Service: Tenant Improvements
The Co-operators Calgary
Tenant Fitout
This project focused on a tenant renovation of two floors in The Co-operators' newly-acquired downtown Calgary office space, and comprised 40,000 square feet. The project has been certified WELL Gold.
Our approach included early coordination with the landlord to ensure handover conditions suited the client’s requirements, as well as close coordination with the construction manager in creating a pre-order due to a condensed construction schedule.
The construction schedule was a key challenge of the project along with the timing of tender. The completion date was an unmovable milestone as the client’s lease was expiring at their other location. At time of tender, product and material availability were fluctuating, which created uncertainty around delivery. To meet the deadline, our team was tasked to do everything possible to ensure the success of the project and keep the schedule on track.
To help ensure timely delivery, our team incorporated a pre-order package for the construction manager to tender, which allowed products to be reviewed and released ahead of the official tender. This effort was successful and was completed according to plan; however, some delivery delays were unavoidable, due to market conditions. To mitigate the impact, we were then tasked with contacting industry partners to help expedite deliveries. In addition, alternative temporary designs were implemented to ensure the move-in date could be met by planning the switchover date once the outstanding equipment arrived.
The Calgary office marks our fifth tenant improvement project for The Co-operators, following similar fitouts for their locations in Guelph ON and Regina SK, as well as pilot projects in Montreal QC and Burlington ON.
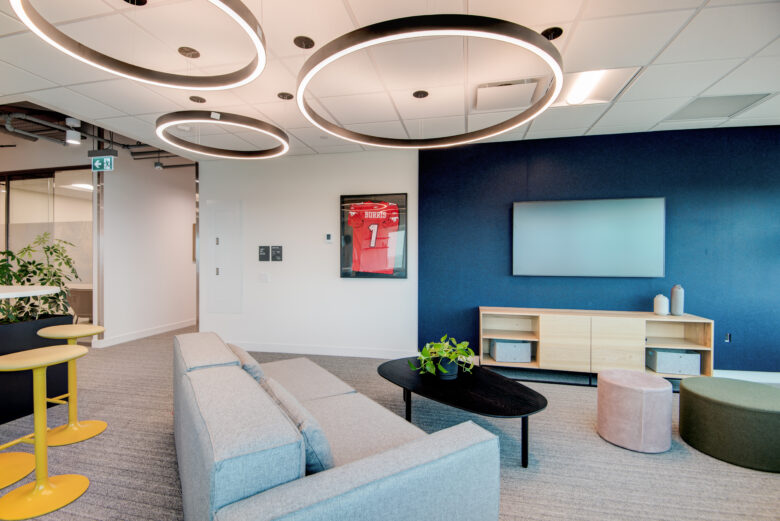
New Lutron lighting control design
New UPS N+1 Design and new LED Lighting Design
SERVICES
Mechanical Engineering | Electrical Engineering | Lighting Design | Communications & Security Design
PROJECT FEATURES
Size: 40,000 ft2 over two floors | Status: Completed 2023
LOCATION
Calgary, Alberta
KEY SCOPE ELEMENTS
Feasibility Study | Tenant renovation | Condensed construction schedule | WELL Gold certified
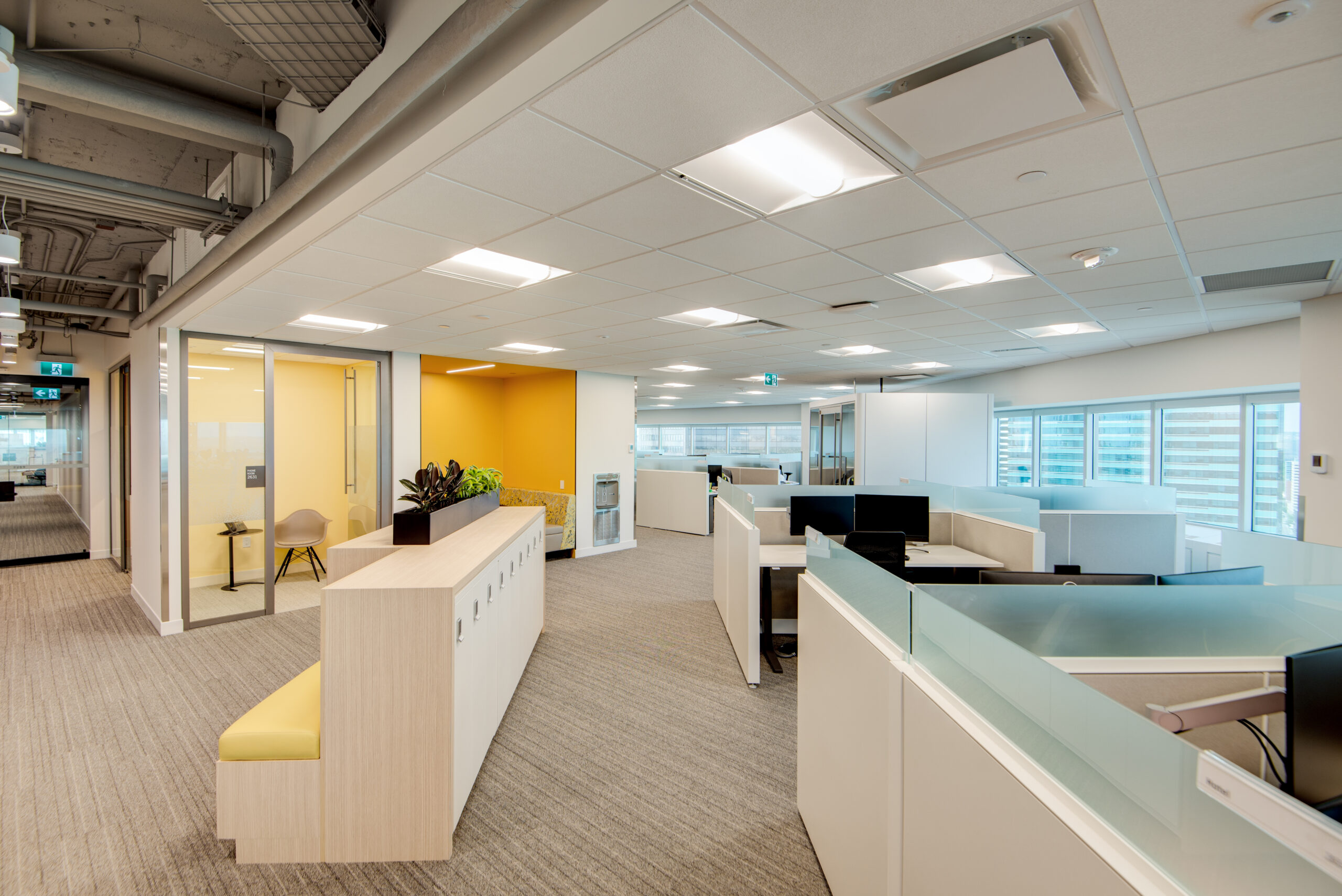
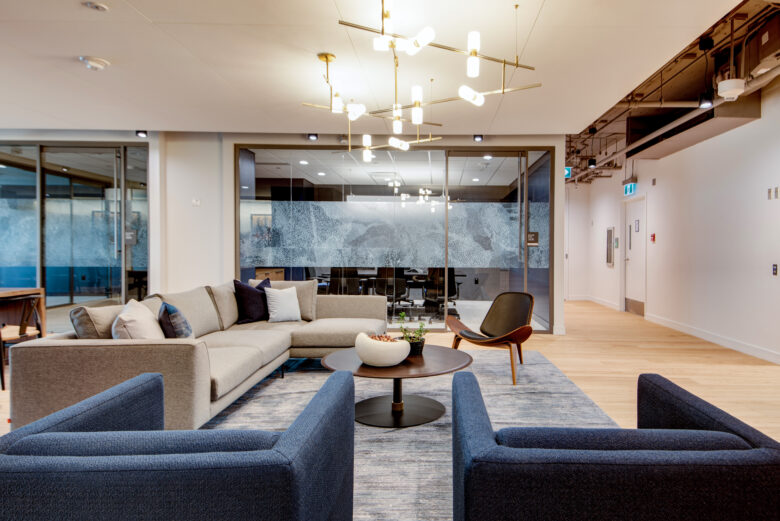
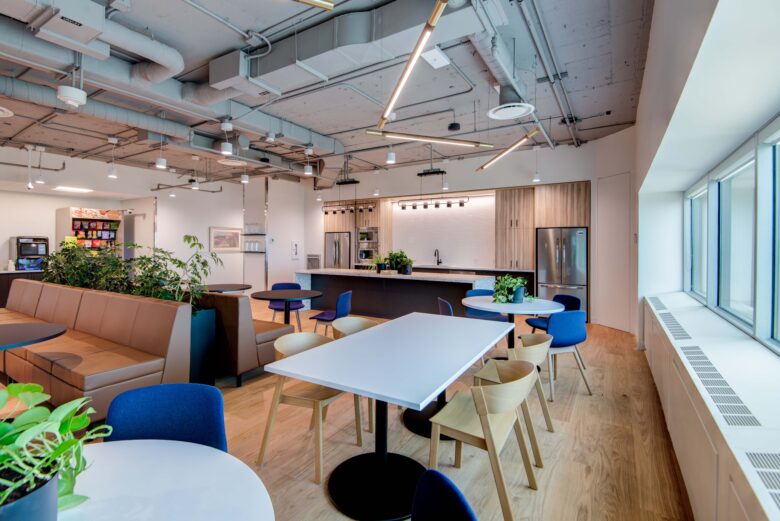
WPP
Toronto Waterfront Campus
WPP Group's building is part of the largest urban revitalization project in North America, bringing together new businesses, restaurants, and transport connections.
Work Design Magazine March 28, 2023
This cutting-edge project on Toronto’s downtown waterfront represents an evolution in commercial office development and reinvents how employees work together in Toronto’s rapidly evolving creative and technology sectors. The new space merges a large number of WPP’s operating companies and 2,000 employees into the top seven floors of the Waterfront Innovation Centre at the city’s iconic ‘Sugar Beach’. HH Angus provided engineering consulting services for this 250,000 ft2 tenant fitout project. WPP is the anchor tenant for the Waterfront Innovation Centre.
The fitout included raised floors for underfloor HVAC systems and is targeting LEED Platinum certification. On each floor, the design features a café, hub and IT equipment room, with one single Main Communications Room.
The 8th floor has a custom production area with very specific acoustic requirements. Our mechanical team worked closely with the acoustical consultant to provide a design that meets the strict acoustic requirements for video and audio production and recording. This was achieved through careful placement of fan-powered boxes equipped with silencers. The production area includes multimedia studios, photo studios and a print lab. Lighting control for these rooms is enhanced with tunable lighting, allowing users to adjust the colour temperature in real time.
The 10th floor is the client-facing floor and includes meeting rooms with fully-integrated AV, smart lighting control, open ceiling design concept (industrial design), a large point-of-sale catering kitchen with back of house facilities and an outdoor terrace.
Our communications team designed several interconnecting fibre risers to provide the client with the most cost effective solution and full redundancy to meet their current and future needs, and to ensure the system will continue to operate in the event of external critical failures.
SERVICES
Mechanical Engineering | Electrical Engineering | Communications Design
PROJECT FEATURES
250,000 ft2 colocation project unifying 28 different companies | Seven-floor fitout | Status: Completed 2022
LOCATION
Toronto, Ontario
KEY SCOPE ELEMENTS
WELL design principles | Pressurized raised floor systems with underfloor HVAC systems | Rigorous acoustic requirements for audio and video recording | Redundant interconnecting communications fibre risers to ensure system will operate in the event of external critical failures
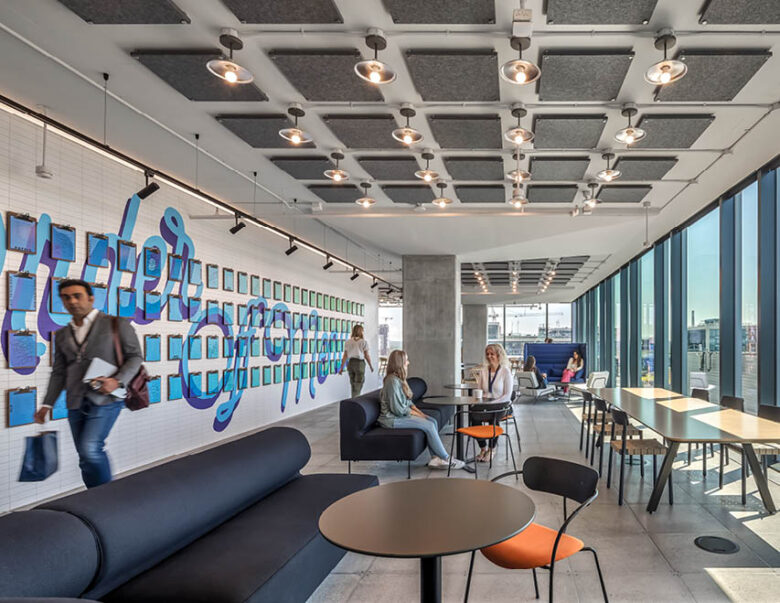
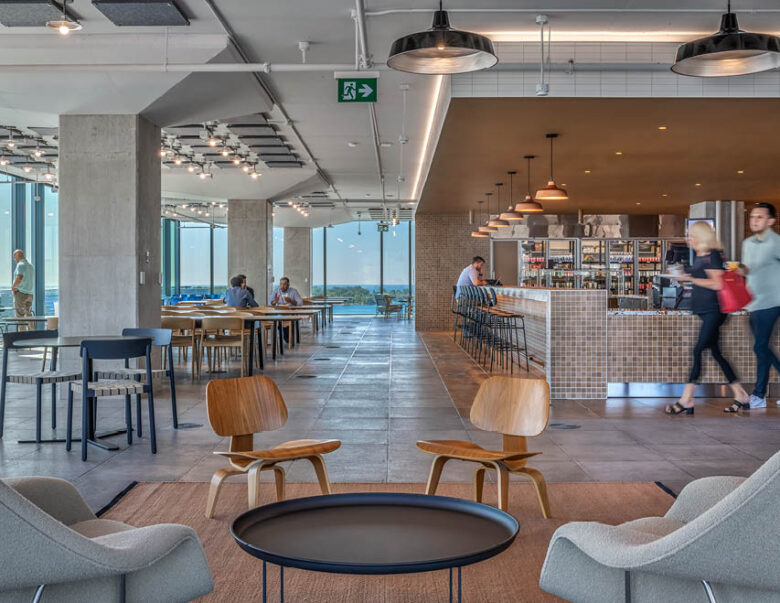
The Co-operators
National Headquarters
The Co-operators’ Headquarters in Guelph, Ontario has been certified a 'Zero Carbon Building' by the Canada Green Building Council. The project is also pursuing LEED Gold, WELL Platinum and BOMA Best certifications.
The project covers three floors totaling 226,000 ft2, and includes a data centre, cafeteria, fitness centre, conference rooms, and three-storey open atrium. HH Angus provided mechanical and electrical consulting engineering, as well as IMIT and lighting design.
The building features an all-electric design to eliminate direct carbon emissions from any on-site source. This means that the company did not need to undertake any retrofits or decarbonization plans to achieve net zero targets. The building has been designed to be highly energy-efficient and to minimize indirect annual carbon emissions from electricity.
Any remaining emissions will be offset through high-quality carbon offsets or carbon-free renewable energy sources. The construction process was also meaningfully reduced, offsetting “embodied carbon” emissions resulting from the manufacture, transportation, and disposal of all building materials.
The Canada Green Building Council has identified the building sector as Canada’s third-largest emitter of greenhouse gases (GHG). Presently, residential, commercial, and institutional buildings are responsible for 17% of Canada’s GHG emissions, and this figure approaches 30% when building materials and construction processes are taken into account.
Despite an aggressive construction schedule, the project overcame the challenges of integrating an all-electric design and achieving Zero Carbon Building certification. It also intended to surpass goals for energy and GHG savings beyond the Ontario Building Code’s all-electric baseline and heating load reduction minimum for new builds. The building features a rooftop solar array and a high-efficiency water source, showcasing innovative approaches to sustainable design.
The building’s low-impact features include:
- Energy and GHG savings 40% greater than the Ontario Building Code’s all-electric baseline
- 60% reduced heating load, surpassing the minimum code requirement for new office builds requirement for new office builds
- A 282 kW rooftop solar array that is expected to produce ~9% of the building’s annual total energy
- Automatic window tinting to reduce glare and save energy
- A highly-insulated and airtight envelope to conserve energy
- High-efficiency water source technology to recover and redistribute heat throughout the building
- LED lighting equipped with occupancy and daylight harvesting sensors that turn on only when needed
Read CaGBC's feature article about The Co-operators Guelph Headquarters.
See Interior Design Magazine's feature on The Co-operators HQ,
The Co-operators Guelph Head Office project awards:
Honourable Mention in the “Best New Build Project” category of the 2024 EM Honours Awards Program, which celebrates excellence in energy efficiency, proactive energy management and decarbonization
2025 Grand Valley Construction Association's 'Building Excellence' award, 'Specialty Award' for Innovation and Sustainability
SERVICES
Mechanical Engineering | Electrical Engineering | IMIT Consulting | Lighting Design
PROJECT FEATURES
226,000 ft2 | Status: Completion 2024 | Certified ‘Zero Carbon Building by CaGBC | Targeting LEED Gold and WELL Platinum certifications | LED lighting | Daylight harvesting
LOCATION
Guelph, Ontario
KEY SCOPE ELEMENTS
Energy and GHG savings 40% greater than all-electric OBC standard | Building designed to achieve net-zero through all-electric design, without retrofits or decarbonization | Targeting reduced embodied carbon emissions during construction, minimizing carbon footprint
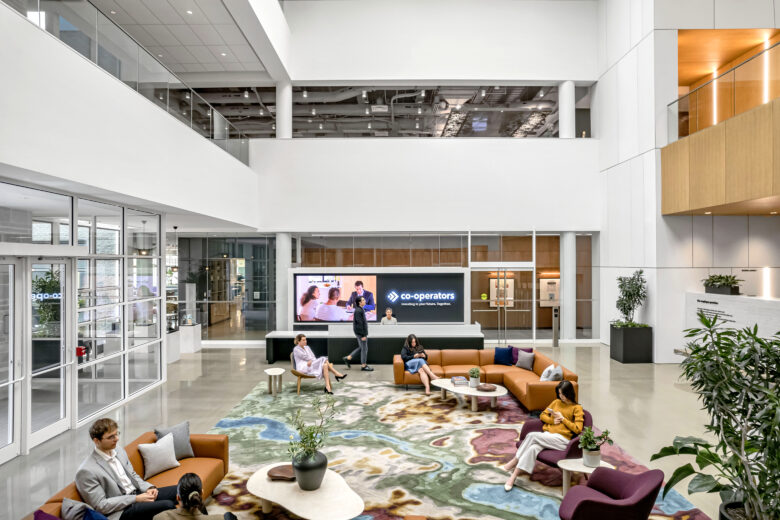
Zero carbon building
The building has attained the ‘zero carbon building design standard’ certification and is pursuing LEED Gold and WELL Platinum certifications.
Carbon offsets
The company will be offsetting embodied carbon emissions resulting from construction, manufacturing, transportation and disposal of all building materials.
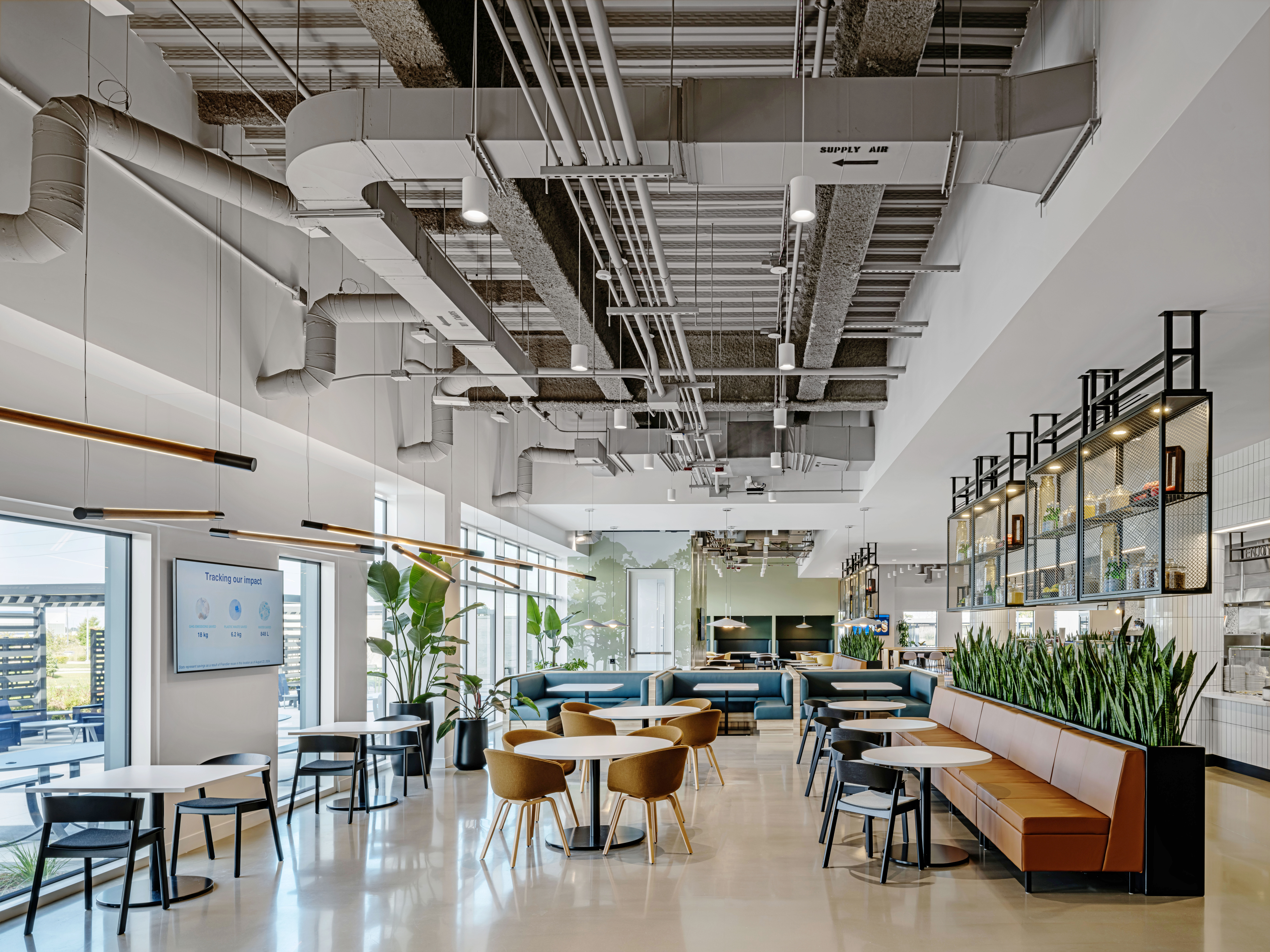
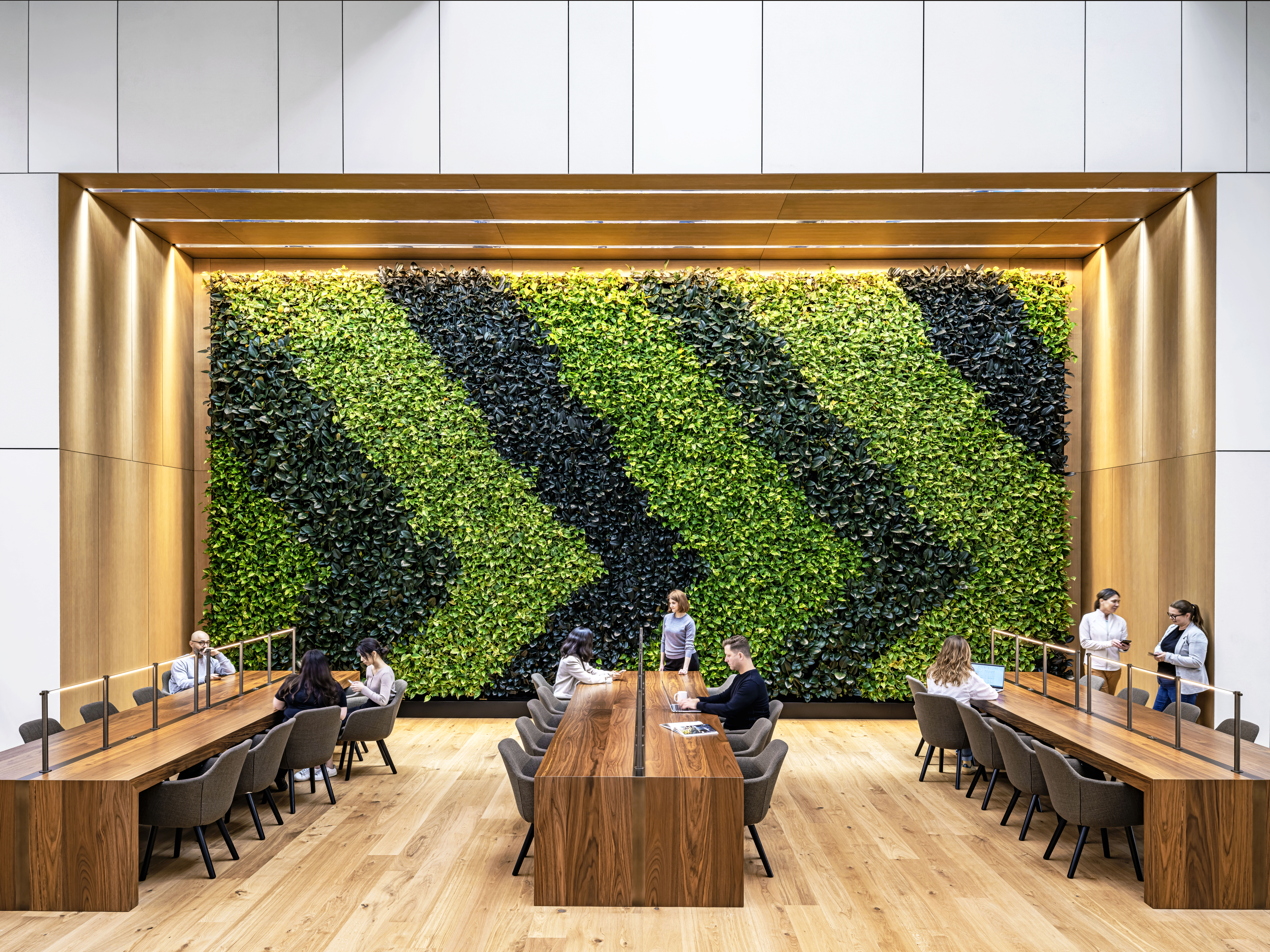
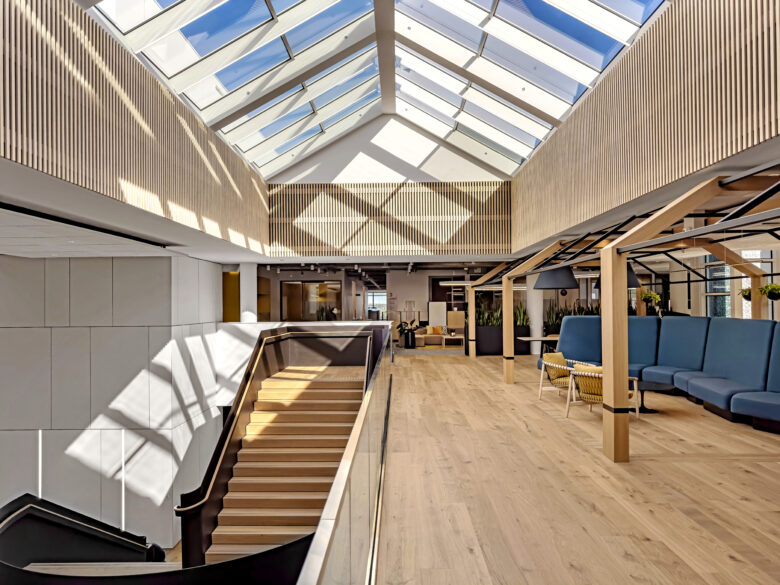
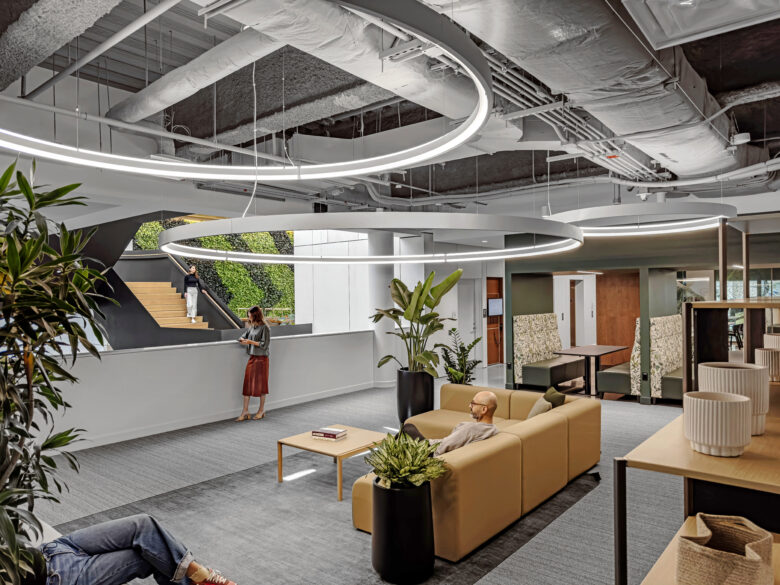
*Source: HOK Canada
AstraZeneca
Tenant Fitout
“The goal of AstraZeneca’s iWORK workplace strategy is to create facilities that meet expectations of how a great place to work should look and feel.”
AZ Workplace Strategy Guidelines
A further goal of the fitout was to use available space more efficiently to create more collaborative, vibrant working environments to achieve a science-driven, patient-focused culture and mindset.
HH Angus provided M&E consulting engineering and IMIT communications design to the project, which presented a number of interesting challenges requiring thoughtful solutions. Among the challenges was an aggressive schedule. The team worked efficiently and collaboratively to meet the project deadlines.
The project did not allow for core drilling to feed workstations or standalone furniture. To address this, the design team and engineers had to be strategic in using perimeter and under-carpet raceways to conceal wiring. A new lighting design was implemented throughout the 5th floor, and provided a sophisticated wireless lighting control system, complete with daylight harvesting and an occupancy setting, independent of the base building control system.
During the schematic design phase, our team noted several deficiencies within the existing base building system affecting the project’s location. We requested the team have a complete site audit done by a local air balancing contractor, which identified several issues with duct connections, system operation and controls. Through this process, we were able to rectify many issues prior to the close-out phase of our project. This resulted in an efficient transition for the client, saving them both time and money.
SERVICES
Mechanical Engineering | Electrical Engineering | IMIT Consulting
PROJECT FEATURES
Size: 72,000 ft2 designed for two floors of tenant fitout (one floor constructed) | Status: Completed 2021
LOCATION
Mississauga, Ontario
KEY SCOPE ELEMENTS
Open floor layout accommodated despite base building risers | Base building deficiencies identified, saving client time and money | Team exceeded contract obligations in protecting client from added costs due to COVID pandemic and to ensure timely project completion
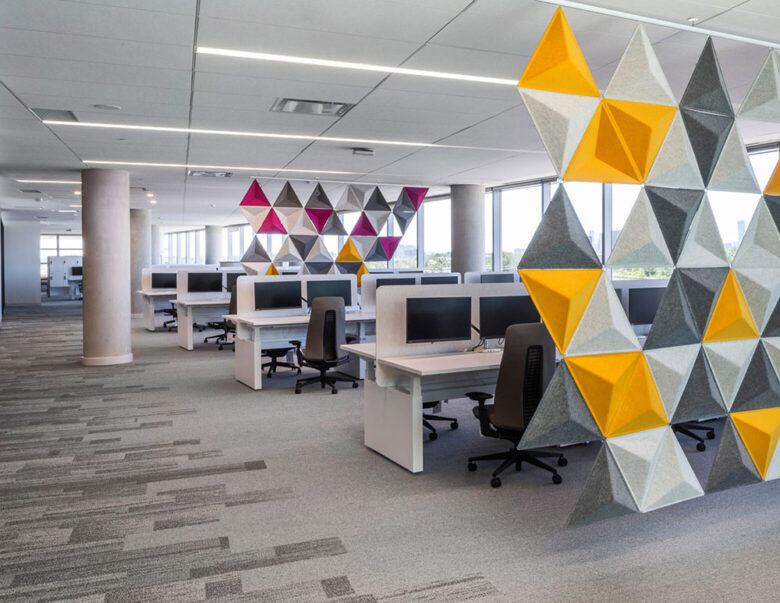
Open concept design
The client had expressed a preference for an open floor layout; however, several of the base building risers were in locations not conducive to the planned interior design. In order to accommodate the client’s wishes, we proactively identified a new shaft location, and re-routed various systems to deliver the floor layout desired by the client.
Pandemic response
The COVID 19 pandemic began in the midst of construction. The project team reacted immediately during these challenging times by providing effective and responsive coordination virtually. The team worked through construction-related delays, and helped mitigate supply distribution delays by using local contacts to expedite shipping to meet the client-requested deadlines.
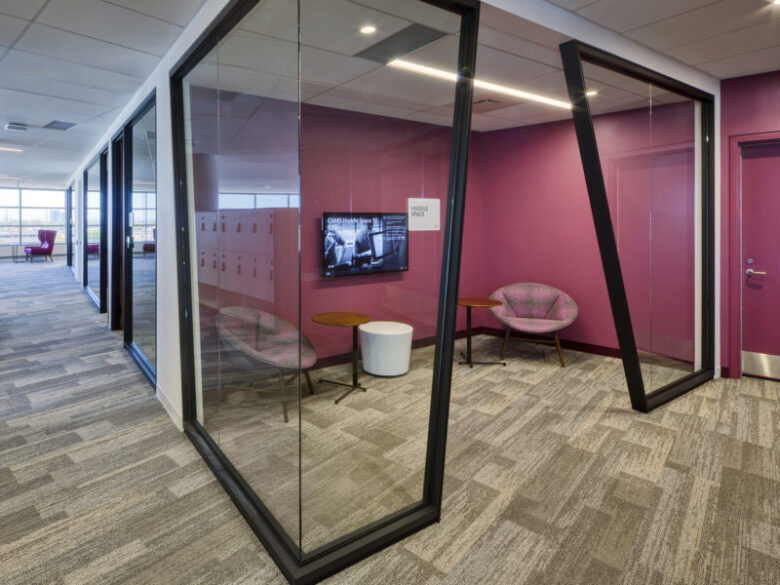
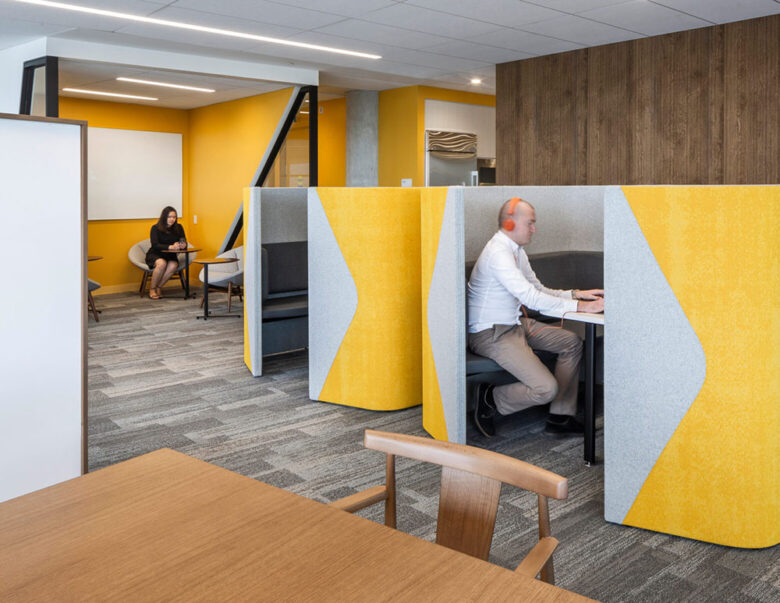
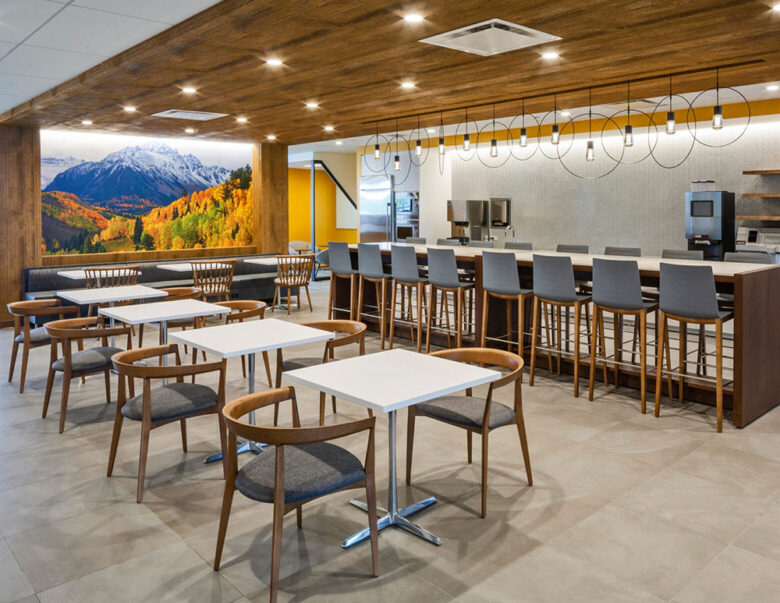
The McEwan Group
Fabbrica TD
Fabbrica's second location was designed as a take-out venue. The 4200 ft2 retail space is accessed via Toronto's underground PATH system, in the heart of the city's financial district. Fabbrica on the PATH joins its sister outlet across the hall, the McEwan grocery store.
HH Angus was engaged to provide mechanical, electrical and lighting design services for the tenant fitout of the new Fabbrica on the concourse level of the TD Centre. Fabbrica took over an existing space which required ceiling demolition in order to install new lighting and electrical systems.
Custom interior lighting was designed to attract the attention of commuters and shoppers in the PATH system. To achieve this, 3500K 12W high-colour-rendering LEDs were incorporated into the lighting design to showcase the vibrant colours of the meal offerings prepared for hungry consumers.
The project's location in the concourse level posed a design challenge to the team, due to the modest amount of ceiling and underfloor clearance. To accommodate these restrictions, HH Angus designed solutions to manage the routing of piping, conduits and drainage within the limited space.
SERVICES
Mechanical Engineering | Electrical Engineering | Lighting Design
PROJECT FEATURES
Size: 4,200 ft2 | Status: Completed 2018
LOCATION
Toronto, Ontario
KEY SCOPE ELEMENTS
Limited space above and below the retail space required innovative design approaches | High Colour Rendering LEDs
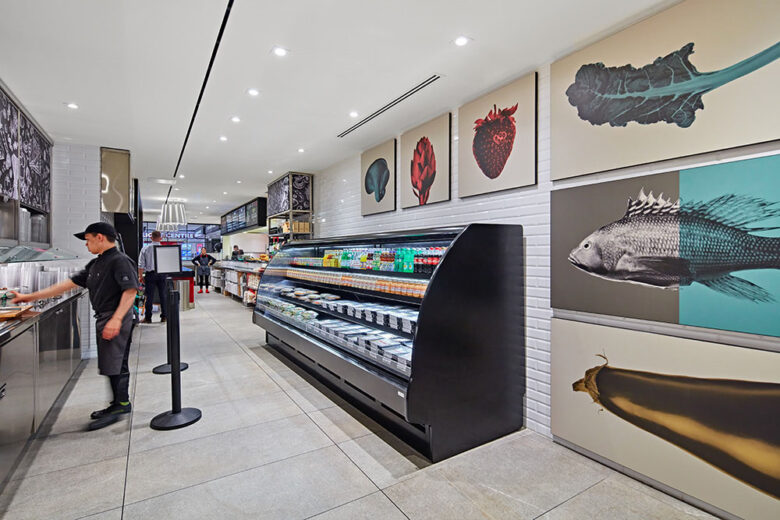
Confined spaces
The space restrictions of the site, with regard to M&E infrastructure, required extensive site surveys, plus special attention being paid to obstructions in the parking levels below.
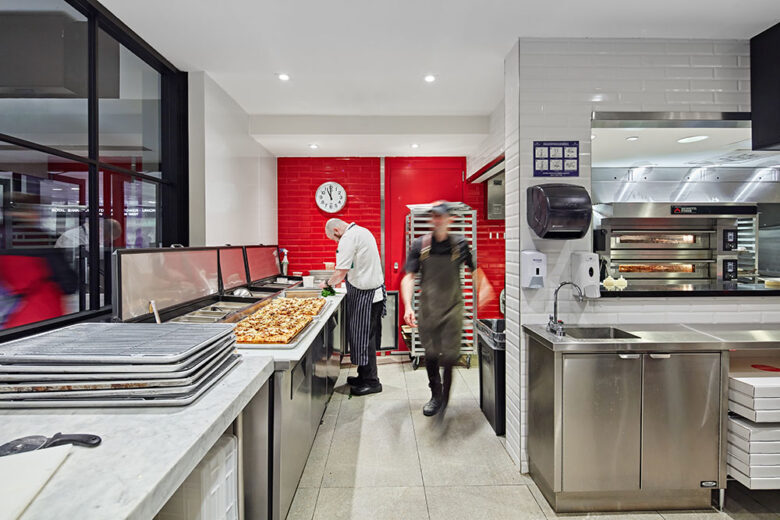
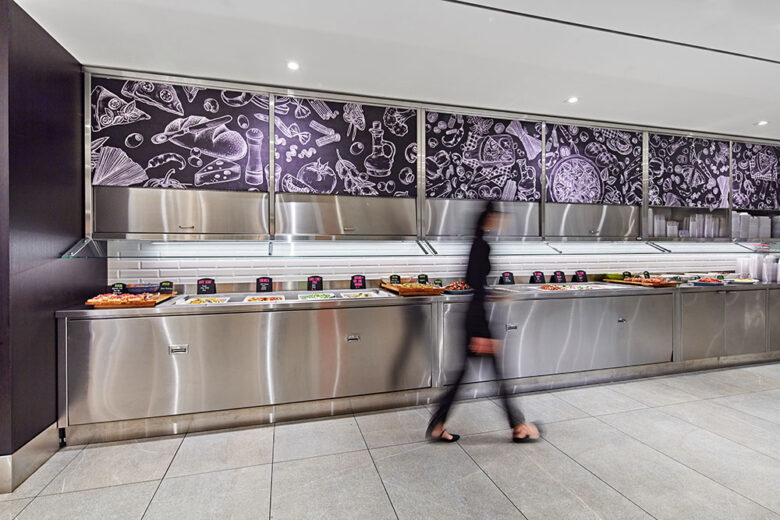