space.
Quote source: SickKids
SERVICES
Mechanical Engineering | Electrical Engineering | IT & Communication Design | Vertical Transportation | Lighting Design
PROJECT FEATURES
Size: 740,000 ft2 with 40,000 ft2 educational space | Status: Completed 2013
LOCATION
Toronto, Ontario
KEY SCOPE ELEMENTS
Complex systems design for a tight downtown urban space | 1.5 storey vivarium | LEED Gold Certified | Incorporated options to permit a future waste heat recovery system
Toronto Transit Commission
Toronto-York Spadina Subway Extension Pioneer Village & Finch West Station
The TTC’s 8.6 km line opened to the public in December 2017. All six stations are fully accessible and Wi-Fi equipped. The line is comprised of both tunnel and cut-and-cover sections. HH Angus provided mechanical and electrical consulting engineering for the Pioneer Village and Finch West stations.
Above ground, the new stations include a main entrance, secondary and automatic entrance and electrical substation. Our mechanical scope included ventilation and air conditioning of services spaces, sanitary and storm drainage for washrooms and service area, track drainage, fire protection systems, as well as incorporation of system-wide tunnel ventilation. In addition, it incorporated water-efficient plumbing fixtures and energy efficient HVAC systems.
Our electrical scope covered power distribution, lighting and communications systems. Design layouts were provided for power distribution of the subway station, as well as traction power for the trains.
SERVICES
Mechanical Engineering | Electrical Engineering | Lighting Design | Communications Consulting
PROJECT FEATURES
Status: Completed 2017
LOCATION
Toronto, Ontario
KEY SCOPE ELEMENTS
Underground subway stations with integrated bus terminals | Integrated traction power substation | Water-efficient plumbing fixtures and energy efficient HVAC systems
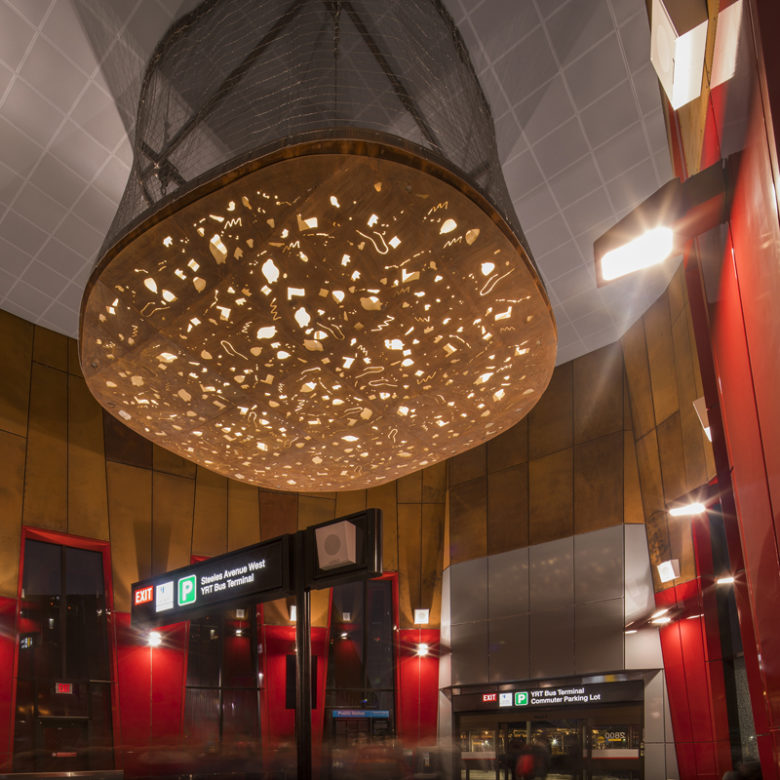
Custom transit lighting
The lighting design featured reduced power consumption. Lighting design for the exterior public zones incorporated increased daylight levels, LED lighting in pylon signs, and energy-efficient lighting in illuminated wayfinding signage.
Comprehensive communications design
The communications systems design included fire alarm protection, public address speakers, passenger intercom, TTC PAX telephones, public telephones and security systems, including closed circuit television.
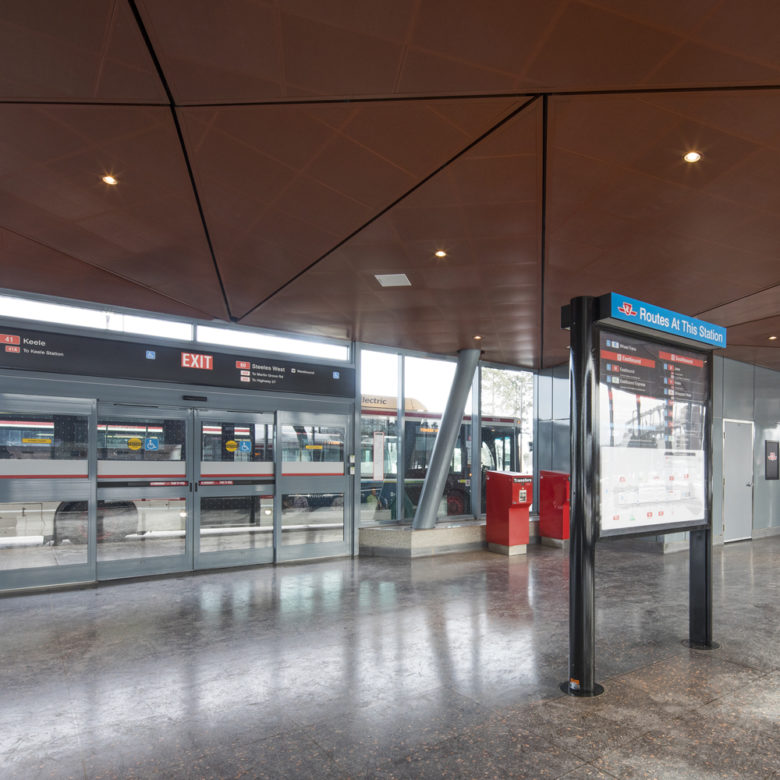
Centre hospitalier de l’Université de Montréal
(CHUM)
Designing the mechanical, electrical, and security systems for one of North America’s largest P3 acute-care hospitals required a comprehensive understanding of the crucial demands placed on a hospital’s electrical system; knowledge of the intent and intricacies of codes and standards; value-engineering approaches gleaned from alternate project delivery projects; and lessons learned from complex redevelopment projects.
The Centre hospitalier de l'Université de Montréal (translated as University of Montreal Health Centre, or CHUM) is a mega-hospital complex designed to replace three existing hospitals in Montreal. One of the largest P3 hospitals in North America, it occupies more than 2.5 city blocks with more than 334,000 m2 (3.5+ million ft2) of floor space.
The CHUM project has been honoured with ~30 awards, including Canada's top engineering award, the Schreyer Award 2018 for HH Angus, plus an ACEC Award of Excellence and three Illumination Engineering Society 2018 Awards for HH Angus’ lighting designs for the Passerelle Skybridge, the Steeple, and Interior Lighting.
The hospital complex consists of a main 20-storey acute care block, with five levels underground. The upper floors house 775 beds in single rooms, and the lower floors contain diagnostic and treatment functions, including a large emergency department, 39 operating rooms, 7 MRIs and a full cancer centre with 12 bunkers. Distinct blocks house ambulatory care clinics, office space and logistics. Our scope also included two large data centres.
The facility has been certified LEED® Silver. HH Angus responded to a number of restrictions and requirements in the RFP with alternative approaches that were subsequently implemented, benefitting the project in terms of better functional use of space, flexibility for the future, cost savings and significantly improved energy efficiency.
SERVICES
Mechanical Engineering | Electrical Engineering | Security Systems Design
PROJECT FEATURES
Size: 3,800,000 ft2 | Status: Phase 1 - 2017 | Ongoing renovations and upgrades | Winner - 2018 Schreyer Award, Canada's top engineering project award
LOCATION
Montréal, Quebec
KEY SCOPE ELEMENTS
Mechanical, electrical and security system designs were provided to facilitate concurrent development | More than 50 Revit® models linked | Project included components that would help future modification of the facility | Certified LEED Silver
A proven P3 approach
HH Angus developed an approach to deliver consistency and standardization of mechanical and electrical products with multiple contracts and installation contractors. To facilitate the concurrent development of multiple parts of the project, more than 50 Revit models were linked. This allowed work to proceed on construction documents for the core and shell of the building (including services), while design development continued in the clinical areas of the building.
Experience creates long-term efficiency
The RFP mandated a number of restrictions on the ventilation system that would have required two full intermediate mechanical floors and would have severely compromised future flexibility. We worked with CHUM and the proponent team to develop an alternative approach from which numerous benefits resulted, including the ability to modify occupancy and enable future renovations, which allowed an extra clinical floor to be constructed under the zoning height restriction.
Delivering more value
The RFP required a distinct air handling unit for each functional department, as well as restrictions on unit size and floors served. HH Angus proposed the use of larger, 100 percent outdoor air units serving multiple floors. We proved the merits of this approach to CHUM from an infection control perspective.
Proving a better solution to save energy
The RFP did not allow the use of heat recovery wheels due to perceived infection control concerns. We used 20+ years of successful experience with heat wheels to prove the approach to the client and compliance team. The RFP was modified to allow the use of heat wheels, enabling a much more cost effective and energy efficient solution.
Saving the client money
The RFP mandated a standby air handling unit for each critical care space, which would have required much higher capital and operating costs over the life of the building. We recommended manifolding a number of air handling units together to share the redundant capacity. This approach considerably increased overall reliability of the systems while reducing operating costs.
Robust, reliable, cost-effective electrics
Similar components in the electrical infrastructure were procured in separate equipment tender packages to obtain best pricing directly from the corresponding vendors. The installation scope was divided into sectors within the building and awarded to separate electrical contractors. This “carving up” of the design scope into multiple tender packages required a high degree of coordination with the DBJV, and was effective in keeping this massive ongoing project on track with budget and schedule.
Multifunctional security system design
Our Angus Connect Division designed a fully convergent IP-based (Internet Protocol) security system and the supporting IT infrastructure required for a large-scale Cisco high availability, medical grade network. We designed an IP-based integrated multimedia security system that includes several thousand IP-based cameras, intelligent card readers, and other security devices located throughout the hospital complex. This system includes PoE (Power over Ethernet)-controlled architectural door hardware connected to Cisco’s high availability medical grade network.
Discrete segments of the security system are reserved for clinical observation, parking control, visitor management, patient wandering and duress applications. Multiple control facilities were provided across the hospital, using multicasting over VLAN, configured on Cisco LAN.
The security system was designed to support sophisticated client “use and workflow cases”, providing interoperability, SOA (Service Oriented Architecture) and SOI (Service Oriented Infrastructure).
Angus Connect integrated all aspects of the security systems into a seamless and efficient operation, leveraging the most current technology wherever possible to improve efficiency, reliability and safety, thus simplifying information flow and access to users.
Bruce County Long Term Care
Brucelea Haven | Gateway Haven
Established in 1898 as the "House of Refuge", Brucelea Haven has been providing residential long term care (LTC) for seniors for more than a century. Built in 2003, both Brucelea and Gateway facilities operate as not-for-profits.
Brucelea Haven and Gateway Haven were constructed to replace separate, outdated existing LTC facilities. The 93,161 ft2 Brucelea Haven facility in Walkerton features 144 beds with two resident floors located over a partial lower floor that houses day facilities and support services. Gateway Haven in Wiarton provides the community with 100 beds over 67,062 ft2 on three resident floors, with a lower floor plan similar to Brucelea.
HVAC systems were a prime consideration in the design of the new facilities, due to the ongoing problems in the old structures. The mechanical design incorporates total enthalpy heat recovery wheels for ventailation for the resident wings. Boilers are high efficiency, feeding hot water to heating coils that provide local room control on a grouped basis.
Both projects qualified under the Federal Government CBIP program for using 25% less energy than a building meeting the National Energy Code.
SERVICES
Mechanical Engineering | Electrical Engineering
PROJECT FEATURES
Status: Completed 2003
LOCATION
Brucelea Haven - Walkerton, ON Gateway Haven - Wiarton, ON
KEY SCOPE ELEMENTS
Long Term Care residential facilities | Projects qualified under Federal CBIP program by using 25% less energy | High efficiency boilers | Total enthalpy heat recovery wheels for ventilation
St. Michael’s Hospital
Peter Gilgan Patient Care Tower
HH Angus is part of the Compliance Team for the new 17-storey Patient Care Tower. The Tower will provide an additional ~250,000 ft2 to the Hospital’s main campus at 30 Bond Street, with an additional ~150,000 ft2 of renovation distributed throughout the existing building.
The new tower will allow patient care to move out of aging and inadequate space, clinical programs and services to be right-sized to meet current standards, and costly, leased administrative space to be repatriated.
The project includes five new operating rooms, enlarged, state-of-the art facilities for orthopedic surgery, coronary care and respirology, an expanded emergency department, and the demolition and new construction of the Shuter Wing. The project is targeting LEED Gold certification.
SERVICES
Mechanical Compliance Engineering | Electrical Compliance Engineering | ICAT Compliance Consulting
PROJECT FEATURES
Size: 26710 m2 | Tertiary Care Hospital | Status: Current
KEY SCOPE ELEMENTS
17 storey patient care tower | Integration of new and existing M&E and IMIT infrastructure | Targeting LEED® Gold
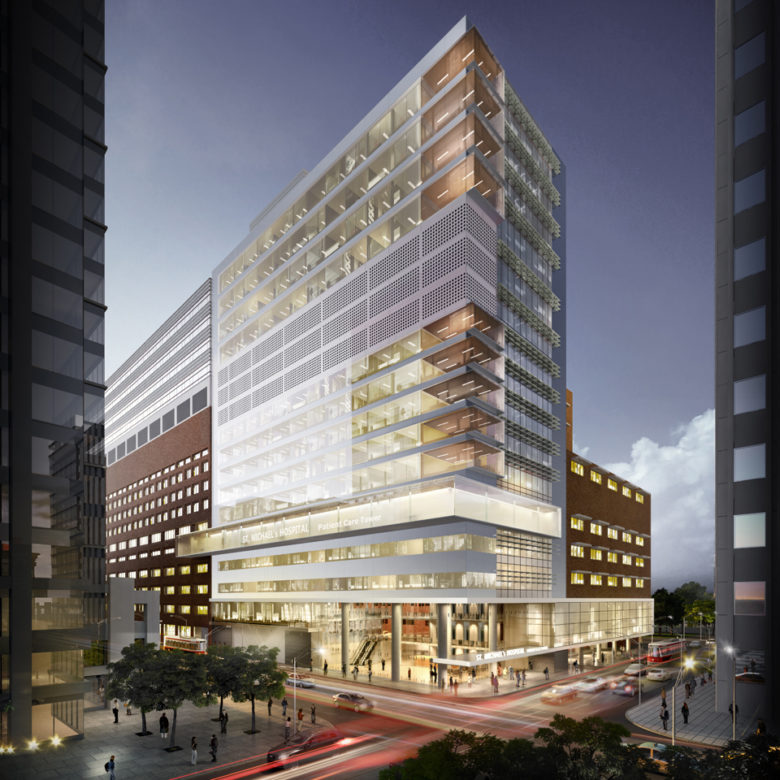
Integrating old and new buildings
Addressing major renovations and integrating new infrastructure with existing systems was a key challenge for the team. To address this, HH Angus provided detailed background information and on-site investigation to mitigate the risks to the Hospital.
IMIT challenges
This challenge extended to the IT systems, where the team had to integrate existing IT infrastructure with the new building. Extensive work was required to bring the Hospital’s aging IT infrastructure up to current standards, and to provide future flexibility. HH Angus designed a solution that would properly integrate and communicate with both new and existing systems.
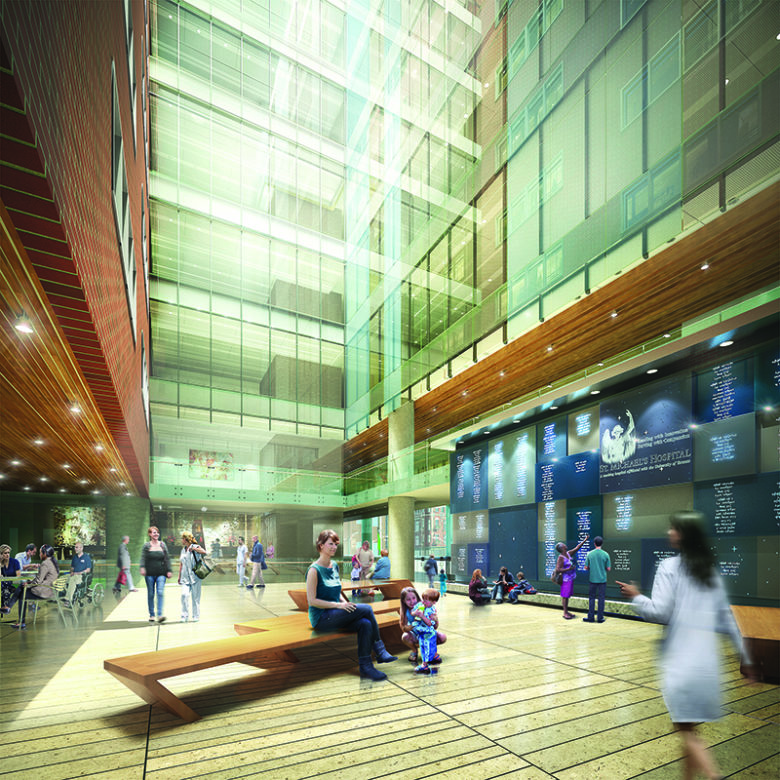
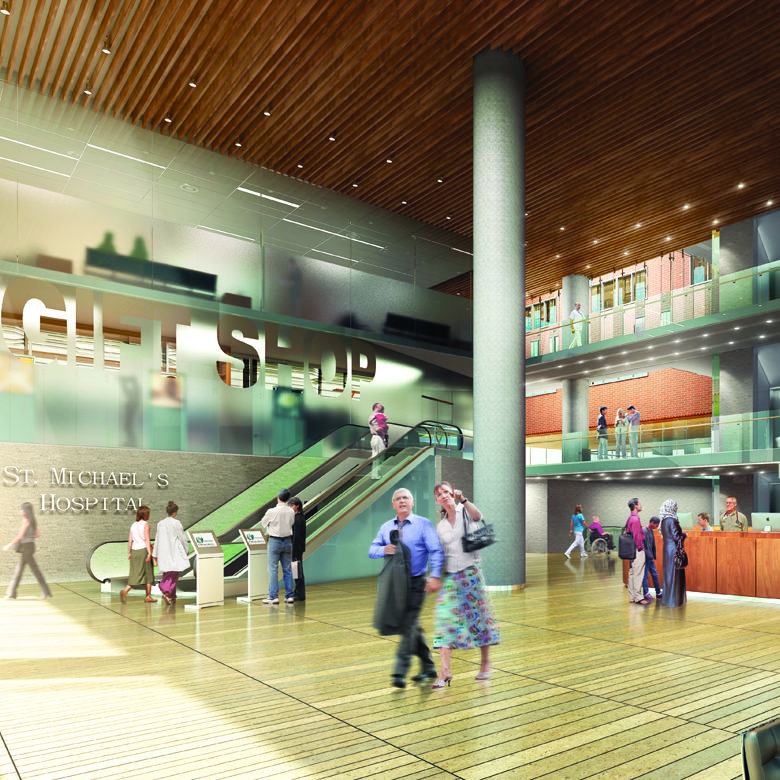
Daylight harvesting
The Tower’s atrium, with 11 storeys of natural light, will feature retail space, a patient information centre, and the Admitting Department.
— Renderings courtesy of Cicada Design