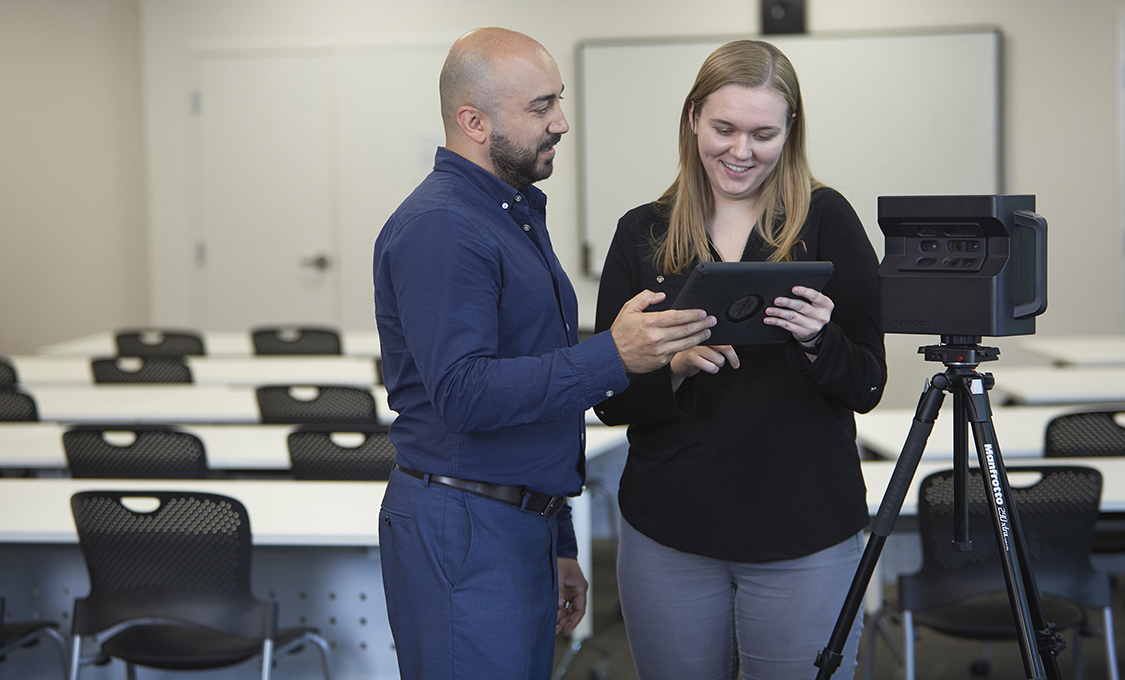
In the architecture, engineering and construction (AEC) industry, 3D reality capture is the process of scanning a building, portion of a building, equipment or site in the real world and converting the scanned data into a useful 3D digital model. A physical space is scanned using various technologies to collect huge amounts of spatial data to create different types of 3D visualization—from 360 degree 4K videos and photorealistic walkthroughs to 3D mesh or point clouds models. Whether using LIDAR-based technology or technology based on photogrammetry, knowing which technology to use for a given application is key to solving the challenges our clients are facing in the operation and maintenance of their facilities.
Why use it?
While you can use traditional 2D design and as-built drawings for a project, 3D reality capture can offer many benefits over the traditional approach, including saving time, reducing costs and improving accuracy.
Barriers to adoption decreasing. The cost of 3D scanners and other reality capture hardware has become increasingly affordable, even as quality and features continue to improve. Also, the software has become very intuitive and easy-to-use.
Highly accurate and reliable information. The reliability of existing as-built 2D drawings often varies from project to project and can be a pain point in retrofits and renovations. Instead of depending on outdated drawings or time-consuming manual measurements or surveys, reality capture technology can capture existing site conditions very efficiently and accurately. The 3D scan and resultant 3D models can then be quickly actioned by importing into the BIM software of choice and utilized by the entire project team.
Create efficiencies. Due to its accuracy and speed, reality capture reduces the need for multiple site visits – many of which are typically made simply to re-measure or double check survey results. By ‘capturing once’, project teams can use 3D scans or BIM models to derive more insights and identify potential conflicts or opportunities much earlier in the design and construction process.
Scan to BIM. By scanning the existing conditions and creating a functional BIM model, teams can begin designing immediately, allowing for greater accuracy, reduction in rework and shortening project schedules.
Improved collaboration. We typically make the resulting 3D scans and/or BIM models available in the cloud, allowing everyone involved in the design and construction process to access the one model from anywhere. Teams can be based anywhere and have the ability to view and interact with the data in real-time – making notes, providing feedback, taking measurements of existing site conditions from the 3D model, and making iterative design changes in a highly interactive and collaborative way.
Documenting progress. Reality Capture allows for fast and efficient documentation of construction progress. Regular scans of the site help ensure that construction is matching the design intent and allows the team to discover discrepancies before they become costly mistakes.
How HH Angus is Using Reality Capture
3D reality capture is very convenient, allowing us to capture dimensionally-accurate records of systems infrastructure (usually hidden above ceilings, under floors or behind walls), without having to rely on sketches or individual photos. Each 3D reality capture tool has unique advantages and applications. Knowing which tool is the best resource in a given situation forms part of the expertise of HH Angus’ technical staff.
Our current in-house technologies capture site data via a Matterport scanner or Theta V 360 camera. The Matterport scanner has an accuracy of 99% to reality; plus 3D scans are captured in 4K, providing very detailed high-resolution images. The scans are hosted on the Matterport cloud platform, and users can easily access or share them through any web browser. We can also produce point cloud data from the Matterport scans, which can be imported into a Revit model for our clients or their third-party vendors, such as architects, contractors, facility maintenance staff, other engineering disciplines, etc.
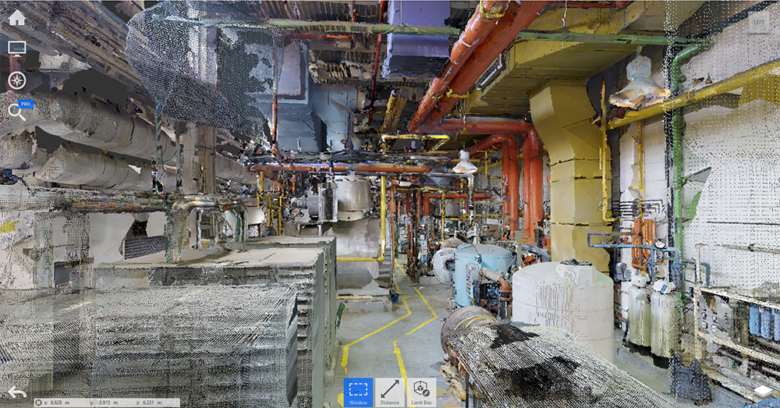
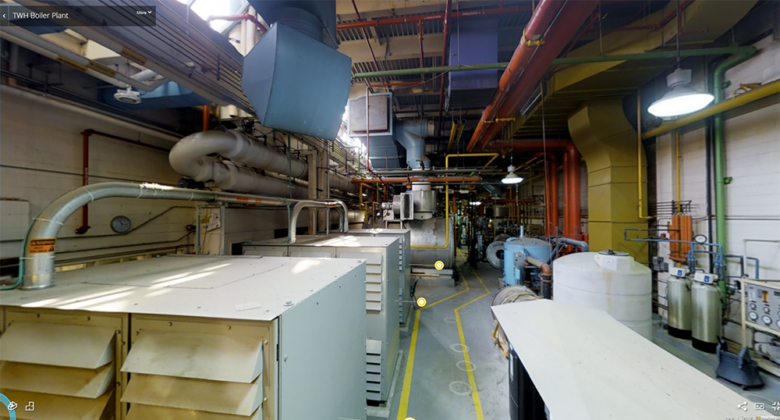

One of the features of the Matterport platform is the ability to create links to specific site locations in the model. Users simply click on a link to be taken instantly to a detailed 360-degree view of that area or equipment within the site model, providing real benefit to clients, their facility managers and third-party vendors.
This virtual walkthrough showcases some of the potential benefits of a Matterport walkthrough for a mechanical room. You can tag significant features, embed drawings and manuals, and create links to external documents or webpages.
Click on the image below to load the Matterport model which you can interact with and navigate in this screen.
Having detailed interactive maps of facility infrastructure provides important resources for future projects. The virtual walk-throughs created using the Theta V 360 camera can replace the contractors’ physical walk-through during the Tender process, freeing up client personnel traditionally required to host the walk-throughs, as well as reducing travel time, parking costs, and the carbon footprint that would otherwise be incurred for bidders traveling to and from site. For clients interested in decreasing the carbon footprint of their operations and facilities, any opportunity to reduce pollution and wasted time makes a great deal of sense. During COVID-19 pandemic restrictions, scans produced by the Matterport scanner or 360 images and video created by the Theta V 360 are providing immense value, making remote site access possible for a range of project stakeholders. The Matterport model also provides a reliable resource for measurements that may be required for scope changes, or that may have been missed during in-person site visits. This makes return visits unnecessary and reduces time demands and the need for off-hours availability for clients who would otherwise have to be on site for these return visits.
Digital Twinning. We also see the vast potential of digital twining and the visualization of live data. In this basic digital twin, we have visualized whether the space airflow is meeting CSA 317.2 requirements. You can filter the model by level, highlight rooms that are out of range, and even zoom into a room that’s experiencing flow issues. The intent of the model is to provide visualizations that allow facility operators to decipher information more easily and make informed decisions faster.
Below is an example of a basic digital twin. Click on the image which will launch the digital twin in a new page.
LIDAR. Another major player in 3D scanning technologies is LIDAR (Light Detection and Ranging), essentially radar with laser. You may have already have heard of LIDAR applications being used in autonomous driving test vehicles and in drone technology. Costs have been dropping steadily for previously expensive terrestrial scanners, and it’s now available on the Apple iPhone 12 Pro and the Apple iPad Pro. LIDAR combines camera images with radar and laser to construct 3D images in real time in order to create a point cloud. Currently, HH Angus is testing how our proprietary HH Angus Onsite app could sync with a smartphone’s LIDAR capabilities to overcome data limits, and how it might fit into project workflows to replace some of the existing programs we’re using in the reality capture service we provide to clients. The intent is to create more efficiencies. Stay tuned for more developments as mobile LIDAR technology improves.
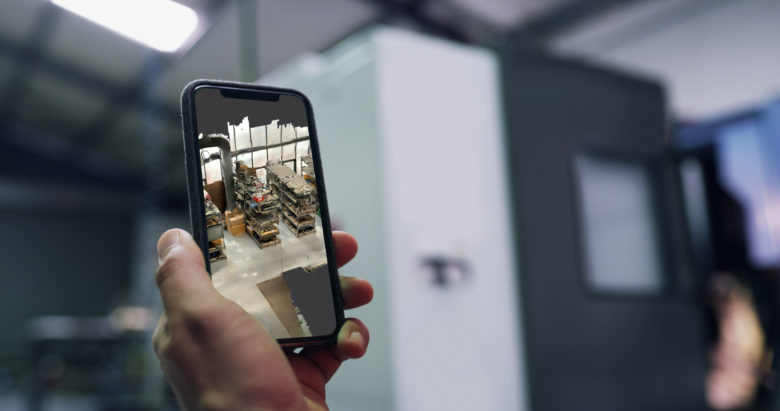
We’re really excited about the value Reality Capture brings to our clients and our workflow. We’re even more excited about its future; from improved capabilities with tools like drones, mobile devices, and robots, to building intelligent digital twins leveraging IoT sensors that can continue with the building past design and into post-occupancy to continually monitor and improve occupancy and operating conditions.
For more information about how our scanning technologies can benefit your facilities, please contact:
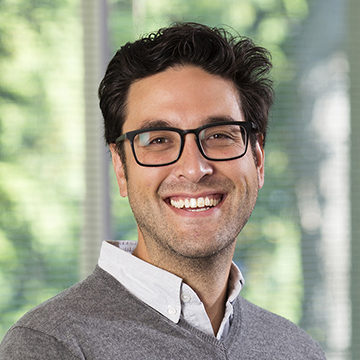
Akira Jones, P.Eng.
BIM Leader
akira.jones@hhangus.com
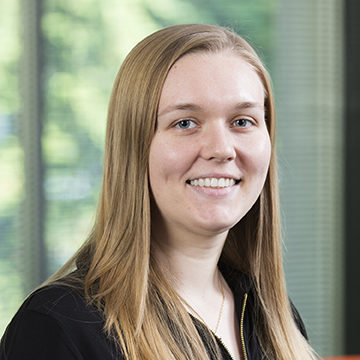
Melissa Parry, CanBIM P1, ACP Revit MEP
BIM Coordinator
melissa.parry@hhangus.com