Service: Mechanical Engineering
Enwave Energy Corporation
Pearl Street Energy Centre
The Pearl Street Energy Centre project has been honoured with an Award of Distinction at the Ontario Engineering Project Awards by the Association of Consulting Engineering Companies (ACEC).
Buildings in Toronto generate more than half of the city's greenhouse gas emissions. New technologies, like Enwave's expanded heat delivery system, will play a critical role in reducing our cumulative carbon footprint.
This project exemplifies cutting-edge engineering and design, integrating robust energy solutions that challenge traditional methods. Our focus on sustainable and efficient energy use through advanced engineering practices not only supports but advances the environmental goals of urban energy systems. HH Angus was the Prime Consultant and Mechanical and Electrical Design Engineers for the Pearl Street Energy Centre (PSEC) project. We also acted as the design team project managers.
When fully utilized, Enwave's low carbon heating facility will provide enough low-carbon heating to reduce emissions in Toronto by approximately 11,600 tCO2e, the equivalent of converting over 10 million square feet of office space to net zero.
As part of the TransformTO Climate Action Plan, which outlines ways to improve the city’s health, grow the economy and improve social equity, district energy was identified as a key strategy. In 2017, Enwave was selected as a partner by Toronto’s City Council to help accelerate the implementation of the plan to reduce greenhouse gas emissions and make the city more resilient.
Enwave’s district energy system is the largest in North America. It serves 180 buildings comprising more than 40 million square feet through 4 interconnected downtown plants and 40 kilometres of underground pipes. The addition of the PSEC to the district energy system will expand Toronto’s district heating and cooling distribution and capacity using low carbon technologies, by installing 3600 tons of cooling and 62,000 Mbh (thousand BTU’s per hour) of heating using water source heat pumps (heat reclaim chillers). Enwave’s ‘Green Heat’ offering is also being made possible by the installation of new assets that utilize waste heat while producing cooling and hot water.
The site offered some interesting complexities to be solved by the design team. The first was space constraints. As the existing Energy Centre did not have any space to house the new equipment, the only available space that could be used for the addition is a small corner on the lot where buried fuel oil tanks are present. A design was implemented to build over the tanks, one that would comply with the requirements of the Ontario Building Code and the Technical Standards and Safety Authority by leaving the ground level open for future removal of the tanks. All disciplines had to overcome many challenges due to space limitations, including structural, architectural, mechanical, and electrical.
A challenge for the mechanical design team centered on how to integrate the new heat pump system with the existing heating and cooling district system, as well as how to stage equipment without impacting Enwave’s existing customers and their stringent temperature requirements. Our solution was to design a false loading system to start and stage on additional heat pumps in order to avoid temperature spikes which would have negative impacts on customers’ critical data centre equipment.
According to the Canada Green Building Council, “it’s estimated that residential, commercial, and institutional buildings contribute 17% of Canada's greenhouse gas emissions today, and when building materials and construction are included, this level approaches 30%”. As the designers and engineers of these facilities, the AEC industry has an outsize role to play in ensuring the success of sustainable development.
HH Angus has a proven track record of promoting innovative and sustainable engineering solutions. We are committed to providing engineering solutions that reduce energy consumption and reduce or eliminate greenhouse gases.
SERVICES
Prime Consultant | Mechanical Engineering | Electrical Engineering
PROJECT FEATURES
Completed 2025 | New assets use waste heat while producing cooling and hot water | 3600 tons of cooling | 62,000 Mbh heating using water source heat pumps
LOCATION
Toronto, Ontario
KEY SCOPE ELEMENTS
Overcame site constraints through innovative design to comply with OBC and TSSA requirements | Integrated new heat pump system to existing system
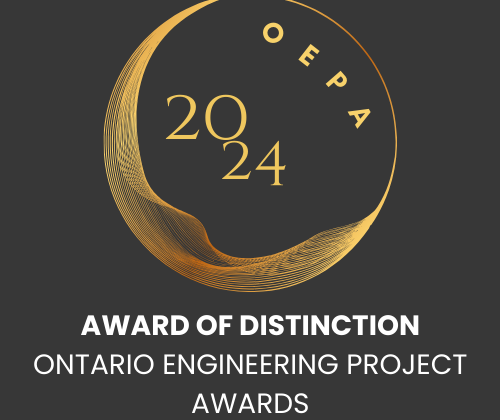
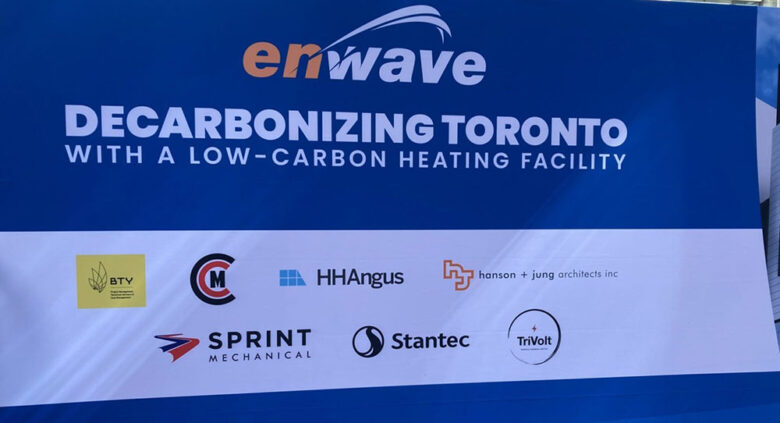
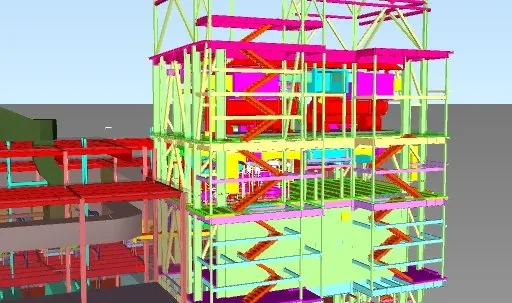
University of Toronto
Robarts Library, Reading Room Renovation
The Robarts Library, renowned as an example of the 'Brutalist' style of architecture, stands as one of Canada's largest academic library buildings, serving as a cornerstone of scholarly pursuit at the University of Toronto.
HH Angus provided mechanical and electrical engineering services, as well as design consulting for IMIT and lighting, for the renovation of the Library's fourth floor Reading Room.
The project, aimed at modernizing the library's facilities to accommodate contemporary learning paradigms, posed several intricate challenges. One notable challenge involved the intricate design of cabling for security and telecoms within the limited capacity channels of the floor slab, while ensuring the preservation of the library's architectural integrity. Moreover, the integration of wireless thermostats for HVAC control demanded meticulous planning to guarantee effective functionality while maintaining the library's iconic aesthetic.
In response to the evolving needs of the campus community, the renovated space has been thoughtfully curated to foster a conducive environment for study, collaboration, and digital scholarship. Individual study areas, equipped with state-of-the-art digital stations and consultation rooms, offer students and faculty alike the resources they need to thrive academically. Additionally, the incorporation of light therapy zones underscores a commitment to promoting wellness and inclusivity within the Library's patrons.
Improved accessibility was a key aspect of this renovation, featuring new study spots with adjustable desk heights, versatile seating configurations, and customizable lighting options, ensuring that all user's needs are considered. As well, strategic wayfinding elements and clear sightlines have been implemented to facilitate seamless navigation throughout the revitalized space.
SERVICES
Mechanical Engineering | Electrical Engineering | IMIT Consultant | Lighting Consultant
PROJECT FEATURES
20,300 ft2 space | Accessible study areas | Integration of building systems
LOCATION
Toronto, Ontario
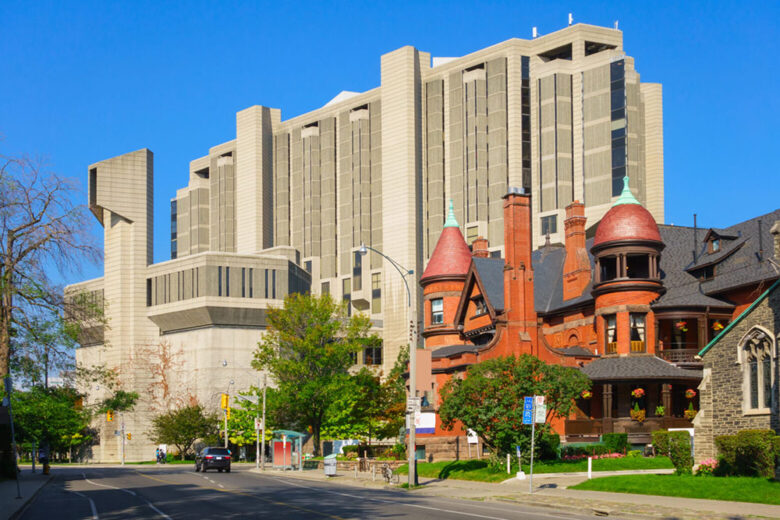
Enhanced environments
The Library renovation is a significant advancement in the modernization of an academic institution, and underscores UofT's dedication to enhancing the built environment for all users.
City of Mississauga
Burnhamthorpe Community Centre Renovation and Expansion
The Community Centre features a state-of-the-art aquatic centre as well as an equipment-based fitness centre. This is the first project designed and built to Mississauga's corporate Green Building standard. The project has also achieved Level 1 CGBS and incorporates net zero and passive house principles, a high-performance building envelope, triple glazing, and a green roof.
HH Angus played a key role in this project, providing mechanical and electrical engineering services, as well as security, IMIT, lighting, AV, and plumbing design. The addition includes a new 25-metre, 6-lane pool, therapeutic pool, fitness centre, and common areas, for a total of 43,000 ft2 of added amenities.
Renovations to the existing community centre encompass improvements across 65,000 ft2, repurposing and relocating multi-purpose program spaces, gymnasium, indoor arena, and upgrading facilities to meet accessibility and green development standards. Despite challenges posed in connecting to the existing building, the addition was situated on the northeast corner, utilizing space from the adjacent park.
To see more renovations, click here
SERVICES
Mechanical Engineering | Electrical Engineering | Plumbing Design | Lighting Design | Audio-Visual Design | Security Design | IMIT Design
PROJECT FEATURES
Green facility design to LEED Silver standard | State-of-the-art aquatic centre | Equipment-based fitness centre | Status: Completed 2024
LOCATION
Mississauga, Ontario
KEY SCOPE ELEMENTS
Project built to Mississauga's Green Building standard | Achieved Level 1 CGBC | Addition connected to existing recreation centre | Renovations and upgrades to existing building
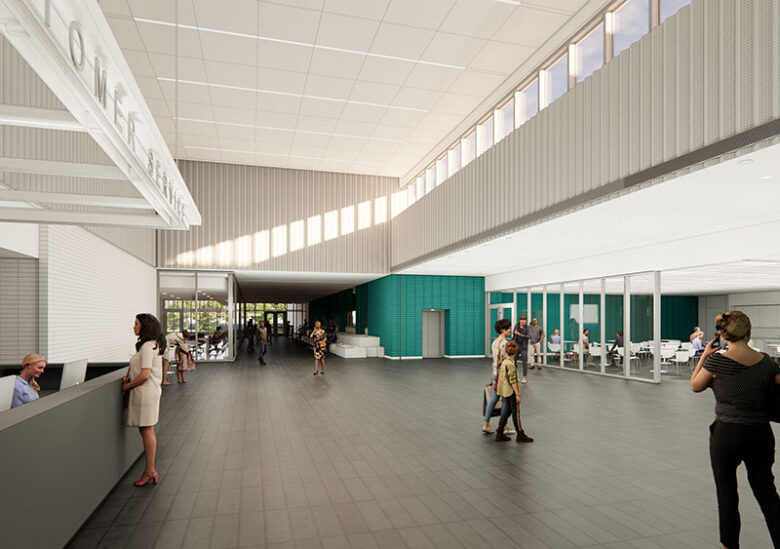
All images courtesy of CS&P Architects
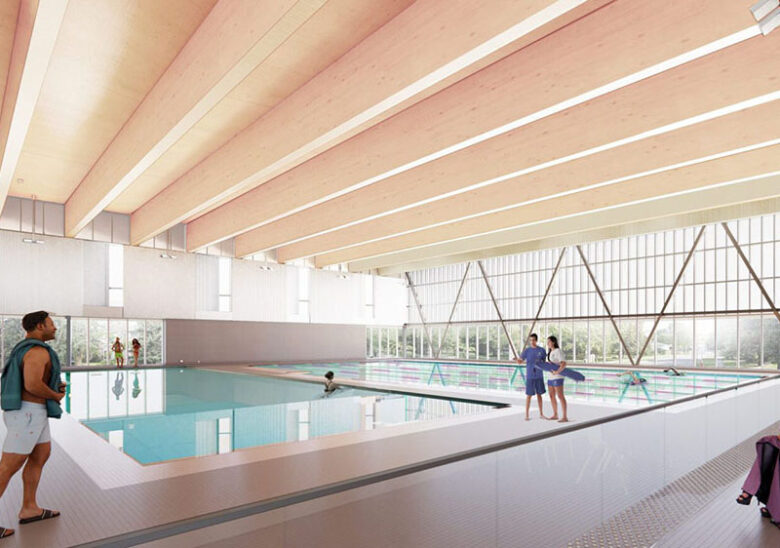
Toronto Western Hospital
New Patient and Surgical Tower
University Health Network’s (UHN) new $1 billion, 15-storey patient care and surgical tower will be built on Toronto Western Hospital’s (TWH) campus in downtown Toronto and enhance UHN’s capabilities caring for complex neurological and orthopedic cases.
We’re excited to be part of this important and transformative healthcare project for UHN. HH Angus, in partnership with DIALOG, is providing mechanical and electrical engineering and ICAT/IMIT design services for the new tower.
The new facility will be over 380,000 ft2 in size over 15-storeys and include 11 clinical program floors, 82 beds, and 20 operating rooms of which three will be hybrid ORs with cutting-edge imaging capabilities.
The new tower will feature many of the latest healthcare technological advancements. We have supported UHN in developing a Digital Strategy for this facility and, have incorporated technologies such as real-time locating systems for patient journey tracking, advanced audio-visual systems for information sharing, and surgical suite technologies to improve flow, communication and educational opportunities.
Among the electrical systems features, emergency generators sized for full backup and a central UPS will improve the resilience of this critical facility.
SERVICES
Mechanical Engineering | Electrical Engineering | ICAT/IMIT Consulting
PROJECT FEATURES
Size: 380,000 ft2 | Budget: $1 billion | 15-storeys | Downtown urban setting | 11 clinical program floors, 82 beds and 20 operating rooms
LOCATION
Toronto, Ontario
KEY SCOPE ELEMENTS
Targeting 32% energy reduction | Wastewater energy transfer (WET) system for heating, cooling, steam and domestic hot water
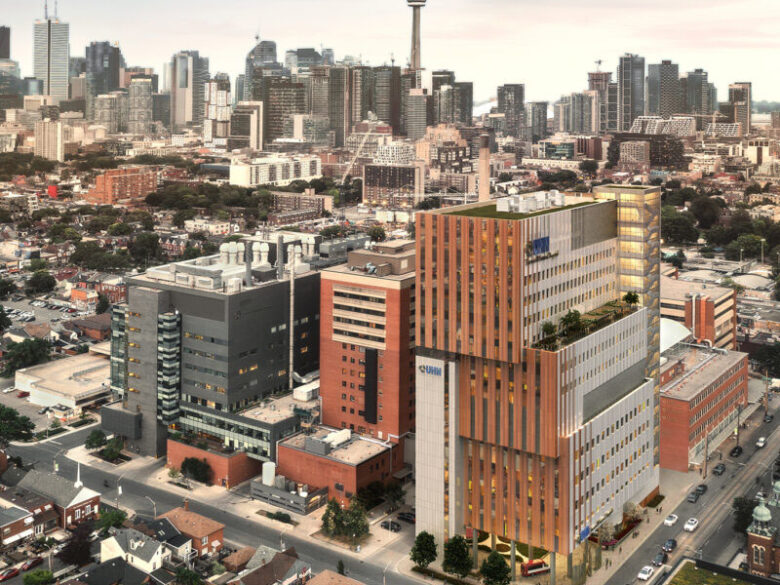
Sustainable Engineering
Building on our decarbonization and sustainability experience for healthcare clients across the country, TWH’s new tower strives to be Net Zero, targeting an overall 32% reduction in energy consumption from the OBC SB-10 (2017) reference model through a variety of initiatives, including integrating with UHN’s wastewater energy transfer system for heating, cooling, steam and domestic hot water. The mechanical design also includes energy recovery wheels on the ventilation system and considerations for predicted future climate conditions.
Proud Partnership
HH Angus is proud to continue collaborating with UHN – ranked number one on the 2023 list of Canada’s Top 40 Research Hospitals – a relationship that spans several decades working on many of their key facilities. Recent collaborations include a major upgrade at TWH’s Power House, which significantly improved the reliability of critical mechanical and electrical infrastructure in order to maintain the integrity of OR services, and the Rapid Assessment Centre Expansion at the Toronto General Hospital.
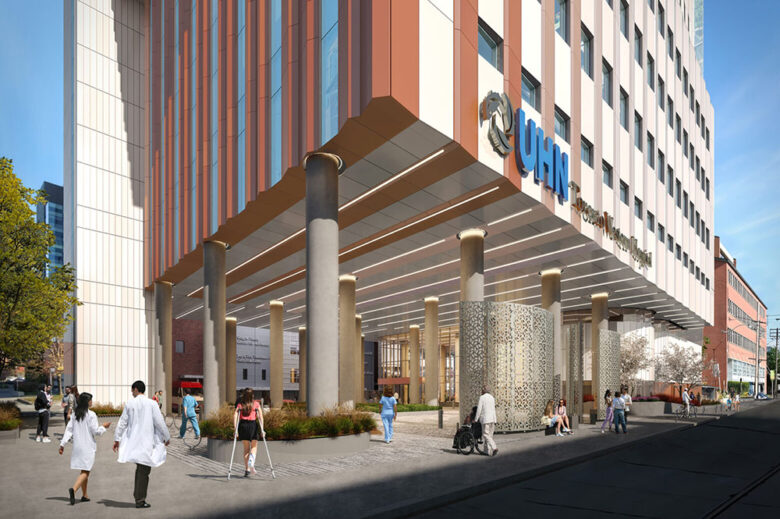
University Health Network
Toronto Western Hospital Critical Infrastructure Reliability Project
Toronto Western Hospital (TWH), part of the University Health Network, initiated a project to enhance the reliability of its critical mechanical and electrical (M&E) infrastructure. With aging equipment dating back to 1954, TWH partnered with HH Angus to undertake a comprehensive upgrade project aimed at ensuring the continuous operation of high-risk medical services.
As the prime consultant, HH Angus was responsible for assessing the condition of existing mechanical and electrical systems. Following the assessment, upgrades were made to the facility, including replacing emergency generators, and establishing a new electrical room serving the ORs and the broader hospital campus. Subconsultants, including architectural, civil, environmental, and cost consultants, played crucial roles throughout the project.
To determine suitable locations for generators, extensive investigations were conducted, including structure analysis, examination of building codes, and assessment of environmental impacts. This collaborative effort led to the approval of a new penthouse above the East Wing for generator placement. The final engineering package involved locating the emergency generators at grade in a new fenced area, alongside the supply and installation of two new 1100W emergency generators and upgrades to the electrical network and distribution systems within the powerhouse.
HH Angus leveraged reality capture workflows, utilizing photogrammetry and a Matterport Pro2 camera, to produce a digital 3D model of the powerhouse and infrastructure. Through the efforts of our BIM team, 3D scans were taken of mechanical and electrical spaces, including complex piping and ductwork, to generate point clouds for reference in Revit. These models accurately depict existing systems, including central steam, chilled water, and emergency power systems serving the hospital's ORs and surrounding campus.
Additionally, the project has been recognized for excellence, with the generator exhaust stack winning in the category of Steel Works – Sculptures – Outdoor Pavilions at the Canadian Institute of Steel Construction's Awards for Excellence. https://hhangus.com/award-for-excellence/
The Toronto Western Hospital Critical Infrastructure Reliability project exemplifies HH Angus's commitment to delivering reliable solutions for healthcare facilities.
SERVICES
Mechanical Engineering | Electrical Engineering | Reality Capture
PROJECT FEATURES
3D modeling of powerhouse |
Scans of mechanical and electrical (M&E) spaces using Matterport Pro2 Camera | Point clouds of complex spaces using ReCap Pro Status: Completed
LOCATION
Eastern Canada
KEY SCOPE ELEMENTS
Upgraded mechanical and electrical systems | Installed emergency generators | Ensured environmental compliance | Modernized the powerhouse infrastructure.