Service: Vertical Transportation
Bermuda International Airport
Redevelopment and New Terminal
The L.F. Wade International airport is the world’s gateway to Bermuda, and the redevelopment of its existing Passenger Terminal Building (PTB) was a high priority for the small island country. Because the current terminal is prone to flooding, it is susceptible to damage from major Atlantic storms, which could seriously impact Bermuda’s vital tourism industry.
The PTB redevelopment was undertaken as a P3 project. HH Angus provided mechanical engineering and vertical transportation design for all systems serving the airside and the PTB, working with a local affiliate to deliver contract administration services during construction.
The vertical transportation scope for the project included five new machine-room-less (MRL) traction passenger elevators and four escalators.
Some of the interesting challenges of the project included its profile as an international project on an island; adapting to local authorities having jurisdiction; resistance to hurricanes; flood mitigation; and the island’s water strategy–Bermuda's building code requires that all rainwater be captured and re-used, and the new PTB represents the largest roof area in the country. Also, salt-laden air and accelerated corrosion require the use of non-traditional materials as compared, for example, to similar buildings in Canada.
Among the features of the engineering design, the high water table easily allowed for geo-thermal heat rejection for the cooling plant.
SERVICES
Mechanical Engineering | Vertical Transportation
PROJECT FEATURES
Size: 2,886,902 ft2 (26,820 m2) | Status: Completion 2020
LOCATION
St. George's, Bermuda
KEY SCOPE ELEMENTS
Five new machine-room-less (MRL) traction passenger elevators and four escalators | Innovative mechanical design | Geothermal heat rejection for cooling plant | Mandated rainwater reuse for largest roof area in the country
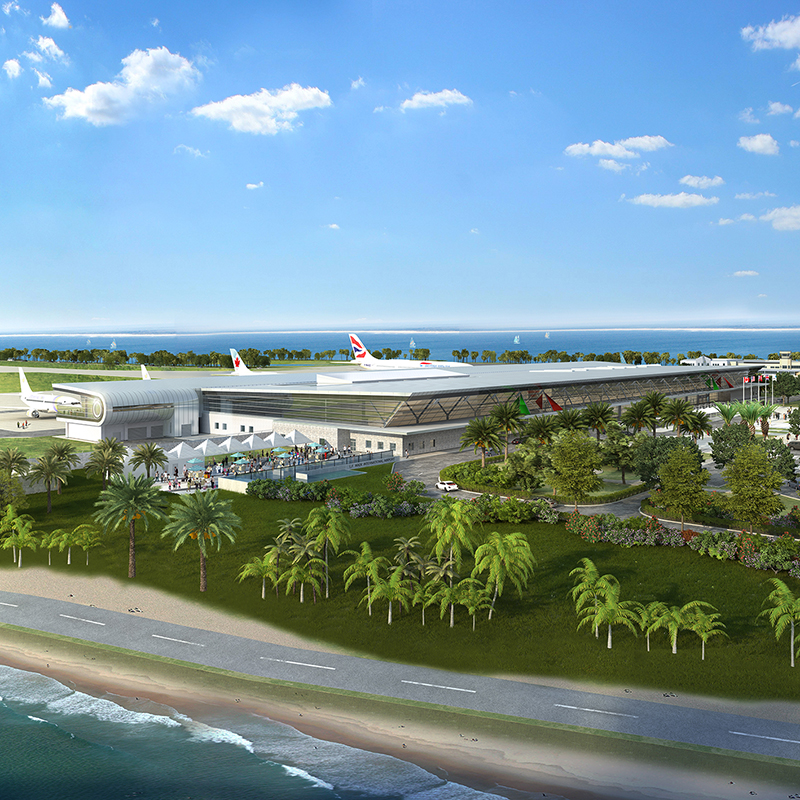
Innovation and Excellence Award
The Bermuda airport project was awarded a 2021 Gold Award for Innovation and Excellence in P3s, from the Canadian Council for Public-Private Partnerships. It is only the second international project recognized by the
CCPPP in its history.
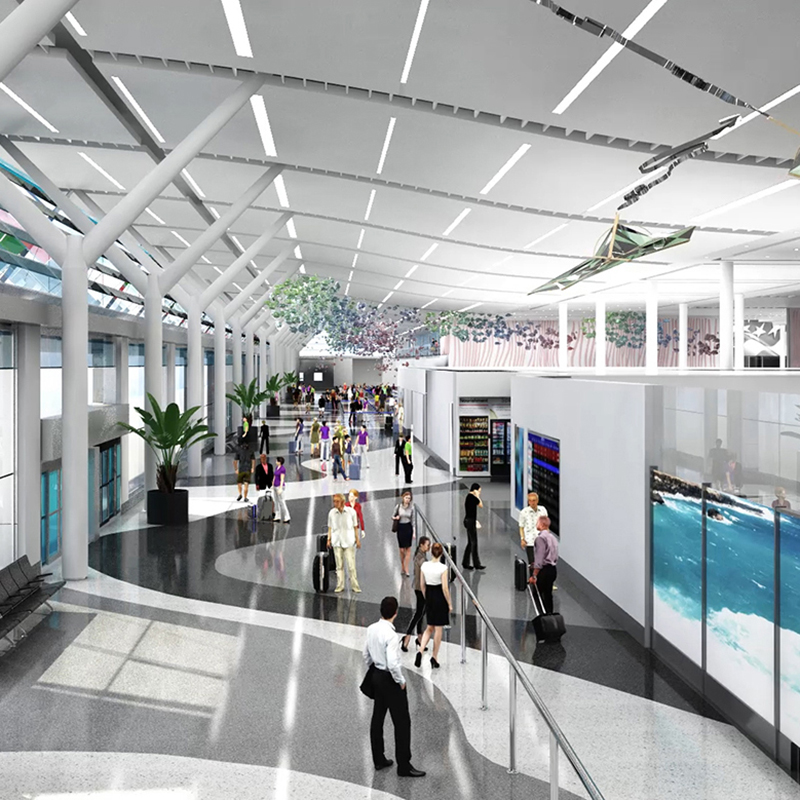
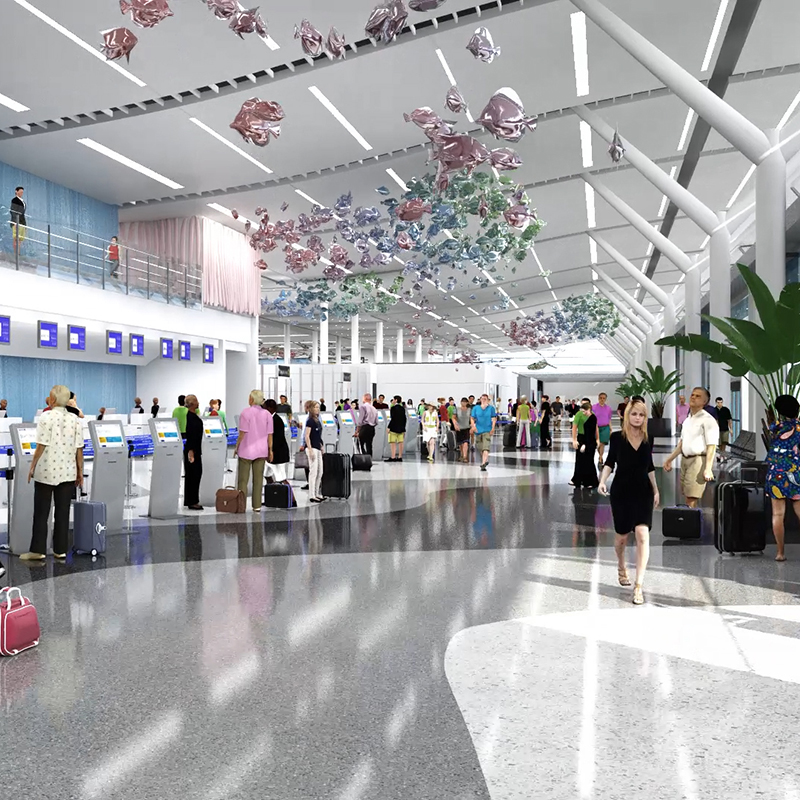
— Renderings courtesy of Scott Associates Architects Inc.
Fraser Health Authority
Royal Columbian Hospital Redevelopment
The Royal Columbian Hospital is the oldest hospital in the province of B.C. and one of the busiest in the Fraser Health Authority. Royal Columbian provides expert care to the province's most seriously ill or injured. It is the only hospital in B.C. that caters to trauma, cardiac care, neurosurgery, high-risk, obstetrics, neonatal intensive care, and acute mental health care all on one site.
HH Angus and Associates is serving as the Planning, Implementation and Closeout Consultant for the Fraser Health Authority’s large, multi-phase redevelopment for Royal Columbian Hospital (RCH) in New Westminster, BC.
RCH is British Columbia’s oldest hospital, and one of only two adult trauma centres in the Lower Mainland. The plan, rolling out in three proposed phases over a decade, will see a major expansion of the acute care campus, with upgrades to critical infrastructure.
Phase 1 included a number of projects to help prepare the hospital’s infrastructure for future expansion. These were a new energy centre; a five-storey, 75-bed mental health and substance abuse facility; underground parking for 450 cars; and a regional data centre which will serve all Fraser Health sites, including 12 hospitals and a large group of community healthcare centres serving a population of 1.6 million.
Phase 1 design challenges included the site itself, which is a steeply sloped, truncated triangle constrained on four sides by roadways. Working closely with CannonDesign, we developed an Indicative Design to ensure the site would work for a mental health building while accommodating the energy centre.
Other challenges included complex scheduling issues to maintain reliable services to the site as the new Energy Centre replaced the old one, and the design of a new, large heating, cooling and electrical plant to serve the current and future RCH campus. HH Angus engineers drew on their deep experience in delivering large healthcare projects to project the future heating, cooling and electrical demands on the Energy Centre that would support the long-term needs of RCH for buildings not yet designed.
Phase 2’s new Acute Care Tower will house a number of services, including emergency, surgery, intensive care and inpatient rooms. Expansion and renovations to the existing buildings will follow in Phase 3. New buildings will be designed to LEED Gold green building standards, and incorporate BC wood, as part of Fraser Health's and the Province's commitment to sustainability.
Image courtesy of Fraser Health.
SERVICES
PDC - Mechanical Compliance Engineering | Electrical Compliance Engineering | Vertical Transportation Compliance
PROJECT FEATURES
Status: Phase 1 – work is finished, Phase 2 – ongoing | Buildings being designed to LEED Gold
LOCATION
New Westminster, BC
KEY SCOPE ELEMENTS
Planning, Implementation and Closeout Consultant | Phase 1 includes a number of projects to help prepare hospital infrastructure for future expansion | Phase 2 Acute Care Tower
Toronto Transit Commission
Downtown Relief Line South (Ontario Line)
“The proposed Relief Line South, a 7.5km long planned subway line with 8 stations, was intended to connect the Yonge-University-Spadina Subway (Line 1) downtown to the Bloor-Danforth Subway (Line 2). The Relief Line South was conceived to relieve crowding on Line 1 south of Bloor, at the Bloor-Yonge Station, and on the surface transit routes coming in and out of downtown.”*
HH Angus was engaged to produce preliminary systems design for two subway stations on the line: Gerrard Station, an in-line station, and Pape, one of the interchange stations, in this case with the existing Bloor/Danforth Line.
Funding and plans for transit relief lines are under review.
* Quote source: Reliefline.ca
SERVICES
Mechanical Engineering | Electrical Engineering | Vertical Transportation
PROJECT FEATURES
Size: 7.5km | Status: Ongoing
LOCATION
Toronto, Ontario
KEY SCOPE ELEMENTS
Preliminary Design
Halton Healthcare
Oakville Trafalgar Memorial Hospital
As a large super hospital, this greenfield ~ 1.5 million ft2 facility features ORs, Emergency Department, Diagnostic Imaging, Mental Health, Long term Critical Care, and Dialysis services. There is also a large central kitchen and central Sterile Processing department. The hospital has been certified LEED Gold NC, exceeding its target of LEED Silver NC.
The central utility plant provides 4200 tons of cooling, 1500 bhp of hot water and 1500 bhp of steam. There is 15 MW of generator capacity onsite, along with 72 hours of fuel oil storage and a large fuel oil distribution system.
Some of the complexity inherent in this project was due to the design work being split between multiple engineering companies, which significantly increased the amount of coordination required. A key challenge was simply the scale of the new hospital, which increased the complexity of all of the systems. It required integration of systems across multiple engineering companies who were producing different portions of the design.
Another challenge was the extremely tight project schedule. This meant that tasks, which are normally completed sequentially, had to be done concurrently. This required very exacting planning and accelerated design work. Regular meetings with multiple engineering and architecture disciplines allow parties to bring their issues and design requirements to the table and to work through them in a collaborative way.
The vertical transportation design scope included 33 elevators servicing the main hospital building and 3 providing service to the parking garage.
The project co. required commissioning support for the contracting team in order to achieve milestones. HH Angus assembled a separate team of technical personnel to blitz specific systems in a 7-week period. With little preparation time, HH Angus leveraged members of the design team to train the commissioning personnel prior to going to site.
SERVICES
Mechanical Engineering | Vertical Transportation Consultant | Commissioning Support
PROJECT FEATURES
Size: 1.5 million ft2 | Completed 2015 | Greenfield super hospital project | LEED Gold
LOCATION
Oakville, Ontario
KEY SCOPE ELEMENTS
Central Utility Plant provides 4200 tons of cooling, 1500 bhp of hot water and 1500 bhp of steam | 36 elevators serve the hospital and parking facilities
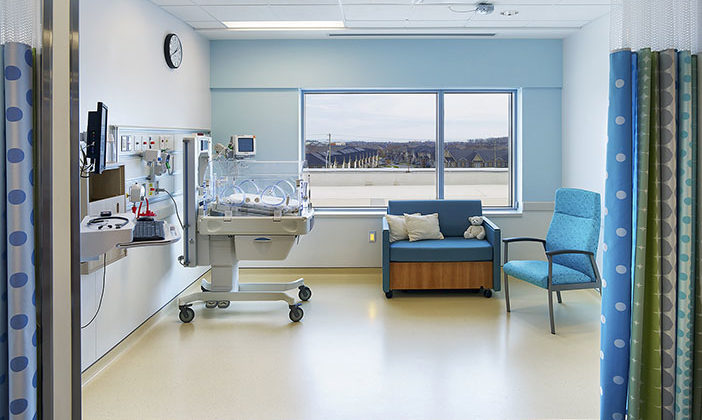
Alternate approach to Cx
Through a cycle of improvements in methodology, HH Angus was able to improve productivity on site by more than 100% with an alternate approach to commissioning, which was shared with other onsite commissioning groups.
SickKids
Peter Gilgan Centre for Research & Learning
“This investment in the Research and Learning Tower will help ensure that Canada remains a world leader in health research, and that we will continue to make discoveries that benefit children around the world.”
– Gary Goodyear, Minister of State for Science and Technology
HH Angus provided mechanical and electrical consulting engineering for this 740,000 ft2 high-rise research and educational facility. This building enhanced the overall campus of SickKids, which totals over 2,500,000 ft2. SickKids is a landmark hospital and renowned internationally as a world-class institution.
The facility has been certified LEED® Gold. Energy modeling indicated a significant improvement over the minimum energy performance required by the program. Systems were segregated to achieve significant thermal reuse within the facility. The option to integrate a waste heat recovery system from the neighbouring district heating provider was incorporated into the design to realize even greater energy efficiency in future.
The building services design supported the main objectives for the new facility:
- Consolidate the Research Institute into a cohesive unit
- Integrate research functions with the hospital
- Provide flexibility for future change
- Maximize functionality and efficiency
- Share support functions
- Utilize current technologies and infrastructure, including a plan for increased security for highly specialized spaces such as Containment Level 3
- Incorporate exemplary sustainable “Green” building design concepts and system
- Create a high-tech, cost-effective space for evolving state-of-the-art technologies
The interesting design challenges inherent in this high-rise lab building contributed to both the complexity and enjoyment of the design process, including a 1½ storey vivarium and 40,000 ft2 of educational space.
Quote source: SickKids
SERVICES
Mechanical Engineering | Electrical Engineering | IT & Communication Design | Vertical Transportation | Lighting Design
PROJECT FEATURES
Size: 740,000 ft2 with 40,000 ft2 educational space | Status: Completed 2013
LOCATION
Toronto, Ontario
KEY SCOPE ELEMENTS
Complex systems design for a tight downtown urban space | 1.5 storey vivarium | LEED Gold Certified | Incorporated options to permit a future waste heat recovery system